Introduction
Most low-cost desktop 3D printers are based on the Fused Deposition Modelling (FDM) technology. They are similar to their high-end industrial counterparts, since both are based on material extrusion and the layer-by-layer deposition of molten thermoplastic through a nozzle, but their capabilities differ.
This article will discuss the main differences between a typical desktop and a typical industrial FDM 3D printer and will offer guidance on selecting the right machine for your application.
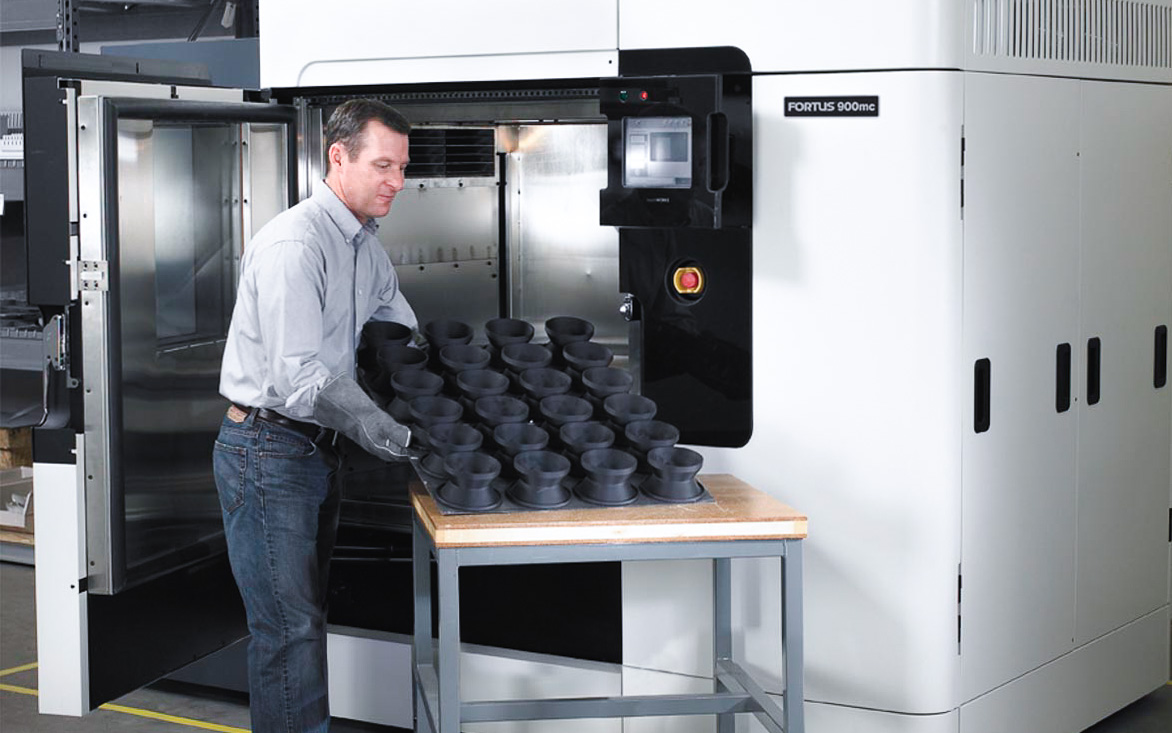
Summary table
The table below summarises the main differences of a typical desktop FDM 3D printer and a typical industrial FDM machine.
Property | Industrial FDM | Desktop FDM |
---|---|---|
Standard accuracy | ± 0.15% (lower limit ± 0.2 mm) | ± 1% (lower limit: ± 1.0 mm) |
Typical layer thickness | 0.18 – 0.5 mm | 0.10 – 0.25 mm |
Minimum wall thickness | 1 mm | 0.8 – 1 mm |
Maximum build envelope | Large (e.g. 900 x 600 x 900 mm) | Medium (e.g. 200 x 200 x 200 mm) |
Common materials | ABS, PC, ULTEM | PLA, ABS, PETG |
Support material | Water-soluble | Same as part (typically) |
Production capabilities (per machine) | Low/Medium | Low |
Machine cost | $50000+ | $500 – $5000 |
Accuracy
Generally the geometric tolerances and part accuracy are dependent upon printer calibration and model complexity.
