Several years ago, the hype around the 3D printing industry seemed deafening. Commentators declared the arrival of a new technology capable of revolutionizing industries across the board, from medicine to product development to manufacturing. The possibilities were undeniable, despite the youth of the technology and the relatively low number of use cases that were viable at that point.
Since that early hype cycle, 3D printing processes have matured steadily, and we’ve now begun to see 3D printing tools, once accessible only to a few high-tech industries, made available to a broader variety of businesses.
3D printing, also known as additive manufacturing, creates three-dimensional components from CAD models. It mimics the biological process, adding material layer by layer to create a physical part. With 3D printing, you can produce functional shapes, all while using less material than traditional manufacturing methods.
The result of the wider availability of 3D printing is that a huge number of industries are beginning to feel the disruption. As the 3D printing workflow empowers both individuals and organizations to take control of their own design and manufacturing processes, more and more use cases are springing up.
Manufacturing & Engineering
1. Automobiles
The automotive industry has been tapping the potential of 3D printing for decades already. 3D printing is extremely useful in rapid prototyping and has proved capable of significantly reducing design times and lead times on new car models.
3D printing has also augmented manufacturing workflow within the industry. Custom jigs, fixtures, and and other tooling that might be required for a single car part, particularly when high-performance machines are concerned, once required an array of custom tools, adding cost and making the process as a whole more and more complex.
With 3D printing, custom jigs and other low volume parts can be created directly for the production line. Manufacturers can cut lead times by up to 90% and lower risk with the integration of 3D printing processes. Through streamlining with in-house production the manufacturing process as a whole grows more efficient and more profitable.
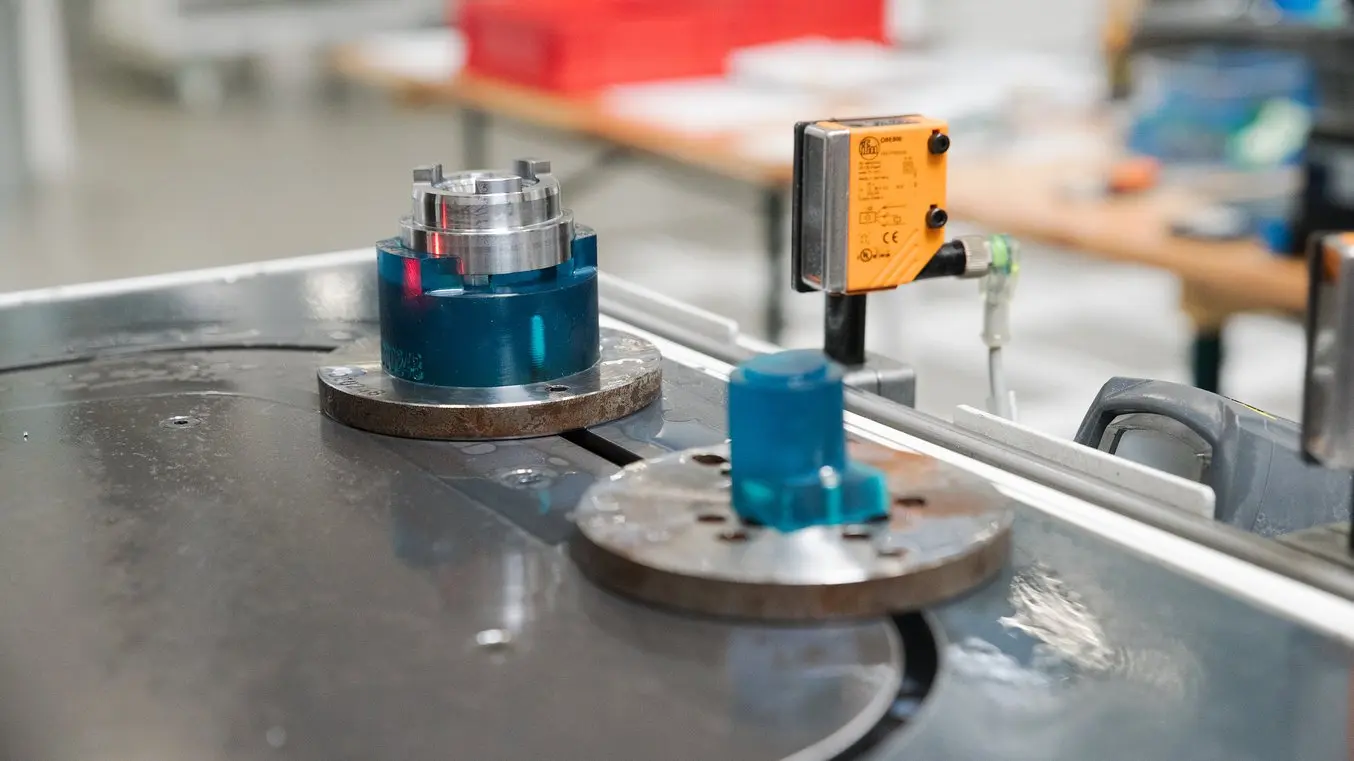
As the quality of the digital workflow continues to increase, as materials get better and processes more affordable, we will see more and more 3D printed parts in cars, increasing the scope for design customization and resulting in better performance. A little further down the line still, but some companies are already working on fully 3D printed cars.
Urethane Cast Auto Parts With Water Transfer Printed Carbon Fiber Pattern
2. Jewelry
3D printing is instigating a design revolution in jewelry. Creating 3D printed pieces that had a comparable look and feel to traditionally handcrafted and cast jewelry used to be a challenge. However, following the latest round of advances in specialist high-end 3D modeling programs, and with more printable materials on offer, more and more jewelry designers now prefer to 3D model and print their designs over traditional handcrafted methods.
Jewelry 3D printers create pieces from resin or wax, based on the 3D model of the jeweler’s design. Digital models can be easily edited, which makes prototyping jewelry with 3D printing incredibly cheap and convenient.
The buying experience is made more tactile as a result—clients can now try on prototypes of pieces they have helped design to ensure it looks and feels just right before purchasing.
