Ever since its inception, metal additive manufacturing has caught the attention of engineers and tech enthusiasts for its unconventional bottom-up approach and the buzz surrounding what it is capable of. Is it really advantageous to use additive manufacturing for a part that’s been reliably produced through subtractive processes for years? This article discusses this question and points out cases when metal 3D printing can be a good choice for the production of parts and when not.
Metal 3D printing (DMLS): The process overview
Conventional manufacturing technologies like CNC machining are normally subtractive processes which means it removes material in order to shape a product whereas metal 3D printing technology is additive. One of the most common and popular metal 3D printing technologies is direct metal laser sintering (DMLS).

The typical DMLS process begins by slicing the 3D design CAD file data into extremely thin layers, effectively generating a 2D model for each layer.
The machine uses a high-powered optic laser. Inside the build chamber area, there is a material dispensing platform and a build platform along with a roller used to move new powder over the build platform. The technology fuses metal powder into a solid part by melting it locally using the focused laser beam. Parts are built up additively layer by layer.
Cases when to choose metal 3D printing
Metal 3D printing comes with its own set of advantages over traditional machining. We listed here a few cases when it is worth considering metal 3D printing over CNC machining.
Your design is complex
When it comes to design complexity and freedom, metal 3D printing has a huge edge over conventional. Many complex designs cannot be manufactured with conventional technologies with as much ease as with 3D printing. Take a look at the example below.
This type of complex design can be very tough to machine with conventional technologies, even using 5-axis CNC machines.
Another advantage here is the low cost of complexity. Creating complex mechanical parts via traditional manufacturing requires precision and skills, especially for the assembly of complex parts, which means that price increases with complexity. It is not the case with 3D printing, which creates an entire piece in one process, instead of creating each component before assembling. Therefore, there is no added cost for complexity.
You urgently need metal prototypes
If the number of parts required is less, say 1 to 5 or so or for prototyping, metal AM is much more advantageous. Since the cost is almost the same for each added unit, it is possible to make a needed amount of changes to the part. It can be used for prototyping: you’d use 3D printing to make a prototype, and update the prototype until the required features are met. This is a crucial step before getting the product to mass production. It can also be used during the rest of the manufacturing process, to create unique pieces that can be more responsive to your needs.
Also, it can be faster to get metal 3D prints rather than CNC machined parts. CNC machining normally requires more time to stock materials, set up the machine, get the right tooling. As a result, it can take several weeks to have the first part in hand. For 3D printing, even for DMLS which is more complex than traditional ones, the part can be printed on demand and shipped without any ramp up or tooling, resulting in shorter lead time compared to conventional technologies. The combination of the reduced lead time and the more efficient prototyping process reduces the turnaround time. This is one of the biggest advantages of metal 3D printing.
You want lightweight and durable components
Aerospace and medical industries naturally require lightweight yet durable parts. Superalloys like Inconel 718, AlSi10Mg, Cobalt-chromium are known to be lightweight compared to their conventionally machined counterparts. Manufacturing a part with these alloys naturally makes them lightweight comparatively. As an example, GE’s renowned 3D printed fuel nozzles for its LEAP family of engines used to be made from 20 discrete parts coming from independent suppliers, but using direct metal laser sintering (DMLS) resulted in a single-piece component that’s 25 percent lighter and five times stronger than the original parts. Click here to learn more.
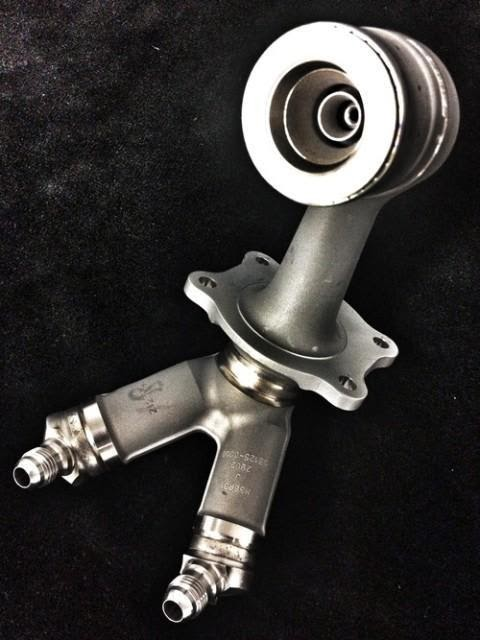
You’d like to avoid wastage of material
3D printing is incredibly resource efficient since the only material consumed is what passes under the laser (or through the extruder, etc.), whereas traditional CNC machining leaves chips and small pieces of metal that should be recycled. The fact that manufacturers don’t have to produce as much of a given product to justify the setup costs also reduces waste.