Typically industrial FDM 3D printers produce parts of higher accuracy than desktop FDM machines, because of the closer control of the processing parameters during printing. Industrial machines run calibration algorithms before each print, include a heated chamber to minimize the effects of rapid cooling of the molten plastic (e.g. warping) and can operate at higher printing temperatures. Most of these machines support dual extrusion. This allows for the deposition of water-soluble support material, which is removed in post-processing and results in smoother surfaces and makes it easier to print complex parts.
On the other hand, desktop FDM 3D printers are now catching up and there are machines that support these advanced features (i.e. calibration algorithms, heated chamber, higher printing temperatures and dual extrusion). A well calibrated basic desktop FDM machine can produce parts with fairly high dimensional accuracy (typically with tolerances of ± 0.5 mm) and with the same minimum feature size as industrial FDM machines (i.e. approx. 1 mm). This accuracy is sufficient for most applications. Most materials used in desktop FDM printing allow for critical dimensions (e.g. holes) or detailed features (e.g. threads) to be machined accurately in a post-processing step.
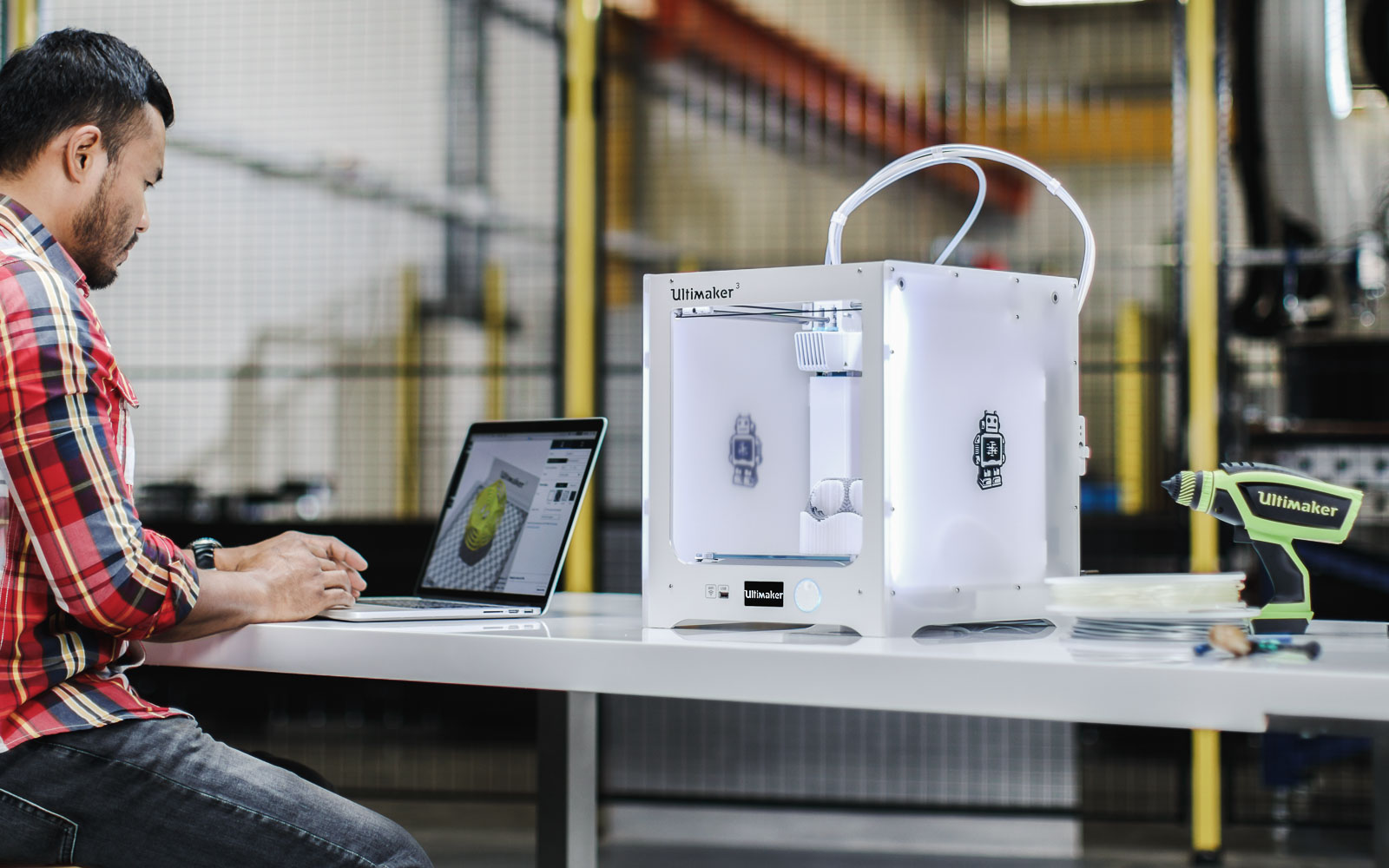
Materials
The material most commonly used on desktop FDM 3D printers is PLA. PLA is easy to print with and can produce parts with finer details. When higher strength, ductility and thermal stability is needed, ABS is commonly used. ABS is more prone to warping (due to shrinkage) and the geometry of the printed part can prohibit its use, especially in machines that do not have a heated chamber. Another alternative material that is rising in popularity is PETG, which has material characteristics comparable to ABS and is easy to print with. These three materials are suitable for most 3D printing applications, from prototyping for form, fit and function to low-volume production of models or functional parts.
