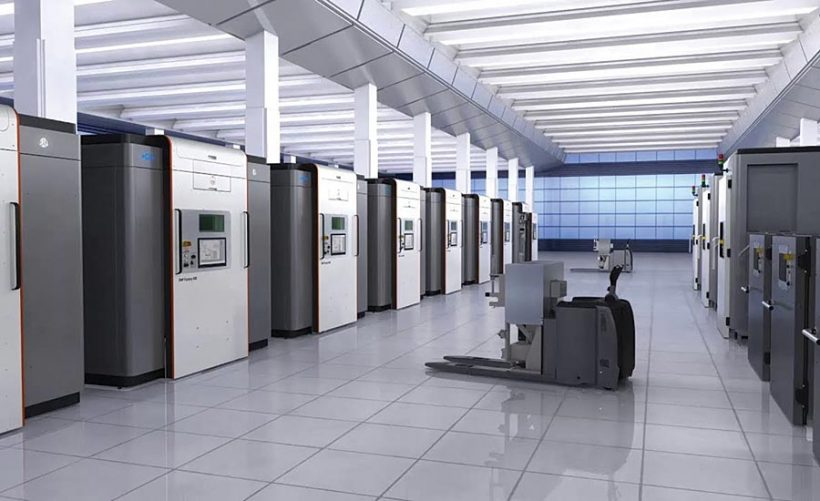
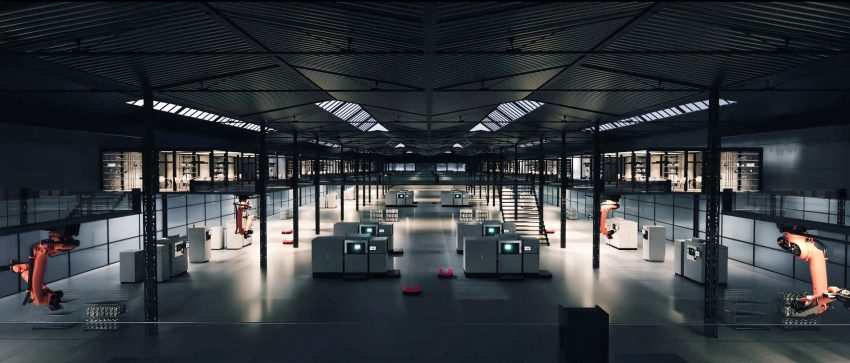
1. Connectivity and Data management
In additive manufacturing, data is being generated continuously, at every stage of production. This includes data from hardware and materials, to data from different software systems (ERP, PLM).
To be able to use this data for insights and operational improvements, it’s crucial to ensure that no piece of equipment or bit of data stays in isolation.
The Industrial Internet of Things (IIoT) is the key technology enabling increased connectivity and data-gathering capabilities, through the use of sensors, transmitters, software and networking.
IIoT offers the ability to remove the silos between operational technology (AM machines and other equipment) and information technology (software and networks) to ensure a continuous, real-time transfer of data.
While the new generation of 3D printers come equipped with IIoT capabilities, manufacturers are still struggling to collect and analyse the data provided by IIoT. One of the primary challenges to using AM data is disconnected systems and manual processes, which don’t allow for real-time access to data.
One way to achieve better connectivity and access to data is through the use of specialised software that can link your machines and software systems, like ERP, PLM, in a single system.
Establishing such a system is possible through Manufacturing Execution System (MES) software, which serves as a centralised platform connecting AM processes.
Connectivity, enabled by MES software, puts data at your fingertips, enabling you to establish a seamless real-time stream of relevant AM data that supports full traceability and agile decision-making.
For example, MES software for AM can provide dashboard capability to track and document KPIs related to Overall Equipment Efficiency (OEE), such as machine usage, production output and time to repair.
This, in turn, allows for the optimisation of AM production planning, which underpins the advanced use of AM in your digital factory.
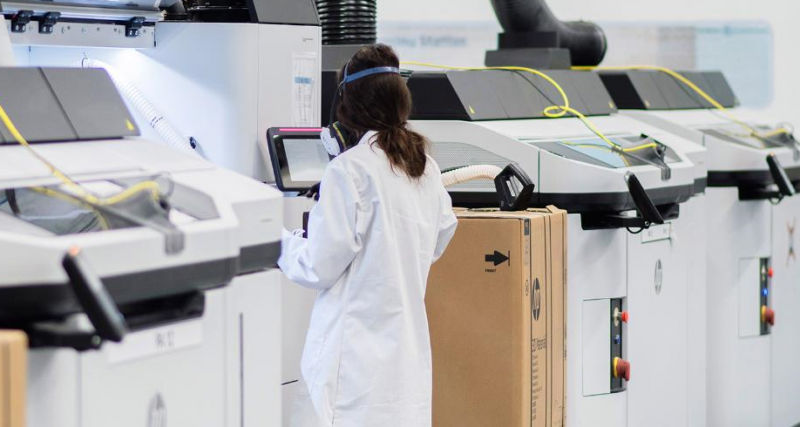
2. Automation
One of the biggest limiting factors for AM today is the cost of human labour for repetitive tasks. That’s why the key to bringing AM on the smart factories’ floors lies in end-to-end automation.
