Have you ever thought about 3D printing flexible parts? If so, Thermoplastic Polyurethane or TPU, as it’s commonly known, is definitely a material to add to your list.
TPU 3D printing offers unique possibilities that are otherwise unachievable with other 3D printing materials like ABS, PLA or nylon. Combining the properties of both plastic and rubber, TPU can produce elastic, highly durable parts that can be easily bent or compressed.
In today’s tutorial, we’ll explore the benefits and applications of TPU, the technologies that support the material, as well as a few tips to help you make 3D printing with TPU as easy and efficient as possible.
What is TPU?
Thermoplastic Polyurethane (TPU) belongs to the family of thermoplastic elastomers and combines the best properties of thermoplastics and rubbers (thermosets).
You may be more familiar with the term TPE — or Thermoplastic Elastomer. Formerly the go-to material for flexible 3D printing, TPE is a very soft, rubber-like plastic that can be bent or stretched without deformation. However, its softness makes TPE a very challenging material for machine extruders to 3D print.
TPU, on the other hand, can be thought of as the newer version of TPE. TPU possesses rubber-like elasticity, high tear and abrasion resistance, high elongation at break as well as thermal stability.
In addition to this, TPU is also resistant to oils, greases, and a variety of solvents. Being firmer than TPE, TPU is therefore also much easier to 3D print with.
Applications
TPU has a wide range of applications. For example, it is a good option for 3D printing flexible functional prototypes or end-use parts that need to be bent and compressed.
Consumer goods
For consumer goods, TPU is ideal for producing accessories, such as phone cases, and footwear components.
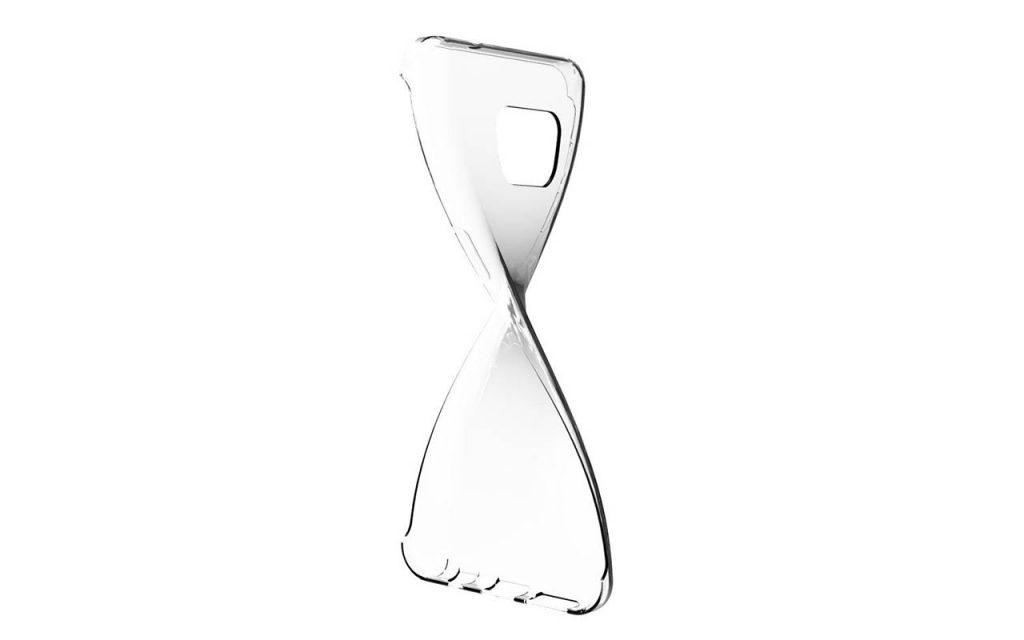
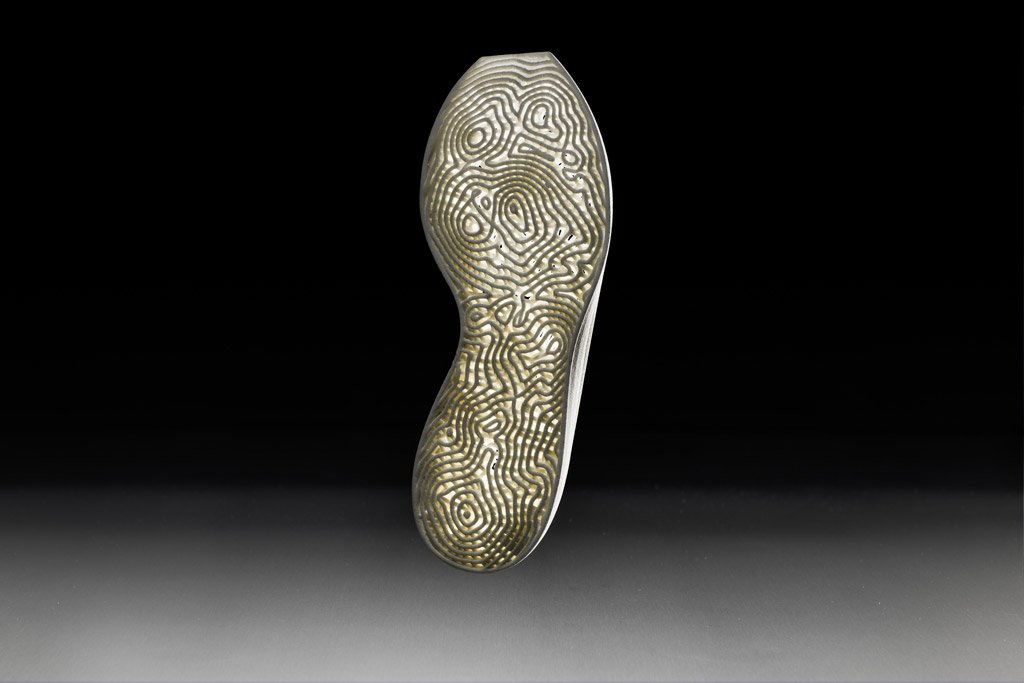
Medical
Another interesting application of TPU is in the medical sector. For example, the material can be used to create orthopedic models. In 2016, US-based company Graphene 3D Lab introduced a conductive TPU filament, suitable for producing flexible electronics, including wearable medical devices like wristbands.
Automotive
With its high chemical resistance to oils and greases, TPU is ideal for automotive applications like seals, gaskets, plugs, tubes and protective applications.
One innovative example is a 3D printed electric car produced by Chinese startup XEV Limited. The car is made up of around 100 parts, many of which were 3D printed with TPU alongside PLA and nylon.
