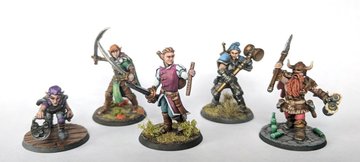
One of the most popular reasons for getting into 3D printing is to make stuff for other hobbies. People print their own tools, gadgets, and gizmos, as well as miniatures (typically 28+ mm) used for tabletop games such as Warhammer and Dungeons & Dragons.
There’s a widely held belief that resin printers are best when printing models with intricate details whereas fused deposition modeling (FDM) printers are thought to be better suited to bigger, bulkier models like terrain features or buildings. Straight out of the box, this can indeed be the case. But with the right amount of fine-tuning, it’s possible to get resin-like results from FDM printers.
In this article, we’ll be covering multiple areas where a little tweaking can bring outstanding results: layers, speed, supports, and cooling. Lastly, we’ll go into printer tuning and give you some additional resources.
Layers
The major benefit of 3D printing is of course the third dimension, height! A print’s vertical structure is achieved through a build-up of layers, but not all layers are created equally.
Two major aspects of a model are layer heights and top layers. Layer height is the thickness of each layer, measured in fractions of a millimeter. The thinner the layer, the more finely detailed the resulting object. However, truly tiny layers can result in huge printing times, layer defects, or even total failure, meaning that there must be a balance between time and detail.
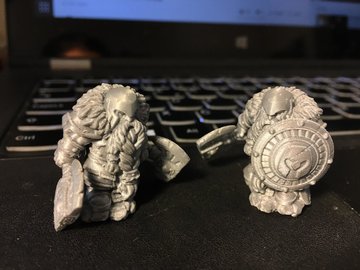
Tips & Tricks
- Start with a 0.01-mm layer height. This setting usually looks great without taking too long to print.
- Sometimes, quantity beats quality. Try increasing the layer heights for a faster print time on minis that work in a mob, such as an army of goblins. They won’t look as intricate, but players won’t mind if there is more to fight!
- Experiment with adaptive layers. For minis with areas of less visual importance, such as the base of this statue, try working with adaptive layers – maintain quality where it counts, and gain print speed where it doesn’t.
- Consider the top layers. When printing something with a flat top such as a base for your miniature, top layers become an issue. (“Top layers” refers to the number of layers on the top of your model.) The finer the layer height settings, the more top layers are required to give a smooth, flat surface and avoid pillowing.
Although these are all important aspects to consider, layers aren’t the only way to achieve your perfect miniature. Next, we’ll look at print speed.
Print speed is one of the most important considerations of 3D printing, and one of the trickiest to get right. Too fast, and you can encounter issues like blobs, poor layer adhesion, or even knocking the print off the bed entirely. Too slow, and you risk print failure from things like drafts or power surges as more time passes.
“Print speed” is a catch-all term for several secondary settings, and your specific print may require you to tweak some or all of them.
Tips & Tricks
- Slow down the initial layer. The key to a good print is a solid first layer, so, the slower the first layer prints, the better the base and adhesion of the rest of the print should be.
- Optimize your travel speed. This is the speed at which the print head moves while not extruding. If too low, you can encounter bloated print times for intricate models with lots of tapering points and valleys, like this model of Xenia, Hunter Heroine.
- Too much speed is dangerous. Be aware that if you increase the travel speed too much, the print could get knocked off the build plate entirely if it gets rammed by the nozzle.
- Tweak your retraction speed. The retraction speed is how quickly the filament is pulled back into the print head before traveling. If it’s not pulled back quickly enough, it can drip onto the model.
Now that we’ve addressed speed, let’s take a look at something else that’s crucial to get right the first time: supports.
Supports
Everyone needs support sometimes, and miniatures are no different.
In this case, support refers to the structures generated by the slicer program to keep the parts of the print that overhang the build plate, such as the wings and upraised arm of an Ashen Manticore model. Without supports, models like this would probably collapse, or in extreme cases, be printed in mid-air without anything underneath!
