ColorJet Printing (CJP), PolyJet and HP Multi Jet Fusion are the only 3 3D printing methods that currently support full-color production. Although the visual result shares much similarity, their differing build styles separate them in terms of materials and applications. Knowing the differences will lead you to the best process choice for your project. Here are the top 4 differences between these 3 methods in terms of full-color 3D printing:
Build Style
ColorJet Printing (CJP)
ColorJet Printing (CJP) is an additive manufacturing technology which involves two major components – core and binder. The Core™ material is spread in thin layers over the build platform with a roller. After each layer is spread, color binder is selectively jetted from inkjet print heads over the core layer, which causes the core to solidify. The build platform lowers with every subsequent layer which is spread and printed, resulting in a full-color three-dimensional model.
PolyJet 3D Printing
PolyJet 3D printing is similar to inkjet printing, but instead of jetting drops of ink onto paper, PolyJet 3D Printers jet layers of curable liquid photopolymer onto a build tray.
PolyJet uses multiple print heads to deposit liquid plastic onto a clean build platform layer by layer. The material is cured as it is deposited. PolyJet can deposit material in layers as fine as 16 microns.
HP Multi Jet Fusion (MJF)
Multi Jet Fusion is an additive manufacturing method invented and developed by the company Hewlett-Packard (HP). It creates parts additively thanks to a multi-agent printing process.
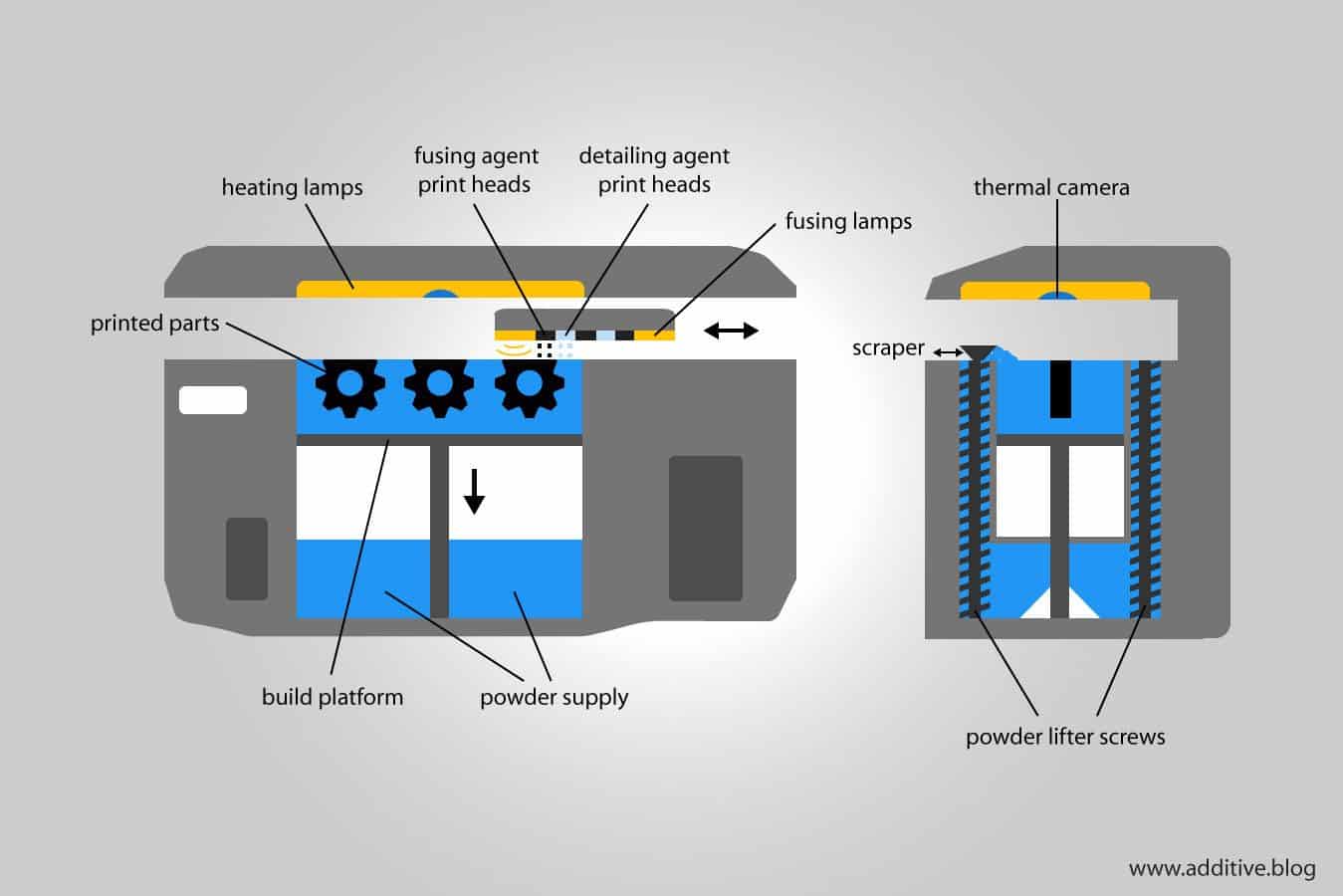
Final parts exhibit quality surface finishes, fine feature resolution, and more consistent mechanical properties when compared to processes like selective laser sintering.