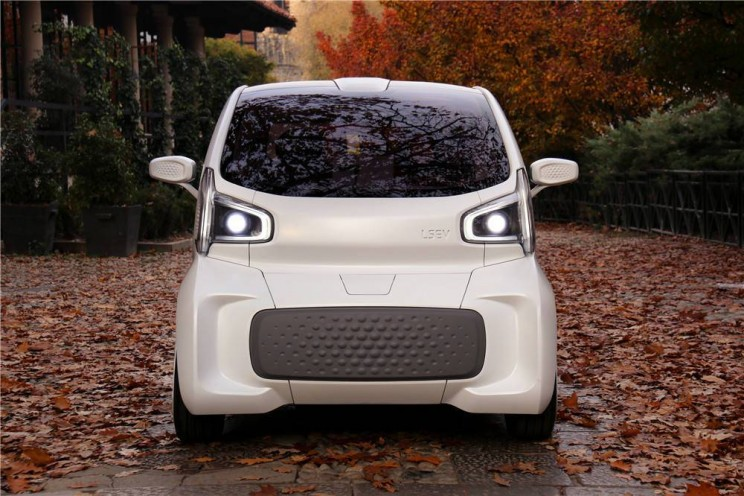
Available TPU Materials
Material Manufacturer | Material Brand Name | Shore A hardness | Key properties | Technology |
---|---|---|---|---|
3D Systems | DuraForm TPU Elastomer | Shore A hardness can be varied | Abrasion and tear-resistant
Easy to process Elongation at break 200% |
SLS |
Prodways | TPU-70A | 70A | High resolution
Elongation at break above 300% |
SLS |
Advanc3D | Adsint TPU 80 shA | 80A | Good abrasive and chemical resistance
Elongation at break 600% |
SLS |
Sinterit | Flexa Soft | 40-55A | Elongation at break 137% | SLS |
Sinterit | Flexa Black | 80-90A | Elongation at break 155% | SLS |
Sinterit | Flexa Grey | 70-90A (adjustable) | Elongation at break 137% | SLS |
Sinterit | Flexa Bright | 79A | Elongation at Break 317% | SLS |
LUVOCOM | LUVOSINT® TPU 92 Shore A | 88A | High strength and high abrasive resistance
Elongation at break 500% |
SLS |
Lubrizol | Estane® 3D TPU F70D-045TR UV | 70D | Low-temperature flexibility and UV stability | FFF, SLS, Multi Jet Fusion (MJF) |
Lubrizol | Estane® 3D TPU F50D-045SR GP | 50D | High stiffness with excellent chemical and oil resistance | FFF, SLS, MJF |
Lubrizol | Estane® 3D TPU F98A-030CR HC | 98A | Excellent mechanical properties, low warpage and shrinkage | FFF, SLS, MJF |
Lubrizol | Estane® 3D TPU F75D-035 TR UV | 75D | Offers high modulus and excellent processing attributes | FFF, SLS, MJF |
Ninjatek | Ninjaflex TPU | 85A | Abrasion resistance 20% better than ABS and 68% better than PLA Resistant to chemicals Elongation at break 660% |
FFF |
Ninjatek | Cheetah TPU | 95A | Great impact strength
Abrasion resistance 40% better than ABS and 76% better than PLA |
FFF |
Ninjatek | Armadillo TPU | 75D | Rigid, abrasion resistant, tough
Excellent bridging capabilities and virtually no warping |
FFF |
Polymaker | PolyFlex™ TPU95 | 95A | Easy to process
Elongation at break 330% |
FFF |
rigid.ink | rigid.ink TPU | 94A | Tough and durable
Elongation at break 500% |
FFF |
MatterHackers | MatterHackers PRO TPU | 95A | Resistant to abrasion, grease and oil | FFF |
Fillamentum | Flexfill TPU | 92A and 98A | Oil resistant with excellent inter-layer adhesion |
FFF |
3D Printing with TPU: The Technologies
If you want to explore 3D printing with this flexible material, there are two main technologies to choose from: Selective Laser Sintering (SLS) and Fused Deposition Modelling (FDM).
Let’s delve into the possibilities of each.
Selective Laser Sintering
Selective Laser Sintering (SLS) is a powder bed fusion 3D printing technology that uses a laser beam to selectively melt and fuse powdered material.
SLS offers many advantages for industrial manufacturing, as the technology is capable of producing functional parts with great mechanical properties. Furthermore, SLS requires no support structures, allowing free-form parts without any support removal marks. However, parts will require some form of post-processing to achieve a better surface finish.
Initially, the technology was used with various types of nylon but with recent advancements in material research, it’s now possible to sinter TPU powder.
Currently, there are a few manufacturers on the market that offer TPU powder with various degrees of shore hardness:
– 3D Systems offers its proprietary DuraForm TPU Elastomer, which is compatible with its Pro 60 HD-HS 3D printer.
– French AM specialist Prodways has TPU-70A in its material portfolio with an elongation at a break of more than 300%. With TPU-70A, shore hardness can be adjusted based on energy input.
