A deep dive into polymer 3D printing: technologies, promising developments, applications, and more.
As major chemical companies are now joining the 3D printing world and industry mainstays are further advancing the capabilities of the technology, polymer 3D printing is given a tremendous boost.
To keep up to the latest developments, below we’ll be diving into the most exciting innovations in polymer 3D printing and opportunities offered by the technology. But first, let’s explore the common polymer 3D printing techniques used across industries.
Polymer 3D Printing: The Technologies
Polymer 3D printers dominate the 3D printing hardware arena. They lead on all fronts: shipment revenues, the installed base, and the number of developments happening in this space.
Polymer 3D printing was predicted to have generated $11.7 billion in revenues in 2020, a figure that includes sales of hardware, materials and 3D-printed parts combined.
Below, we’re taking a look at the key technologies driving this growth.
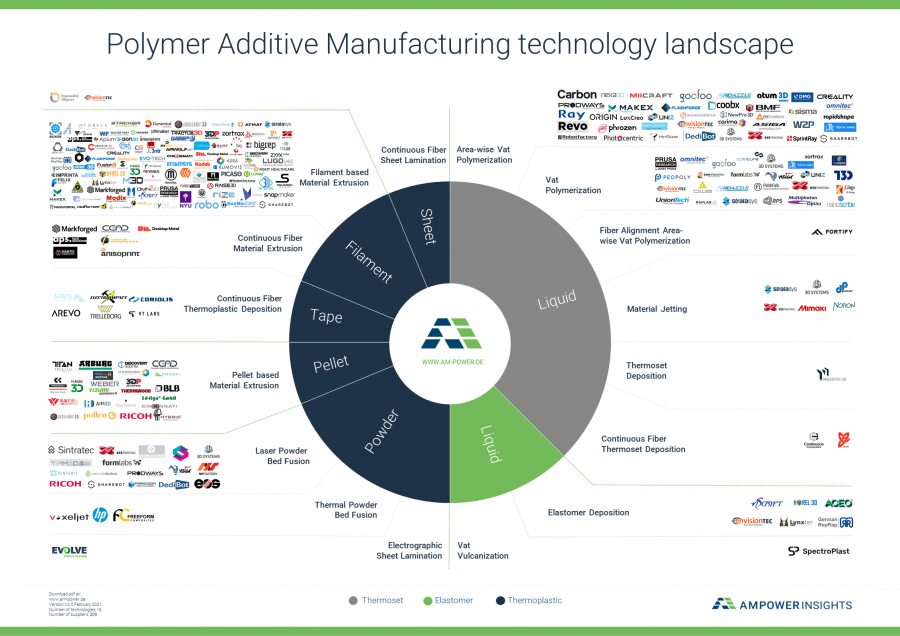
Vat Polymerisation
Stereolithography
The emergence of Stereolithography (SLA) in the 1980s marked the beginning of the 3D printing era. SLA is an ideal technology for producing great-looking parts with an excellent surface finish. Due to its accuracy and high resolution, SLA parts are mostly used for form and fit concept models or as master patterns for moulding applications.
SLA relies on liquid photocurable resins. These are selectively cured by a UV laser layer by layer, causing the resin to solidify.
While SLA parts offer a great surface finish, they tend to be less durable than parts produced with other additive technologies. Also, since SLA materials are sensitive to UV light, their mechanical properties can change due to overexposure to sunlight, thus making them unsuitable for outdoor use.
SLA photopolymers come in a variety of colour options as well as several speciality materials (castable, durable, high-temperature, medical-grade).
The choice of materials for SLA is constantly expanding. Over the last 12 months, we’ve heard multiple announcements about new 3D printing resins from the likes of Formlabs, Henkel, Zortrax, DSM, and many more.
What can be distilled from the recent news is that 3D printing resin development has reached a new level: companies are extremely focused on advanced applications, particularly in the medical, dental and engineering fields.
Material Extrusion
FDM/FFF
Fused Deposition Modeling (FDM), as known as fused filament fabrication (FFF), is one of the most popular 3D printing methods for industrial uses. According to a market research firm, CONTEXT, the largest revenues from shipments came from this category of machines in 2020, reaching almost $150 million.