The final designs can then be 3D printed and cast in a mold using the same workflow as with traditional jewelry. The results can be stunning:
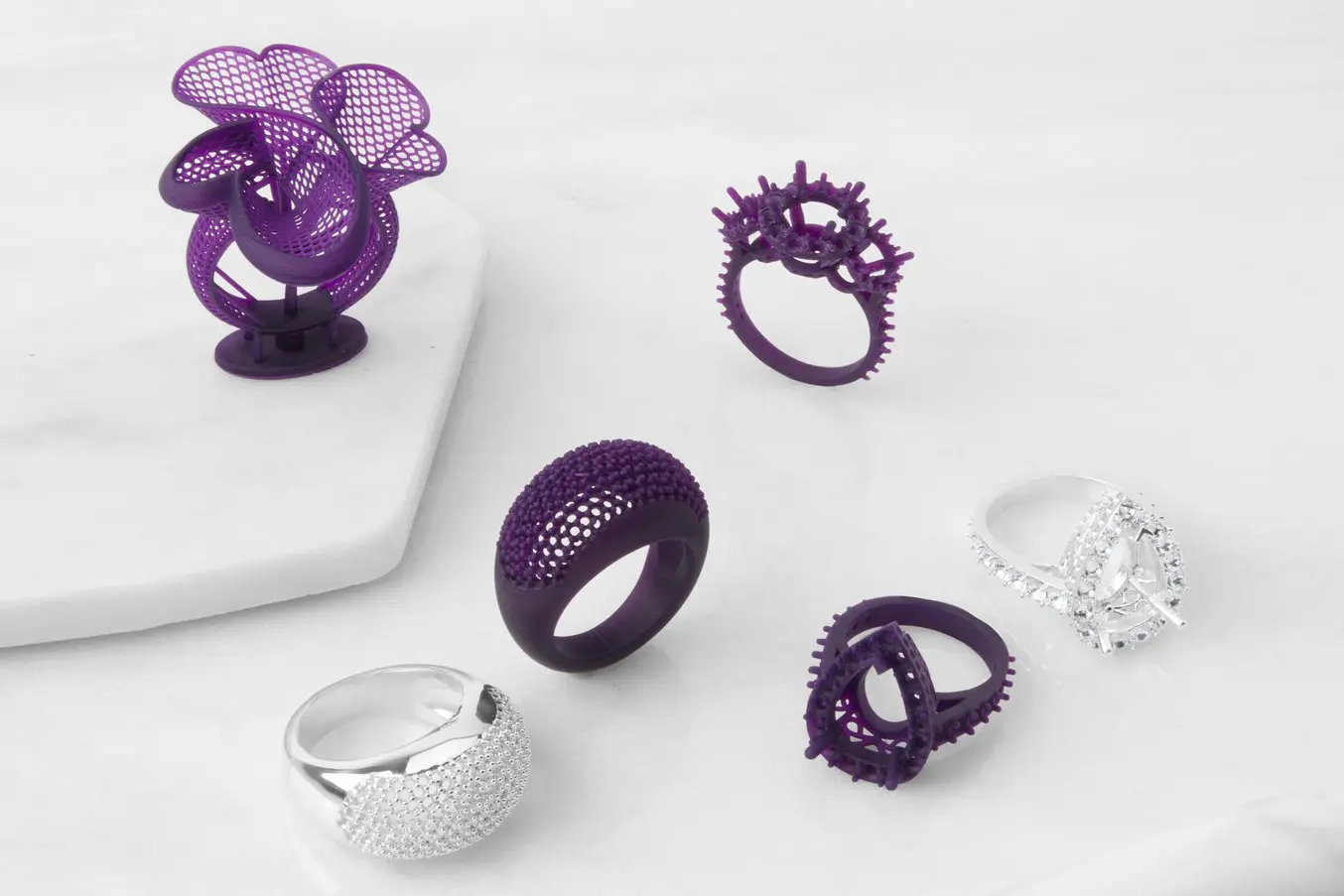
With the digital workflow complementing traditional production methods, and more new designers entering the workshop equipped with CAD/CAM skills, custom jewelry is rapidly becoming more accessible, enabling jewelry makers and retailers to forge closer relationships with their customers.
DLP 3D Printed Wax Pattern Models for Casting
3. Onshoring
Anything with so much power to alter design and production methods as 3D printing is bound to make waves in manufacturing. But there are potential advantages to embracing 3D printing in this field that are harder to visualize.
One of these is the onshoring of manufacturing. In recent decades, there has been a pronounced decline in US manufacturing as firms moved operations overseas to take advantage of the lower cost of labor. The commercial sense in this move is undeniable, as “a tool made in China or Vietnam can cost anywhere from $10,000 to $50,000 less than a tool made in the US.”
Offshoring, nevertheless, has its drawbacks on the design and production process. Lead times are frequently long, importing products from overseas is costly and environmentally unfriendly.
3D printing, with its ability to produce more complex designs, has the potential to turn onshoring back into an attractive prospect. Its usefulness to the design process, capacity to improve lead times dramatically and raise efficiency, all make in-house production feel viable again.
4. Spare & Replacements Parts
The effects of losing or breaking parts of products or devices can range from the inconvenient to the disastrous.
3D printing will consign the days of having to pay exorbitant repair costs, or else throw away a mostly functioning device, to the past, by enabling consumers to produce replacement and spare parts.
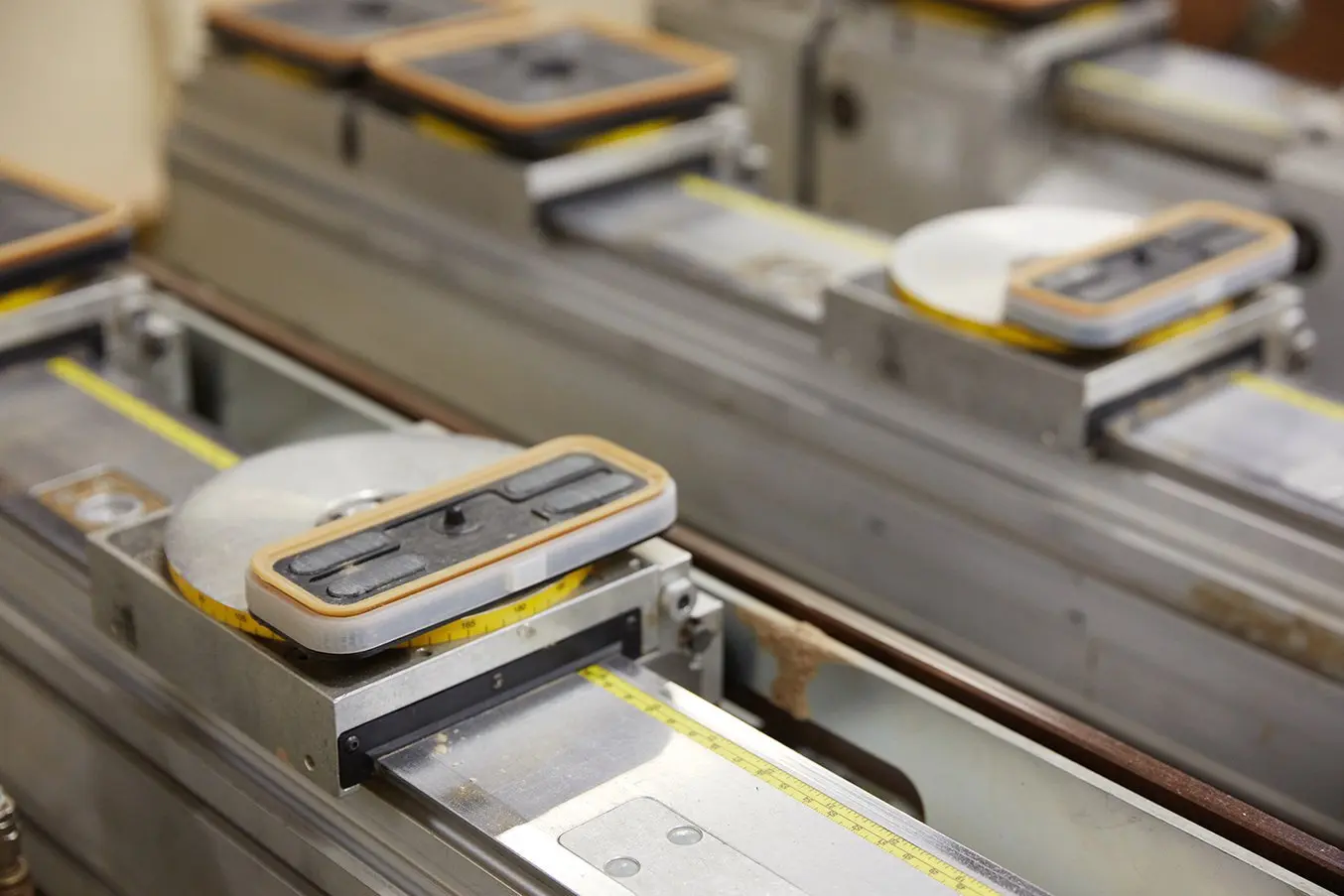
The digital workflow means that costly storage of rarely-ordered replacement parts will no longer be an issue for manufacturers, and consumers will stand a chance of having even their out-of-production components replaced.