However, supports bring their own problems, namely that they have to be removed after printing, which can leave pockmarks or other damage on the model. Even worse, supports are often used for areas of visual focus (like dramatically upraised arms), which means any marks will be clearly visible.
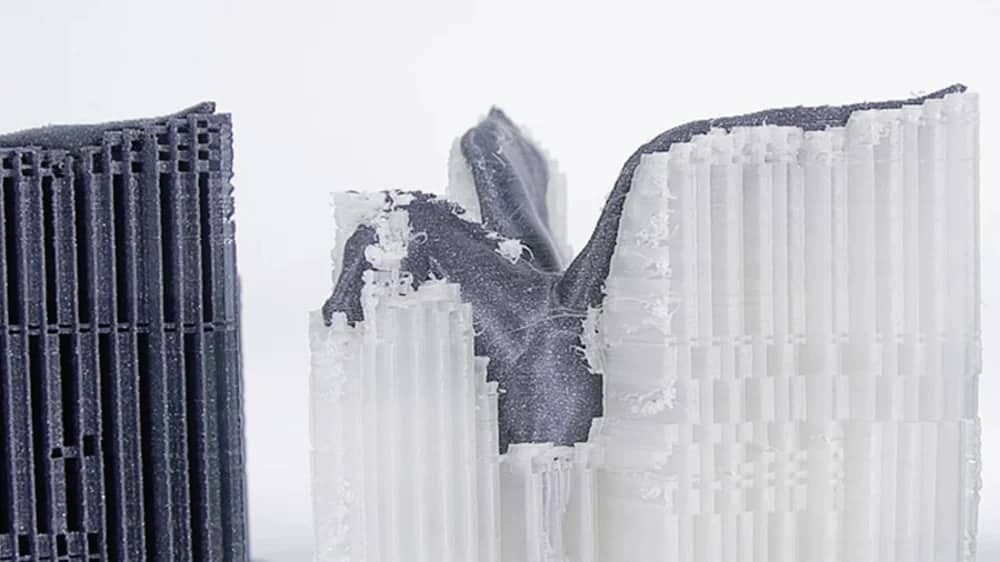
Tips & Tricks
- Use supports only on extreme overhangs. What constitutes “extreme” is a matter of debate, but 60° is a good starting point. Anything much less than that is wasting time, effort, and filament.
- Enable tree supports. Tree supports create structures that reach in from around the model to support it, like a hug, rather than straight up and down. This makes for fewer contact points and easier removal, while still being able to support the delicate parts of a model, like antennae or spears.
- Use a plug-in. Install the Custom Supports plug-in from Cura Marketplace, which allows you to place supports only where you think they are necessary, rather than relying on an algorithm.
Now we know how to support the delicate areas of a print, it’s time to think about the print as a whole.
Cooling
FDM printing is essentially the process of melting plastic and letting it cool into new shapes. However, there are ways to control these temperature changes for better results. Generally, printers use the cooling fan included with the hot end to blow air onto the print.
Cooling is more important for miniatures than for larger models, as the hot end will remain in a confined area for longer, which can increase the chance of artifacts or even deformation.
