Design flexibility, material efficiency and viable low-volume production are just some of the reasons why companies have increasingly turned to additive manufacturing (AM). But to make the most of AM in production, there are still some issues to tackle.
Below, we’re looking at some of the most pressing challenges the technology needs to overcome to accelerate its adoption:
Technological challenges
1. Slow production speeds
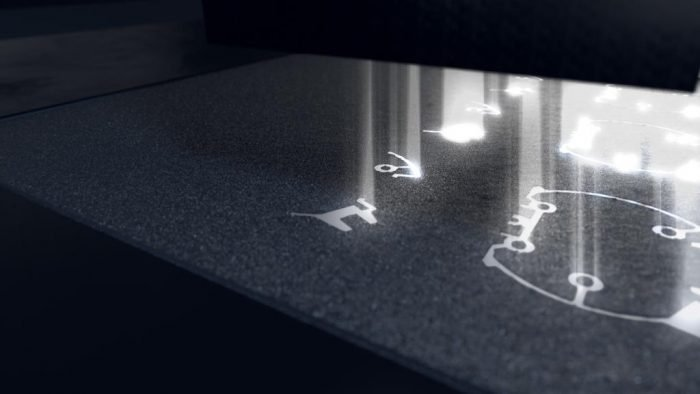
This, particularly, is an obstacle for adoption in industries driven by mass serial production, such as automotive and consumer goods. In these industries, products need to be manufactured and delivered in as short a timeframe as possible, in order to maintain production efficiency.
High-speed AM has been an area of robust development and investment in recent years.
Most 3D printer manufacturers, targeting production applications, are looking for ways to make 3D printing faster. Some have developed modular systems that can help increase throughput, while others are working to further improve the technology behind their existing machines.
For example, German hardware manufacturer, EOS, is developing its Laser Pro Fusion technology, with an aim to increase the throughput in Selective Laser Sintering (SLS) technology. While current SLS systems use one or two CO2 lasers to fuse polymer powder together, the new 3D printer will be equipped with up to 1 million diode lasers, which could significantly accelerate the printing time.
There have also been some notable developments on the metal 3D printing side. Australian Aurora Labs’ Multilevel Concurrent Printing (MCP™) technology is one example. With this powder bed fusion process, Aurora Labs is looking to enable metal 3D printing at much faster speeds.
Unlike traditional powder bed technologies, that print one layer at a time, MCP prints multiple layers simultaneously in a single pass. At Formnext 2018, the company reported that it was able to print around 30 layers at a time, with the goal to increase this to 100 layers over the next 12 months.
Recently, the company has reported that its PMP1 3D printer can reach a print speed of 350 kg/day. Aurora Labs says this result indicates a 2000 per cent speed improvement compared to the speed reported last year.
Increasing production speed is no mean feat and requires substantial technological innovation. As of 2019, both EOS’ and Aurora Labs’ technologies are still in the development stage, meaning, it will take time to prove their production speed claims.
That said, we are confident that 3D printing will ultimately get there, as progress continues.
2. Materials development and inconsistencies in material properties
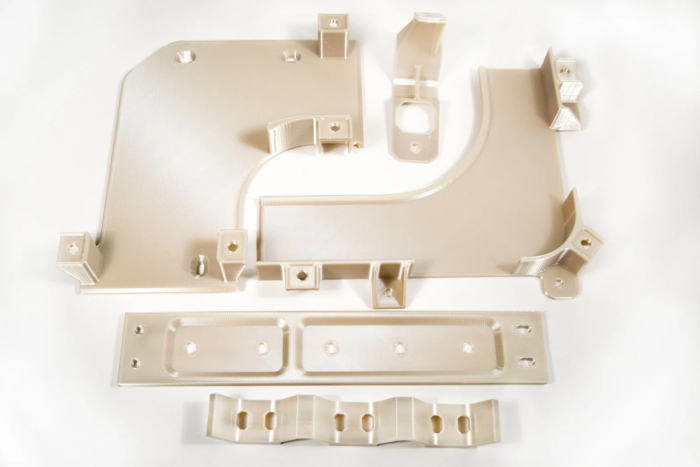
In the early years of 3D printing, when the industry’s focus was on prototyping, much less emphasis was put on material properties. However, with the technology transforming into a production solution, the material development process has accelerated tremendously.
A particularly exciting trend is the advancements in high-performance 3D printing polymer and composite materials. Large chemical companies like Arkema, BASF and DuPont are developing carbon-reinforced polymers, which offer strength sometimes comparable to metals.
