What are they?
Prepreg carbon fiber and wet carbon fiber are two types of composite materials made of carbon fibers and resin. They are used for various applications that require high strength, stiffness, and lightweight.
How are they made?
Prepreg Carbon Fiber

Prepreg carbon fiber is made by impregnating carbon fiber fabrics with a controlled amount of resin, usually epoxy or phenolic, in a factory setting. The resin is partially cured to allow easy handling and storage. The prepreg material is then cut into sheets or rolls and stored in a cooled area to prevent complete curing. Prepreg carbon fiber requires an oven or autoclave to cure fully and form the final composite part.
Wet Carbon Fiber

Wet carbon fiber is made by applying resin to dry carbon fiber fabrics by hand or machine in a mold. The resin can be epoxy, polyester, or vinyl ester. The wet lay-up process involves placing the resin-coated fabrics into a mold and removing air bubbles with a roller or a brush. The resin transfer molding (RTM) process involves injecting resin into a closed mold that contains dry fabrics under pressure. The wet carbon fiber is then cured at room temperature or with heat.
What are the advantages and disadvantages?
Prepreg Carbon Fiber
Prepreg carbon fiber has several advantages over wet carbon fiber, such as:
- Higher fiber-to-resin ratio, resulting in better mechanical properties and lighter weight
- Better control over resin content and distribution, resulting in consistent quality and performance
- Less waste and environmental impact, as excess resin is removed during the impregnation process
- Cleaner and safer working environment, as resin exposure is minimized
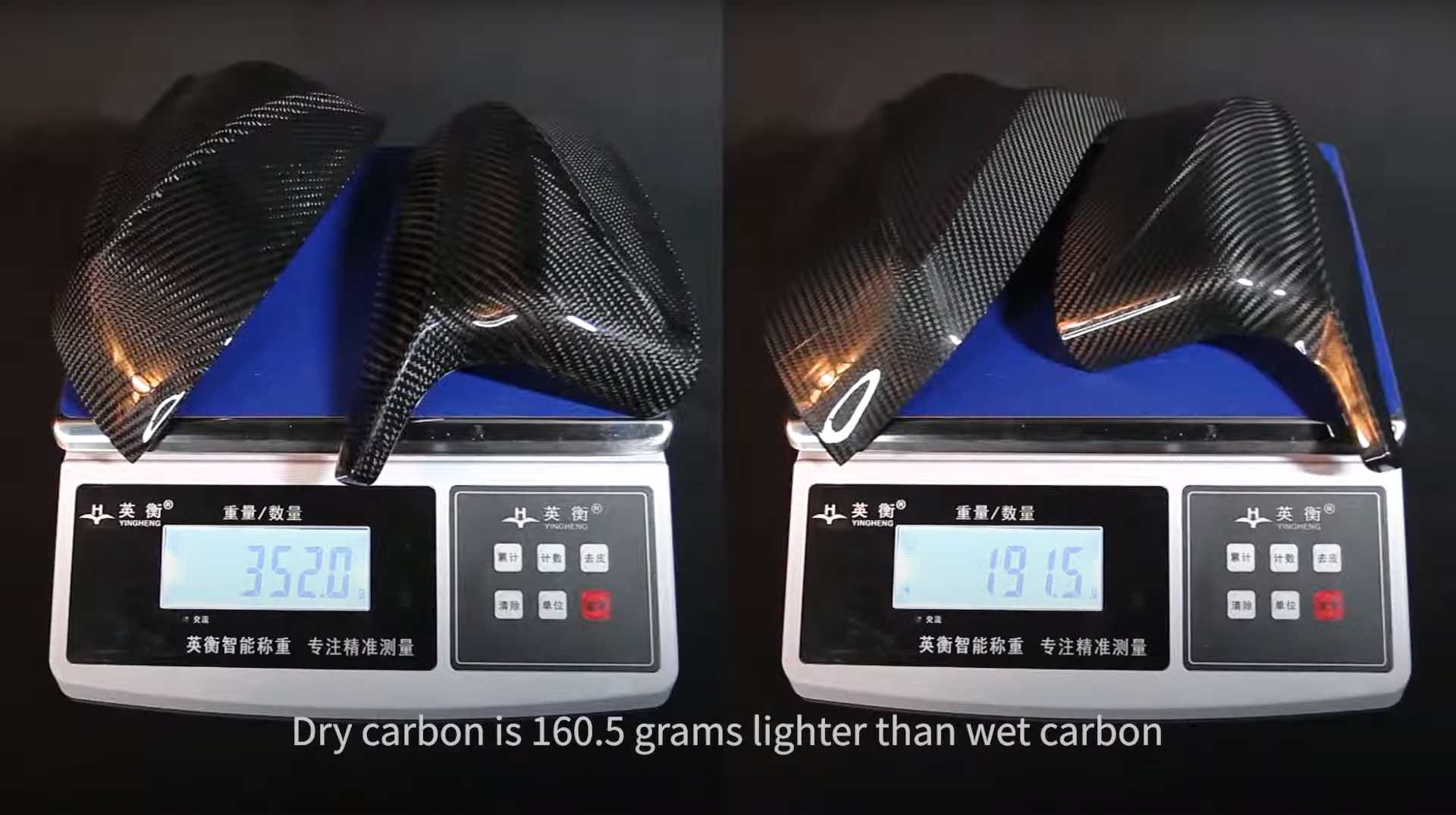
However, prepreg carbon fiber also has some disadvantages, such as:
- Higher cost, as prepreg materials are more expensive than dry fabrics and resins
