Forging provides a higher level of structural integrity than any other metalworking process while CNC machining offers many advantages in small-volume precise production with complicated shapes -that’s our common sense.
Ultimately, the manufacturer will look at a number of criteria before choosing which metalworking process is best for a particular application: cold forge, hot forge, or CNC machining? In this article, we’d like to discuss all the aspects which may alter your manufacturing decision.
Definition
Forge
Forging is a manufacturing process, which shapes a solid-phase metal workpiece by applying compressive forces on it. According to the temperature at which it is performed, forging is classified in “hot”, “warm” and “cold”. It involves using a mold which comprises the movable tool and the stationary die. A press that exerts tons of force pushes the two halves of the mold onto a sheet of metal, creating the desired shape.
Cold Forge
The cold forging manufacturing process is performed at room temperature. The workpiece is squeezed between two dies until it has assumed their shape. To deliver a finished, ready to fit component, the technique includes rolling, drawing, pressing, spinning, extruding and heading.
Hot Forge
The hot forging manufacturing process is performed at an extremely high temperature. This temperature is necessary in order to avoid strain hardening of the metal during deformation.
CNC Machining
CNC (Computer Numeric Control) machining, involves passing a lump of metal (or a billet as it’s known in the trade) into a machine tool. The machine has sensors built into position and guides the billet. It is fully motorized and is controlled by a computer panel. A rotating tool cuts away unwanted metal to form the part. The computer interpolates the design to give smooth curves and circles.

Temperature
Hot Forge
When a piece of metal is hot forged it must be heated significantly. The average forging temperature necessary for hot forging of different metals is:
- Up to 1150 degrees Celsius for Steel
- 360 – 520 degrees Celsius for Al-Alloys
- 700 – 800 degrees Celsius for Cu-Alloys
During hot forging, the temperature reaches above the recrystallization point of the metal. This kind of extreme heat is necessary for avoiding strain hardening of the metal during deformation.
Cold Forge
Cold forging deforms metal while it is below its recrystallization point, which means you can perform under the indoor temperature.
- below 360 – 450 degrees Celsius for Steel
- below 100 – 150 degrees Celsius for Al-Alloys
- below 200 – 270 degrees Celsius for Cu-Alloys
Cold forging is generally preferred when the metal is already a soft metal, like aluminum. Sometimes, when aluminum is cold-forged into the desired shape, it is heat-treated to strengthen the piece. This is called “tempering.”
CNC Machining
No doubt the high temperature affects the CNC machine performance and working. If the CNC machine workshop temperature goes too high, the CNC machine might stop working.
- the best-recommended temperature is 25 degrees Celsius
- generally the indoor temperature is enough
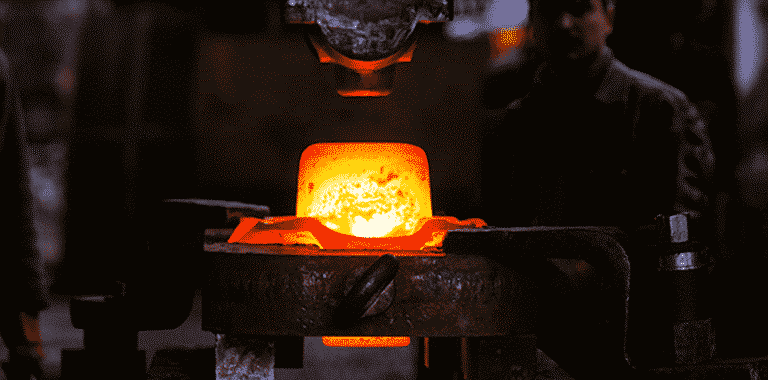
Material and Die
Cold Forge
The significant advantage of the cold forge is material savings achieved through precision shapes. The economic advantages combined with high production rates and long die life are more than enough to convince many manufacturers that cold forging is the best option for them.
However, cold-forged metals are less ductile, which makes them inappropriate for certain configurations.
Hot Forge
Hot forged components possess increased ductility which makes them desirable for many configurations. It’s also material-saving just as the cold forge process.
CNC Machining
CNC machining process takes time and depends on volume and complexity. It needs well-trained operators and high-end machines, which means higher initial costs.
CNC machines are quite complicated bits of kit with various motors and moving parts, thus it needs lots of oiling and continuous maintenance, further adding to the cost of running.
However, the real cost is in the amount of waste created. Metal is cut away from each fabrication, which ends up as shavings that can only be sold for scrap, meaning production overheads can mount up quickly if you’re manufacturing large numbers of intricate parts.