FDM became commercially available in the 1990s, serving as an affordable and user-friendly prototyping technology. Since then, FDM has evolved to offer greater reliability, accuracy and material choice, making it suitable for a number of production applications such as manufacturing aids.
FDM uses thermoplastic filaments that are extruded through a nozzle onto the printing platform one layer at a time. One of the main limitations of FDM parts is anisotropy, meaning that their mechanical properties are not equal in all spatial dimensions. This can result in weaker parts.
Furthermore, FDM has a slower printing speed compared to other 3D technologies like SLS or SLA, making it generally impractical for series production.
Today, manufacturers have a variety of FDM filaments at their disposal, from elastic TPU to durable and reinforced ABS and high-performance materials like PEEK. With the availability of production-grade thermoplastics, FDM is ideal for producing functional, durable products.
Powder Bed Fusion
Selective Laser Sintering
Selective Laser Sintering (SLS) is an additive manufacturing process that involves the fusing of plastic powdered material using a powerful laser. With a combination of high accuracy, speed, reliability and lack of support structures, SLS is used both for functional prototyping and low-volume production.
SLS typically uses polyamide (nylon) powders, with PA11 and PA12 being the two most commonly used polyamides, in addition to flexible TPU material.
However, companies are continually adding new material offerings. For example, in 2018, Evonik released the world’s first flexible plastic PEBA-based (polyether block amide) powder for SLS.
German 3D printer manufacturer EOS has also made available carbon-fibre reinforced PEKK thermoplastic for its SLS systems, in addition to its certified PEEK material. The new PEKK thermoplastic is said to be able to replace aluminium parts in aerospace and industrial applications.
Notably, EOS is currently the only manufacturer that offers an SLS system capable of processing high-performance thermoplastics like PEEK and PEKK – the EOS P800.
Historically, SLS technology has been more expensive for companies to acquire (costing into the hundreds of thousands of dollars). However, in 2014, the patent for the technology expired, giving rise to more affordable alternatives, such as the Formlabs Fuse 1 benchtop 3D printer.
Multi Jet Fusion
Since its introduction to the market in 2016, HP’s Multi Jet Fusion (MJF) has opened a new dimension for the production of industrial-grade functional parts and prototypes.
Like SLS, the technology uses nylon powders. However, instead of using lasers, MJF operates by dropping a fusing agent on each layer of powder, which is then fused by an infrared light source.
Compared to SLS, MJF offers a faster workflow due to HP’s innovative post-processing station, which speeds up the cooling process and aids in powder removal. The Jet Fusion 300/500 series also offers full-colour 3D printing capabilities.
There are a few limitations with HP’s Multi Jet Fusion, for example, its currently limited material selection (PA11, PA12, PA12 filled with glass beads).
However, HP promotes an Open Platform model, which encourages collaboration with material developers. Through this approach, HP has partnered with over 50 companies, including Evonik, BASF and Lubrizol, which are working on the development of new materials suitable for the technology.
Material Jetting
Material Jetting is an inkjet printing process that involves depositing a liquid photoreactive material onto a build platform layer by layer. Similarly to SLA, Material Jetting uses resins, which solidify under a UV light.
One of the key benefits of Material Jetting is the ability to combine two or more photopolymers during the printing process, resulting in a part with hybrid properties (e.g. combining rigidity with flexibility). Furthermore, the technology is capable of producing full-colour parts, which makes it ideal for prototypes with a final-product look.
Resins used in Material Jetting are similar to those used in SLA, but have a less viscous, ink-like form. Their cost is also typically higher.
Among the limitations of the technology is the poor mechanical properties of the printed parts, which make material jetted parts generally unsuitable for functional applications.
Polymer 3D Printing: The Opportunities and Applications
Industrial 3D printing with polymer materials unlocks a wide array of possibilities both for production and product development departments. Below, we’ve outlined the most prominent of them.
Rapid prototyping
Prototyping remains one of the primary application areas for polymer 3D printing. With the evolution of 3D printing technologies, prototypes can now be produced much faster, they are more durable and visually appealing.
The automotive industry, which is said to have purchased the greatest number of printers in 2017, is a prominent user of polymer 3D printing for prototyping purposes. Here, all kinds of 3D printing technologies are leveraged both for form and fit, as well as functional, testing and validation.
