3D printing is heralded as one of the technologies that will enable smart, sustainable manufacturing. While 3D printing is considered as a less wasteful process, the questions remain open: where does 3D printing stand on the green scale? Is it indeed environmentally friendly?
Today’s article will seek the answers while exploring misconceptions and facts surrounding the environmental aspect of the technology.
3D printing as a sustainable manufacturing technology
As we strive for a sustainable future, businesses are looking for ways to optimise their manufacturing processes to reduce energy consumption and waste – an approach known as sustainable manufacturing.
3D printing is often viewed as one of the key sustainable technologies, primarily due to two benefits: it facilitates more efficient designs and creates less waste. Let’s dive deeper into these benefits.
3D printing as a design-efficient technology
3D printing allows engineers to explore new design practices, like topology optimisation, with the opportunity to create more efficient, lightweight parts.
Topology optimisation software applies computational algorithms to a pre-existing design in order to optimise its shape and weight.
For systems where energy consumption is impacted by the system’s weight, lighter, optimised parts lead to the long-term benefit in fuel savings. Every gram removed from cars’ or aeroplanes’ weight translates to fuel that is never burned – and therefore CO2 that is never emitted into the atmosphere.
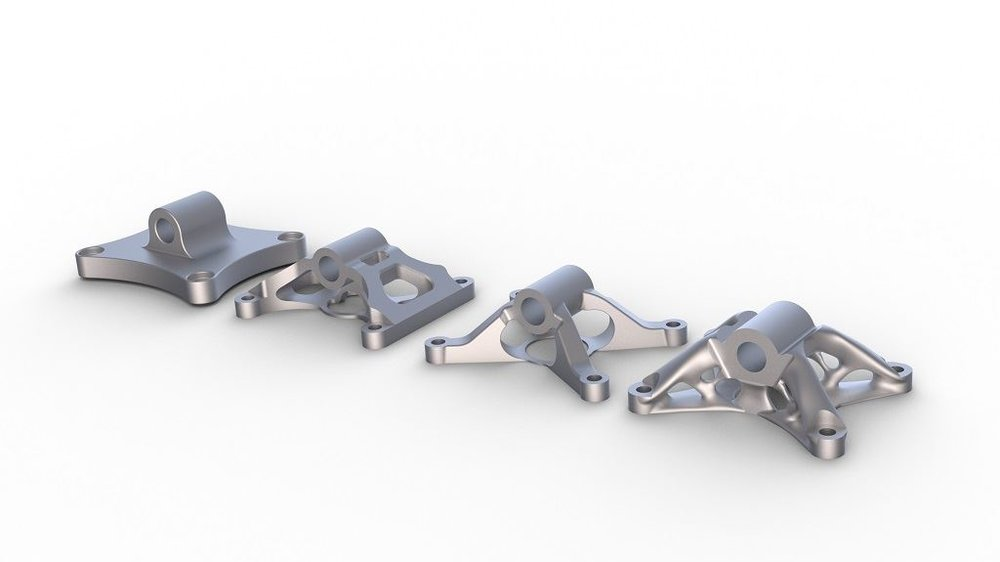
The researchers estimated that by replacing a number of routine components with topology optimised 3D-printed parts, like this bracket, overall aircraft weight could be reduced by 4 to 7 per cent, with fuel consumption lowered by as much as 6.4 percent.
This means that weight reductions in relatively small components – multiplied over the hundreds to thousands of such parts used in an aircraft or fleet – can lead to real savings, felt in greater energy efficiency over the service life of a product.
Environmental impact of part consolidation
In addition to using topology optimisation, companies can improve components’ designs, consisting of several pieces, by redesigning and 3D printing them as a single unit. This practice is known as part consolidation and offers multiple benefits.
Firstly, it reduces the number of parts that need to be designed and manufactured into the final assembly. Secondly, it simplifies the assembly process because fewer parts need to be welded or screwed together.
Finally, consolidation allows for a better performing part that exhibits increased durability, due to having fewer seams and tighter tolerances. Reduced part interfaces also mean less vibration and fewer paths for leaks.
These benefits contribute to achieving sustainability goals as well. To date, the most impressive example of driving sustainability through an additive manufacturing (AM)-enabled design comes from General Electric (GE) and its work on new Catalyst aircraft engines.
With the Catalyst, GE took a design that originally required 855 engine components and reduced it down to 12 titanium 3D-printed parts that retain all the functionality of older models. The changes significantly reduced both the weight and cost of production.
