In rapidly maturing 3D printing industry, what are the trends shaping the materials market?
Materials are one of the three key pillars underpinning 3D printing, alongside hardware and software. According to the Wohlers Report 2019, the 3D printing material segment experienced record growth in 2018 due to the increasing use of 3D printing for series production.
In 2019, this growth is only set to continue, supported by a number of trends at which we’ll be taking a closer look at below.
1. Composite 3D printing is taking off
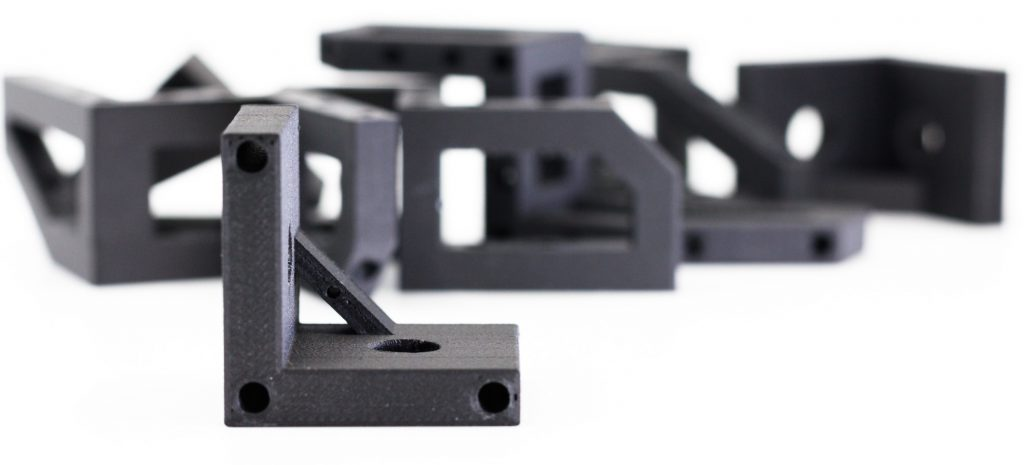
In 3D printing, composites typically comprise a core polymer material, like nylon, and a reinforcing material, like chopped or continuous fibre. The composite material offers higher strength and stiffness compared to non-reinforced polymers. In some cases, it can even replace metals like aluminium.
These enhanced material properties make composites sought-after materials for tooling and end-use applications in a range of industries, like aerospace, automotive, energy and oil & gas.
The end-use applications of composite 3D printing
A great case in point is Shawcor. Thanks to composite 3D printing, the Canada-based global energy services company has saved $1.6 million CAD (roughly $1.2m USD).
The company needed a custom machine to help transfer large tape pads that would be too heavy for one person to do alone. However, the company was faced with a lose-lose situation: either to spend too much time and money to build a custom machine using traditional methods or lose revenue by not having it at all.
However, using Markforged’s composite 3D printer, Shawcor’s team has been able to create parts to create a custom loading machine. Around 50% of all the 53 printed parts have been reinforced with either Kevlar, HSHT fibreglass or carbon fibre, which were used to replace aluminium and sheet metal parts.
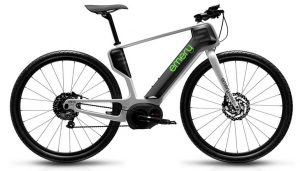
Applications such as these showcase the largely untapped capabilities of composite 3D printing, and the potential the sector has for huge growth.
Material development
Helping to fuel the growth of composite 3D printing is an ongoing material development. For example, Markforged, a pioneer of composite 3D printing, has recently introduced the Onyx FR, the first flame-retardant composite material.
The material is nylon reinforced with continuous strands of carbon fibre. But additionally, Onyx FR is self-extinguishing — meaning it can stop itself from burning within a few seconds.
Markforged says that Onyx FR will open up more 3D printing use cases across the automotive, aerospace and defence industries as the material meets higher fire safety standards.
Another development comes from Techmer PM. The US-based materials manufacturer has recently announced the opening of a new high-capacity production line designed to produce carbon fibre-reinforced polymers. This investment has particularly been spurred by the demand from manufacturers of large-format 3D printers.
In a similar vein, Arkema has opened a plant to make its Kepstan PEKK material. Observing a “strong demand for carbon fiber reinforced composites and 3D printing”, the company has made a clear move to support it.
There’s undoubtedly a lot of activity in the composite 3D printing sector, pushing both the technology and materials accompanying it to new heights.