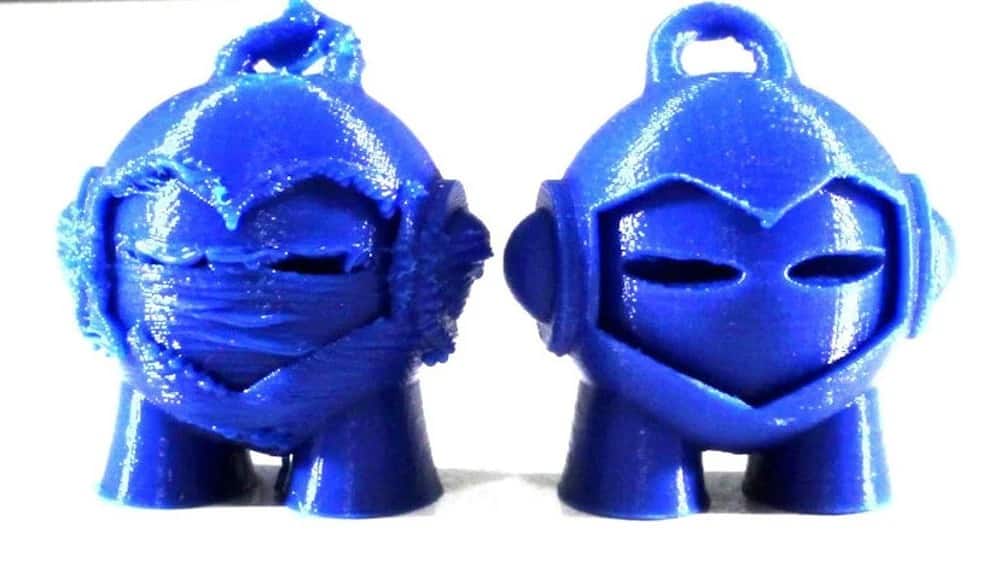
Tips & Tricks
- Ensure cooling is activated. Check this in Cura by going to the Cooling menu and making sure the “Enable Print Cooling” box is selected.
- Cooling is filament dependent. The level of cooling needed depends on what kind of plastic you’re using. PLA requires cooling during the entire print, while PETG and ABS require little to none, and can even fail if over-cooled. Check your filament spool or the manufacturer’s website for the suggested cooling temperatures for your materials.
- Print your own fan upgrade. Search for your printer model on a design site like Thingiverse to find printable upgrades.
While so far we’ve covered aspects relevant to your slicer, there’s one crucial element we haven’t mentioned: the printer itself.
Printer Tuning
Of course, all the software tweaks in the world won’t matter if the printer itself is busted. Regular maintenance of your FDM printer will enable you to print reliably and accurately, whether it’s an army of low-quality grots or an intricately detailed three-headed dragon. A few areas to keep in mind are bed leveling, nozzle cleaning, and the occasional upgrade if required.
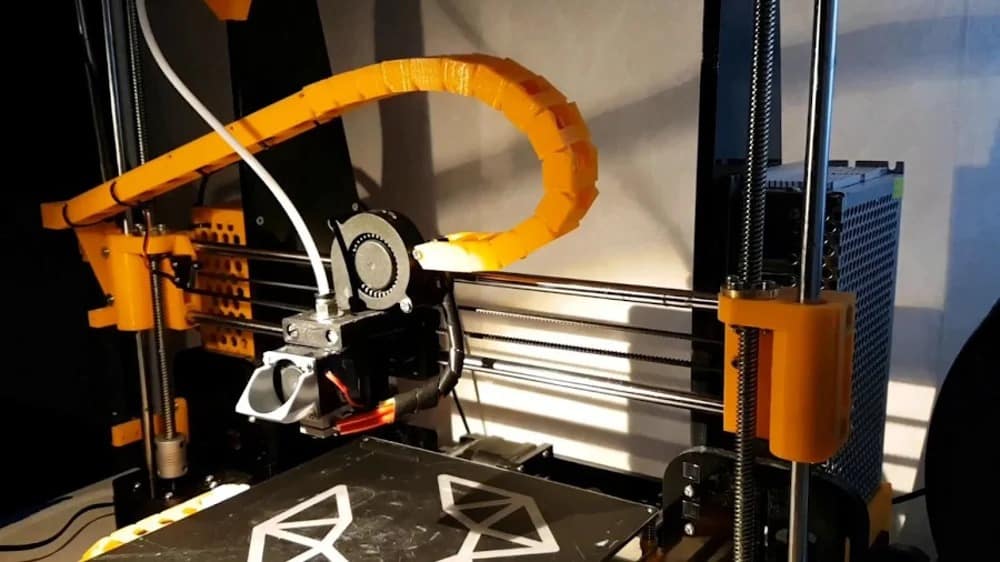
Tips & Tricks
- A clean nozzle is essential. A clogged nozzle can leave blobs on your mini, or worse, cause under-extrusion. If you haven’t changed filaments for a while, consider performing a cold pull to clean out any build-up in the hot end.