Industrial FDM 3D printers use mainly engineering plastics (ABS, polycarbonate (PC) or Ultem). These materials are usually loaded with certain additives that alter their properties and make them particularly useful for a certain industrial need (e.g. high impact strength, thermal stability, chemical resistance and biocompatibility). Some materials printed with industrial FDM have similar material properties to injection molded parts and often times can be ‘good enough’ for creating functional end-parts. The temperature-resistant properties of these materials also mean that they are suitable for mold-printing for low-run injection molding.
Production capabilities and cost
A key difference between desktop and industrial 3D printers is the associated cost. The rise in popularity of desktop 3D printers has reduced dramatically the cost of owning and running an FDM machine, as well as the cost and availability of the consumables.
The production capabilities of an industrial FDM 3D printer are typically greater than that of a desktop 3D printer meaning that an industrial FDM machine can complete a large order faster than a desktop 3D printer. Industrial 3D printers also have a larger printing area, which means that they can produce larger parts in one print or print more models at the same time.
Industrial FDM printers are also designed for repeatability and reliability. They can often produce the same part over and over again. Desktop FDM printers require a high level of user maintenance and regular calibration.
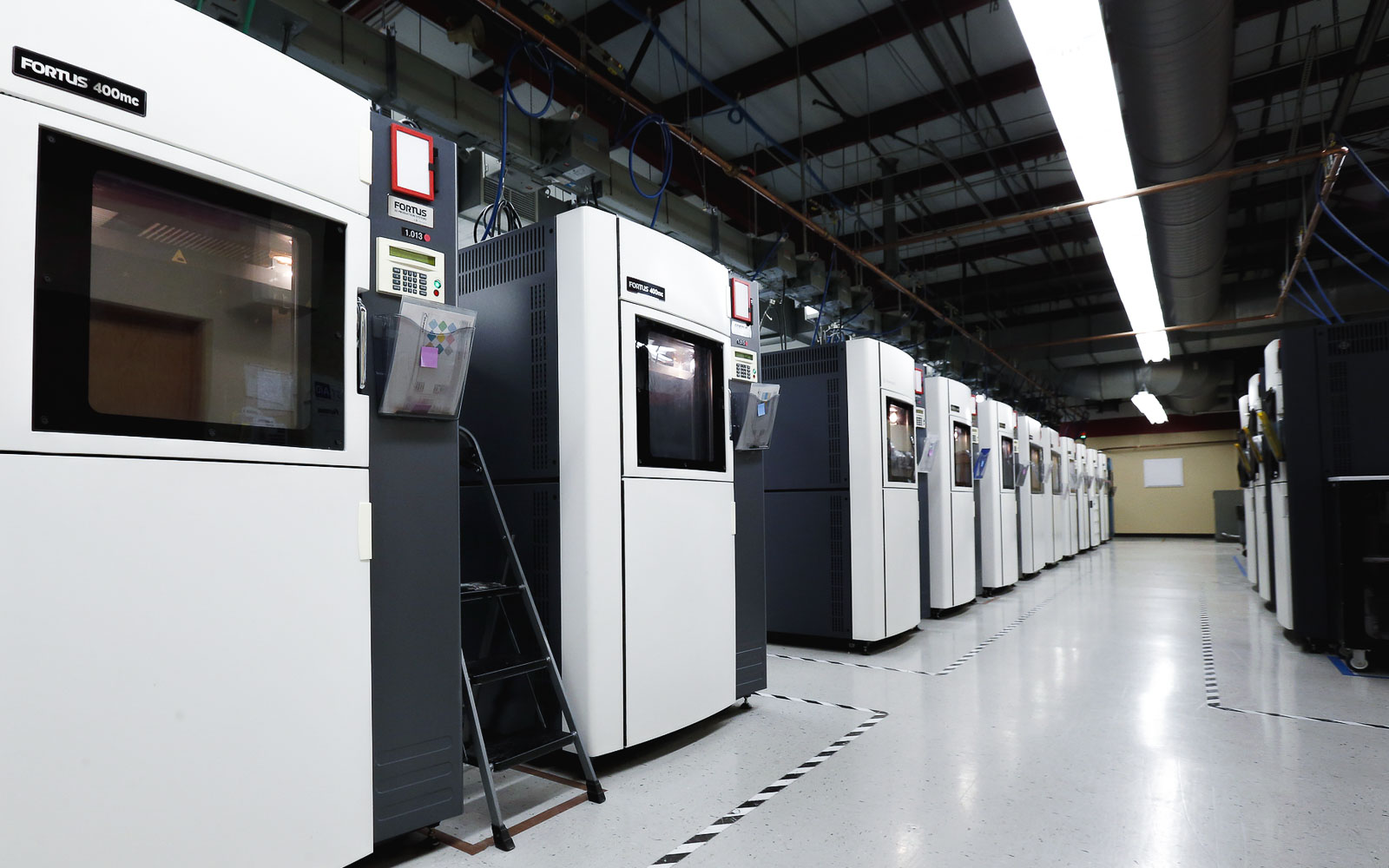
FDM expectations