One example is Audi, which is using Stratasys’ J750 PolyJet 3D printer to design and validate parts, such as taillight covers, for its automobiles.
As a full-colour, multi-material process, Stratasys Polyjet 3D printing allows building physical prototypes with the final product look, thus considerably simplifying and accelerating the product development process.
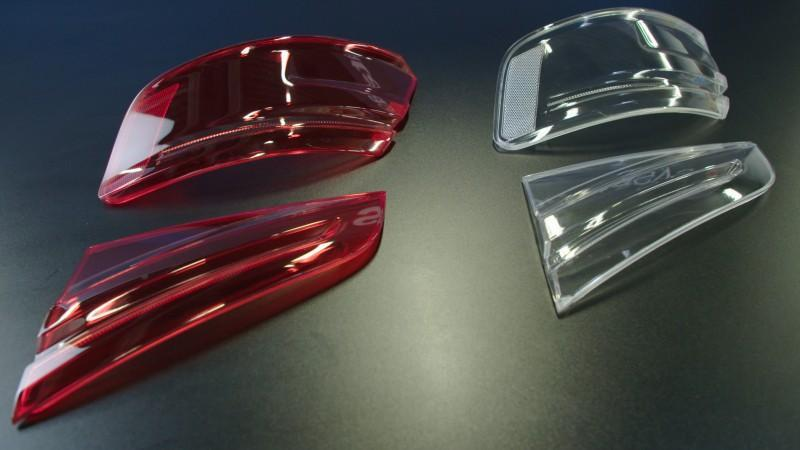
More efficient tooling
3D printing for tooling has emerged as one of the most promising uses of the technology. From jigs and fixtures to investment casting patterns, polymer 3D printing opens the door to faster, cheaper and customised tools.
Generally, companies turn to FDM and SLA technologies to produce tooling due to their relative affordability and ease of use.
Car manufacturer Ford is reported to be using Ultimaker FDM 3D printers to create custom tools.
The benefits go beyond affordability, too. According to Ford’s Technical Leader, Harold Sears, 3D printing is “helping people do their jobs by making tools that are more ergonomically correct for operators. This is perhaps a soft benefit but one that is certainly helpful if operators are happier and more comfortable doing their job. They’ll also do a better job which only improves quality.”
Additionally, at times the available 3D printable thermoplastic materials currently available are even strong enough to replace metal tools, which makes the assembly process a lot easier and lowers the cost of the custom tool.
Medical applications
The medical industry was one of the early adopters of polymer 3D printing. Today, the technology has found a number of uses in the sector, from 3D printed surgical guides and tools to replicas of human organs for pre-surgical planning.
Increasingly, 3D printing is being used to directly produce custom medical devices, including low-cost prosthetics and dental devices such as aliners and bridges.
One of the sectors of the industry that has been completely transformed by 3D printing is hearing aids. Today, more than 90% of hearing aids are manufactured worldwide using SLA 3D printing technology.
Since the outbreak of the pandemic, polymer 3D printing has also established itself as a viable technology for the production of ventilator valves, safety goggles, protective face shields and testing swabs.
Customised consumer products
Consumer goods companies are increasingly eyeing plastic 3D printing as an option for mass customisation. Since 3D printing doesn’t require labour-intensive and costly tooling and can create complex objects cost-effectively, it enables the production of personalised products tailored to consumers.
One brand exploring 3D printing is Dr. Scholl‘s, the provider of foot care products. It has partnered with technology company Wiivv to make custom 3D printed inserts.
Using Wiivv Fit Technology, Dr Scholl’s offers a customisation app, which maps out 400 points on each user’s feet with a few phone photos. Though this process, which takes less than five minutes, inserts can be designed and then printed to the exact specifications of customers‘ feet.
Customised consumer products
Consumer goods companies are increasingly eyeing plastic 3D printing as an option for mass customisation. Since 3D printing doesn’t require labour-intensive and costly tooling and can create complex objects cost-effectively, it enables the production of personalised products tailored to consumers.
One brand exploring 3D printing is Dr. Scholl‘s, the provider of foot care products. It has partnered with technology company Wiivv to make custom 3D printed inserts.
Using Wiivv Fit Technology, Dr Scholl’s offers a customisation app, which maps out 400 points on each user’s feet with a few phone photos. Though this process, which takes less than five minutes, inserts can be designed and then printed to the exact specifications of customers‘ feet.