These important savings, however, could decrease emissions dramatically. GE estimates that the improvements made possible by 3D printing help to reduce overall weight by 5 per cent and improve brake-specific fuel consumption by 1 per cent.
The implications of such a reduction are amplified by GE’s scale: the company’s technology already powers a huge proportion of all aviation. The more the Catalyst will be integrated into the company’s overall product mix, the greater the impact will be in terms of emissions saved.
Is 3D printing less resource-wasteful than traditional technologies?
The short answer: it depends on which technology 3D printing is compared to. When compared to CNC machining, which has a similar value proposition of economic low-volume production, 3D printing has an edge.
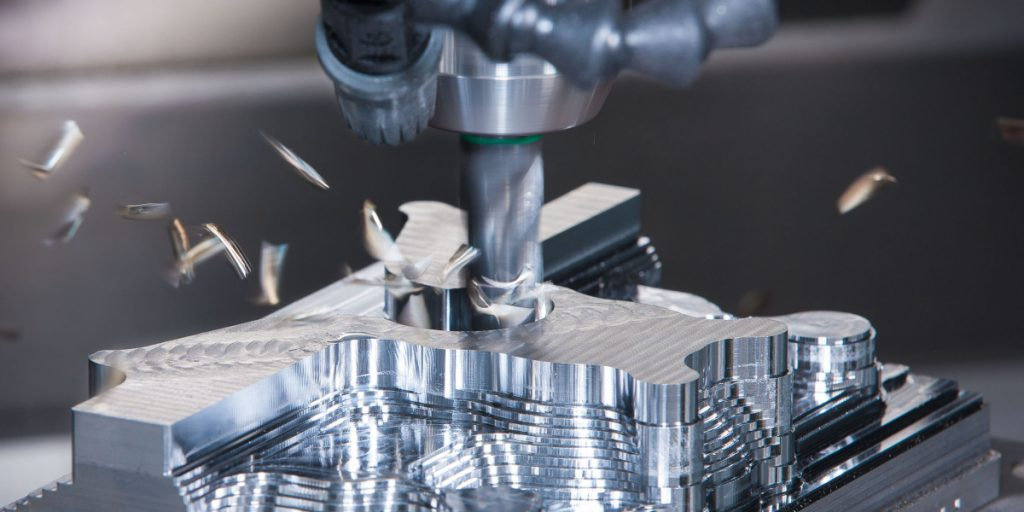
Simply put, the technology creates an object by successively bonding thin layers of material, each being a cross-section of the final part. This allows 3D printers, depending on the process, to melt, fuse, bind or sinter the exact amount of material required for the part.
With a subtractive process like machining, the material is cut away from a solid block to create a final part. In many cases, only a small percentage of the material goes into a final part, with the cut-away material waste often reaching more than 50 per cent.
Reducing this waste, by switching to 3D printing, is one of the benefits that makes the additive technologies so attractive.
Another technology 3D printing is often compared to is injection moulding. While injection moulding is nearly a zero-waste process, it tends to be resource-consuming when low volumes of parts are needed.
In a bid to amortise high tooling costs, it’s not uncommon for manufacturers to injection mould more parts than necessary, thus keeping the surplus part inventory. This results in added inventory holding costs and associated wastage of raw material.
Compared to injection moulding, 3D printing allows manufacturers to produce small batches of parts, without having to worry about tooling at all. Ultimately, it means that 3D printing can produce the exact amount of parts that were ordered, saving raw material and inventory space.
Waste streams in 3D printing
That said, 3D printing processes are not inherently wasteless. There are two key sources of waste, one being post-processing waste and the other – failed prints.
Due to the design considerations, parts designed for 3D printing usually require supports – structures that help to prevent part deformation during the 3D printing process.
After the process is complete, supports need to be removed. Waste, resulting from supports, is typically not huge but still needs to be considered.