FDM is one of the most popular 3D printing technique as it can produce high-quality parts from durable materials, which retain sound mechanical properties over time. The dimensional accuracy of both desktop and industrial FDM 3D printers is suitable for most prototyping, modeling or low-volume manufacturing requirements.
The minimum feature size of both grade of FDM machines is limited by the diameter of the nozzle and the layer thickness. Material extrusion makes it impossible to produce vertical features (in the Z direction) with geometry smaller than the layer height (typically 0.1 – 0.2 mm). The relatively high layer thickness also can introduce unwanted “stair-step” effect. Moreover, planar features (on the XY plane) that are smaller than the nozzle diameter (typically 0.4 – 0.5 mm) cannot be produced and walls must also be at least 2 to 3 times larger than the nozzle diameter (i.e. 0.8 to 1.2 mm). When smooth surfaces and very fine features are needed post-processing might be necessary (e.g. sandblasting, machining etc) or another additive manufacturing technique might be more suitable (e.g. SLA or SLS).
Rules of thumb
- For designs that require tolerances better than 1 mm, engineering materials that offer specific material properties (heat or chemical resistance) or a large build size (greater than 200mm x 200mm x 200 mm), industrial FDM 3D printers are the best FDM solution. These properties come at a higher associated cost.
- Desktop FDM 3D printers are suitable for prototyping and low-volume production requirements offering very short lead times and a wide range of materials at a low cost. The ± 1% tolerance is generally adequate for most fit and form prototype applications.
- When very fine details are needed the use of an alternative 3D printing method (such as SLA or SLS) should be considered.