In a challenging demonstration of Wire Arc Additive Manufacturing (WAAM), French aerostructure manufacturer STELIA Aerospace has made aluminum panels that can be used to build an airplane fuselage.
The panels are the product of a project started by STELIA in 2014 in collaboration with French engineering school Centrale Nantes, engineering consultancy firm CT Ingenierie, and Dutch aluminum company Constellium.
Due to the project’s success, STELIA is optimistic that WAAM will eventually replace the traditional means of production for airplane fuselage panels, eradicating the need for some further fixings and welding.
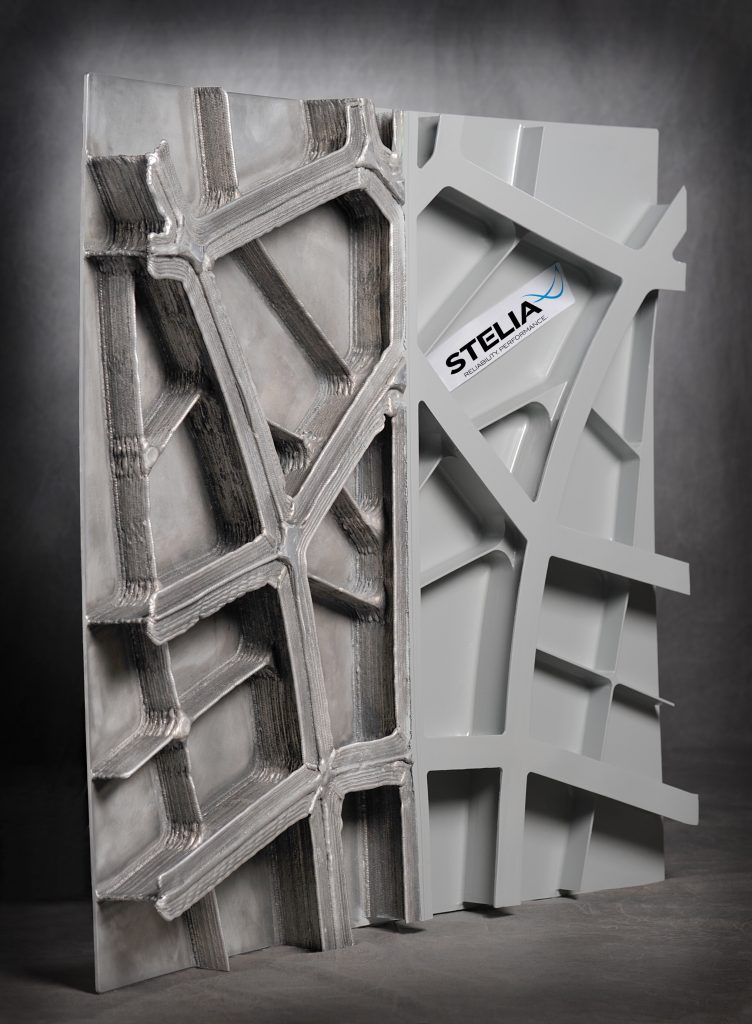
Cédric Gautier, CEO of STELIA Aerospace, comments, “With this 3D additive manufacturing demonstrator, STELIA Aerospace aims to provide its customers with innovative designs on very large structural parts derived from new calculation methods,”
“THROUGH ITS R&T DEPARTMENT, AND THANKS TO ITS PARTNERS, STELIA AEROSPACE IS THEREFORE PREPARING THE FUTURE OF AERONAUTICS, WITH A VIEW TO DEVELOP TECHNOLOGIES THAT ARE ALWAYS MORE INNOVATIVE AND WILL DIRECTLY IMPACT OUR CORE BUSINESS, AEROSTRUCTURES.”
Topology optimization for stronger parts
The parent of the fuselage breakthrough is topology optimization research and technology (R & T) project DEFACTO (DEveloppement de la Fabrication Additive pour Composant TOpologique). With the same goals, and all of the same collaborators plus Centrale Nantes, DEFACTO appears to be an extension of STELIA’s FAST project, that was in early stages of development in 2015.
Through topology optimization, STELIA R & T designers and engineers have created a fuselage skeleton with strategically placed stiffeners directly 3D printed onto the panel surfaces. Typically, these stiffeners would be affixed to fuselage panels using bolts and screws. By avoiding the need for further components, 3D printed panel stiffeners are less susceptible to weakness, creating a much more stable airplane body.
