Somewhat ironically, many processes in additive manufacturing – which is often defined as a digital manufacturing technology – remain manual and siloed.
Automation is still not widely deployed in additive manufacturing. The vast majority of companies adopting 3D printing remain dependent on human labour and access to physical inventories.
Below we’ll be exploring the stages of maturity in additive manufacturing IT automation; areas companies should consider automating and software solutions available to help you digitise and streamline your additive manufacturing operations.
5 Stages of Maturity in Additive Manufacturing Software Automation
In our 5-stage model, automation as a spectrum spans different levels of increasing value and complexity. We take a closer look at each stage below:
Manual operations
With manual operations, companies’ employees spend a lot of their time on repetitive, labour-intensive tasks, including but not limited to:
- entering data into systems
- replying to customer requests
- calculating and providing cost estimates
- bringing USB sticks to AM systems to have files 3D-printed
- checking AM system status by looking over each machine
Native automation
Most AM companies are operating at the native automation stage in combination with manual processes. They use simple tools like Excel to analyse data or apps like Zapier to relay data from one system to another.
However, native automations are not entirely compatible with other systems and require human interaction to be value-adding.
While good for simple tasks, this stage of automation can’t be easily scaled and often leads to data silos and a lack of visibility, creating a disconnected, unoptimised business ecosystem.
If you face challenges in processing more information (e.g. 3D printing requests, file conversions/repair, project status update comms) or want to scale up your AM operations, you should consider leaping to the next stage of more efficient process automation.
Moving to basic automation
Basic automation is the form of automation technology solutions that address simple manual and repetitive tasks.
In AM, basic automation can mean a software solution that is taught a workflow with multiple steps and applications.
Here’s an example from a 3D printing lab at L’Oréal: before using automation, engineers would send emails with production requirements and 3D designs files, while a lab assistant would key in data to calculate the price. Then, the assistant would email the engineer who had placed the order about its status and delivery date etc.
To reduce this low value-added manual activity, L’Oréal adopted a 3D printing workflow software, enabling the company to automate each step in the ordering process. So instead of emails, engineers use a portal to send requests, and the backend system automatically calculates project costs and notifies the engineers about their project status.
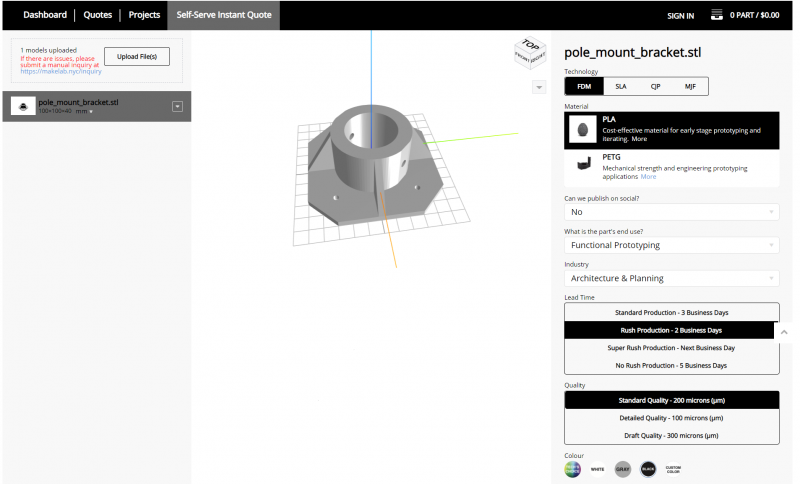
Basic automation with workflow software for additive manufacturing can go beyond ordering and customer comms. Some solutions offer rule-based automation for production scheduling, allowing files, once they are approved, to be assigned to specific machines and sent for production automatically.
Workflow automation software is designed to reduce the burden for employees of completing repetitive, time-consuming tasks. As an additional benefit, it helps enforce a repeatable workflow, which is critical for AM standardisation.
While basic automation already has many advantages, it shouldn’t be the end of your additive manufacturing automation journey.
Intelligent automation
If you need a solution that can help you automate end-to-end business processes, you may be ready to add intelligent automation to your AM operations.
Intelligent automation is about creating a seamless digital thread to enhance visibility and decision-making.
At AMFG, we empower companies to shift to intelligent automation using a set of solutions for control, execution and integration of AM workflow. For example, we can integrate with your AM systems for real-time machine monitoring or connect you to your manufacturing partners for direct routing of job orders.