2. Materials production is increasing
Another key trend within the 3D printing materials market centres around business expansion. More companies are establishing R&D as well as material production facilities, helping to further the industrialisation of the technology.
For example, last month Amastan Technologies, a US-based material producer, announced the acquisition of AL Solutions, a producer of refined titanium materials. The latter will be rebranded as Amastan Additive and become part of Amastan’s yet-to-be-built AM metal powder facility.
Thanks to AL Solutions’ proprietary recycling technology and Amastan’s plasma-based UniMelt™ technology, the company is now well-positioned to become one of the key players in AM titanium powder production.
Jabil is another company pushing AM materials development. Spurred by customer demand, the global manufacturing services company has launched a separate business unit, Jabil Engineered Materials this January.
The limited choice of materials has been a significant obstacle for the adoption of 3D printing, according to the company. To overcome this, the new unit will focus on developing, validating and bringing to market engineered materials for industrial 3D printing.
Importantly, Jabil will not only use new materials internally but also provide them to the open market, so that more companies can benefit from a wider material choice. So far, the company has launched PETg, PETg ESD, TPU 90 A and TPU 90 A ESD, but plans to deliver more in the months ahead.
Looking ahead, we expect other industry players to start ramping up their material production capabilities in a bid to keep pace with the demand. As this trend unfolds, it could bring a tremendous boost to the whole 3D printing industry.
3. Open materials is an expanding concept
Despite ongoing progress, material development for 3D printing is still slower than one might expect.
One obstacle to greater material diversity is the proprietary nature of many 3D printable materials. Many 3D printer manufacturers develop their machines to work exclusively with the materials they develop in-house. This limits the opportunities for their customers to use third-party materials.
A proprietary materials model typically results in higher material prices and a slower pace of innovation for new material formulations.
One possible solution to overcoming these constraints is an open materials model. This model encourages major material producers to partner with 3D printer manufacturers and develop new materials for their systems.
Such an approach has two key benefits. First, it helps to expand the choice of materials for end-users. Second, it speeds up the material development process.
One of the biggest success stories of the open materials model has been Ultimaker’s Material Alliance Program. The program involves material manufacturers sharing the print parameters for their materials in a special database, which can be accessed by Ultimaker’s customers. The vision behind this is to enable the customers to reliably use third-party filaments on Ultimaker 3D printers.
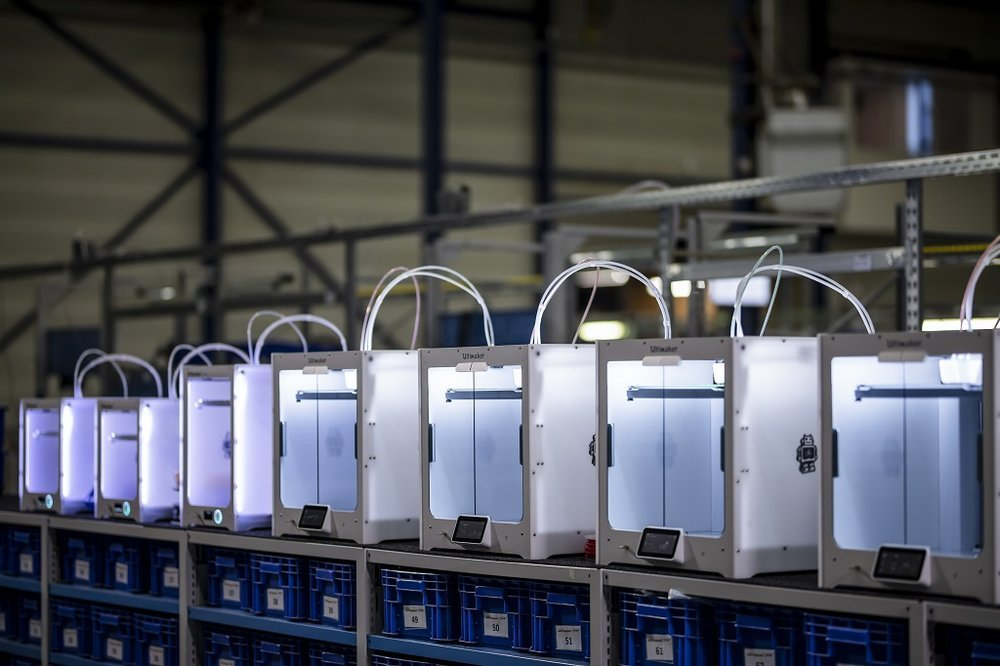
For example, Arkema brought its PVDF-based filament, known as FluorX, to the program last month. The material is designed for printing high-performance parts with exceptional thermal and chemical resistance.