- More complex processing, as prepreg materials require specialized equipment and skills to handle and cure
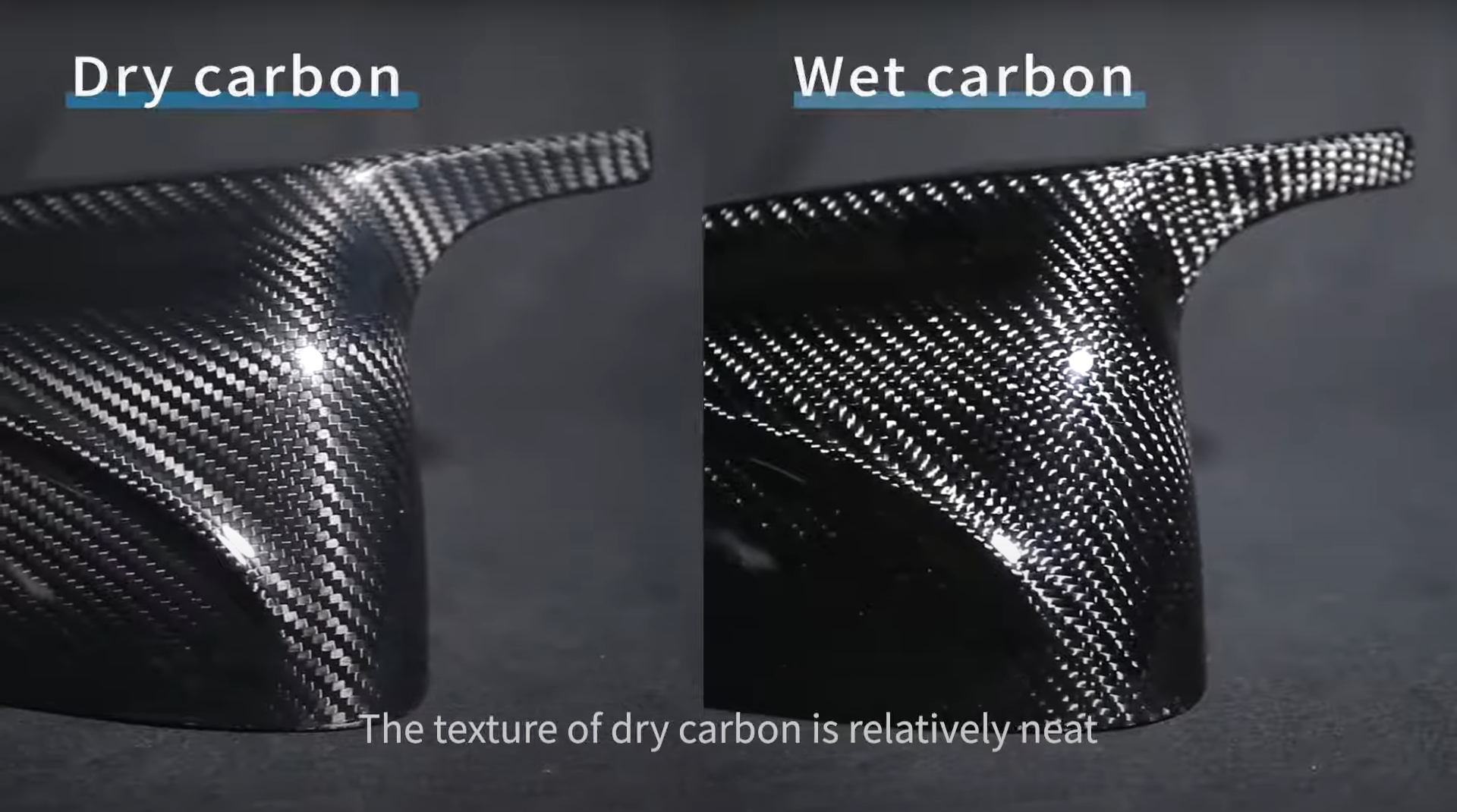
Wet Carbon Fiber
Wet carbon fiber has some advantages over prepreg carbon fiber, such as:
- Lower cost, as wet lay-up and RTM processes use cheaper materials and equipment
- More flexibility, as wet lay-up and RTM processes can accommodate complex shapes and large parts
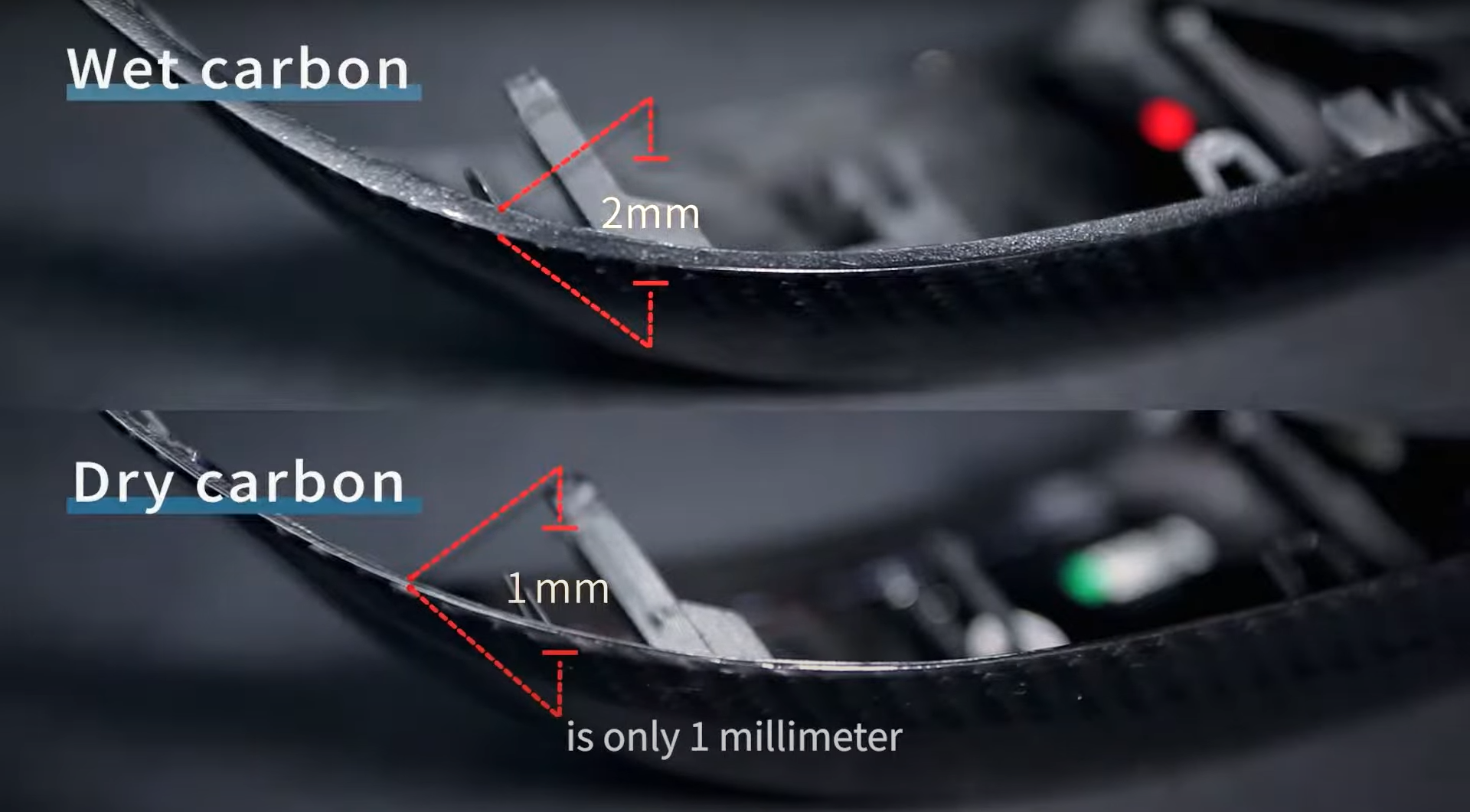
However, wet carbon fiber also has some disadvantages, such as:
- Lower fiber-to-resin ratio, resulting in lower mechanical properties and heavier weight
- Less control over resin content and distribution, resulting in variable quality and performance
- More waste and environmental impact, as excess resin is discarded or cured in the mold
- Messier and riskier working environment, as resin exposure is higher
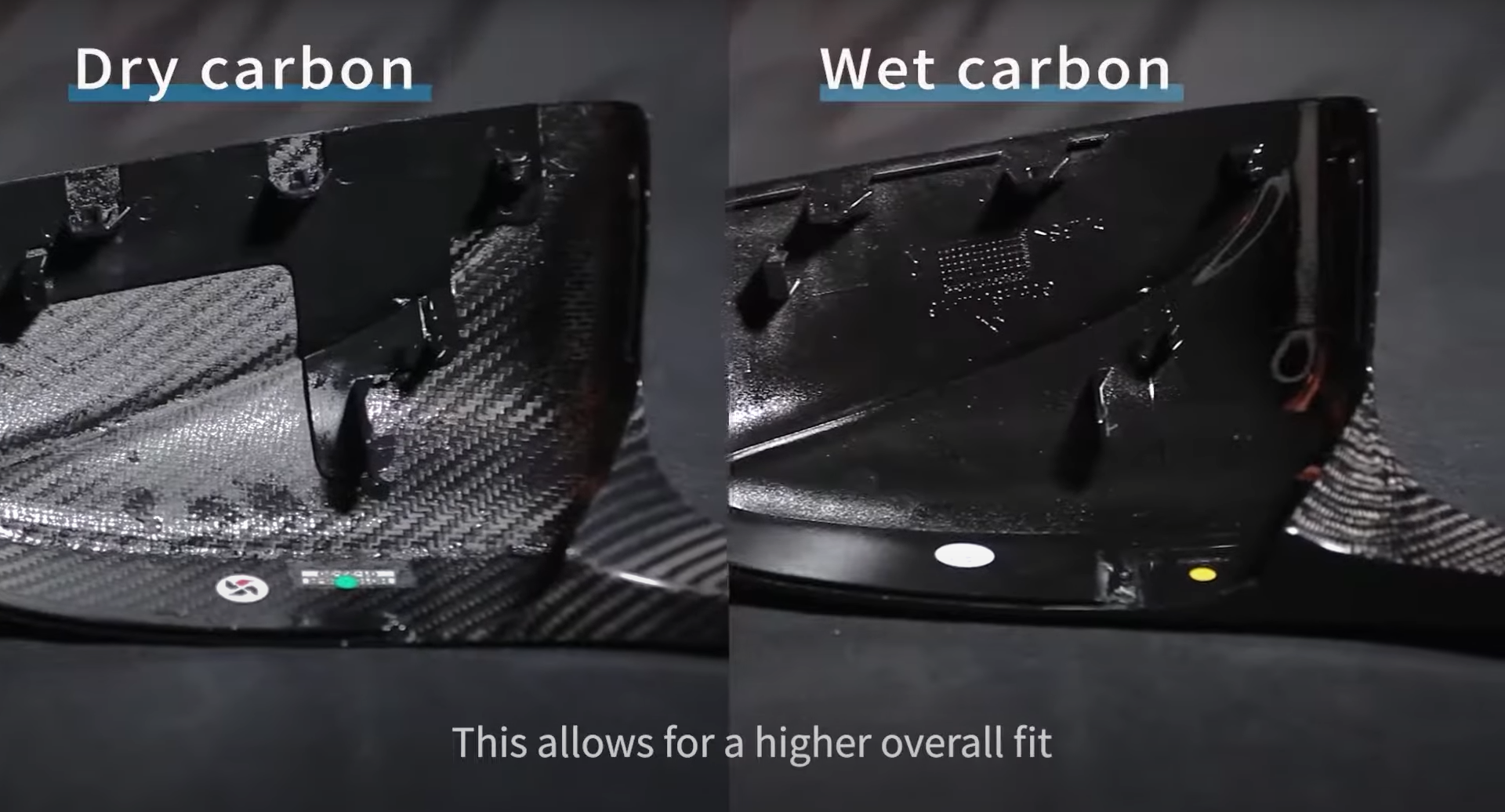
How are they used?