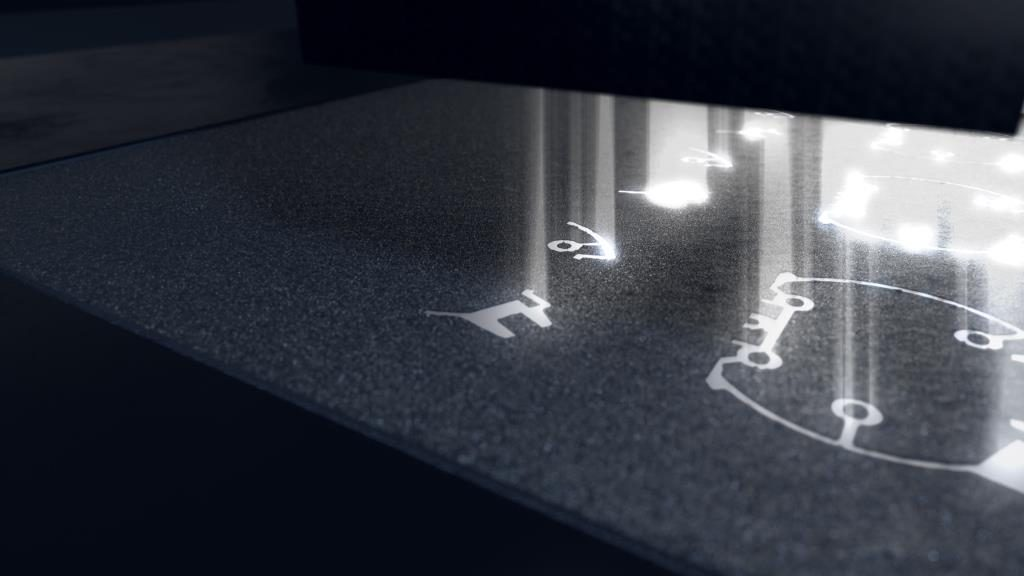
Although it’s unclear when the system becomes commercially available, the announcement is yet another indicator of the industrialisation of 3D printing technologies.
High-speed photopolymerisation
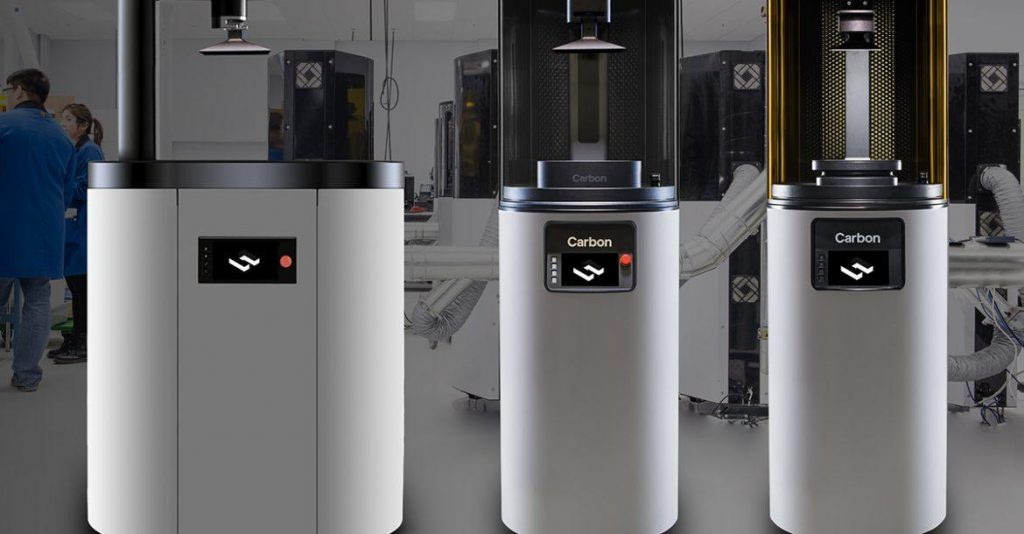
This technology has been forging ahead as a mass manufacturing process and the recent introduction of high-speed photopolymerisation has only accelerated this trend.
Almost all major players in this field have introduced systems capable of printing functional resin parts close to injection moulding volumes.
