Generative design is a software tool that enables engineers and designers to approach design problems in more innovative and efficient ways. Generative design algorithms explore all possible design solutions by defining goals and constraints, offering engineers numerous options to explore.
Although still in its infancy, generative design has shown remarkable potential for industrial applications, particularly when coupled with 3D printing. Together, generative design and 3D printing can achieve more design flexibility, while creating lighter and stronger parts.
Today, we’ll be looking at the benefits and current challenges of using generative design, particularly when coupled with 3D printing. We’ll also explore some of the most popular generative design software used with 3D printing and take a look at the companies leveraging generative design technology to drive innovation.
What is generative design?
Generative design is a fairly new technology. As with any new technology, there remains a lack of industry consensus around its definition. In spite of this, there seem to be two main ways of looking at generative design: either as a broad term encompassing topology optimisation or as an entirely distinct technology.
A common view of generative design describes it as a technology which makes use of powerful computation to assist in the design process.
Here’s a step-by-step look at how generative design works:
1. Set parameters
The designer specifies and sets the parameters for the part design, based on parameters such as weight, material, size, cost, strength, and manufacturing methods.
2. Generate designs
The generative design software uses algorithms to explore and generate thousands of design options. At this stage, the software can also use AI-powered algorithms to analyse each design and establish the most efficient designs.
3. Select the best options
The designer can then study these designs and select the outcomes which best meet the design goal.
To determine the geometry of the design, generative design algorithms may use a range of different approaches, such as topology optimisation, biomimicry and morphogenesis.
The main difference between these approaches is that topology optimisation algorithms typically start with a pre-existing design and remove the material from it to reduce part’s weight.
Biomimicry and morphogenesis, in contrast, mimic nature’s evolutionary approach to design, like the growth of roots and branches in trees, or the evolution of bone structures, using this to generate design options.
The benefits of generative design
When used with 3D printing, the benefits can be further expanded to include decreased manufacturing costs and increased productivity. We’ve identified 3 core advantages:
1. Innovative design options
Generative design software can produce geometries that go beyond what humans can conceive, thereby enhancing human capabilities in product design.
2. Lightweighting
Generative design tools give engineers the resources to create lightweight parts using the minimum amount of material necessary, whilst adhering to the engineering requirements.
3. Part consolidation
Generative design can provide solutions to consolidate subassemblies into a single part. Consolidating parts simplifies the assembly process, maintenance and can reduce overall manufacturing costs.
Why is generative design a perfect fit for 3D printing?
Generative design software helps to conceptualise parts with complex, organic shapes. 3D printing, on the other hand, is perhaps the ideal technology to bring these shapes to life, since it is not only capable of creating complex geometries but also does it cost-effectively. With traditional manufacturing, producing these shaped might often be impractical, if not impossible, either due to high costs or the limitations of the technology.
However, it would be misleading to state that generative design is limited to only additive manufacturing, although in many cases the technology will be the most optimal production method. With some generative design software packages, you can specify manufacturing methods like CNC machining, casting or injection moulding, in addition to AM.
The challenges of generative design
Currently, generative design is in an early stage of development, which means early users may come across certain challenges.
#1: Learning curve
For example, accurately defining a design problem in computable terms, which generative design software has to solve, will involve a steep learning curve. Engineers inexperienced with expressing the design problem as a set of parameters may end up with loosely defined structural constraints or loads, which will ultimately result in a failed design.
#2: Gap between design and manufacture
Another point to consider with generative design is that efficient designs are not always can be efficiently manufactured. For example, in a Renishaw case study, engineers topologically optimised a suspension bell-crank. They didn’t, however, take into account the manufacturability of the optimised part. This resulted in a design that required a lot of supports to be printed, whereas a good practice is to design parts with as few supports needed as possible.
#3: Challenging geometries
Furthermore, designs created with the help of generative design tools can create geometries that are challenging even for 3D printing. Overhanging features and thin walls are just a couple of examples of this. However, new generative design tools provide options allowing the user to specify additional manufacturing data like overhang angles and minimum wall thickness.
