This is Part 2 of our series on MES software. Discover the rest of the articles in this series:
1. Streamline production scheduling
Additive MES software gives manufacturers a reliable tool to schedule and prioritise AM production jobs.
As orders come in, additive production managers can use workflow software to easily group orders according to their production technology, material requirements and priority levels. The grouped orders create production batches, often called builds.
In advanced workflow management solutions, there’s also a feature that allows orders to be assigned to build jobs only when they meet the requirements of that build. This means that schedulers won’t be able to add, for example, parts to be produced in PA 12 to a build using PA 11. This feature ultimately helps to prevent potentially costly mistakes and rework, streamlining scheduling even further.
Takeaway: Use MES and workflow software to automate build preparation and ensure accurate scheduling.
2. Increase production planning visibility
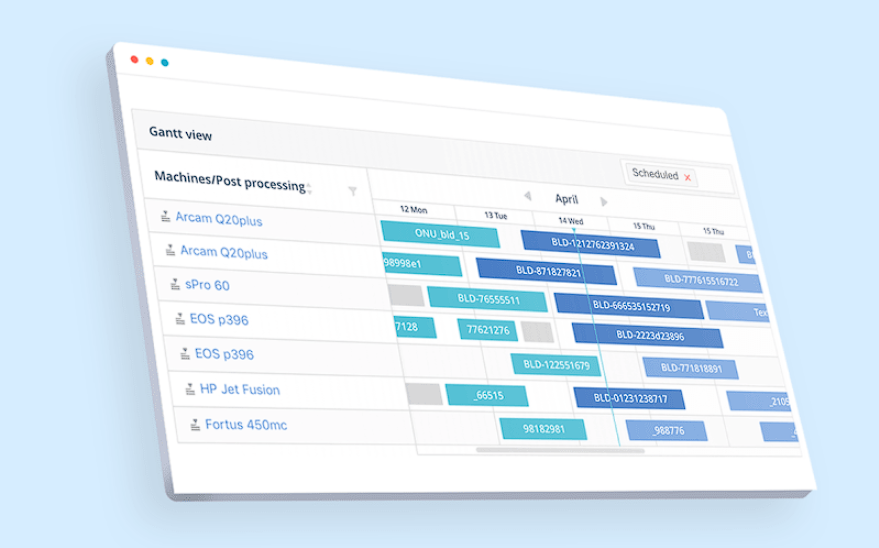
The Gantt chart provides the information relevant to production scheduling at one glance. For example, at AMFG’s Gantt chart you can see:
- A start and end dates of a build
- Build time and status
- Number of parts in a build
- Information about the machine and material used
Clearly defined dates and deadlines empower your staff to prioritise their work and meet deadlines. Furthermore, displaying an up-to-date AM job schedule helps to keep everyone (teams and customers) informed of the progress.
In addition to this, Gantt charts allow you to see a project’s timeline where you can easily see how and where the AM systems are being used. When machines are properly managed, AM jobs are more likely to be completed within budget and deadlines.
Takeaway: Use MES and workflow software to improve production visibility and better understand capacity.
3. Use MES software to create a data-driven digital thread
As we’ve seen, data is crucial to additive manufacturing operations.
Fundamentally, MES and workflow software provides a foundation upon which OEMs can track and analyse data across the entire AM production process, including post-processing and quality management.
Additionally, historic data can be accessed to provide key learnings and optimise processes.
KPI tracking, reporting and analytics are another way in which manufacturers can leverage MES software to take a deeper dive into the key factors that are driving productivity.
Having these processes managed by a digital platform provides a seamless digital thread and creates greater operational efficiency and traceability.
Takeaway: Use data insights provided by MES software to learn, scale and build a repeatable AM production process.
4. Ensure repeatability for serial production
For manufacturers looking to leverage AM to produce end parts, repeatability and predictability are key.
As we’ve seen, ensuring that the same part is produced every time and that quality standards are consistently met, is crucial for serial production.
For this, a repeatable workflow management process that ensures predictability is vital. Key criteria for this are:
- Part orientation
- Position
- Material
- Machine
Workflow software can track the parameters that have led to past success, giving you a high-level detail into the optimal process steps.
For example, the parameters needed for a specific part to be produced can be tracked by the system, and accessed again should the same part need to be produced. This, in turn, can be linked to the post-processing management steps that need to be taken immediately following production.
Bonus: Manage prototyping production more easily
When it comes to prototyping, typically, you will be producing a high volume of one-off parts.
Here, the challenge isn’t repeatability, but managing a high volume of requests for your product development and other teams.
Conventional methods of managing this, such as email and spreadsheets, are typically disruptive to the production planning process, as they lack integration with the wider AM workflow. MES software can solve this.
Takeaway: Use MES and workflow software to establish clear, standardised process steps that ensure production repeatability and predictability.
5. Gain a 360-degree view of your operations
MES software helps to maintain internal traceability of files, parts and processes. Each product or batch can receive its own identification number, which can also be assigned additional information throughout the manufacturing process, such as dimensions or QA results.
AM workflow software offers a ‘single version of truth’ that helps companies meet their quality standards and complete audit checks.
Takeaway: Using workflow software enables you to gain complete traceability across your AM operations.
6. Coordinate and manage suppliers more easily
A robust MES system is one that allows you to coordinate suppliers and manage outsourcing on one, standardised platform.
The benefit of this is that it keeps your suppliers and internal stakeholders aligned and up-to-date with the real-time status of specific tasks and actions.
Takeaway: Use MES software to manage your internal and external production, and streamline your supply chains.
Rethinking production planning with additive MES software
Additive manufacturing offers manufacturers a strategic opportunity to develop a competitive advantage.
However, just as AM requires a different approach to thinking about design, achieving the above objectives means rethinking traditional approaches to managing AM production.
In reality, this means adapting your internal processes to suit the requirements of AM production and ensuring that workflow steps are integrated to achieve efficiency, visibility and productivity.
Using systems that are disconnected from each other or highly manual is one of the biggest barriers to production efficiency and control.
Ultimately, MES software that can coordinate process steps, provide traceability and data-driven insights is the key to a solid production management strategy – and enabling you to scale your AM operations for the future.
Learn more about production management for additive manufacturing
If you’d like to learn more about how to scale your AM operations with software, we recommend reading our new white paper, Additive Manufacturing MES Software: The Essential Guide.
As well as providing more insights into production planning for AM, you’ll learn more about how to develop a comprehensive AM strategy and how you can use MES software to help you scale and expand your AM operations.