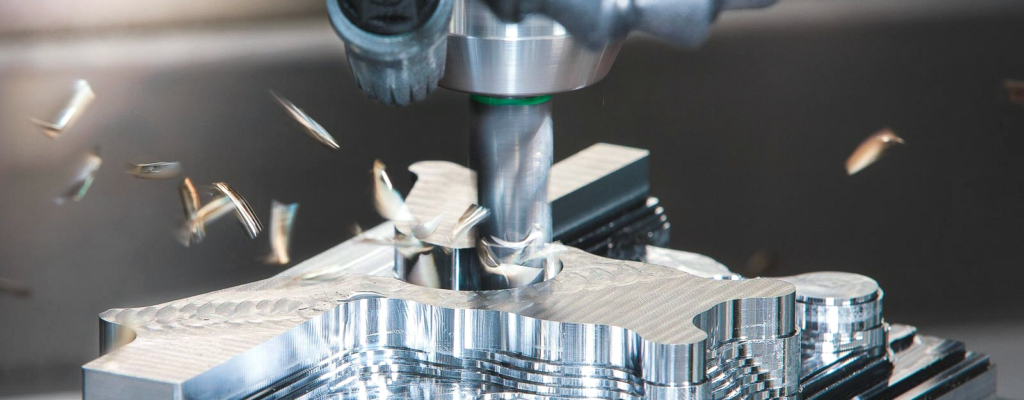
Shape and Quality
Cold Forge
Depending on the manufacturer’s requirements, some of the cold forging characteristics may turn out disadvantages; e.g. only simple shapes in high volumes can be shaped. Therefore, if the customer is searching for a specific customized component, cold forging won’t be the best alternative.
Forging cannot create parts that have acute angles (less than 90 degrees) as they are too difficult to remove from the mold, meaning sharpened points are out of the question. Also, there are other features that cannot be made by forging, such as internal threads. You would have to have a separate machine to tap the thread when the forging process is complete.
Besides, because of the grain structure that gives the material its strength, residual stress may occur.
Hot Forge
Hot forging is more flexible than cold forging since customized parts can be manufactured.
Furthermore, the hot forging manufacturing process keeps materials from strain hardening at high temperatures, which results in optimum yield strength, low hardness, and high ductility.
On the downside, less precise dimensional tolerance is possible of hot forged components compared to the cold-forged and CNC machined ones.
The cooling process should be also performed under special conditions; otherwise, there is a risk of warping.
Also, the grain structure of forged metals may vary and there is always a possibility of reactions between the atmosphere and the workpiece.
CNC Machining
CNC machining is ideal if you’re making parts that have complex or acute-angled shapes. For example, aerospace engineers making unique parts for a space shuttle or fighter jet would find it more convenient and cost-effective to use CNC machining.
Some forges actually use CNC machines to create the molds to be used in their forging press. If you have specific requirements, such as internal threads or sharpened points, and you’re not looking for mass production levels of output, then CNC is the best option for you.
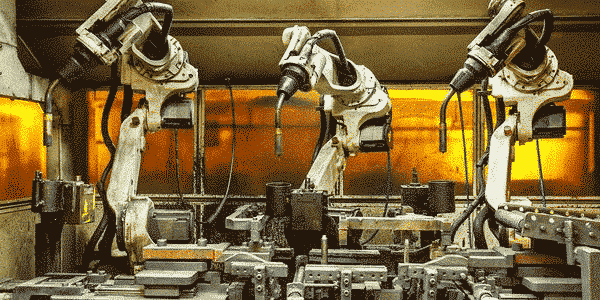
Finishing Process
Cold Forge
Manufacturers may prefer cold over hot forging process since cold forged parts require very little or no finishing work, which saves cost.
Hot Forge
The excellent surface quality of hot forging part allows a wide range of finishing work as polishing, coating or painting, tailored to customers’ specific needs.
CNC Machining
Surface finishes on a CNC machined part will typically be near perfect and appear very consistent and precise, whereas cast or forged parts will be a little rougher, usually requiring polishing or tumbling in an abrasive media to achieve a better surface finish.
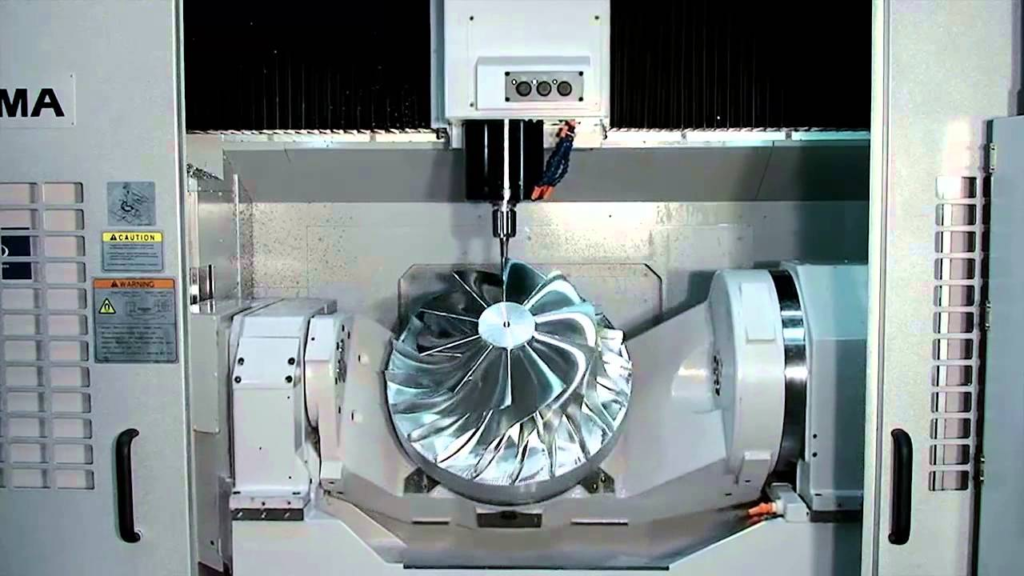