There are currently multiple additive manufacturing technologies that exist in the industry, each focusing on different materials and sectors. Today, we present to you our complete guide on Binder Jetting, a technology used for ceramic materials, metals, and more recently plastic polymers. How does this technology work? Which materials are used? Who are the manufacturers? We tell you everything below!
Binder Jetting technology was invented during an MIT project in 1993. Due to the quality of the results, the American company Z Corporation acquired it two years later, taking over all rights to this technology. Years later this corporation was acquired by one of the well-known giants in the industry, 3D Systems. Regarding Binder Jetting technology for metals, it was developed by the American company ExOne in 1996.
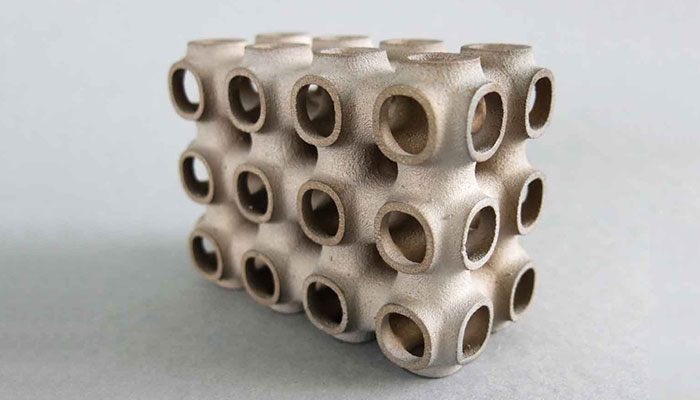
What is 3D printing using Binder Jetting?
The printing process with this technology consists of spraying a liquid binder onto a bed of powder, solidifying the cross-section of the piece, layer by layer. The materials that solidify thanks to the binder are usually gypsum, sand, ceramics, metals or polymers in granular forms.
As with any 3D printing technology, the first step is to model the object in CAD software, before slicing it and sending it to the 3D printer. A Binder Jetting 3D printer is normally composed of two tanks and a printing platform. At the beginning of the printing process, one of the tanks is empty, whilst the other holds the powdered printing material. The levelling roller spreads a first layer of powder over the platform. The print head, similar to those of 2D printers sprays the binding agent in the form of droplets of 80 μm. As a result, the powder is unified and the piece is formed, layer after layer. It is possible to print in colour using this technology. For example, in the case of ceramics, the colour is added at the same time as the binder. As the binder and colour is added to the successive layers of powder, the piece is formed in full-colour.
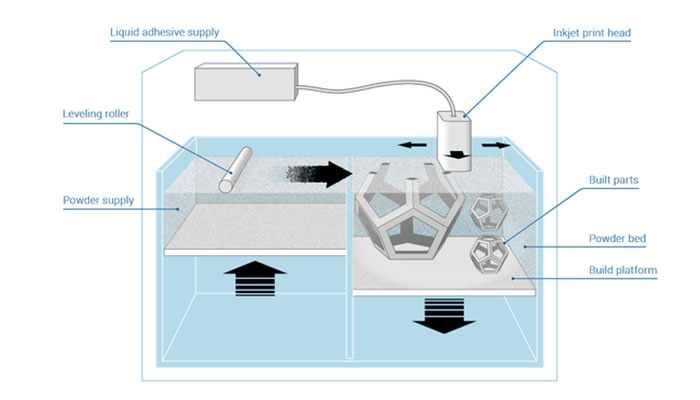
Once printing is complete, the pieces must be freed from the unsolidified powder that covers them. They also need to be cured to increase their resistance and revive the colours. The powder residue is removed with a brush or using pressurised air. Depending on the material used, be it ceramics or metals, a further step is necessary. In the case of metal Binder Jetting, the pieces must be sintered or infiltrated with a low-melting-temperature metal such as bronze. In the case of coloured ceramic pieces, it is also necessary to cover them by adding acrylic in order to improve the colours and mechanical resistance of the pieces.