5. Aerospace
Minimizing weight is a primary way in which 3D printing has enabled the aerospace industry to make a considerable saving. The lower volume of components required in a 3D printed construction of a part leads to parts that are lighter overall—this seemingly small change to production positively affects an aircraft’s payload, emissions, and fuel consumption and speed and safety, all the while markedly reducing production waste. As in numerous other fields, the workflow also allows the production of components simply too complex for traditional methods to handle.
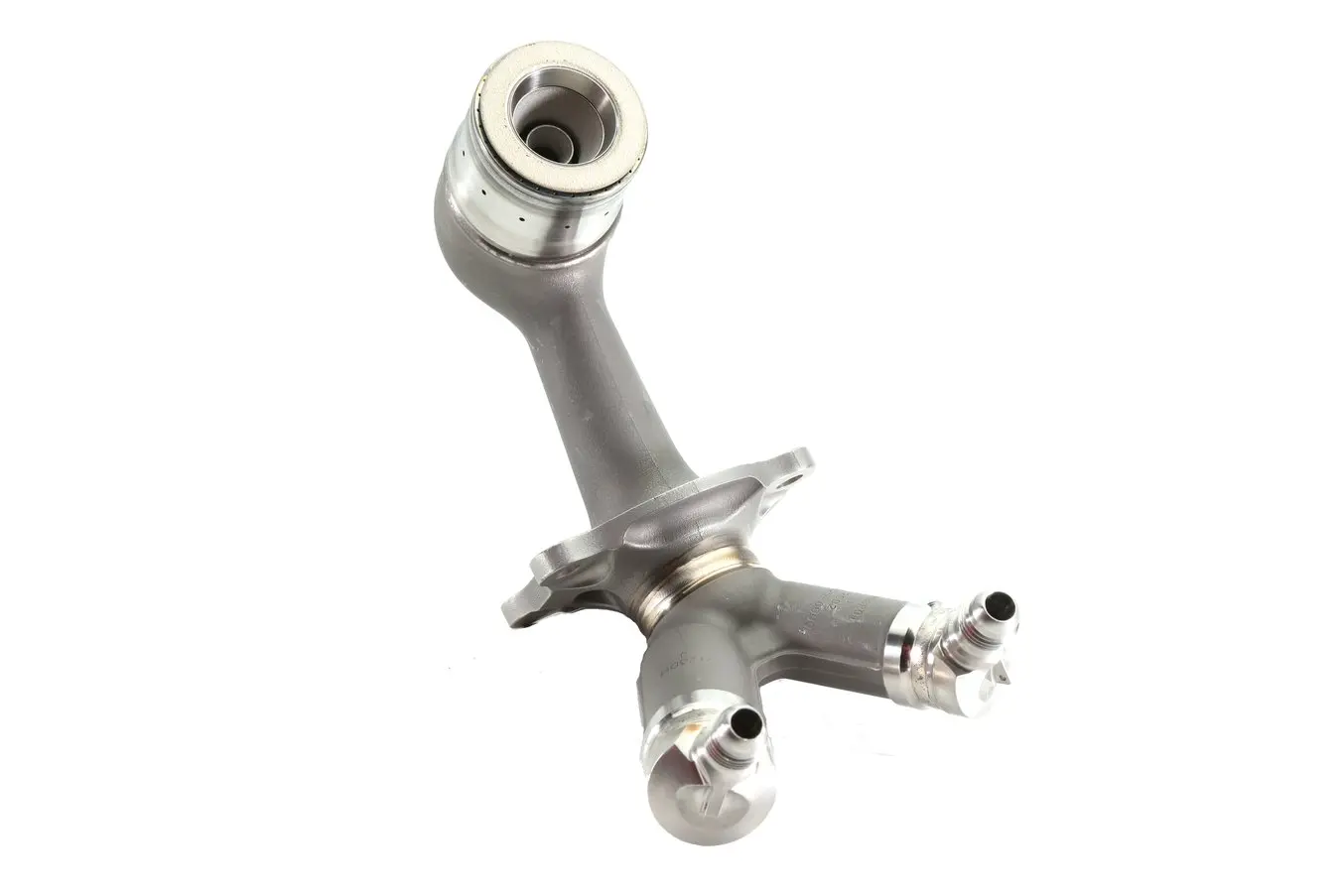
The likes of GE, Boeing, and Airbus have endorsed the value of 3D printing, and are already incorporating thousands of 3D printed parts into their vessels.
SLA 3D Printed Aircraft Engine Presentation Assembly Models
6. Glasses and Eyewear
Having to cater to all manner of face shapes, eyewear is also an industry that stands to benefit distinctly from 3D printing’s limitless capacity for customization. New designs intended to optimize both comfort and quality of design can be, as elsewhere, rapidly prototyped using 3D and produced at a lower cost and at greater convenience to the customer.
The results are lighter, more comfortable eyewear, made with minimal waste incurred. Some companies in the field are even using the attributes of 3D printing production to encourage customers to design their own glasses, excellent for generating brand loyalty and empowering consumers.
MJF 3D Printed Full-color Nylon Glasses Frame
7. Shoes
The sport-footwear industry has long relied on technology to optimize the performance of their products, and with the digital workflow they have more options than ever in customization.
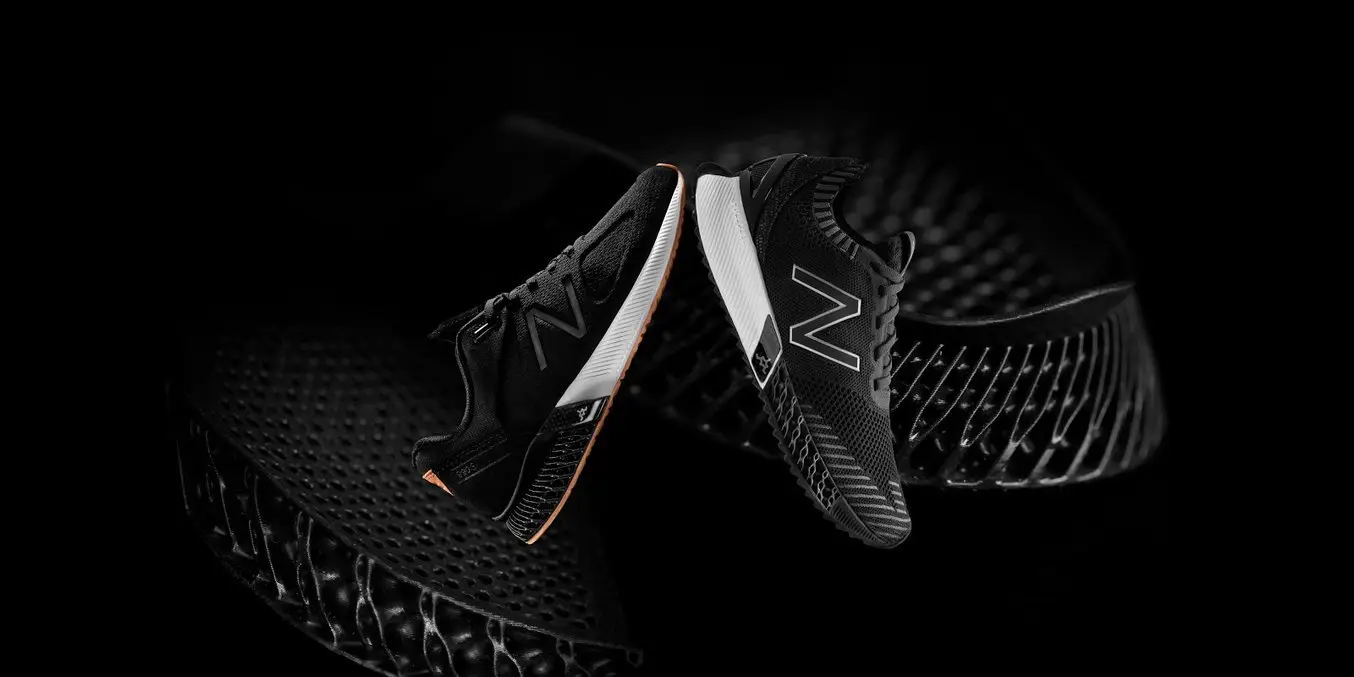
Large brands like New Balance, Adidas, and Nike, having recognized the power of additive manufacture, intend to mass produce custom midsoles made from 3D printed materials. As in other industries, the digital workflow will augment traditional methods of manufacture here—critical, highly-customized components of each product will be entrusted to the 3D printing, and the rest left to traditional means.
In a field with such a passionate consumer-base, 3D printing also stands to empower customers directly. It will enable consumers to design their own shoes, for both personal and widespread consumption. The viral potential of this aspect of 3D printing has already been seized upon by brands.
First Fully SLS and FDM 3D Printed Sneakers using TPU
8. Fashion and Smart Clothing (On the Horizon)
One area in which the commercial and artistic potential of 3D printing will likely collide is in the field of fashion and smart clothing. As the pallet of materials and textiles usable in the 3D workflow increases, designers will be afforded an immense range of new possibilities.
Not only can 3D printing technology alter the production of textiles—it will also provide the opportunity to create new textiles that are, for example, bulletproof, fireproof and capable of retaining heat. This particular branch of 3D workflow has yet to be perfected, but in the near future, we will see 3D printed clothing graduate from museums and haute couture to the boutique.
Artists empowered by the workflow have also used 3D smart clothing as “personalized, wearable, data-driven sculpture” with an artistic purpose.
SLA 3D Printed Custom Crystal Fairy Dress with Clear Resin
9. Model making
Model making is another niche practice to which the 3D workflow is ideally suited. Where realistic reproductions were once inordinately expensive or impossible to model, the quality of detailing and finish possible through 3D printing methods has made the production of realistic, detailed miniatures and scale models more affordable and easier.
CAD can make light work of formerly complex modeling challenges, empowering designers to essentially reverse engineer a structure as complex as an engine from 3D scans or SpaceX rockets.
The in-house production aspect of the digital workflow enables a business that revolves around custom modeling to scale in a traditionally niche market. For example, DM-Toys’ extensive integration of desktop 3D printers has enabled them both to disrupt the long-standing European model railway market, and deliver to customers more quickly and more cheaply.
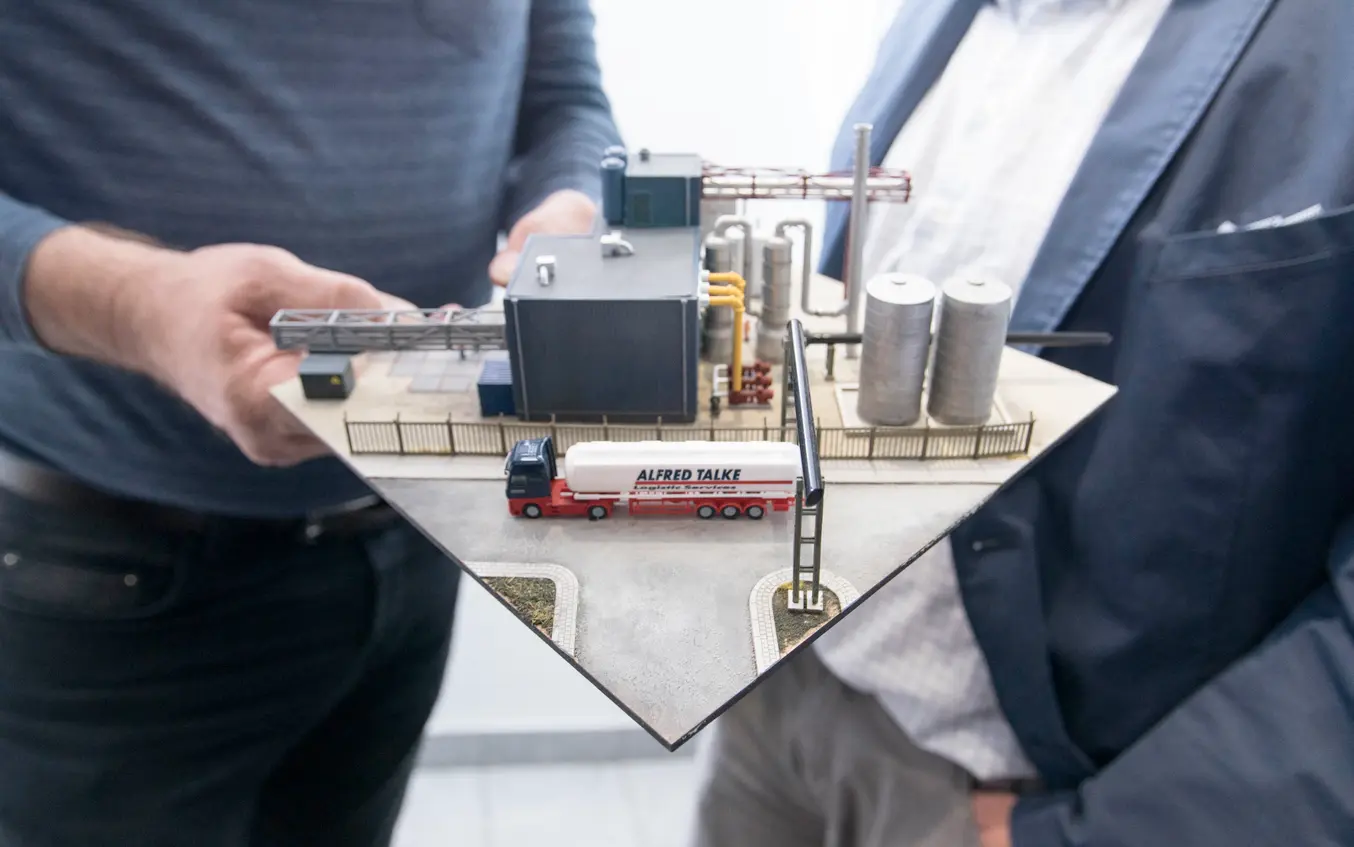
SLA 3D Printed Train and Train Bridge Resin Models for a Railfan
Healthcare
10. Audiology
The versatility and vast degree of customization possible through 3D printing means that it’s of great use in the spheres of medicine. We’ve seen it beginning to transform the audiology space already, hearing specialists and ear mold labs has been using the technology to manufacture high volumes of custom ear products like hearing aids, protective plugs and earphone for years.