Achieved through a combination of hardware and software, as well as robotics, sensors and networks, automation ensures more streamlined processes as part of an end-to-end digital production cycle.
AM automation spans all levels of the AM workflow, from design to production, to parts handling and post-processing.
In the design stage, there are currently solutions that help automate some parts of the design process, like support generation.
Additionally, design tools, like topology optimisation, are evolving to help generate and validate the best AM designs for a given application and engineering requirements.
In the production stage, there is an opportunity to streamline production planning and management with the help of MES software. The software replaces labour-intensive processes, like manual order handling and project management, through the use of a single digital platform.
Furthermore, 3D printing hardware is becoming more automated through the use of sensors, enabling full process monitoring. One example of how companies can benefit from smarter hardware is remote maintenance, which, in case of a failure, enables companies to find a solution faster to ensure a high OEE.
Among all AM workflow stages, AM post-processing has long been the least automated. This is changing now, with the introduction of post-processing systems geared towards automated cleaning, depowdering, support removal and dyeing for 3D-printed parts.
Robots and automated guided vehicles also play a growing role in AM process automation by streamlining part handling and load/upload operations.
3. Traceability
Traceability is currently one of the key concerns facing companies adopting AM for production.
In manufacturing, traceability means the ability to track every part and product throughout the manufacturing process, from the moment when raw materials enter the factory to the moment when final products are shipped.
The importance of traceability goes beyond possible product recalls – it is also a question of improving visibility along the production process and enabling you to keep track of key data and optimise your processes.
The demand for traceability along the AM production process is driven by several factors, including:
- the need for adequate quality processes
- the need for accurate production data reporting
- customer requirements
With regulations, reporting and quality control requirements coming into play, the current lack of traceability across the AM ecosystem and supply chain must be tackled if AM is to be integrated into a smart factory.
One challenge to this is the ability to trace reused material. For example, in metal Powder Bed Fusion technology, after the printing process is complete, some amount of metal powder remains unmelted and can be sieved and then blended with a new powder in a specified proportion.
The material reuse process must be traceable, so that end users can be assured that they are using high-quality materials to build critical parts.
Several software solutions are currently available to track the origin of powder, the number of times it was recycled and in which builds it was used.
Furthermore, batch traceability is essential to ensure that parts in each batch comply with any safety or quality standards.
If a part fails, for example, the root cause will need to be identified. Having a system that allows operators to track the cause of a part failure is a fundamental example of traceability at work. Without the right data at hand, achieving this level of traceability is impossible.
One example of a system AM companies embrace to achieve traceability is MES. End-to-end traceability, enabled by MES software, can establish more effective quality management processes through data analytics and business intelligence tools.
Being able to track exactly what has happened to your 3D files and parts, and when, along the product life cycle, adds a new level of process quality for AM, as companies can easily review key data and optimise processes when errors or faults arise.
Establishing traceable AM operations is the first step towards using the technology for production, as it helps to ensure transparency and accountability throughout the supply chain and to prove that products meet certain standards and comply with industry regulations.
Tips on securing AM in a smart factory environment
There are several things you need to focus on to secure the AM data across your smart factory.
Educate your people
Firstly, you need to acknowledge that users can be your biggest threat. Staff may make mistakes that put your company’s data or systems at risk, often because they don’t have the required training to teach them how to protect the business they work for.
That’s why it must become your top priority to educate your staff and motivate them to pay attention to cyberthreats and countermeasures.
Manage access to your data
Secondly, you need to focus on how you manage access to data, as well as follow encryption and strong authentication practices.
Several companies are developing security solutions for AM, enabling you to encrypt design files, so only authorised users have access to the data enclosed.
Switch to secure file formats
Another consideration is to adopt standardised file formats that support secure data transfer and interoperability.
While the AM industry continues to rely on an old-fashioned .stl file format, there have been moves to replace it with a more efficient file format, called .3mf. Compared to .stl, the new file format has been designed with data protection capabilities in mind that prevent commercial misuse of data or data corruption.
Invest in AM hardware with security features in mind
Furthermore, as 3D printer connectivity is increasing, you need to make security a requirement during the procurement process. Since your AM equipment will be serving you for many years, security features need to be integrated into the design of the equipment, to make maintenance and protection easier in a highly connected factory network.
While there are many possibilities for securing AM, the bottom line is that there is no single solution to address all of the issues. Rather, it will take a variety of technologies to adequately secure production-grade AM throughout the full lifecycle.
Scaling AM in a smart factory with the right tools
COVID-19 has shown the world that traditional supply chains and manufacturing ecosystems must become more adaptable and agile to keep up with changes and challenges brought about by the current crisis.
One solution lies in embracing digital technologies, like AM, as part of a drive towards smart manufacturing.
While many companies adopt AM, they will need to use the right tools and processes to set up a traceable, automated, secure, and sustainable workflow.
A large part of these requirements can be achieved with the help of MES, designed for the unique needs of the AM technology.
Additive MES software enables manufacturers to link production planning, scheduling and implementation into a digital thread that uses data to achieve greater visibility and establish best practice processes across the entire organisation.
Only with a strategic goal and the right tools and technologies in place can manufacturers lay the groundwork for the long-term AM success in their factory of the future.
Source: https://facfox.com/docs/kb/additive-manufacturing-in-a-smart-factory-5-keys-to-success