Multi Jet Fusion uses an inkjet array to selectively apply fusing and detailing agents across a bed of nylon powder, which are then fused by heating elements into a solid layer. After each layer, powder is distributed on top of the bed and the process repeats until the part is complete.
Materials
ColorJet Printing (CJP): Fullcolor Sandstone
CJP prints with Composite Multicolor material (Fullcolor Sandstone), it can withstand temperatures of up to 60°C (140°F) – beyond that the object’s properties can be significantly altered. Composite Multicolor objects are also somewhat fragile (comparable to a porcelaine), so it is important to handle them with caution.
The prints have a gritty surface and are relatively porous. It is thus important to avoid direct contact with water as it could result in discoloration or running of the colors.
PolyJet: Fullcolor Resin/Photopolymer
PolyJet prints with Vero+Agilus material (PolyJet Fullcolor), it can withstand temperatures of up to 50°C (122°F) – beyond that the object’s properties can be significantly altered.
Compared with CJP fullcolor sandstone, Polyjet photopolymer is much stronger and stiffer in terms of tensile strength, flex strength and flex modulus. However, it is more similar to an acrylic than an ABS, PC, polypropylene or polyamide. This is why the Polyjet Vero is generally designated for light functional testing, patterns, prototypes and models.
With regards to water qualities, VeroWhite resin is water-resistant but not waterproof. Thus the 3D object must not rest in contact with water for extended periods of time. In terms of temperature, if the Verowhite 3D printed part is subjected to heat above 50°C (122°F), it is possible that the physical form of the object can significantly altered.
The prints have a smooth surface and are quite detailed. And please note: PolyJet is the only method that can print transparent full colored parts. Which makes it perfect for medical guidance model.
However to avoid objects in PolyJet Fullcolor to become dirtied, you can often clean them with soapy water and a cloth, letting it dry thoroughly.
HP Multi Jet Fusion (MJF): Fullcolor Nylon
MJF prints full colored parts with HP 3D High Reusability CB PA 12 material, according to HP’s public information, the full color parts are only applicable with the HP Jet Fusion 580 Color 3D Printer. The cutting edge technology allows users to produce functional parts in full color with voxel control in a fraction of the time.
Compared with CJP full-color sandstone and PolyJet Fullcolor photopolymer, MJF colorful plastic has the best mechanical strength, which is engineering grade and ideal for functional prototyping, ductile parts and visual display models.
The look of the fullcolor nylon is sort of granular and porous, but it’s smoother than CJP fullcolor sandstone.
Post-processing
ColorJet Printing (CJP): Cleaning, Gluing and Varnishing
CJP doesn’t require support material, the material powder work as supports. After printing is finished, the objects are then carefully removed by hand from the batch. The excess powder from the print is saved for a future print.
Then the excess bits of powder which can not be removed by hand are removed with pressurized air. The object is then dunked in a cyanoacrylate bath, which further solidifies the object and brings out the colors a bit more.
Finally your object is given an anti-UV varnish to protect it from extensive light exposure. If you choose other varnishing options for your object, they would be applied at this stage.
PolyJet: Support Removal and Finishing
PolyJet parts are built fully cured. PolyJet supports are created out of a separate material specially formulated to release from the final part with water blasting and some hand labor.
After the photopolymerization is completed, the batch is placed under a pressurized water jet. This allows any excess liquid or supports to be removed without human interaction.
If a gloss effect was chosen for the object, polishing and UV-coating will be applied after the 3D printed object is washed.
HP Multi Jet Fusion (MJF): Cleaning, Brushing and Sandblasting
The HP process is faster than SLS technology but it still needs to cool. When the parts are 3D printed, the building box is placed into the post-processing station that cools the parts and prepares them for cleaning. The object is extracted from the powder which is sieved and partly recycled for another 3D printing batch.
The object is then brushed, which removes a large portion of the polyamide powder, and vacuum-cleaned, which removes the fine polyamide powder that the brush may have missed.
Conclusion
The above 3 methods are all excellent choices for master patterns, prototypes and models. The following chart will give you a better understanding of how to select the best material for your project:
Add a Comment
You must be logged in to post a comment