In 2014, Carbon introduced its high-speed Digital Light Synthesis technology, which evolved into a M2 3D printer capable of printing at the speed of 20 cm/hour.
Photopolymerisation, which includes the SLA and DLP processes, has evolved significantly over the last several years.
This technology has been forging ahead as a mass manufacturing process and the recent introduction of high-speed photopolymerisation has only accelerated this trend.
Almost all major players in this field have introduced systems capable of printing functional resin parts close to injection moulding volumes.
In 2014, Carbon introduced its high-speed Digital Light Synthesis technology, which evolved into a M2 3D printer capable of printing at the speed of 20 cm/hour.
One of the major barriers to the wider adoption of FDM for industrial applications is the size of the build envelope. This is a barrier the German company BigRep is repeatedly attempting to overcome with its incredibly large and highly capable line of 3D printers.
At formnext 2018, BigRep unveiled two next-generation 3D printers – the BigRep PRO (1005 x 1005 x 1005 mm) and BigRep EDGE ( 1500 x 800 x 600 mm) — geared towards industrial use.
Both systems are equipped with proprietary Metering Extruder Technology (MXT), which sets them apart from other large-scale options. This new extruder technology provides a clear separation between filament feeding, melting and extrusion, thus enabling faster printing speeds with greater precision and quality. For example, the BigRep PRO is said to offer five times the filament throughput rate and three times the average extrusion rate, compared to other FDM machines available on the market.
The MXT is optimised to work with professional-grade materials like ASA/ABS and nylon that BigRep is producing in collaboration with the German chemical company BASF.
Notably, the BigRep PRO incorporates state-of-art CNC control systems and drives by Bosch Rexroth, enabling IoT and data processing capabilities. This will ultimately help accelerate the printer’s integration into the Industry 4.0 vision.
Evolve’s STEP technology
More and more 3D printer manufacturers are setting their eyes on mass production, and Stratasys spin-off Evolve Additive Solutions is no different.
After almost a decade of development, the company unveiled its new production-speed “STEP” (short for Selective Toner Electrophotographic Process) technology for polymers last year.
Evolve’s STEP process offers a novel approach to volume production with additive manufacturing, not least because it is said to be 50 times faster than the fastest 3D printing technologies available.
What’s more, the company claims that the technology is capable of producing parts with quality comparable to those made with conventional methods, and not just in terms of aesthetic finish, but also strength. Additionally, STEP technology provides multi-material and full-colour printing capabilities.
Although Evolve is still two years away from commercialisation, their technology will be one to keep an eye on.
Stratasys’ SAF
The 3D printing industry mainstay, Stratasys, also continues to increase its presence in the rapidly expanding area of production-grade 3D printing systems. The company just presented the upcoming line of powder bed fusion (PBF) based 3D printers.
The new H Series Production Platform will be powered by Selective Absorption Fusion (SAF) technology specifically designed to meet the needs of volume manufacturing.
SAF is a powder-based 3D printing process. However, while SLS uses a laser to selectively fuse polymer particles, SAF does something entirely different.
SAF uses a counter-rotating roller to coat powder layers onto a print bed and then printheads selectively drop absorber fluid to form the part’s layer. The imaged layer is fused by passing an IR lamp over the entire span of the print bed, causing the selected regions to fuse.
What’s good about this new process is that it will reportedly offer high printing speed and scalability. Commercial availability of 3D printers based on SAF technology is currently expected in the third quarter of 2021.
If Stratasys’ SAF delivers on its vision, it could become a viable alternative to the established SLS and Multi Jet Fusion processes.
Polymer 3D printing trends
Polymer 3D printing market consolidation
The additive manufacturing industry has seen a spate of acquisitions and mergers over the last six months, many of which were in the polymer AM sector.
While M&A activity is nothing new in the AM space, recent announcements have something significant in common: production focus.
Here are some highlights of the recent M&A moves in polymer 3D printing:
- In September 2020, Covestro announced the intent to acquire the DSM Resins & Functional Materials line of business, including DSM Additive Manufacturing.
- In December 2020, Stratasys announced the acquisition of Origin.
- In January 2021, Desktop Metal announced the intent to acquire EnvisionTEC.
It’s encouraging to see companies coming together to strengthen their offerings and present compelling solutions for industrial AM production.