#4: Resources needed
Lastly, generative design approaches can be computationally intensive and require powerful computing capabilities of the hardware. However, more and more companies offer generative design software that leverages cloud computing, eliminating the need to invest in expensive hardware.
Generative design software solutions for 3D printing
While the market for generative design software is new, there are already a number of software packages available for both additive and subtractive manufacturing. In this section, we’ll take a look at some of the most promising offerings in generative design for 3D printing.
Autodesk Generative Design
Autodesk has been at the forefront of generative design development. In April, the company launched its Autodesk Generative Design platform, incorporated into its cloud-based Fusion 360 Ultimate product development software.
How it works
The platform allows engineers to define design parameters like material, size, weight, strength, manufacturing methods, and cost constraints. Notably, the software uses AI-based algorithms, which help to filter valid designs among an array of design options. The software also takes manufacturability into account, allowing designers to select up to ten different additive manufacturing materials to study the design.
Frustum GENERATE
Frustum, a young company founded in 2014, is looking to become a significant player in the generative design field. The company’s offering is its GENERATE software – an intuitive program for creating topology-optimized components for additive manufacturing, milling and casting. GENERATE is a cloud-based platform, available in three tiers: Free, Professional, and Enterprise.
How it works
In GENERATE, the user assigns particular load and constraint values to the faces of a part. The program, powered by Frustum’s generative design engine TrueSOLIDⓇ, then generates a finite element analysis (FEA) map of stress concentrations. With this map, the users can make modifications to the part’s geometry, particularly to reduce the amount of unnecessary material in its structure. The model can be saved in STL format and is ready to be 3D printed.
Last year Frustum announced a partnership with Siemens, and currently, the technology is commercially licensed to Siemens PLM software and integrated into Siemens NX and Siemens SolidEdge.
Desktop Metal’s Live Parts™
The research group DM Lab from Desktop Metal, a US-based manufacturer of metal AM systems, has recently announced its experimental technology called Live Parts™.
How it works
The Live Parts™ generative design platform uses nature-inspired algorithms which cause parts to ‘grow’ based on a set of predetermined parameters, like size, purpose and weight. The program creates a design by developing it from a seed cell into an optimised structure, which is strong, lightweight and resistant to fatigue. The process of ‘growing’ a part typically takes between 5 and 5 minutes, depending on the size of a model.
Generative design in practice
Although generatively designed products are far from becoming mainstream, they hold a great promise for high-value industries like aerospace, automotive and medical. To be first to reap the benefits of generatively designed and additively manufactured products, some companies in these industries have already started investigating the combination of both.
Automotive
For example, with 3D printing and generative design, Bugatti Automobiles has innovated the real wing control system for the 1,500 PS Chiron super sports car in a testing project of Siemens generative design software.
Using Siemens NX platform, the automaker was able to optimise the weight of the assembly, which was then 3D printed in titanium and carbon fibre. This approach led to a weight reduction of more than 50%.
General Motors is another car manufacturer exploring the possibilities of generative design and 3D printing for its future products by using Autodesk generative design software.
“At GM, we see great potential for generative design combined with additive manufacturing processes to enable part designs that are lightweight with the performance criteria we expect,” says Kevin Quinn, director of additive manufacturing at General Motors.
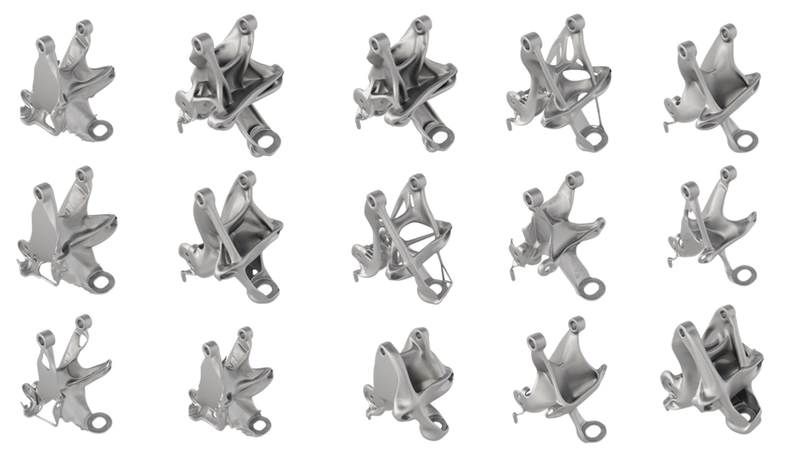
For now, GM doesn’t 3D print generatively designed parts for production, focusing instead on proof of concept . For example, in an initial project, GM used Autodesk’s software to produce more than 150 design options of a seat bracket. These were 40% lighter and 20% stronger than the bracket currently in use. The company was also able to consolidate the eight different components of the bracket into one 3D-printed part.
Yet, one automotive company has achieved a milestone with generatively designed and mass-produced 3D printed part. BMW recently showcased its award-winning roof bracket for BMW i8 roadster. Engineers at BMW used topology optimization to minimize the amount of material required in the part and then 3D printed the part in titanium. The topology optimization not only led to a weight reduction of 44%, but also created a design that required no support structures during the 3D printing process.
Medical
In the medical sector, generative design can be used to create implants that reproduce the porous nature of the human bone. NuVasive, a US-based medical company uses its proprietary design optimisation software to create titanium implants. The software enables latticed, asymmetric, lightweight designs, which are possible only with additive manufacturing.
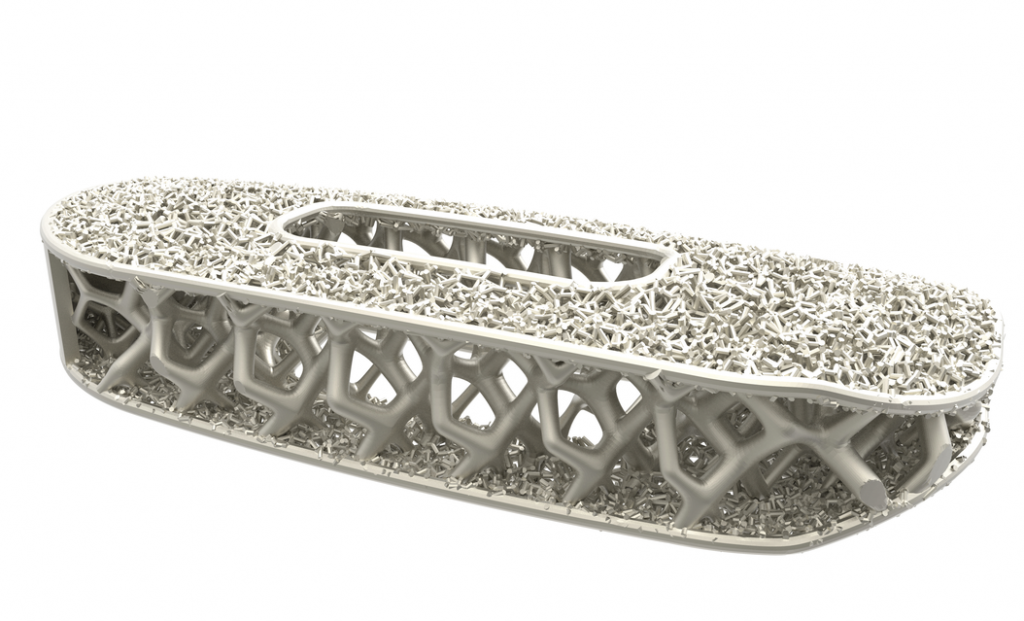
Looking ahead: the future of generative design
Examples of generative design being used across industries are becoming more common, as the technology is increasingly integrated into product design workflows. While still a relatively new technology, it already offers engineers an entirely new way of looking at product design.
While AI and machine learning has been responsible for much of the recent progress in generative design technology, additive manufacturing has also played a key role in driving adoption of generative design software. With further advancements in machine learning, cloud computing capabilities and AM, expect generative design technology to follow, becoming a key factor in the future of manufacturing.