A manufacturer of composite 3D printing technologies, Markforged, is also advancing this area and has developed several new materials. The most recently introduced is the Onyx FR, the first flame-retardant composite material.
On the metal side, material development takes longer, sometimes a few years, but the advancements are also ongoing.
While the availability of materials is increasing, there are still a lot of inconsistencies in the properties of the 3D printable materials. Currently, the industry lacks a solid database of materials with proven printing parameters and defined specifications. As a result, it becomes challenging to achieve a consistent and repeatable 3D printing process.
This means that most manufacturers will remain reluctant to use the technology, until they can ensure that material properties meet the industry’s predefined and accepted norms and standards.
The only way forward is the development of an AM material database with information on mechanical and thermal properties and specifications for successful printing.
The 3D printing industry is working towards achieving this goal. Standards developing organisations, like ISO and ASTM, have issued a few specifications on metal powders like nickel, titanium and stainless steel.
At the same time, other bodies build out a database of materials and process information for AM. For example, America Makes in collaboration with Stratasys and National Institute for Aviation Research (NIAR) released a database of material properties for ULTEM™ 9085 Type I used in Fused Deposition Modeling (FDM) earlier this year.
The establishment of such a database will help to further the use of the certified polymer material for aircraft interior components.
Ultimately, developments like this one will be key to ensuring that AM materials can meet manufacturers’ expectations for performance and reliability.
3. Manual post-processing
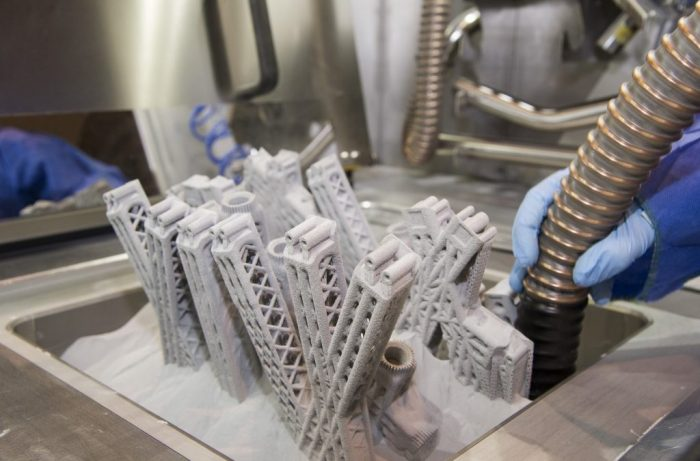
This is not a big issue when using 3D printing for prototyping. However, as the technology is transitioning to an end-part manufacturing process, scaling and automating, post-processing, has become one of the key bottlenecks to establishing AM production lines.
The majority of post-processing operations Terry Wohlers describes above are still heavily manual processes, requiring skilled operators to perform key tasks.
It might be cost-effective to use human labour to finish a prototype or even a couple of dozen parts. However, when producing hundreds or even thousands of 3D-printed parts, the need for post-processing automation becomes extremely acute.
Currently, there are only a few AM-specific solutions which help to automate post-processing operations, like DyeMansion’s cleaning machines, AMT’s surface smoothing solutions and PostProcess Technologies’ support removal and surface finishing systems. Admittedly, these systems are designed primarily for polymer 3D-printed parts.
When it comes to metal 3D printing, post-processing technologies, used for traditionally manufactured parts, are currently being adapted for 3D-printed components.
To further automate these technologies, companies are now also beginning to implement robotic solutions to eliminate operations like material switchovers and part handling. For example, 3D printer manufacturer, Digital Metal, launched a fully automated production concept last year.
According to this concept, a robot will handle most of the process steps, such as feeding the printer with build boxes and then removing them for post-processing. The goal is to eliminate all manual work to facilitate continuous, high-volume production.
While such developments are encouraging, the pace of innovation in this area is sluggish. However, the number of advanced post-processing solutions will surely be increasing to match the ever-growing AM production volumes.
Software challenges
4. Limited capabilities in data preparation and design
While it may seem as though 3D printing is as simple as pressing a button, that isn’t remotely the case. For one thing, industrial 3D printing requires significant design preparation to get a model ready for printing.
The design process is complicated by the fact that for a long time, Computer-Aided Design (CAD) and Computer-Aided Engineering software was largely not optimised for the requirements of 3D printing.