Thanks to Ultimaker’s strategy, its customers now have access to a greater variety of materials with specific properties like impact and chemical resistance, flexibility, strength and more.
Other companies, too, are embracing the open materials model: these include HP, Origin and Prodways. Even Stratasys, which has been developing its materials in-house, has admitted that the company needs “to partner with others to develop more high-performance materials”.
Ultimately, we’ll see increasingly more companies adopting the strategy in the next couple of years, spurring even more dynamic material development for 3D printing.
4. Material costs are coming down (slowly)
The high cost of 3D printing materials has always been a sticking point. One study suggests that the raw material cost 3D printing materials can be up to ten times higher than traditional manufacturing materials.
Naturally, exact costs depend on a number of factors, such as the 3D printing process and materials used during production.
For example, the price of resins for SLA 3D printing typically ranges between $50 per litre for standard resins and $500 per litre for professional resins. However, according to one resin manufacturer, the resins could cost as low as $10-$20 per litre.
There are several reasons why materials costs for 3D printing remain high. One is that the overall volume of material shipments is relatively low.
Another is that the majority of the 3D printing materials available are proprietary, requiring users to purchase them directly from the 3D printer manufacturers themselves. This creates a monopoly on the 3D printing material market, with manufacturers marking up the cost.
However, there are some key developments which could help to reduce material prices. One is the growing use of 3D printing for serial production. As the volumes for 3D printing production increase, this should lead to reduced material costs.
One example of this is Carbon. Just last year, the 3D printer manufacturer reduced its price for three different resins to $50 per litre, down from $300 per litre in 2016. Carbon says that the key to the price reduction lies in high-volume applications of its 3D printers.
With Carbon’s example in mind, we believe that there’s a potential for other manufacturers to follow a similar path as their volume and customer reach expand.
The rise of the open materials model could also help to bring material costs down, as it opens the market to many more material suppliers. The more market players there are, the higher the competition — which could help to bring prices down.
5. Global chemical companies are getting more involved
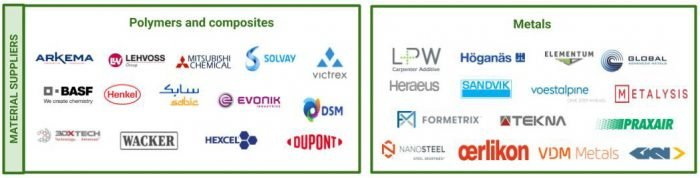
For example, Stratasys and Solvay have announced a joint materials roadmap in May of this year. This roadmap will see Solvay developing high-performance materials like PEEK for Stratasys 3D printers. Thanks to this partnership, the two companies are already preparing to commercialise an AM-ready filament based on Solvay’s Radel polyphenylsulfone (PPSU) polymer.
On the investment side, UK-based material developer Victrex plans to invest millions of euros into Dutch 3D printer and software developer Bond 3D. The substantial investment will help the company to accelerate 3D printed PAEK and PEEK parts to market.
Furthermore, chemical giant BASF has signed numerous partnerships within the 3D printing industry. The most recent has been 3D printing startup, Impossible Objects. Through this partnership, BASF will provide Impossible Objects with its Polyamide 6 material. By combining it with Impossible Objects’ new composite technology, the companies look to broaden the range of production applications, especially in the automotive and industrial sectors.
These examples showcase a strong trend within the 3D printing industry: large material companies are getting more and more serious about 3D printing as an industrial solution – yet another indicator of this industry’s overall potential over the next few years.
Toward a thriving future
The materials market remains a vital part of the 3D printing industry — and as we’ve seen, a few key trends are helping to shape the future of the market.
Perhaps the trend that will have the biggest impact is the increased activity within materials development. In many ways, this increase in activity is being driven by market demand, with customers demanding more materials, particularly for production applications.
To capitalise on this growing demand, chemical companies are continuing to strengthen their position in the market through greater R&D, investment and partnerships. Similarly, machine manufacturers are also aiming to leverage the power of collaboration.
As the material selection expands and costs begin to come down, this can only serve to broaden the current applications of 3D printing, and further the adoption of the technology across industries.