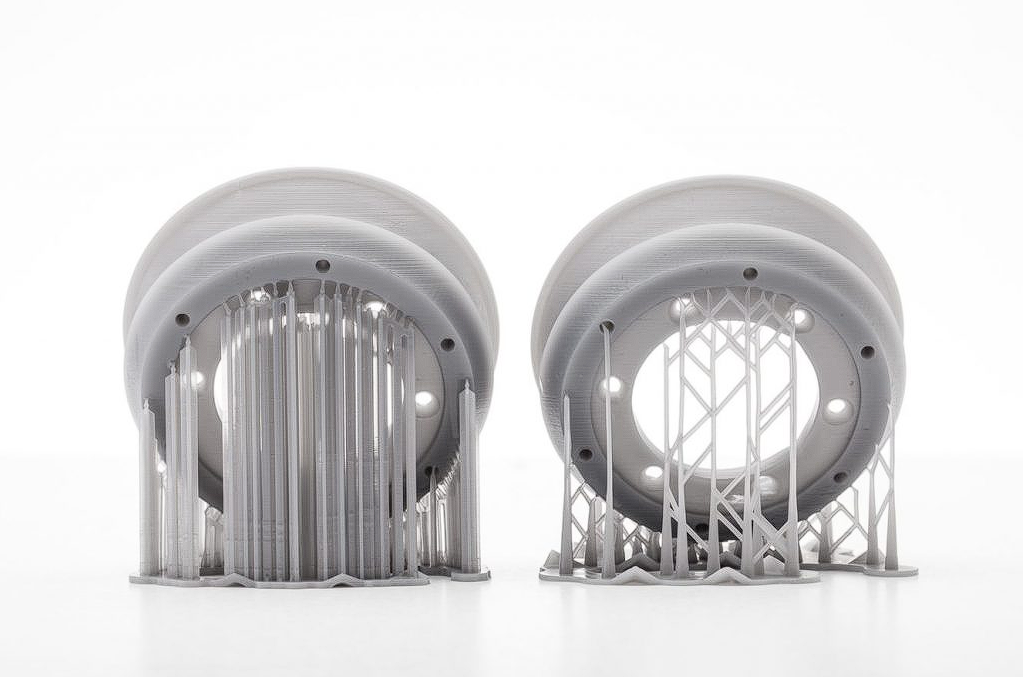
For example, in metal powder bed fusion (PBF), supports can generate around 10 per cent of waste. However, with a good design approach, aimed at minimising supports, it is possible to reduce this number to around 2 per cent.
Another waste-generating step in post-processing is surface finishing. For polymer 3D-printed parts, the amount of this kind of waste is negligible.
On the other hand, the post-processing of some metal 3D-printed parts can generate a much larger amount of waste. This is particularly the case with low-resolution processes, like wire-based Direct Energy Deposition, where parts need to be machined to achieve near-net-shape. An example of wire DED waste is shown in the image below.
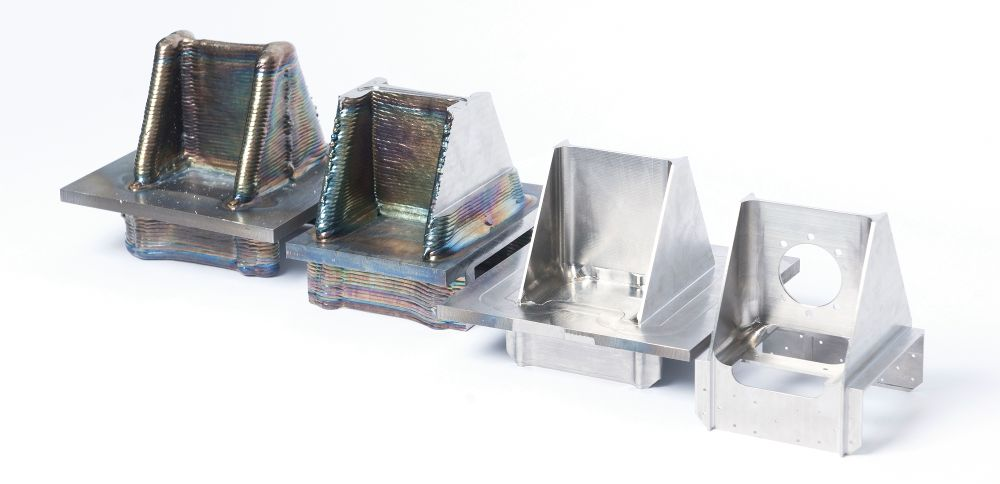
Failed parts
Failed prints are another large source of waste. There’s still a lack of understanding of how to best leverage design for AM, which differs from traditional design approaches.
Without this expertise, creating a successful design that won’t fail, while keeping the process cost-effective, is challenging. Too often engineers must scrap multiple parts before they find the optimal build orientation and support strategy.
Luckily, this issue is being addressed by using advanced simulation software. Such software provides engineers with a glimpse into how a part will behave during the printing process. It means they can predict printing issues that would lead to a failed print and make up for them at the design stage.
Summing up, 3D printing can indeed be less wasteful when compared with machining and injection moulding. While it has its own waste streams, in most cases they can be greatly minimised by taking them into account at the design and build preparation stages.
With support structures optimised and failed prints prevented with the help of simulation, the possibility to establish a nearly wasteless 3D printing process is within reach.
