Traditionally, copper is a very popular material due to its thermal and electrical conductivity. Recent developments have opened new possibilities in additive manufacturing.
Copper is an extremely interesting material due to its conductivity properties and for being highly malleable.
These very same properties hindered its success as a feasible option for 3D printing. However, that has changed.
The most common technique for 3D printing copper is Powder Bed Fusion. It uses electronic beams to melt material powders and “glue” the material. When the temperature drops, the material consolidates together.
The most popular processes of Powder Bed Fusion are known as Selective Laser Sintering (SLS), for plastics, and Selective Laser Melting (SLM), for metals.
Despite SLM being an excellent printing process for many metals, there was a particular challenge when it came to 3D printing with copper.
The conductivity properties of the material cause the heat of the electron beams to be reflected instead of absorbed.
Another reoccurring problem was the fact that the printed part would crack when the temperature would drop too fast and/or too low.
Towards a solution: Green laser and pre-heating
Last year, researchers from the Fraunhofer Institute in Germany defied the status quo and developed a technique that made 3D printing high-quality copper parts possible.
Their solution consisted of switching the infrared laser from an SLM machine with a green laser. It sounds simple, right?
It is a bit more complex than that. A quick search on Wikipedia teaches us that laser is an acronym for Light Amplification by Stimulated Emission of Radiation. In short, lasers are light sources characterized by their wavelength in a vacuum. Each type of laser projects a concentrated beam that is amplified using stimulated radiation.
The light from this green laser for SLM printers developed by the German institute is better absorbed by copper which facilitates the melting of the material.
But the issue of cracking due to temperature drops was still there. The solution was to pre-heat the material before starting the printing process, which is sufficient to avoid a huge temperature drop.
This technique comes as the first real alternative for copper 3D printing, presenting a fantastic opportunity for manufacturers.
Machine manufacturer TRUMPF has applied these technologies in its new machine, the TruPrint 5000.
The machine uses TruPrint Laser Metal Fusion (LMF), a green laser, and preheats the material to 500 °C.
The TruPrint 5000 was demonstrated at the Formnext, 3D print fair in Frankfurt in November 2018.
The machine also prints with other precious metals – not only copper.
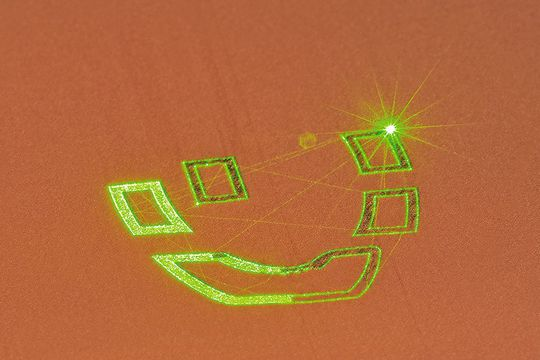
Copper Powder
If the challenges for printing with copper are indeed overcome, copper has the potential to be widely adopted in additive manufacturing.
As pointed out: copper has interesting thermal properties and together with the advantages of AM, particularly the design freedom, makes the additive manufacturing process beneficial for many thermal applications.
To anticipate the demand for copper in AM, different companies are developing special copper and copper alloy powders for the 3D printing market.
Applications
Copper is a soft, malleable, and ductile metal. Copper is a native metal with a has an orange-red color. It has a very high thermal and electrical conductivity.
Applications for copper are:
- electrical wiring (copper is a conductor of heat and electricity,
- building material for roofing, plumbing, decorative elements, and sculptures (for ex the Statue of Liberty is made from copper). The copper oxidizes and becomes a light green color.
- a constituent of various metal alloys, such as bronze (a copper-tin alloy) and brass (a copper-zinc alloy), and Sterling silver (silver-copper alloy)
- machinery and motors
- marine applications: copper is biostatic, bacteria or other life forms will not grow on it. It was used in shipping to prevent growth on hulls.
- sinks, faucets, doorknobs, handrails, etc. Because copper is biostatic it is used (in various alloys) in appliances that are handled by many people, to avoid spreading bacteria.
Conclusion
In summary, 3D printing with copper is fast becoming a reality. Technical hurdles are being overcome, and large companies are developing copper alloys in anticipation of market demand.