For example, it can be difficult to use traditional CAD software to design components made with graded materials, create lattice structures or model porosity.
Furthermore, the AM design workflow involves multiple steps, which are often bogged down by the need to use separate software solutions.
For example, in a typical scenario, a designer would create a solid model in their CAD system and then convert it into a triangulated model to perform printability checks, optimise the structure to reduce weight, add supports and run simulation analysis. All these steps will require different programs, different software environments and multiple file formats.
Then, imagine that you run a simulation and the results indicate a build failure, requiring you to alter the part orientation or support structures to prevent it. As a result, you’ll have to go back through all the steps and programs to change some parameters and make the model printable.
This need to transfer AM design data through multiple software solutions results in a time-intensive and error-prone design process.
The industry is trying to ease the burden of 3D model preparation in multiple ways. For example, software companies, like PTC, Autodesk and Dassault Systèmes, are melding specific 3D print functionality into their CAD programs.
For example, PTC is offering its Creo 6.0 software to enable design and print preparation in one environment. At the end of 2018, PTC acquired generative design software company, Frustum. The company is now working to add generative design technology, which is often combined with 3D printing, to its CAD platform.
At the same time, 3D printer manufacturers develop their own software solutions to streamline 3D model preparation. Stratasys’ GrabCAD and 3D Systems’ 3DXpert are just two examples of the software developed to eliminate or minimise the need for multiple data transfer and conversions.
Although great progress is being made on the AM design and print preparation front, there’s still room for development. Providing the designers with the ability to modify 3D models within the CAD environment and quickly iterating them without cumbersome data conversion, will be key to making the design preparation challenges a thing of the past.
Quality assurance challenges
5. Part-to-part variation
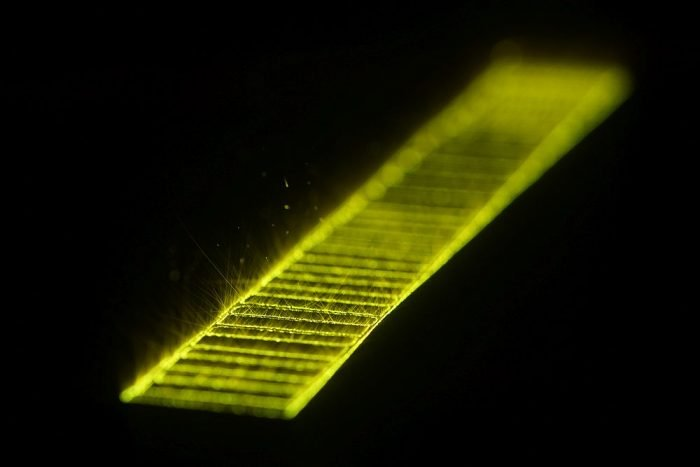
This is particularly the case with metal 3D printing. For example, some of the flaws unique to metal AM can include powder trapped inside a part, microcracks and the lack of fusion.
One of the key sources of variations in part quality is material chemistry. Safety-critical applications, such as aircraft parts or medical devices, require a material to have the right morphology (particle size and shape) and be 100% free of contamination.
Impurities, caused by improper storage or handling, or questionable quality of the feedstock, can alter the properties of the final part, which could in turn, lead to a failed print.
Ensuring the quality of the material requires standardised test methods and tools, which the industry is largely lacking. To overcome these issues, AM users are partnering with trusted testing laboratories or, if they have enough resources, developing the necessary expertise in-house.
Another challenge impacting part variability lies in the lack of advanced process control in 3D printers. To minimise part variation, 3D printers need to shift from an open-loop to a closed-loop control system.
The latter refers to the ability of a 3D printing system to spot deviations during the printing process and automatically adjust the system to compensate for them. This is achieved by embedding sensors and cameras inside a 3D printer, which allows users to monitor the build in real-time.
Maintaining control over the build process, through the closed-loop control system, enables manufacturers to achieve consistent geometries, surface finishes and material properties that underpin quality.
However, in-process quality control, enabled by a closed-loop system, is still relatively new to AM technologies and presents a barrier to manufacturers to implement. As of 2019, only a small percentage of 3D printers available on the market are equipped with closed-loop control units.
That said, in-process control will become an absolute necessity, as 3D printing is moving to production floors. This ultimately means that the number of smarter systems is only set to increase in the near future.
