Tensile strength testing is a foundational engineering and materials science test broadly used for a variety of manufacturing methods such as injection molding, machining, and industrial-grade 3D printing (additive manufacturing). For 3D printing, the test provides insight into the quality and mechanical behavior of a 3D printed material to determine how it will behave under load. Tensile testing also aids manufacturers ensuring their process is consistent and in alignment with industry standards. Tensile testing is useful to perform when engaging in research and development activities around a new or changing material, manufacturing method, or product application.
This post explores how tensile testing is done, looks at how stress-strain curves are calculated, reviews commonly used standards for testing materials, and includes a comparison materials chart with associated tensile strengths.
Considerations for Additive Material Testing
First, let’s discuss how engineers test “dog bones.” Wait. What? Well, the tensile specimens or tensile bars, which are frequently used for testing 3D-printed material mechanical properties, are shaped like dog bones—hence the nickname. Imagine your typical dog biscuit for Fido, like a Milk-Bone biscuit (see photo). The dog bone for tensile testing is designed to have two opposing shoulders connected by a narrower cross-section. Each end of the specimen is gripped in a tensile testing machine, which applies tension until the specimen breaks. This narrower cross-section is designed to be a predictable point of failure in a tensile test. The cross-section can be round or rectangular in shape. Think about breaking a dog biscuit in half. Similar concept. It is easiest to break in the middle of the biscuit.
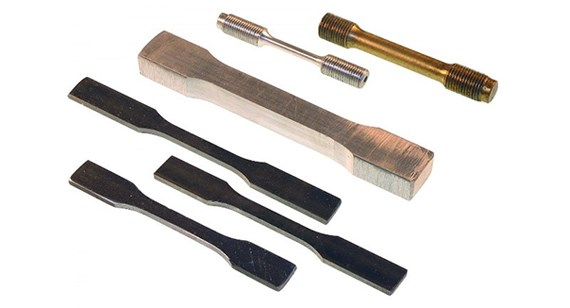
Securing the dog bone in the tensile tester is most often achieved with threaded or serrated pneumatic grips attached to load cells. One commonly used tensile testing machine (see photo) is offered by Instron. These tensile testers are tried and true machines that pull a specimen to failure at a programmed rate. The testers—or dog bones—are placed and gripped by the opposing grips. The crosshead pulls the dog bone at a constant rate until it deforms and breaks at its weakest point. A load cell precisely measures tension applied to the specimen and an extensometer measures how much it stretches. This allows the machine to generate a stress-strain curve for analysis.
Stress-Strain Curves Calculated
Force, displacement, and “strain” (how much the material stretches), are measured, and the strain-stress curves are graphically displayed to give insight on a myriad of material properties.
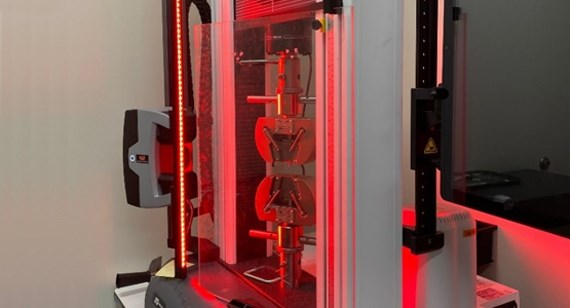
Commonly reported mechanical properties include ultimate tensile stress (maximum stress the part experiences under tension) and elongation at break (how much the “gauge length” stretches before breaking). Elastic modulus can be calculated from these values by dividing stress overstrain.
Test a statistically significant number of dog bones, and you will gain insights for your research and development application or quality control measure.
ASTM Standards for Testing Materials
The most commonly used and accepted standard for testing plastic materials is ASTM D638 – 14 Standard Test Method for Tensile Properties of Plastics. FacFox uses this standard to test plastic 3D-printed materials. For certain 3D printing processes, build orientation plays a role in mechanical property outputs. For FacFox’s SLA materials, the testers—or dog bones—are 3D printed and reported in the xy plane, meaning the test pull direction is in line with the layer lines. For FacFox’s selective laser sintering materials, dog bones are 3D printed and values are reported in both the xy and z planes.
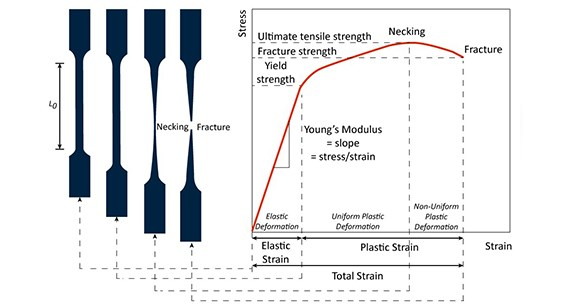
The most commonly used standard for testing metal materials is ASTM E8/E8M – 09 Standard Test Methods for Tension Testing of Metallic Materials. For 3D-printed metal materials, there are a handful of dedicated ASTM standards that address expected mechanical properties for powder-based sintering applications. For FacFox’s direct metal laser sintering materials, tensile bars are 3D printed vertically, meaning the test pull direction is transverse to the layer lines. Below is a list of standards used to test and report for each metal 3D printing material.
DMLS MATERIAL | STANDARD |
---|---|
Aluminum AlSi10Mg | ASTM F3318-18 |
Cobalt Chrome | ASTM F3213-17 |
Inconel 718 | ASTM F3055-14A |
Stainless Steel 17-4 PH | AMS5604G |
Stainless Steel 316L | ASTM F3184-16 |
Titanium Ti6Al-4V | ASTM F2924-14 |
Comparison of Tensile Strengths: 3D Printed Materials
The tensile strength chart at left (click to enlarge) shows a representation of FacFox’s materials and their associated tensile strengths.
SLA materials tend to be hard and brittle when compared with injection-molded equivalents. They have a high elastic modulus and little elongation occurs before the dog bone breaks. SLS and MJF nylons are tougher than SLA materials so they tend to have a lower elastic modulus and longer elongation. SLS, MJF, and SLA show some variation of strength depending on the build orientation of the part—this is typically due to weaker bonding between layers, but all three are superior to Fused Deposition Modeling (FDM or FFF) in this respect.
As material development progresses, improved isotropic mechanical properties have been made possible, such as the high elongation, impact resistance, and flexibility offered by Carbon RPU 70 and FPU 50. DMLS metals have high strength characteristics with 17-4 stainless steel being the strongest and Aluminum AlSi10Mg being the weakest.