Prepreg carbon fiber and wet carbon fiber are used for various applications that require high strength, stiffness, and lightweight. Some examples are:
Application | Prepreg Carbon Fiber | Wet Carbon Fiber |
---|---|---|
Aerospace | Airframes, wings, propellers | Fuselage panels, interior components |
Automotive | Body panels, chassis, spoilers | Bumpers, hoods, fenders |
Sports | Bicycles, golf clubs, tennis rackets | Kayaks, surfboards, helmets |
Medical | Prosthetics, orthotics, implants | Wheelchairs, braces, splints |
Conclusion
Prepreg carbon fiber and wet carbon fiber are two types of composite materials that offer high strength, stiffness, and lightweight for various applications. They differ in their manufacturing processes, costs, and performance characteristics. Depending on the design requirements and budget constraints, one type may be more suitable than the other for a specific project.
If you are looking for a reliable and affordable way to manufacture carbon fiber parts, you may want to consider FacFox 3D printing services. FacFox is a leading online platform that provides high-quality 3D printing and post-processing solutions for a wide range of industries. FacFox can help you create complex and intricate carbon fiber parts using both prepreg and wet carbon fiber finishing methods.
You can choose from different types of fibers, resins, weaves, and curing options to customize your parts according to your specifications. FacFox also offers fast turnaround times, competitive prices, and professional customer support. Beyond these two technologies, we also have composite material like: Polymaker PolyMide PA12-CF, Polymaker Polymide PA6-CF, FDM Nylon 12 Carbon Fiber.
To learn more about FacFox 3D printing services and how they can help you with your carbon fiber projects, visit their website at https://facfox.com/ or contact them at info@facfox.com.