3D printing makes for an excellent match for audiology, as it offers customization possibilities at no extra costs, which used to be complex and expensive using traditional methods.
As the technology becomes more affordable, we will see more and more consumer applications, like custom earbuds, appear: the process will be as simple as walking into a store, getting your ears scanned, and having your custom earbuds 3D printed.
As with jewelry, the 3D printing can produce quantities of complex designs at a low cost while cutting lead times. It can all be managed from a printer small enough to fit on a desktop. Audiologists are seeing manufacturing costs go down, their need for outsourcing reduced (key for smaller businesses).
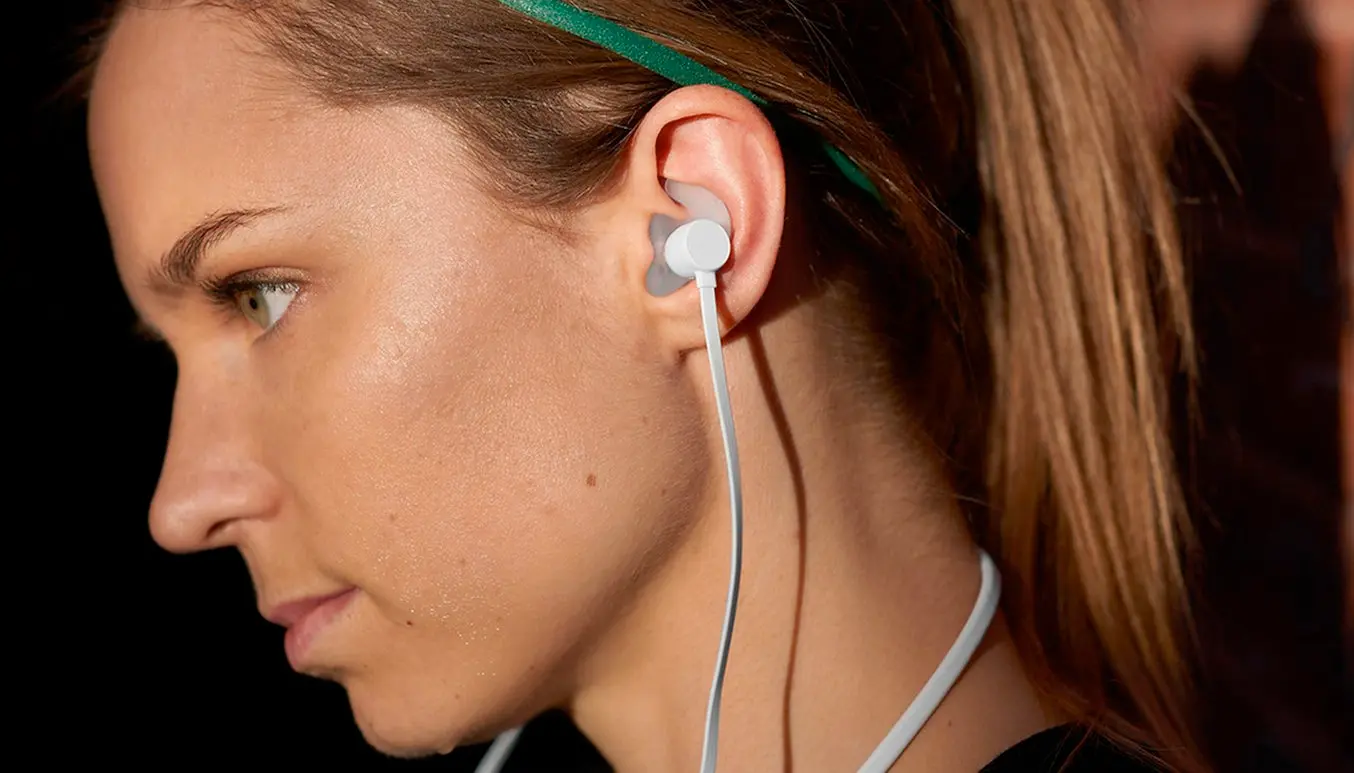
Customers will directly feel the benefits, as through extremely precise customization of their 3D printed audio devices they can look forward to new degrees of specialization and comfort in their in-ear technology.
11. Dentistry
Dentistry has also been one of the most prominent users of 3D printing, desktop 3D printers are an increasingly common sight in dental labs and practices. As matter of fact, the popular clear aligners, thermoformed on 3D printed molds, are possibly the single most successful use of 3D printing we’ve seen to date.
Consistently creating high-quality dental products that are affordable has proved difficult, owing to the uniqueness of each dental case and the number of possibilities for human error. Digital workflows in dentistry bring possibilities for greater consistency, accuracy and precision than before. Intraoral digital impression scanning can provide much better data to technicians, enabling easy creation of repeatable models through 3D printing, and improving efficiency in both the dental practice and the lab.
Dental 3D printers mostly use resin-based 3D printing processes, like SLA or digital light processing (DLP), to create a variety of indications like surgical guides, dental models, molds for clear aligners, dentures, or castable patterns for crowns and bridges quickly, with enhanced accuracy and lower cost than traditional methods.
The result for the customer is a plethora of dental products that fit better and work better, with higher clinical acceptance by the patient. The time saved by the streamlined workflow leads to better throughput, lower material costs, and better results for the patients.

DLP 3D Printed Dental Teeth Model For Display
12. Prosthetics
3D printing’s impact is not limited to improving workflows or enabling rapid prototyping. It can also change lives directly. With 30 million people worldwide in need of artificial limbs and braces, there is hope that 3D printing can provide new solutions where cost and specification have traditionally been hurdles.
There is a global shortage of prosthetics relative to demand, and the time and financial cost required to acquire needed prosthetics can prove prohibitive, especially given the degree of customization involved and the high need for prosthetic supplies in, for example, developing countries. Prostheses and braces not built to specification can end up giving discomfort those they should be assisting and empowering.
3D printing can provide an affordable alternative that, like many related advances in medicine, can provide therapy that is much more closely tailored to a patient’s needs. The affordability and customizability of 3D printing techniques can profoundly alter the quality of life for the better for those suffering from injury or disability, as we saw in this story of a father and son.
SLA 3D Printed Exoskeletal Cast to Heal Broken Bones
13. Surgery
3D printing can also help make the difference during key moments in surgery. Doctors can scan the patient before the operation and create custom 3D printed models anatomical models to plan and practice for surgery.
For example, researchers at the University Hospital of Lübeck reduced risks during brain operations by using 3D printed arteries. Elsewhere, healthcare providers have doubled down on 3D printing to provide fast, realistic 3D surgical models.