- Invest in spare nozzles. You can also purchase cheap replacement nozzles to switch out regularly. A side benefit to this is having a variety of nozzle diameters, allowing you to experiment with increased flow rates or thinner layer heights.
- Check your print bed is level. Bed leveling is probably the most-encountered problem printers have, as even a slight change in alignment can ruin a print. If you have a manually leveled printer, there is a downloadable G-code that you can run to help semi-automate the process. Alternatively, you can purchase an automatic bed-leveling sensor like the BLTouch.
If your printer came as a build-it-yourself kit, like the Creality Ender 3, the bed may not be perfectly level. This can cause your other calibrations to be off – and useless. To check, place your printer on a flat, stable surface like a table, and press down on each corner of the base. If it rocks, it needs adjustment. Thankfully, what can be built, can be modified. Check online to troubleshoot your specific model of printer.
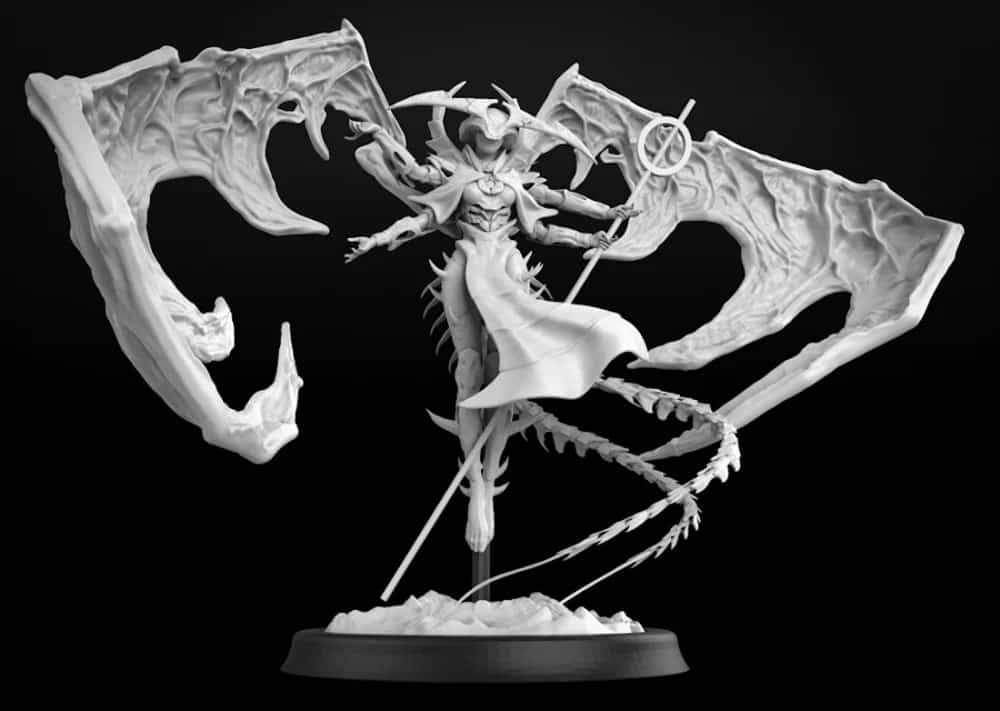
Other Resources
What we’ve covered with how to best print 3D miniatures is just the tip of the iceberg and might not even cover your particular printing needs. Rest assured that whatever you plan to print, there are tweaks and settings out there which can improve your miniature-printing game. A great source of specific information can be online communities, including Reddit and Facebook.