3D printing and waste management
Another important sustainability factor to consider is the recyclability and reuse of 3D printing materials. This issue is particularly pertinent to the metal 3D printing industry, where material prices are high and misconceptions persist that metal in the powder form cannot be reused.
In metal PBF, after the printing process is complete, some amount of metal powder remains unmelted and can be sieved and then blended with a new powder in a specified proportion. However, many companies remain sceptical about powder recycling and often dispose of all old powder.
In fact, multiple studies have proved that proper recycling and reuse of metal powders has minimal effect on the mechanical properties of the material.
This approach enables the powder-based process to be more efficient and economical. That’s why metal 3D printer manufacturers and technology companies are also developing sieving solutions for metal 3D printing, which are now an industry norm.
In addition to AM powder reuse, several companies have also developed approaches to recycling scrap material into a powder suitable for 3D printing.
For example, 6K, formerly Amastan Technologies, is contributing to a fully circular economy with its UniMelt process. It uses a proprietary method of mechanically grinding scrap from machining, like turnings and swarf, as well as AM supports and rejected parts into fine particles. These are then fed through a plasma system to produce high-quality powders.
With solutions like the one from 6K, the metal AM industry is getting closer to using 100 per cent of the materials that enter the metal AM supply chain.
Reusing thermoplastics
Despite the progress in metal recycling, most recycling initiatives take place in the polymer 3D printing space. Many companies today produce plastic filaments from recycled plastic. Among them are companies like GreenGate3D, Filamentive, NefilaTek, Refil and RePLAy 3D that are producing fully or partially recycled filaments.
In one example, 30,000 water bottles were recycled into filament to 3D print a public structure in Dubai (above). The pavilion demonstrates how 3D printing can be applied to creative structures using materials that would otherwise be thrown away.
Waste management in resin 3D printing
While thermoplastics, like filament, can be easy to recycle by just remelting them, the process for recycling resin materials doesn’t currently exist.
Resin materials that are used in Stereolithography and material jetting processes, tend to be viscous, and a chemical reaction, like an application of energy from a laser, causes the materials to solidify. The resulting object cannot be recycled back into original material for re-printing. Once made, it’s done.
This means that all scraps from resin 3D printing, including support structures and failed prints, are essentially unrecoverable waste.
Waste management in SLS
The reusability of polymer powders used in the Selective Laser Sintering process is also not entirely straightforward.
Normally, the unfused support powder in an SLS machine is the same material used to print a part, and it tends to be expensive. Of course, this wouldn’t be a problem if the powder could be 100 per cent reused, which is currently impossible.
One reason is that, in the SLS process, polymers get exposed to high heat for long periods of time, thus undergoing chemical changes that make their sintering characteristics much less predictable.
Currently, the only way to overcome this issue is by mixing ‘used-but-unfused’ powder with about 50 per cent virgin powder, in order to be reused. For some high-performance powders like PEEK, the refresh rate is drastically reduced and, in some cases, none of the excess powder can be reused.
As estimated by one service provider, out of 500 kg of PA 2200 (nylon) powder it buys per month, ‘25% becomes a part, 25% is waste and 50% is reused for refreshing the next build’.
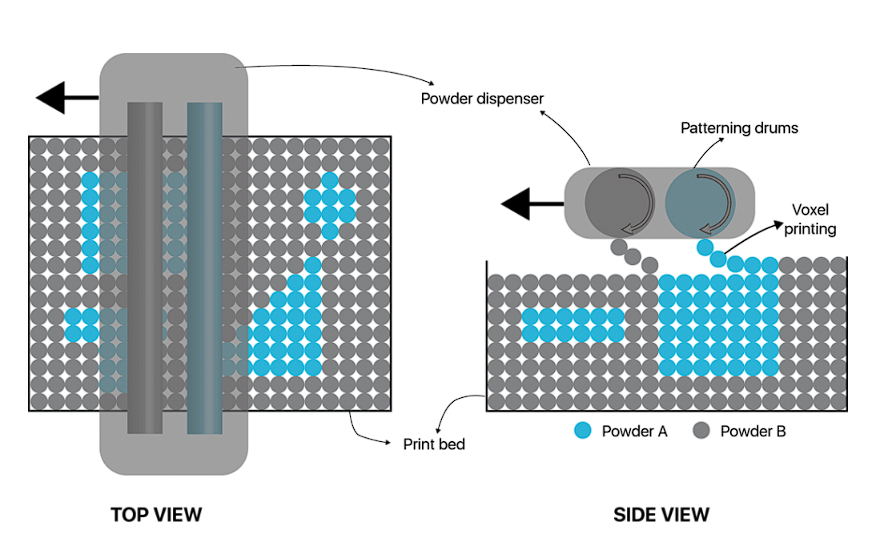
Introducing a machine that can use cheap support material and a second material for part printing, could make the SLS process much more sustainable. One company developing such a solution is Aerosint, a Belgian start-up that has developed a multi-powder deposition SLS technology.