– In 2017, German material manufacturer Advanc3D introduced the Adsint TPU 80 shA material, said to be the stretchiest material commercially available for SLS technology.
Design Tips when Using TPU powders
Minimum wall thickness
1.5 mm is the minimum wall thickness when using TPU powder. Parts 3D printed with 1.5 mm walls will be very flexible but you can also make your part more rigid by increasing the wall thickness to 3 mm.
Minimum feature size
When designing details for your TPU part, ensure that they are a minimum of 0.5 mm in size. For the visibility of embossed and engraved details, their height and width should not be smaller than 1.5 mm.
Complex designs
As a powder bed technology, SLS can create enclosed and interlocking parts, eliminating the need to assemble individually printed components. For this to be successful, keep in mind that the clearance between parts should be a minimum of 1 mm. For large objects, the clearance should be increased.
Escape holes
Hollowing your part may be useful, as it reduces printing time and saves material. However, when doing so, don’t forget to factor into your design holes with a diameter of at least 1.5 mm to help remove the powder stuck inside your part after the printing process.
Fused Deposition Modelling
FDM technology can also be used with TPU filaments.
There are two major benefits of using FDM instead of SLS when manufacturing TPU parts: firstly, FDM is less expensive and secondly, it is typically faster to produce TPU parts with filaments rather than with powders.
On the other hand, 3D printing with TPU filaments using FDM will result in a less dimensionally accurate part, with visible print layers that cannot be smoothed. Additionally, since TPU is a soft material, particularly when compared to ABS and PLA thermoplastics, TPU filaments can flex in the extruder mechanism, resulting in coiling of the filament and clogging of an extruder. However, the softness of the material is what makes the layer-to-layer adhesion in TPU prints strong and durable.
5 Tips for 3D printing with TPU filaments
Basic printer requirements:
- Extruder temperature: 225-250°C
- Type of the extruder: Direct Drive extruder is recommended
- Heated print bed: 50 ±10 °C
- Cooling: part cooling fan is recommended (medium or high setting)
- Enclosure: not necessary
- Build Surface: Kapton tape (PEI), blue painter’s tape
Printing Temperature
The recommended extrusion temperature range is between 225-250°C depending on the type of a 3D printer and a TPU filament you have. However, keep in mind that printing with higher temperatures will allow the filament to melt faster and to flow easier from a nozzle.
Speed
TPU typically prints best at slower speeds. It is a good practice to set half of the average speed (15 mm/s – 20 mm/s) to ensure high-quality prints.
Extrusion multiplier
Extrusion Multiplier is a 3D printer’s setting that allows you to control how much filament comes out of the nozzle or simply the extrusion flow rate. As TPU filaments can improperly extrude during the printing process, resulting in improper bonding of layers and perimeters. One way of dealing with this issue is to slightly increase your extrusion multiplier.
Retraction
Retraction is the mechanism in a 3D printer, which pulls the filament backward into the extruder as a means of preventing the oozing of the melted filament. This feature is very useful with rigid filaments like PLA and ABS, however, with TPU filaments, retractions can be challenging and can result in clogging. That’s why it is highly advisable to disable retraction to prevent stretching and compressing of the flexible filament in the nozzle.
Rafts and skirts
A raft is a throwaway horizontal surface on top of which a part is printed, and it is used to prevent warping. However, since TPU parts usually do not warp, rafts are not recommended when 3D printing with TPU, not at least because they can cause additional printing issues due to high printing speeds. In contrast, it would be wise to print a skirt — a few loops of material around the print — to check the flow of the filament and ensure the success of the first few layers.
Conclusion
TPU is a highly useful material, providing unique properties and a wide range of possible applications.
However, 3D printing with TPU can be tricky due to the unique properties of the material, which is why it’s important to understand the possibilities and limitations of TPU before printing. With this guide, we hope that you’re now well on the way to successfully producing your 3D-printed TPU parts.