One of the greatest breakthroughs in the field of 3D printing materials in recent years was the launch of a process that makes 3D printing with silicone possible. Learn more about this exciting development.
Throughout history, inventions and breakthroughs in the field of material science have influenced the development of societies. And it is not very different nowadays. The likelihood of these breakthroughs having a significant impact on our technological future is extremely high.
Take 3D printing as an example. New material discoveries allow us to produce tools, mechanical parts, or even functional prototypes in a completely new way. But not only that, it also unlocks a new level of freedom for the manufacturing industry to design and innovate.
In the end, having a wide range of 3D printing materials available makes product development easier than ever before. Especially when these materials mimic their traditional counterparts but have had certain properties adjusted to fit new applications.
3D Printing Silicone is now possible
One of the most recent developments in additive manufacturing was the emergence of a new technology that enables the use of silicone as a 3D printing material.
The announcement brought excitement to the industrial 3D printing community.
After all, 3D printing with silicone, and by that, we mean real silicone, is a game-changer.
It serves so many markets: medical, automotive, consumer products. We can safely say that it is one of those breakthroughs that will truly impact our technological future.
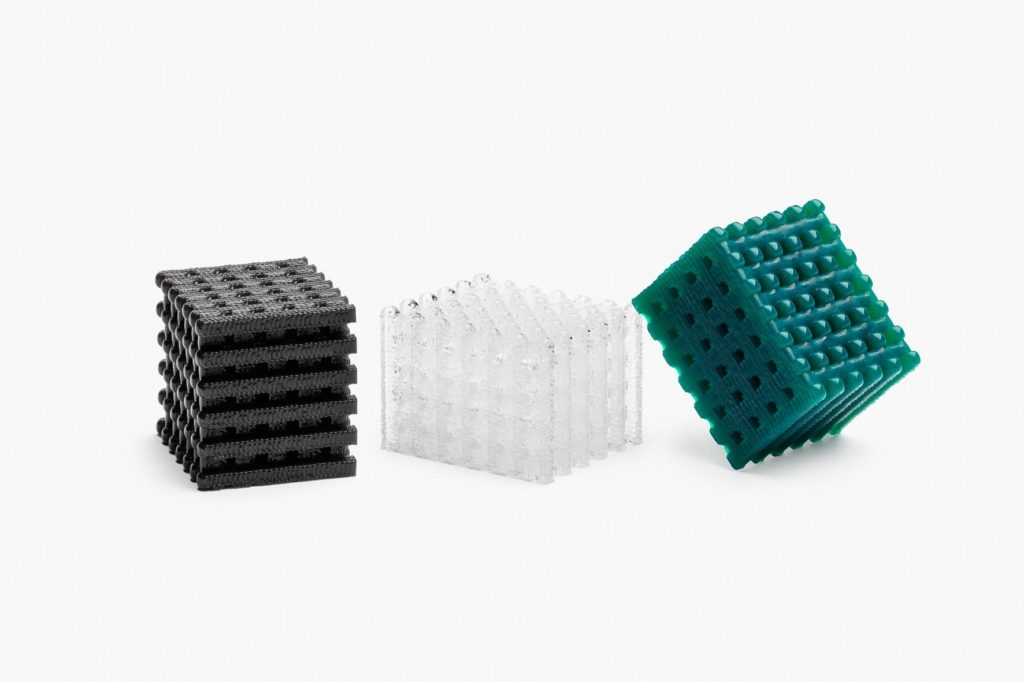
Before that, producing silicone parts were only possible through injection molding, casting, and compression molding. An extremely expensive process due to the high cost of molds.
Clearly not suitable for the creation of prototypes, bio-models, or small batches of products.
Ironically, the reason why silicone was so attractive as a 3D printing material was also what made it not a viable option.
It is not possible to melt silicone by exposing it to heat and then print a 3D object layer by layer like it is with plastics or metals.
For those reasons, several companies have attempted to develop materials that would simulate silicone although it was never truly the same.
The new technology, developed by ACEO ®- the brand for 3D printing with Silicones from the German chemical giant WACKER – has made it possible to create 3D objects from silicone materials without thermal changes.
The technology is a variation of the Material Jetting process based on a “Drop-on-Demand” principle. Basically, the print head deposits single silicone voxels on the build platform.
How does ACEO®’s 3D printer for Silicone work?
According to WACKER, their 3D printer for silicone functions just like an inkjet printer. The workspace and a robot are within a glass case.
One by one, tiny droplets are rapidly extruded from the nozzle onto to the printing area until a fine line is created.
A computer gives the exact coordinates in order to form the desired shape. The area is then exposed to UV light which causes the silicone to immediately vulcanize.
The process is repeated until the object is formed.
Once solidified silicone does not come back to its liquid state, so the final objects are – just like traditionally produced silicone parts – heat resistant.
Important to mention is the impressive precision with which the robot lays down the droplets to form extremely fine structures.
We have seen structures where the width of the silicone strip was just 0.6mm and half the thickness.
ACEO®’s Silicone material properties
Silicones manifold properties make it suitable for the most diverse applications:
- Temperature and radiation stability, allow it to be exposed to temperatures that vary from -55 to +180 degrees
- It has impressive elastomer properties, with a high variation of hardness being suitable for applications where a low compression set or high flexibility are required.
- ACEO®’s silicones have been tested for biocompatibility, making it a good option for several applications in the medical field.
- It is an insulating material that can be used for sealings in the automotive industry and other hydraulic applications where flow of fluids needs to be secured.
- ACEO® also offers a special grade of silicones that is electrically conductive and can be used in multi-material prints to provide conductivity and resistance for electrical components such as heat pads.
- Available in different colors but also translucent.
Can I buy Silicone filaments and resins?
At the moment, Silicone filaments and resins are not available for the market as most 3D printers for Silicone have been developed by companies that are not machine manufacturers.
On the other hand, silicone filaments and resins that can be found online are not the real deal – so be very careful.
The best way to 3D print in silicone is still through a silicone 3D printing service.
How to start 3D Printing in Silicone?
If you are looking for a silicone 3D printing service, you have come to the right place.
The first step to start 3D printing in silicone is to have an STL or OBJ file of the object you want to print. We prepared this silicone design guideline to help you make sure your part is 3D printable without further modifications.
You can upload your file to FacFox’s platform and our team will provide you with a quote as soon as possible. Don’t worry, all uploads are secure.