However, Aerosint’s technology hasn’t been commercialised yet, so it will take time to see how feasible Aerosint’s process is and to assess its environmental implications.
Energy consumption in 3D printing
Any industrial process requires energy to run, including 3D printing. From a sustainability standpoint, energy consumption rates directly correlate with environmental considerations, like CO2 emissions.
3D printing, particularly with metals, is by no means a low-energy technology. However, some studies show that it can be more energy-efficient than most conventional manufacturing processes.
A study, conducted by metal 3D printer manufacturer, Digital Alloys, compared the energy consumption of different metal 3D printing technologies with CNC machining.
At the manufacturing stage, energy consumption is indeed larger with metal 3D printing processes, particularly laser PBF.
However, when considering different factors, like material waste, the possibility of material recycling and post-processing, it’s been shown that machining is the most energy-consuming process, due to the amount of material waste – (in Digital Alloys’ example it was more than 90 per cent).
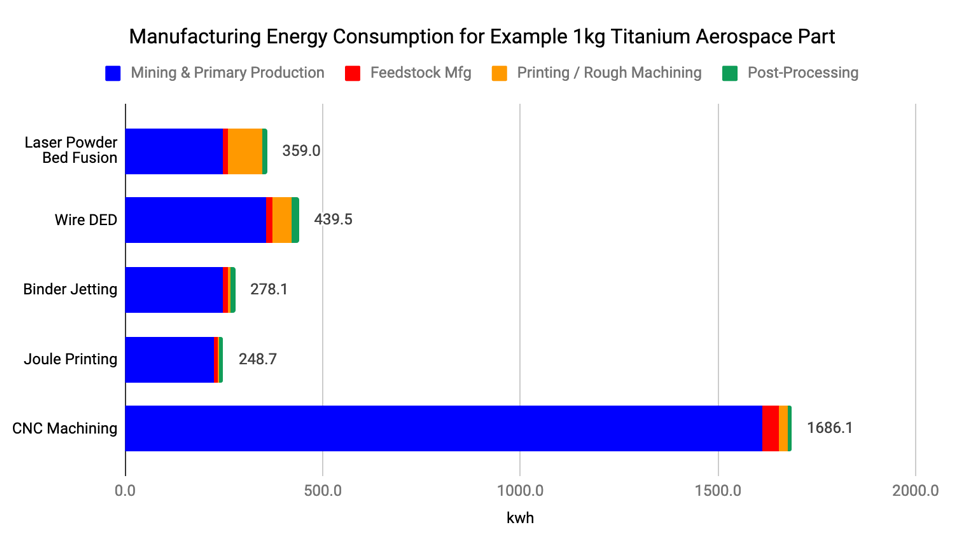
That said, not all agree that metal 3D printing is more energy-efficient than traditional technologies.
Timothy Gutowski, head of MIT’s Environmentally Benign Manufacturing (EBM) research group, states that ‘additive processes tend to be more energy-intensive … because they’re slower. They use a lot of energy to produce the same amount of product.
In fact, most 3D printing processes are something like seven orders of magnitude more energy-intensive than high-volume conventional manufacturing processes’, he explains in an interview with The Fabricator.
The truth, as always, lies somewhere in between. While 3D printing can be energy-intensive, choosing the application suitable for the technology and optimising its design will help to offset high energy consumption. It will also result in an overall energy-efficient system, where this part will be used.
On the way towards sustainability
With so many AM technologies out there, there’s no simple answer to the question of 3D printing’s sustainability. Some processes have the drawback of non-recyclable materials, while others are plagued by high energy consumption.
What’s encouraging, however, is the fact that 3D printing tends to be more resource-saving, particularly compared to subtractive technologies. And it also opens the door for more efficient designs that contribute to lowering manufacturing and inventory requirements and, ultimately, help to reduce fuel consumption.
Our verdict is that 3D printing is not entirely ‘green’ technology, but with the right approach, it can come closer to becoming an incredibly powerful sustainable manufacturing solution.
Source: https://amfg.ai/2020/03/10/how-sustainable-is-industrial-3d-printing/