6. Lack of industry-wide standards
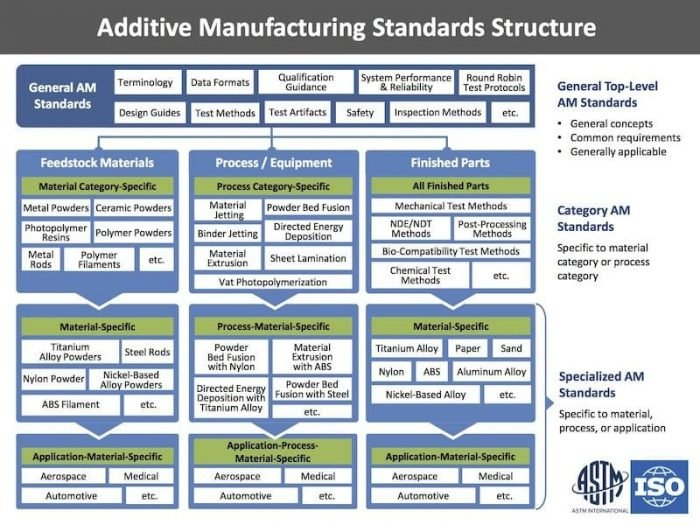
In manufacturing, standards are essential, as they outline the parameters that must be met to deliver a quality product. Raw materials, machines, equipment operators and engineers, suppliers and the manufacturing process itself, all need standards and a mechanism for qualifying/certifying against those standards to make parts with the required quality.
Although 3D printing has been around for more than 30 years, the manufacturing world began to recognise it as a production method only recently. For this reason, the industry has just begun to develop production-relevant and industry-wide standards.
The lack of 3D printing standards remains one of the key bottlenecks slowing down its wider adoption.
However, there have been a lot of promising developments on this front. Some of the largest standards developing organisations, like ISO and ASTM International, have established committees dedicated to AM standards development. By 2018, the two organisations approved 28 standards, with many more to be issued in the next couple of years.
Standards development is also greatly bolstered by industry collaboration and partnerships. One example is a collaboration between Oerlikon and Boeing. Targeting AM use in aerospace and defence, the partnership is focused on standardising materials and processes for powder-based metal 3D printing of structural titanium components.
Perhaps the most powerful collaboration involves the launch of Additive Manufacturing Center of Excellence (AM CoE) last year. The new facility, founded by ASTM International in collaboration with Auburn University, NASA, EWI and the UK-based Manufacturing Technology Centre (MTC), is focused on bridging R&D and standardisation to fill key industry gaps.
In September, ASTM International announced the second round of funding with the goal to support AM CoE’s standardisation projects. Each of the nine projects contributes towards different standard gaps in design, feedstock, process, post-processing, testing and qualification.
While standards development is a time-intensive process, the recent progress suggests that it will eventually yield results, enabling manufacturers to develop and implement AM applications faster and more easily.
7. Lack of understanding and expertise in AM
A lack of thorough understanding of the capabilities of 3D printing technologies can create many barriers to entry. Currently, there is still a knowledge gap in terms of what 3D printing technologies are, what their capabilities are and how they can be used. As a result, businesses, which could benefit from the technology, are unwilling to adopt it, as they struggle to develop a business case or use case for 3D printing.
8. Making the initial investment
Adopting AM does take time and effort. However, the greatest barrier to adoption may lie in substantial investment needed to put AM on the production floor.
Investment in AM is not only about buying the equipment. It’s more about investing in the AM ecosystem, which encompasses software, materials, employees training, post-processing equipment, certification and finally establishing a facility to accommodate all this.
The capital and resources required to put this puzzle together, are sometimes so enormous that an organisation is unwilling or even unable to invest in AM.
However, there are companies making hardware more accessible. On the polymer side, a number of 3D printer manufacturers are developing industrial desktop 3D printers, which are easy to set up and use. Such systems typically cost much less than high-end 3D printers, which could easily run into hundreds of thousands of dollars.
For example, UK-based automotive manufacturing company, Dunlop Systems and Components, has integrated Markforged’s composite 3D printer, priced at around $15,000.
In less than nine months after installing the 3D printer, the company found multiple uses for the technology, which could save it up to £40,000 per year. The company also says that it had the payback within six months, which is quite impressive.
There are similar developments on the metal side, with companies like Desktop Metal, Markforged and Xact Metal, offering entry-level metal AM systems. Metal 3D printers of this kind are compact and cost up to $150,000, which is a fraction of the cost compared to larger metal 3D printers.
While investment in AM technology may be daunting, it often can be justified when considering the overall impact of the technology on the bottom line. That’s why it’s important to develop a business case before jumping in. In Dunlop’s case, for example, the company started by identifying a handful of quick wins that could reduce costs and generate clear financial payoffs in the short term.
When successful, the quick wins will attract attention and create a sense of momentum, eventually generating resources that can be invested in more ambitious, longer-term projects.
Workflow and integration challenges
9. Disjointed AM ecosystem
For AM processes to scale at the industrial level, the AM value chain, which begins from conception to production and post-processing of the product, needs to become more consolidated.
Currently, the market is saturated with many different solutions, which ideally could be integrated to create a comprehensive offering, thereby simplifying the adoption of the technology.
As a result, companies looking to adopt AM are faced with the need to buy disparate solutions and then try to make them work together. This lack of integration in the AM value chain creates a lot of inefficiencies in the workflow.
Some companies are overcoming this challenge through collaboration. Many AM hardware manufacturers are teaming up with software providers to improve user experience.
One example includes the partnership between industrial desktop 3D printer developer, RIZE, and software company, Dassault Systèmes. With this partnership, Dassault’s SOLIDWORKS and RIZE will work together to enable seamless integration between SOLIDWORKS design software and RIZE printers.
Other companies are consolidating the AM ecosystem by expanding their roles along the value chain. For example, Henkel, a chemical manufacturer and formulation specialist, has developed a variety of offerings along the entire value chain.
These include producing custom-made material formulations, selling printers under the Loctite brand and reselling printing equipment manufactured by HP and Carbon. Henkel also offers services for printing and post-processing of parts.
10. A lack of digital infrastructure
To be able to use 3D printing in production, companies need the right digital infrastructure to manage their 3D printing operations efficiently.
Many companies are establishing such an infrastructure by using off-the-shelf IT solutions. In many cases, these solutions have been developed with the requirements of traditional manufacturing in mind and are often not optimised for 3D printing workflows.
To overcome this issue, the industry has been developing workflow management software specifically for 3D printing. Such software helps to manage the entire workflow, from request management, printability analysis and machine analytics to production scheduling, post-processing management and communicating with suppliers.
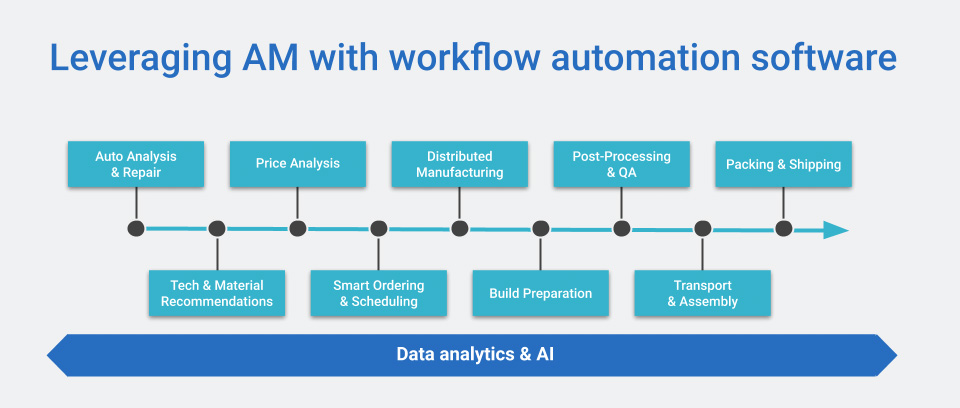
As a result, a company can have a centralised production planning and monitoring system, which enables it to track parts and view projects, allowing for greater traceability.
Workflow management software is fast becoming one of the key solutions needed to create the digital infrastructure for AM production. It makes day-to-day business processes more efficient, by coordinating tasks between people. Finally, it helps to synchronise data between systems, making the integration of AM into a digital manufacturing environment much simpler.
The evolving industry
As a young technology, 3D printing has many challenges, but the good thing is that the industry is eager to overcome them. Over the last decade, the industry has made a quantum leap forward by developing better and faster systems, creating more materials and automation solutions and expanding the list of approved standards.
Furthermore, we’ve seen a lot of effort made to bridge the knowledge gaps and foster a new generation of AM professionals. Finally, the industry itself is becoming more consolidated, as companies are looking to partner, in a bid to create comprehensive solutions.
All these activities are indicative of a thriving industry, which will continue to grow and evolve in the years to come.