Disadvantages of choosing metal 3D printing
Apart from the advantages metal 3D printing possess over conventional technologies, there are a few considerations where preferring the latter is advised
Grainy surface finish
3D printing is an additive process, which means surfaces won’t be as smooth as with CNC machining, and that it won’t be as easy to produce the desired surface textures. So if the surface texture is important for you, CNC machining should be considered instead. Nevertheless, there are many post-processing techniques that are available to remove support structures, enhance the finish and improve the aesthetics, the cost also increases accordingly.
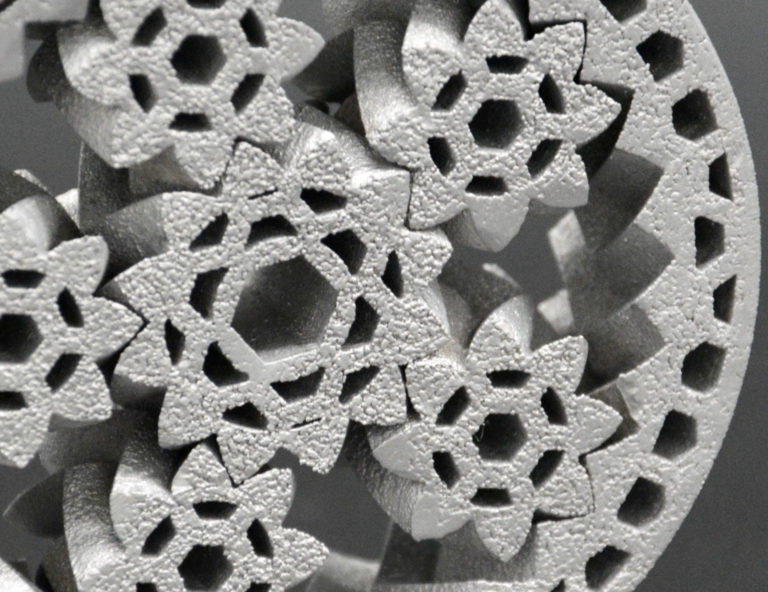
Less stronger parts
Because of the additive technology itself, metal 3D printed parts cannot be as strong as the one machined out of a solid metal block. The final strength depends on the design, size and material, but in general compressive strength of metal 3D prints is on average 40-50% lower than of CNC machined parts.
Expensive serial production
It becomes cheaper to mass produce through CNC machining. Mass production is still a huge deciding factor across the industries and this is where 3D printing lags behind and the speed at which a 3D printer can assemble an object often pales in comparison to the traditional assembly line.
Limited build volume
When large part size is required, it’s always better to go with CNC machining. For instance, the maximum part size that is achieved with DMLS is 250 x 250 x 325 mm and for CNC machining , it is 2000 x 800 x 1000 mm. The size comparison clearly shows the inability of 3D printing in manufacturing huge parts due to its limited powder bed size.
Limited material selection
Conventional manufacturing options like injection molding and CNC machining can offer a high material selection. When it comes to metal 3D printing, the material selection is lower, which can be a limiting factor when specific materials are needed for the required part, and must be taken into consideration when deciding which technical properties you want your product to have. As of now at FacFox we have five metal/alloy powders that support DMLS whereas if the required part needs some other material, there is no other option apart from traditional machining processes.
Summary
It cannot be said that metal 3D printing replaces traditional manufacturing technologies in all aspects as both of these have their own set of advantages where they shine and disadvantages where they don’t. Here is a brief summary of what are the strengths of both technologies:
Metal 3D printing | CNC machining |
Quicker turnaround | Mass production |
Prototyping and low volume production | Solid surface structure |
Ease of achieving complex designs | Use of materials and need for technical characteristics unavailable with 3D printing |
Reduced waste | Large-sized parts |
Customization and adaptability | Strong parts |
If you have ready designs, feel free to get a quote for both CNC machining and DMLS 3D printing in our Instant Quoting Engine to compare the prices and lead time.