This level of connectivity allows you to create a centralised and unified environment for AM (aka digital thread), aiding in enhanced production planning, traceability and standardisation.
Hyperautomation
Hyperautomation is the most mature level of automation technology that combines basic and intelligent automation with artificial intelligence (AI) and machine learning (ML).
AI and ML enable software to learn on its own by processing massive amounts of data.
Where automation can be the simple optimisation of tasks, hyperautomation has an extra layer of ‘intelligence’ that makes the processes even smarter.
Hyperautomation may be thought of as an “end stage,” but it’s one that is highly individualised and strategically driven, based on each organisation’s needs.
Hyperautomation is the right move for large companies that strive to transform their manufacturing through digitisation and set up smart, autonomous factories.
While still aspirational, hyperautomation is what some enterprises are currently working towards.
NextGenAM project
One example showcasing how automation can turn AM operations into a smart factory is the NextGenAM pilot.
EOS, Daimler, and Premium AEROTEC partnered to launch their NextGenAM initiative in 2017, which resulted in a digital, fully automated production line for serial 3D printing.
How have the companies achieved it?
The partners have established an AM production line with an EOS M 400-4 quad laser metal system, driverless transport, robots and software at its core. All the components were networked for maximum automation.
For example, before production, build job data can be sent to the control centre, which automatically prioritises the various build requests and allocates them to an AM system. The material is automatically transported to the AM system, which 3D prints parts and continuously monitors their quality through sensor data.
Once complete, the build is automatically moved to the next stage, where robots and machining centres handle post-processing steps, like part removal and quality assurance.
The result? Without manual input, the automated production line reduces manufacturing costs by up to 50 per cent, compared to currently available metal AM systems.
Achieving hyperautomation: the quest for interoperability
Because hyperautomation, by definition, involves a mix of technologies, it’s crucial for businesses investing in it to select the right solutions. By “right” we mean software that supports connectivity and interoperability.
If you’re looking for a tool or platform to power your smart AM factory, a good starting point is to search for one that is easy to use, scalable and works across platforms and systems.
Particularly the latter is a must, as acquiring a system that doesn’t speak with your organisation’s existing environment is a step back, slowing your progress and hampering productivity.
Challenges in additive manufacturing automation
Despite the clear benefits of software automation, many companies operating AM struggle to embark on digital transformation.
Many are halted by the cost of investment, deeming it unaffordable. In reality, however, the initially high investment pays off faster than expected, and companies can feel the benefits of automation almost immediately.
What makes the adoption of automation more complicated is not so much the cost as the lack of automation strategy.
AM companies need to be clear about the digital capabilities they need to aspire to – for example, what they need to buy, versus what they need to build. A thoughtful, structured strategy here will help to ensure that innovative ideas are not abandoned or overlooked.
It’s also important to understand that companies need to find the right level of automation to help them meet their organisation’s near-term and long-term needs. For example, this means that hyperautomation may not be for everyone – some companies could find their operations transformed by combining basic and intelligent automation solutions.
The final challenge companies face when implementing automation is the closed AM ecosystem. The AM industry is still largely dominated by proprietary systems which are not necessarily designed to work well with each other.
The good news is that the industry recognises the importance of becoming more open to creating integrated, interoperable 3D printing workflows.
Increasingly more AM hardware and software companies are providing open APIs – a software intermediary that allows one software application to communicate with another – to enable seamless data flow and integration.
One example is our recent collaboration with HP, whereas HP provided an open API to integrate with our additive MES system. This integration allows HP Multi Jet Fusion users to connect their machines to our software to monitor and collect data about their AM systems.
Scaling across each automation stage with advanced workflow automation software
When embarking on the digital transformation journey, it’s essential to invest in solutions that allow you to combine quick wins with larger longer-term benefits. At its core, such solutions should be modular, flexible and scalable.
At AMFG, we’re developing a modular workflow automation and manufacturing execution platform to help AM companies maximise their investment in additive manufacturing. Designed with interconnectedness and security in mind, our solutions integrate easily with your IT environment and AM systems.
Whether you’re just getting started with additive manufacturing automation, or are already further down the path, now is the best time to consider embracing new software capabilities and set the stage for accelerated performance gains and sustainable growth.