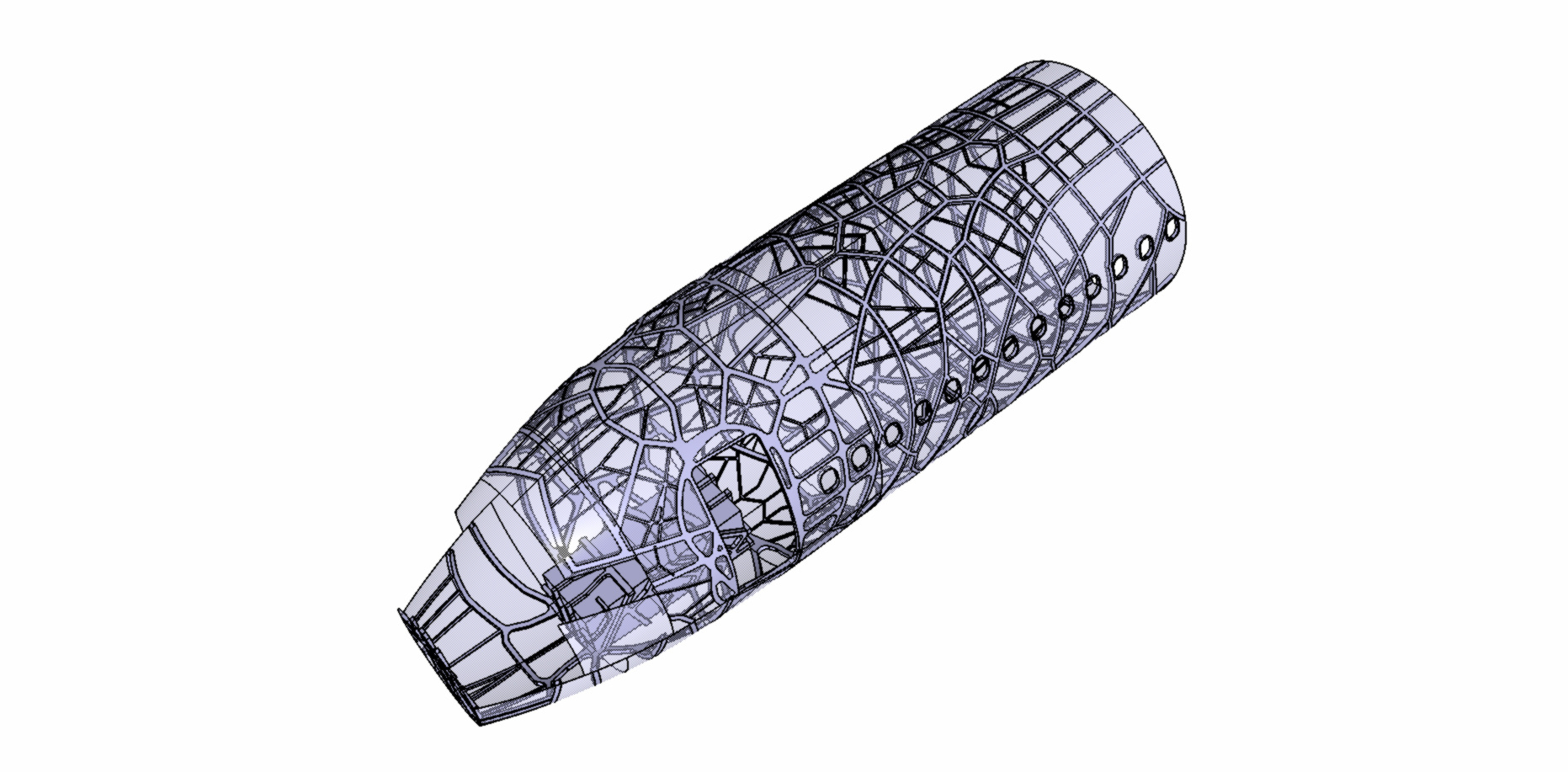
WAAM impact
As in Damen Shipyard’s WAAMpeller project, and the 1,000kg crane hook 3D printed by Huisman, STELIA’s fuselage panel demonstrator was made using a free-forming robotic arm. A single fuselage panel manufactured in this way measures 1 sq. meter. With its proprietary Electron Beam Additive Manufacturing (EBAM) technology, Sciaky has also been investigating the ability to 3D print large airplane parts.
For the ecological aspect of the project, i.e. less material waste, lower recurring manufacturing costs. STELIA’s DEFACTO is 50/50 funded by the French Directorate General for Civil Aviation (DGAC).