Selective laser melting (SLM) is the premier metal 3D printing technology revolutionizing the additive manufacture of metal parts, but how does it work, and which 3D printers do it best?
Most metal 3D printers use selective laser melting technology, which involves a laser that melts powdered metal. In fact, this method accounts for more than 80% of the metal 3D printer market and dozens of manufacturers worldwide offer machines in a wide range of sizes with varying features.
The dominance of SLM tech may not be apparent at first since there’s different terminology in the industry to refer to the same technology. Aside from SLM, there’s direct metal laser sintering (DMLS), direct metal laser melting (DMLM), laser metal fusion (LMF), laser cusing, and laser powder bed fusion (LPBF), among others. This variety of terms begs the question: What’s the difference between them?
You may be surprised to learn that there is no difference.
What is SLM?
To get the definitive word on this technology, All3DP turned to one of the inventors of the process, Wilhelm Meiners.
Just over 20 years ago, Meiners and his colleagues Kurt Wissenbach and Andres Gasser developed and patented the technology while working at the Fraunhofer Institute in Germany.
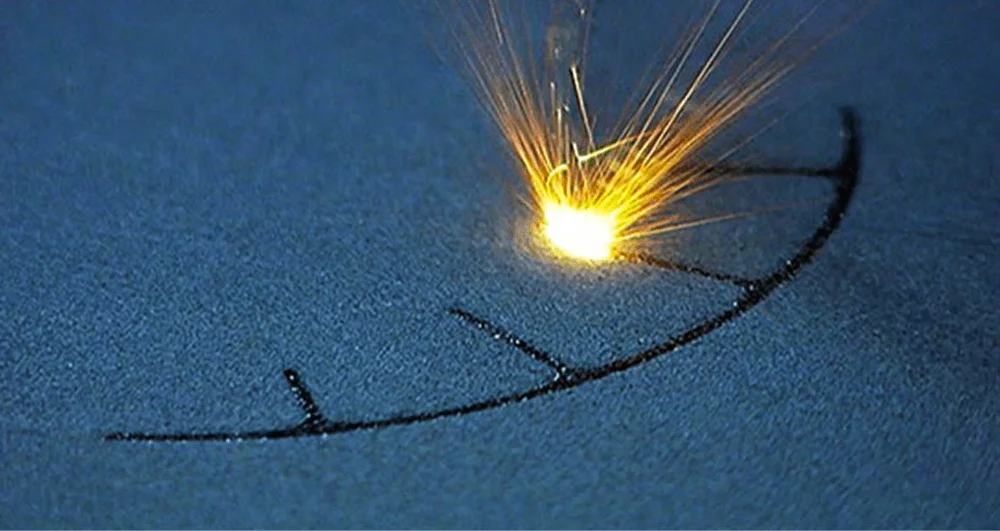
According to Meiners, the technology’s official name is laser powder bed fusion or LPBF.
“The different names for the LPBF process are due to historical causes,” he says. “In the early years, every machine supplier created its own name for the same process and kept it until today.” All of these other terms are simply brand names for the standardized technology called laser powder bed fusion.
Indeed, German 3D printer manufacturer EOS coined the term “direct metal laser sintering” and still uses it today. It’s a bit of a misnomer since the metal powder is melted not sintered, but that could have been lost in translation. SLM, the more popular term, is actually a trademark held by the printer manufacturer SLM Solutions. Concept Laser, on the other hand, called their process laser cusing, but once GE Additive acquired the company in 2016, they changed the name to direct metal laser melting (DMLM). Printer manufacturer Trumpf likes to use the term laser metal fusion while 3D Systems uses direct metal printing.
Although we used the most popular term, selective laser melting, in the title of this article, for the rest, we’re going to go with the official name used by Meiners and the standards organization ASTM: laser powder bed fusion.
Despite the confusing terminology, LPBF is one of the most exciting 3D printing technologies available today. It’s used across industries for rapid prototyping, specialty high-performance parts, and mass production with a wide range of metals. Let’s take a look!
How Does LPBF Work?
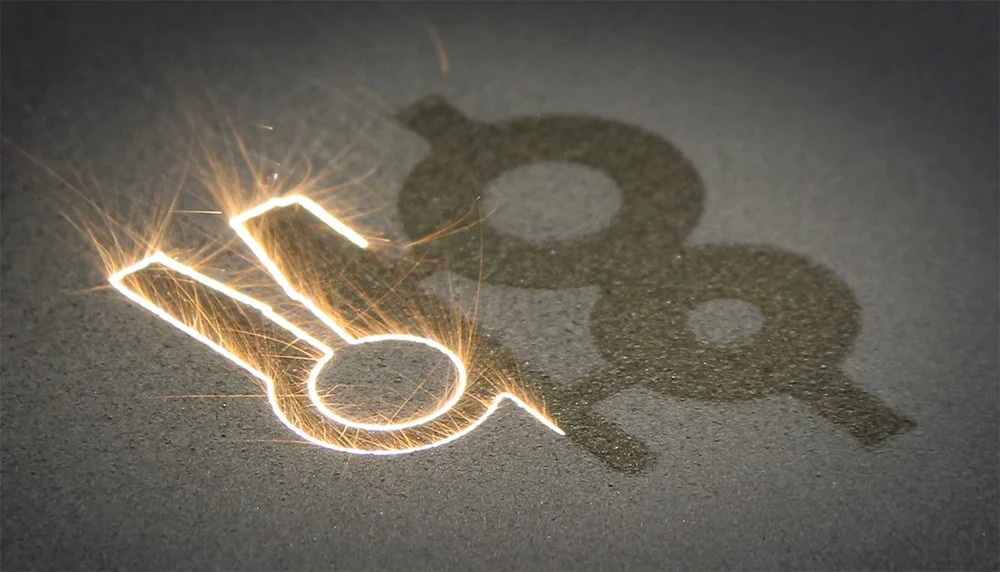
LPBF 3D printers use high-powered lasers to selectively melt a metal powder. The melted parts fuse together layer-by-layer on a molecular basis until the homogenous model is complete.