In surgical cases, 3D printing is able to decisively augment existing physical practices—for instance, the less-precise use of cameras to assess the state of an organ in real time. By combining aspects of the digital workflow with the use of computer-aided engineering and data visualization, doctors were able to create these closely modeled objects, and work with new degrees of accuracy and care at the point of treatment.
3D printing has also made formerly impossible surgeries a reality. Replacing the upper jaw, forming a new skull and replacing cancerous vertebrae, all unthinkable before the advent of advanced 3D imaging and printing, have now been carried out successfully because of it.
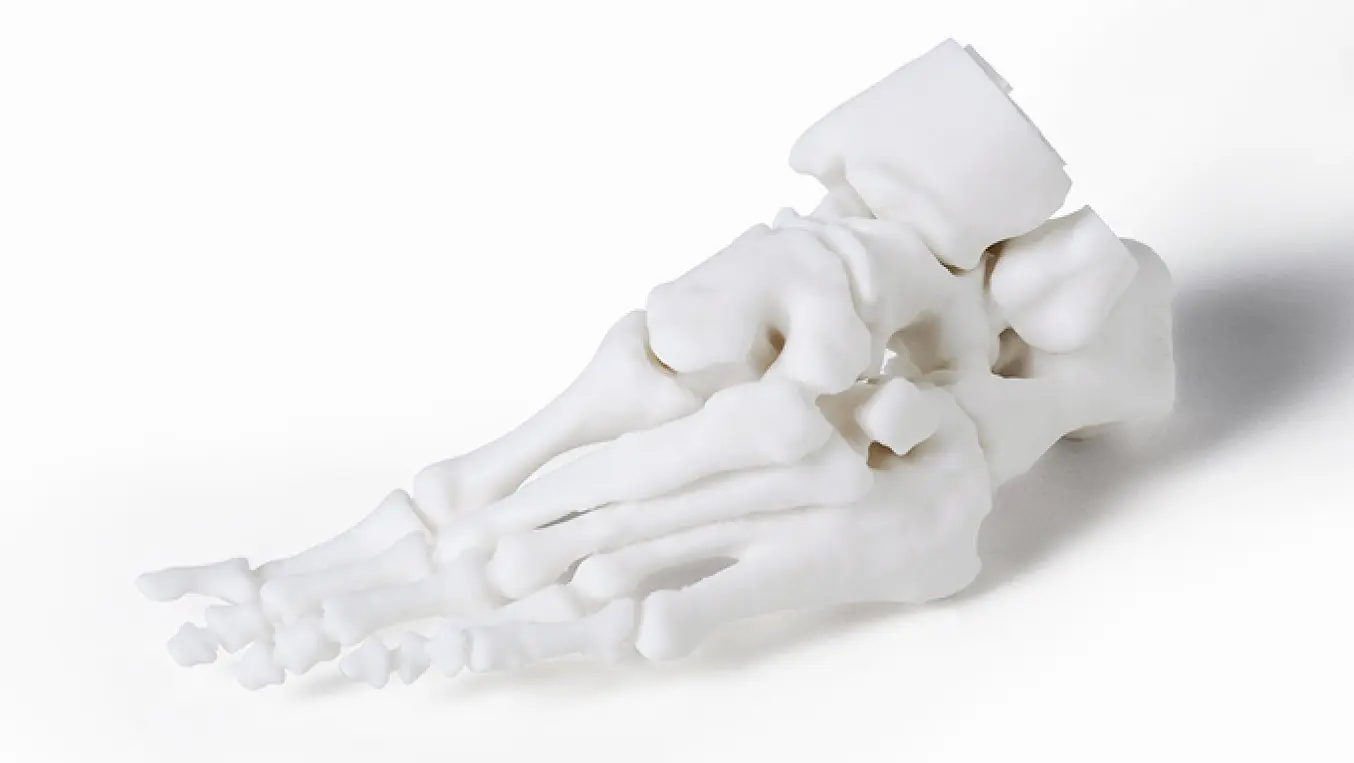
PolyJet 3D Printed Tumor Model with Resin for Bowel Cancer Surgery
14. 3D Printed Organs (On the Horizon)
As much as 3D printing technology has developed in the past few years, there are even more high-impact, and seemingly unlikely, use cases of it currently in development. Printed organs is one of them.
Being able to easily create new organs has for decades been a dream for scientists working in regenerative medicine. While it remains in its early stages, the use of the 3D workflow to produce organic tissue eligible for transplant is bearing early fruit. The likes of Organovo and various other laboratories and startups around the world have made creating liver tissue via 3D printing a research priority.
3D organ creation centers around the practice of bioprinting, a specialist offshoot of 3D printing, which takes cells from donors, turns them into printable bio-ink, and then layers and cultures them into mature tissue ready for organ transplantation.
The potential benefits of being able to use 3D printing technology to provide necessary transplant organs are incalculable. What’s more, they may yet pave the way for even greater strides in regenerative medicine, offering new, safe ways to design and test drugs that could treat organ disease and prevent the need for organ transplants altogether.
Construction
15. Architecture
As an industry already based on geometric design, prototyping and modeling, architecture stands to gain enormously from advances in 3D printing technology. We’ve seen the digital workflow produce complex architectural scale models in full detail, improving the 3D modeling phase of architectural design.
On top of saving time during model production, the 3D printed models allow architects to anticipate the effects of certain design features with much greater certainty, e.g., by seeing a model produced with a fuller complement of materials, an architect can measure aspects such a light flow through the structure with higher precision.
The high presentation value of having such an exact model also means that 3D printing can be an acute commercial tool for firms looking to win projects and commissions by showing off the full attributes of their design.
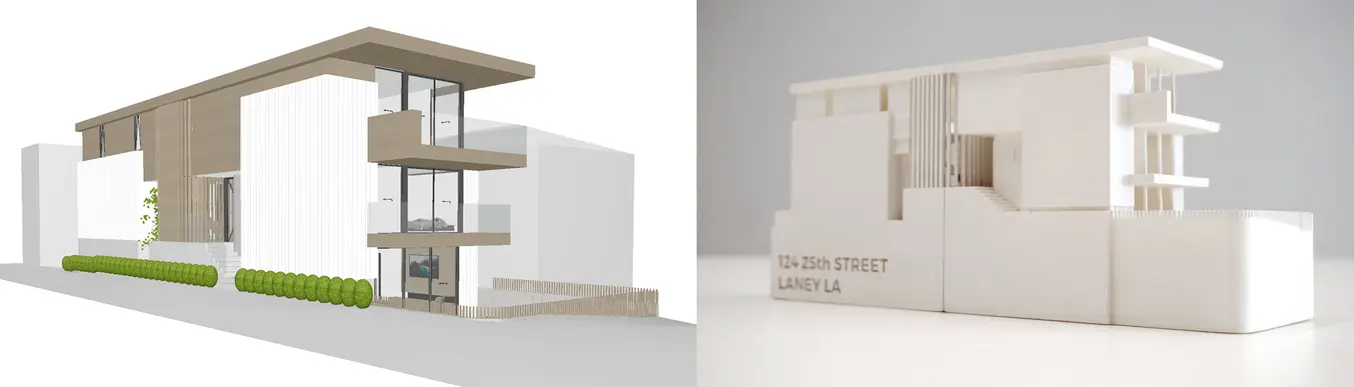
SLA 3D Printed Resin Architectural Models of Detached Houses
Art
16. Sculptures
The boom in “additive art” has been growing by degrees over the last decade or so, and we’ve seen 3D printing techniques infiltrate various corners of the art world, from consumer artworks to sculpture fit for the Smithsonian.
Using 3D photographic scanning systems to create physical artwork, 3D printing processes can provide a lot of new choices for customers. These developments have given both artists and customers a measure of new creative power, too—anything they can conceive of and design, they can produce, and to highly detailed standards.
SLA 3D Printed and Glued Large Hanging Futuristic Resin Sculpture
17. Movies and Visual Effects
3D printing has already been integrated into the production of Hollywood films and is widely used for practical visual effects and costuming.
Whereas the creation of film’s most fantastic creatures once required meticulous handcraft, the increased deadline pressure and time demands of modern moviemaking have made a quicker method of creating practical effects vital. Effects studios like Aaron Sims Creative now use a hybridized approach, practical effect-making enhanced by the digital workflow, to create new opportunities for collaboration and cut lead times on bringing ideas to life.
SLA 3D Printed and Electroplated Phoenix Models as Movie Props
18. Dance and Music
3D printing’s artistic potential is not limited to physical artwork. It also has the power to bring entirely new dimensions to forms like dance and music.
For example, consider the 3D printed, wearable “instruments” developed by Joseph Malloch and Ian Hattwick of McGill University. Using advanced sensing technologies, they transform movement, orientation and touch into music.
19. Musical Instruments
3D printing can even disrupt industries that have been in a static paradigm for years or centuries.
For instance, the manufacture of violins had been unchanged for several hundred years—an entirely manual process of master craftsmen, as automated manufacture has proved unable to produce the instrument to the necessary quality of finish.
Owing to the precision of detailing that 3D printing is capable of, we have seen a hard-to-break industry disrupted
As the customization and specification of musical instruments have proven costly in the past, 3D printing capabilities should lead to key changes in the market as new and valuable designs are made possible, potentially paving the way for the creation of entirely new instruments.
20. Art Restoration
3D scanning, CAD, and 3D printing have been used to restore the works of some of history’s most famous artists, returning works by the likes of Michelangelo and da Vinci to their former glory.
After the present state of a given artwork has been evaluated, the work can be digitally scanned and modeled. The possibility of unintended interpretation is minimized by using existing pieces of a work as the basis for subsequent restoration. Restorers are able to access a wealth of data on potential issues as well as enhancements, followed by documentation, the design of shapes, and restoration.
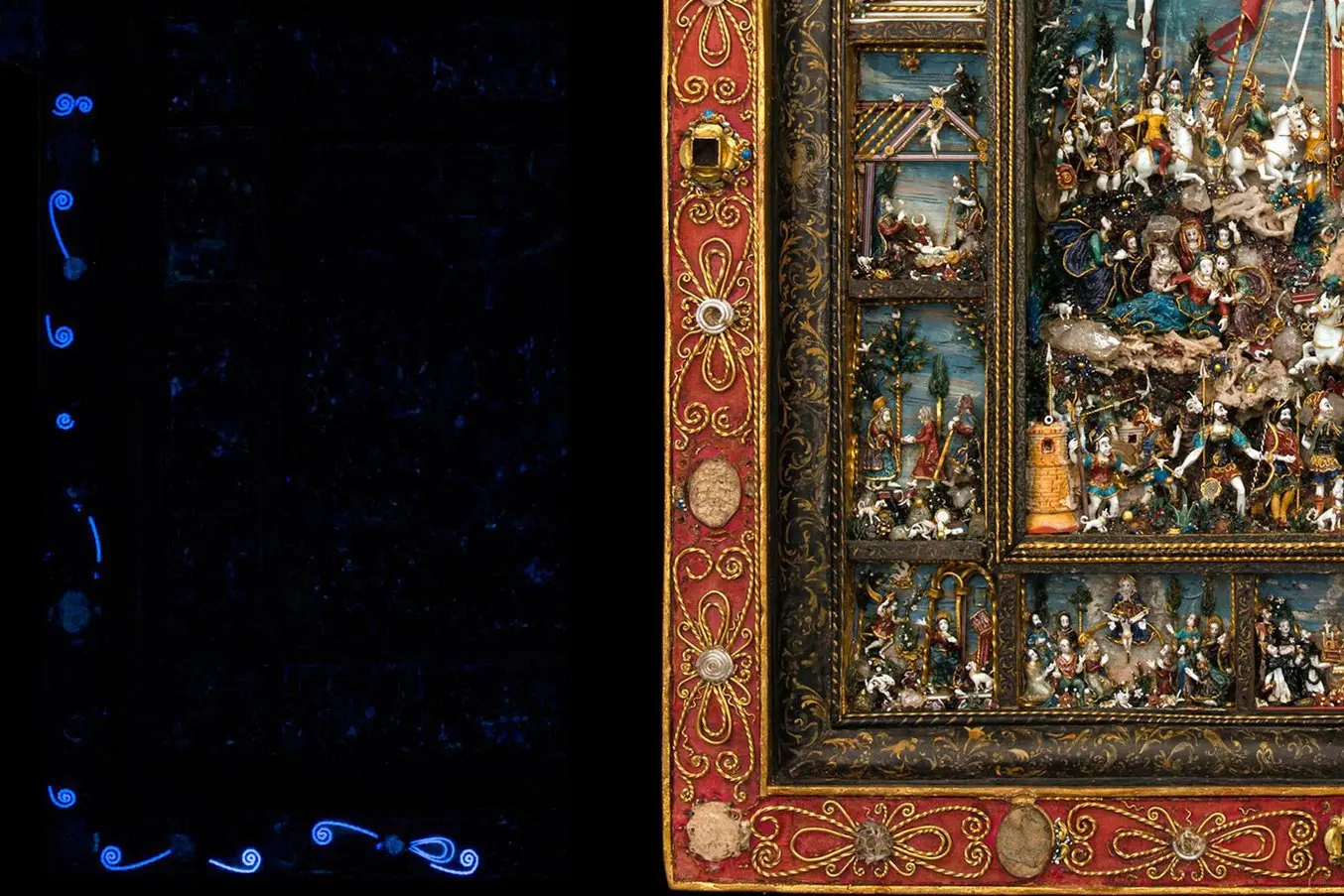
Owing to the complexity of the features involved, and the lack of techniques that could guarantee safe and secure recovery, many previous attempted restorations were abandoned as impossible. Now, with the help of the digital workflow, even incredibly intricate, multi-material restorations are feasible, like this one undertaken in the Museo Tesoro dei Granduchi in Florence.
Research
21. Forensics
3D printing has as much potential utility in reconstruction as it does in production. The work of a forensic artist is often made difficult by incomplete evidence. Digital technologies can be of tremendous use in legal investigations and can augment the abilities of forensic artists to reconstruct accurate models of persons of interest or victims.
The digital workflow here involves turning CT scans into 3D prints to aid in identification. For instance, when investigators find just part of a skull as evidence, a printer can model and replicate the complete sample.
Reconstructions of the appearance of crime victims have already played a key role in attaining justice, proving once again the utility of 3D printing beyond considerations of design and productive efficiency.