This desire to expand process and materials portfolios to include more options from a single parent source operating through a single distribution network will enable a lot more customer requests to be met.
Doing so on a large scale, with a focus on repeatability and reliability, is a major step forward for polymer 3D printing.
Using plastic instead of metal
Weight reduction is a particular goal for some industries like aerospace and motorsports. Making an aircraft or a vehicle lighter helps reduce fuel consumption and optimise a vehicle’s performance.
While these industries generally rely on metal lightweighting solutions to reduce weight, the recent advancements in polymer 3D printing materials offer some exciting opportunities. The ability to 3D print high-performance thermoplastics like carbon-fibre, ULTEM and PEEK can mean metals can be replaced with plastics in some applications.
According to one analysis, replacing aluminium aircraft brackets with PEEK alternatives can result in a 5% to 9% weight reduction, which can have a tremendous bottom-line impact on the fuel consumption of an aircraft.
Replacing a metal part with 3D-printed plastic can also be beneficial for speeding up the maintenance process. One service bureau has used Stratasys FDM Nylon 12CF carbon-filled thermoplastic to make a replacement for a metal machine part. 3D printing the spare part resulted in a superior component, produced much faster than its conventionally manufactured counterpart.
Things to consider when adopting polymer 3D printing in-house
Sustainability
Recycling and reuse of polymer 3D printing materials is an important factor to consider when adopting polymer AM in-house.
In filament-based 3D printing, recycling is commonplace, with many companies producing plastic filaments from recycled plastic.
However, while thermoplastics, like filament, can be easy to recycle by just remelting them, thermoset plastics cannot be remelted, which means they are unable to be recycled.
In powder-based polymer 3D printing, powder reuse is also not entirely straightforward. In most cases, you’ll need to mix ‘used-but-unfused’ powder with about 50% virgin powder, in order for it to be reused. For some high-performance powders like PEEK, the refresh rate is drastically reduced and, in some cases, none of the excess powder can be reused.
So how can you print sustainably with polymer 3D printing materials? One way is by minimising waste through better designs. Additionally, make sure to contact your local waste or recycling centre to see if they have the capacity to dispose of 3D-printed polymers safely.
More on this: How Sustainable is Industrial 3D Printing?
Post-processing
Removal processes, such as support removal, resin or powder removal, are the most commonly employed post-processing operations in polymer 3D printing. They are typically performed manually, which takes up a lot of time and labour resources.
Further complicating this stage is the fact that you may want to use several 3D printing technologies, each with its own post-processing requirements.
To improve post-processing operations, companies, like Rösler, PostProcess Technologies, AMT and DyeMansion, have been developing solutions to help AM users streamline post-processing.
Currently, the biggest trend is on creating end-to-end post-processing solutions, covering sorting, material removal and de-powdering, smoothing and dyeing, and inspection.
When adopting polymer 3D printing, understanding the post-processing requirements is imperative. Unoptimised post-processing can add a lot of cost to 3D printing operations, which can and should be avoided through automation.
Workflow management
Adopting polymer 3D printing in-house will also require you to consider approaches to managing operations, such as order management, cost calculation, production scheduling, inventory management, etc.
Many companies today either rely on solutions initially developed for traditional manufacturing or develop their software internally. Each approach often leads to siloed workflow, which lacks visibility and can’t be easily scaled.
Not to fall into the trap of an inefficient, unscalable workflow, a good practice is to implement workflow management and manufacturing execution solutions that have been developed with 3D printing requirements in mind.
Several options are available on the market today but only a few offer end-to-end solutions that cover the entire 3D printing workflow.
The future of polymer 3D printing
From realistic concept models to sturdy prototypes, ergonomic tools and functional end-use parts, the opportunities created by polymer 3D printing are immense.
Although some challenges remain to be overcome, such as expanding the material selection and ensuring the reduction of material costs, ongoing developments in polymer 3D printing will help companies further reap the benefits of the technology.
As the AM industry as a whole, and polymer 3D printing in particular, moves toward the production of end parts, we see 3D printable composites and high-performance thermoplastics gaining greater traction.
While polymer 3D printing won’t replace conventional processes, the technology will certainly enhance current manufacturing capabilities, further unlocking advanced industrial applications.