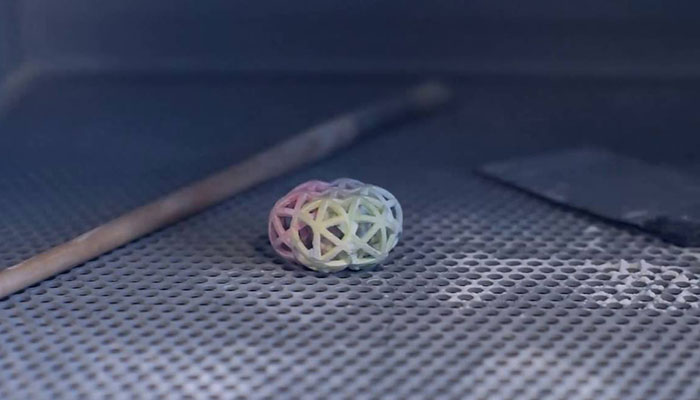
Materials used with Binder Jetting technology
Binder Jetting technology has been widely used for ceramic 3D printing because it can work with all materials belonging to this family. Moreover, this technology even enables 3D printing with sand, the only material that does not require additional post-processing. As far as metals are concerned, the Binder Jetting technology allows the production of various types of metal alloys such as 420SS/BR and 316 inxodibal steels, titanium, and others such as Inconel 625 or copper. Recently the possibility of printing with some thermoplastic polymers and polyamides has also been added.
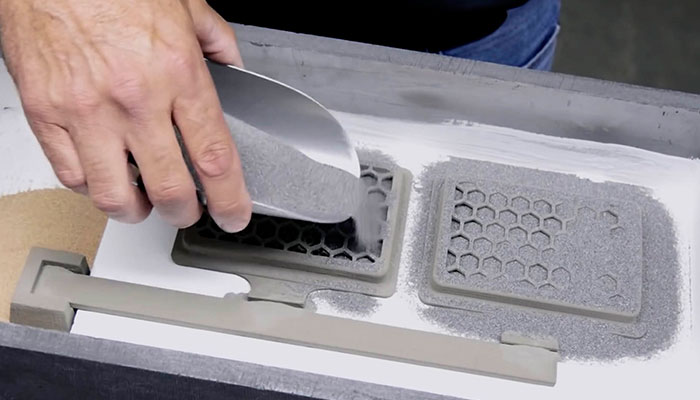
Actors and Developments
The Binder Jetting technology can produce metal parts or colour prototypes at a lower cost than using other technologies such as DMLS or Material Jetting, although there is greater porosity in the parts which could affect the mechanical properties of them. This technology is valued for producing batches of parts due to the large printing volume of most machines.
Currently the main manufacturer of 3D printers that use Binder Jetting technology for ceramic materials continues to be 3D Systems, using the term ColorJet Printing to refer to this technology. We also find companies such as the German manufacturer Voxeljet AG, supplying machines that also allow printing with thermoplastics. And finally, CONCR3DE, the manufacturer from the Netherlands. Recently the Taiwanese company ComeTrue was founded, offering Binder Jetting desktop 3D printers. With regard to metal technology, the leader continues to be ExOne, and other players have emerged such as the Swedish company Höganäs with its Digital Metal machine.
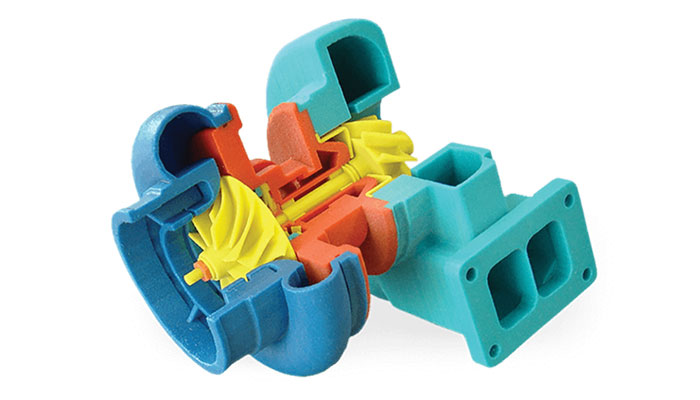
Another company that can be considered to use Binder Jetting is the giant HP, their technology is called Multi Jet Fusion. Since HP’s arrival in the additive manufacturing industry in 2016, it has been increasing the opportunities of its technology. It started with plastic materials such as polyamides, and expanded to full-colour 3D printing and is now reaching the metal AM market. Undoubtedly, contributing to the evolution of Binder Jetting technology.
In the following video from the CegepTR team, you can find some further information about Binder Jetting: