Online 3D printing is a well-known option for creating prototypes and parts for other designs. However, many of the orders we’ve received are for end-use parts that see both industrial and consumer applications.
An end-use part is meant to be sold or placed in use immediately after production. Although 3D printed products are often post-processed before use, this isn’t always necessary. Many 3D printing methods are capable of making functional parts that can be used as soon as the shipment arrives.
3D printed parts can be made from either plastic, metal, or ceramic. Both these types of materials can be used for end-use applications. Plastic 3D printing is often used to create cost-efficient, highly customizable items that can be produced quickly. The low price-per-unit and the extremely short lead times make 3D printing an attractive alternative to processes like CNC machining, vacuum casting, or injection molding.
There are three plastic 3D printing methods typically associated with end-use parts:
- Thermoplastic based process: FDM
- Resin-based processes: Laser-Based resin curing and HD Projector-Based resin curing
- Powder-based processes: Laser-Based Powder Sintering and Powder-Based adhesive technology
Each of these processes creates items with different structural integrities and design features. Many of the thermoplastic materials used are durable enough for engineering applications; 3D printed items might be used to supplement manufacturing processes, create industry-specific items, or meet structural requirements that can’t be achieved cheaply with other methods.
FDM/FFF: Simple, durable products with short lead times
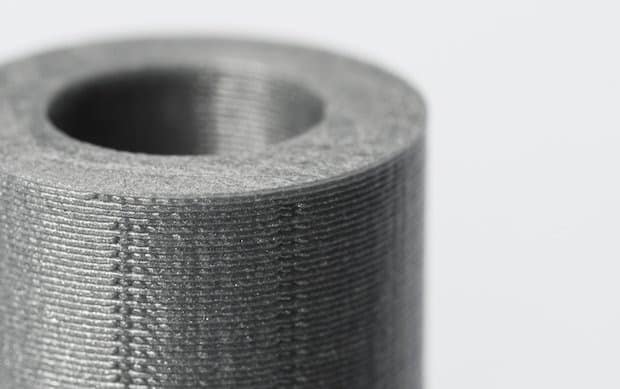
Fused deposition modeling, or FDM, is a classic and widespread printing process. An FDM printer creates objects by extruding heated plastics into the desired shape. FDM objects are easy to create and can be produced with extremely short lead times.
FDM parts can be created with either commodity or engineering thermoplastics. Common materials include ABS, PLA, and nylon. These materials are durable and easy to work with, but they don’t usually have consumer-ready finishes. Because of this, end-use FDM products are typically used for internal operations where appearance is less of a concern.
FDM can be used as an affordable alternative to most manufacturing processes. For small batches of less than 100 units, FDM is one of the most cost-effective manufacturing processes available. FDM printing avoids the startup costs and lengthy production times associated with CNC machining, vacuum tubing, and injection molding. Many engineers use FDM to replace single parts or to make small batches of items for an internal project.
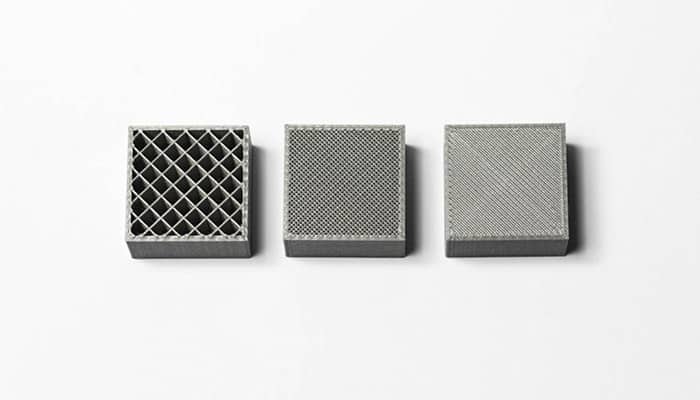
Use case: Jigs, fixtures, and brackets
FDM products are highly durable and can be manufactured to meet specific design requirements. This makes FDM an ideal choice for custom support structures like jigs and fixtures. The plastics can easily withstand physical pressures, and factors like appearance and heat resistance do not impact the efficiency of the final product.
FDM printing truly shines with its short turnaround times and cost efficiency in small batches. Engineers might use online 3D printing to create support fixtures for a single project; the parts will arrive quickly, and the cost will be much lower than if CNC machining or injection molding was used.
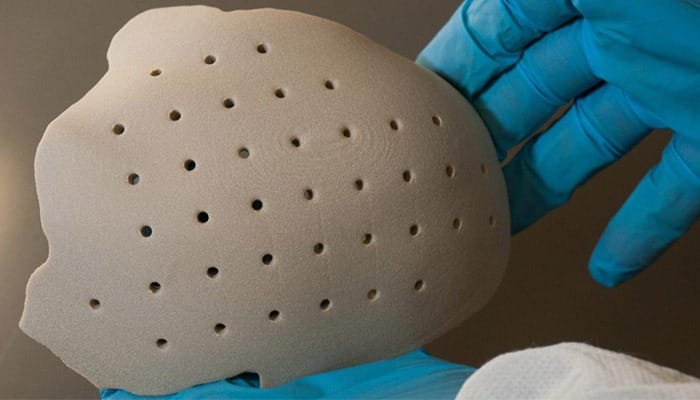
Use case: Medical equipment
FDM 3D printing can extrude almost any type of thermoplastic. Plastics like PEEK or ULTEM can be placed in an autoclave, and that means that they can be used for medical applications.
SLA/DLP: Consumer-ready parts with high detail
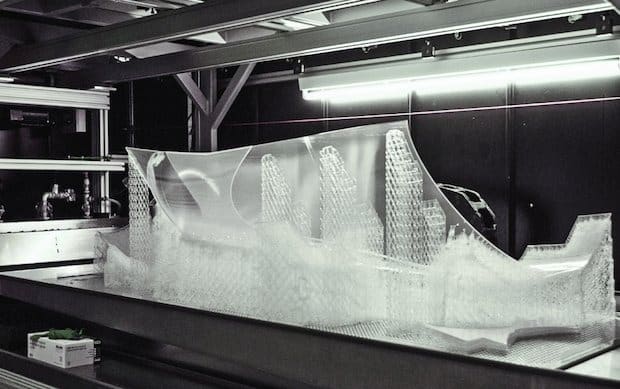
Stereolithography SLA 3D printing uses ultraviolet light to solidify layers of liquid resin until the object is created. This creates highly detailed products with smooth finishes similar to those produced by injection molding.
Thermoset resins used for SLA are slightly more brittle than thermoplastics, so SLA printing is typically reserved for parts where appearance and shape are more important than durability. However, engineering-strength resins are available and are often used when both appearance and physical strength are desired.
SLA printing is often used as an alternative to CNC machining or vacuum casting. SLA printing is most cost-effective in batches less than 50. This method doesn’t have the same startup costs as vacuum casting, and products can be created far more quickly than with CNC machining.
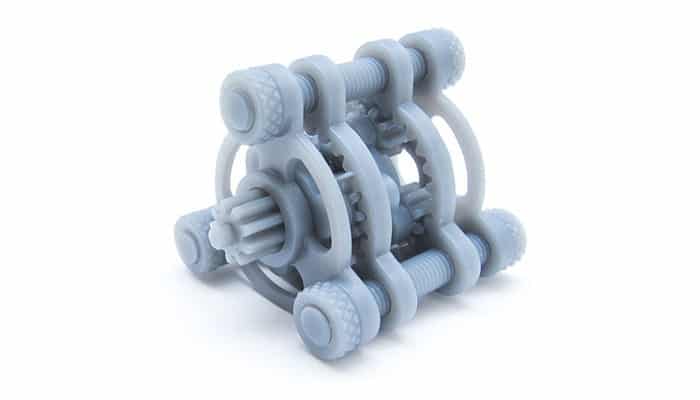
Use case: Mass customization
Thermoset resins are available in a variety of colors, so SLA products are an excellent choice for widely customized product lines. From hearing aids to razors, SLA printing can be used to produce small batches of matching items with slight tweaks to visual appearance. These products have low mechanical strength but are durable enough for daily use, and the smooth finish that results from SLA printing greatly reduces the amount of post-processing time required.
SLS/MJF: Small batches of functional nylon parts
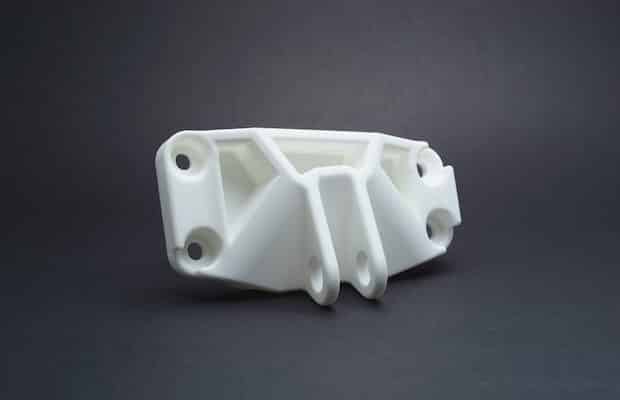
Selective laser sintering (SLS) and multi jet fusion (MJF) both create products by selectively binding polymer powders into structural layers. This results in parts with high structural integrity and internal uniformity.
SLS products are usually made out of nylon. Glass-filled and carbon-filled nylon can be used for added strength; thermoplastic elastomers like TPU or TPE are also available. The products made with SLS are typically much stronger than objects made with FDM, and they almost always feature higher thermal stability. Engineers often use SLS printing to create flame retardant and chemically resistant parts for industrial applications.
Other nylon manufacturing methods like CNC machining, injection molding, and vacuum casting are not cost-effective in small batches. SLS is a good way to make less than 300 units of a functional and resistant part.
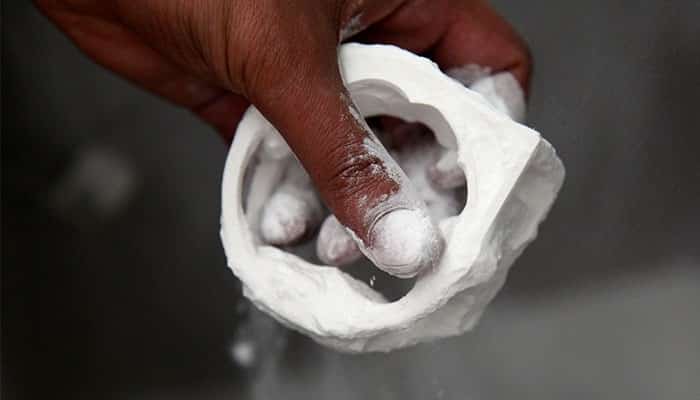
Use case: Low-run production
SLS creates the same kind of durable, usable products that could also be made with injection molding. However, since injection molding has a high startup cost, most manufacturers request a minimum order of 500 units. SLS printing is cost-efficient from the first unit and remains efficient for large batches, so a 3D printing service is often used for small to medium batches of nylon items in the hundreds.
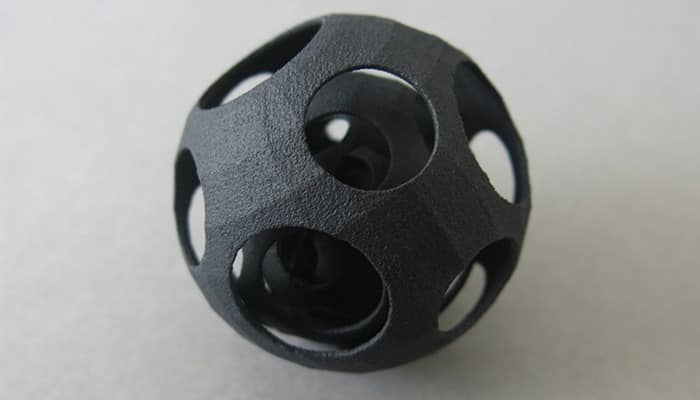
Pro tip: For a cost-efficient method of operation, mass-produce items with injection molding. When spare parts or replacements are needed, use SLS printing to create a small batch of matching nylon parts.
In general, most engineers choose FDM printing for internal applications, SLA printing for consumer-ready items, and SLS printing when structural integrity is the highest concern. Many end-use parts are also created with 3D metal printing; read part two for a detailed explanation.
The quickest way to get end-use plastic parts is with FacFox’s online 3D printing service. Upload any CAD file to the online manufacturing tool, and compare the prices and functional differences between printing methods. The free design for manufacturing analysis will check any design for compatibility with the chosen manufacturing method, and the instant quote generator will estimate both costs and lead time.