22. Paleontology
Paleontologists will have a field day with 3D printing, as it may help complete dinosaur skeletons by printing elusive missing bones.
The Smithsonian museum staff experimented recently by printing the missing bones of a T. rex exactly to specification. The 3D workflow enabled the team to experiment widely and safely using modeling software, saved time and reduced risk to the integrity of the real skeleton.
SLA 3D Printed 1:35 Livyatan Whale Model
Near-Future Use Cases
Having seen 3D printing’s capabilities develop rapidly over the past decade, some of the most exciting and unexpected use cases of the workflow are those that, though not immediately feasible, will become a plausible reality soon.
23. Housing and Construction
Desktop 3D printing is limited to producing smaller items, while manufacture-scale additive workflow can produce much larger functional components. In the last few years, various initiatives have gotten underway to create houses and larger structures that are entirely the product of 3D printing, opening new frontiers in sustainable living and construction.
The 3D printing technique gives freedom of form to architects, even with previously less malleable building materials like concrete. More broadly speaking, it allows fully sustainable and energy-efficient homes to be built that also meet modern comfort standards. Construction by this means could be entirely waste-free, and provide very low-utility cost.
In February of 2019, Texas company Sunconomy announced plans to sell the world’s first fully 3D-printed house. It will look something like this.
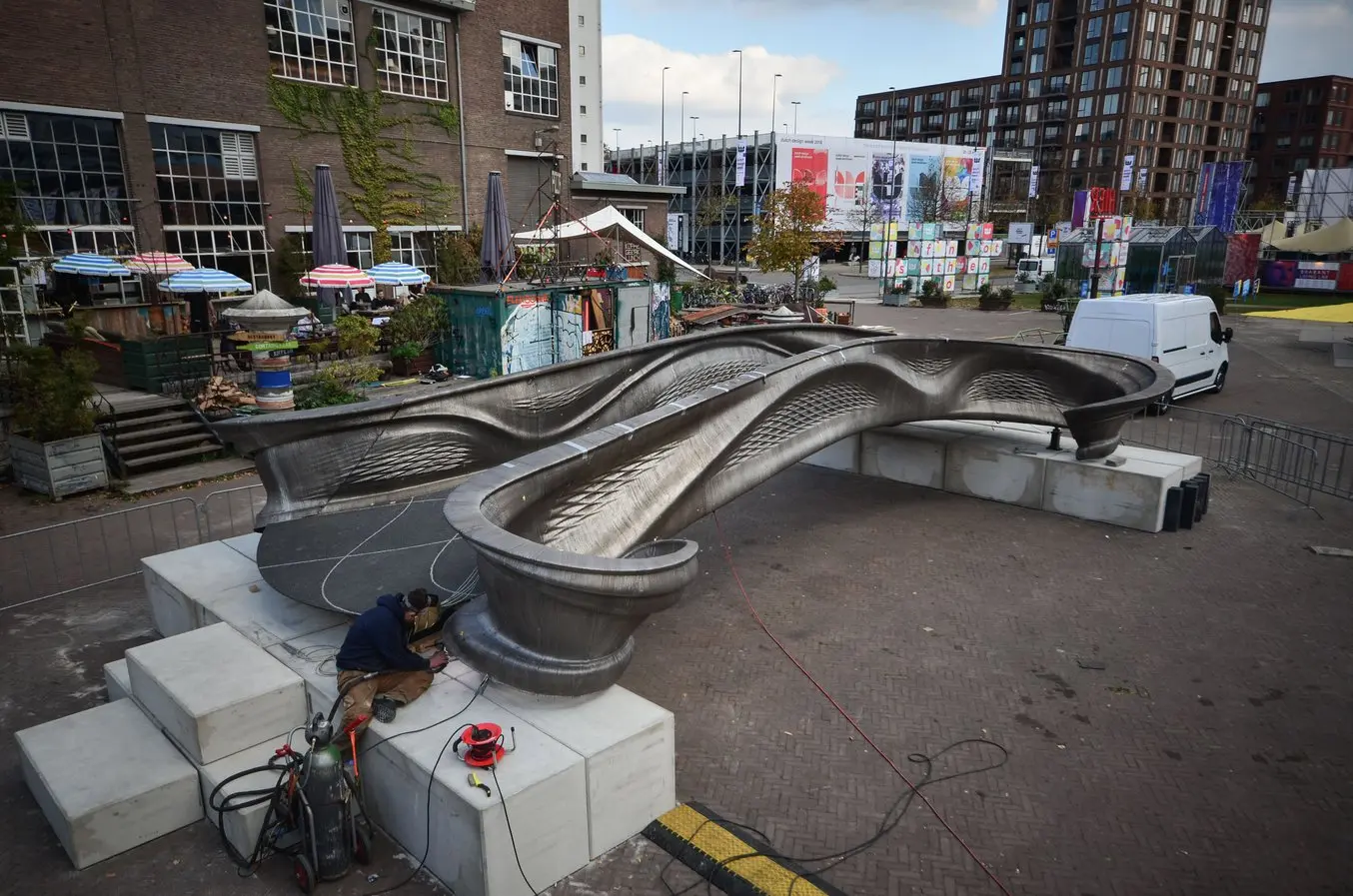
24. Recreating History
The loss of historical artifacts feels devastating because of the sense that recreating them is impossible. The destruction of many Syrian heritage sites, such as the ancient city of Palmyra, at the hands of ISIS seemed to represent a dark and irreversible step backward. Through forward steps in 3D printing, we may soon be able to recreate—and ensure—the glories of the past.
Through the Million Image Database project, a campaign to recreate the damaged ruins of Palmyra with 3D printing is underway. It uses 3D models of the site assembled from photographs to generate recreations that are, in scale and detail, true-to-history. Equally exciting, the same modeling techniques can also be extended to ensure the great masterpieces of artistic history against potential loss.
Going forward, 3D printing will not only have a transformative effect on production and design—it will also be able to play a major role in affairs of international and historical importance.
25. A New Space Race
With one of the highest barriers-to-entry of any industry in the world, space travel may be one of the most surprising areas of 3D printing innovation.
Aerospace startup Relativity has tested the creation of aluminium rocket engines using additive manufacturing. If successful, this application would sharply reduce the costs and practical difficulties of space travel, opening up the field to new business and to a vast potential for growth.

SpaceX’s choice of the 3D printing was taken on account of cost- and waste-cutting aptitudes of the technology, and to preserve flexibility in the production process too. The engine’s combustion chamber, also produced through 3D printing, was proven to have a superior strength, ductility, fracture resistance to conventional materials.
We’ve even seen 3D printing used in space, when NASA used a 3D printer to build a ratchet wrench aboard the International Space Station, the first tool of its kind to be manufactured in space.
Endless Possibilities
Visualizing 3D printing-driven changes in the way things are made does not require the feats of imagination it once did. As workflows have developed over the last several years and gained footholds in various industries, we are beginning to see that revolutionary potential demonstrated.
From dentistry and across healthcare to consumer goods, architecture, and manufacturing, the public is interacting more and more with the end products of 3D printing.
Making sustainable reductions to the waste involved in traditional production, cutting lead times and overheads, and empowering customers by bringing them closer to the products they want—we can only expect the influence of 3D printing to continue expanding.
Source: https://formlabs.com/blog/25-unexpected-3d-printing-use-cases/