Printer operators can use “pure” metal materials, although alloys also see regular use. There are dozens of metals available for the LPBF process, but some of the most common materials include:
- Aluminum
- Cobalt Chrome
- Copper
- Nickel (Inconel)
- Stainless and Tool Steels
- Titanium
- Precious Metals
In theory, LPBF — like the related and similarly functioning selective laser sintering (SLS) for plastics — is a support-less AM technology. The packed powder on the printing bed provides support to the model during the printing process.
However, due to high thermal gradients between the molten part and surrounding powder, stresses can arise causing warpage and distortion. Support structures are therefore often needed in order to dissipate heat from critical areas and fix the part securely onto the build plate. A general rule of thumb is that overhangs or hollow structures angled between 0 and 45 degrees should be supported.
An LPBF 3D printer houses metal feedstock powder. The printer pushes powder into the chamber where a coater blade (like a windshield wiper) or roller spreads it into a thin layer across the substrate or build plate.
Next, a high-powered laser fuses a two-dimensional slice of the part by selectively melting the powdered material. The build plate then lowers by the height of one small layer, and the coater spreads another layer of fresh powder across the surface. The printer repeats these steps until you have the finished part.
Some printers have bidirectional coaters, which can push powder onto the bed moving both ways, speeding up the coating process by up to 40%. Another way LPBF printer manufacturers make printing faster is by employing more powerful or several lasers.
A small, compact LPBF printer might have a single 30-watt laser. As the machines grow larger, they can start incorporating stronger lasers or multiple lasers in one array. For example, the AddUp FormUp 350 features four 500-watt lasers, while the SLM Solutions NXG XII 600 employs a total of 12 lasers, each with 1000 watts of power.
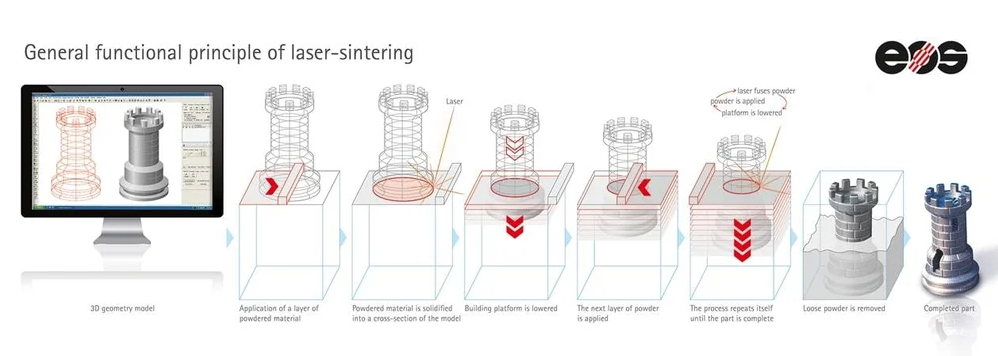
Increasing the power or number of lasers means the printer can melt the metal powder more effectively. It directly results in faster build rates and increased throughput, and typically a higher price tag. As an example, SLM Solutions claims the NXG XII 600 can provide 20 times faster build rates than single-laser systems, up to 1,000 cm3/h.
Depending on your application, when considering in a LPBF 3D printer you’ll look at the level of laser power, the laser beam diameter, the scan speed, the possible layer thickness (from 20 to 120 μm), the scan strategy, the part cooling strategy, and other features that set different brands, and different models within brands, apart.
The LPBF printing process happens in a controlled atmosphere inside the machine, which means inert gas (nitrogen or argon) fills the build chamber.
Once the part is built, it can be removed from the machine after cooling. Large parts can take many hours to cool before handling is possible. Metal powder that is not fused is collected afterwards and reused for further LPBF projects. Printed parts are initially attached to the build plate, from which they are usually separated by cutting or machining, or by wire erosion.
If the part needed supports, you must next remove them as well. As LPBF printers don’t use separate support materials, this can be a difficult and time-consuming process.
The surface finish of the final melted part is rough and, depending on your requirements, it may need post-processing to achieve a smooth and shiny result. It is also relatively common to further machine parts to achieve tighter tolerances and finish fine features, surfaces, and holes.
LPBF vs. Traditional Manufacturing
LPBF, like every manufacturing technology, has its strong and weak points. The pros and cons of producing a model via LPBF include:
ADVANTAGES
- Large range of available metals
- Ability to realize complex shapes or internal structures, possibly without supports
- Reduced total lead times, due to no need for tooling
- Part consolidation, allowing operators to create previously multi-component parts as one print
- Reduced waste, due to additive manufacturing and powder reclamation
- Ability to reduce standing inventory due to fast on-demand production
- Potential for mass-customization of parts
DRAWBACKS
- No low-bar for entry. All LPBF 3D printers cost in the tens of thousands of dollars
- Cost per part can be a lot higher compared to traditional manufacturing methods
- Parts require post-processing, such as de-powdering, support removal, and surface grinding
- Size limited currently to one meter
- Lasers require a lot of energy
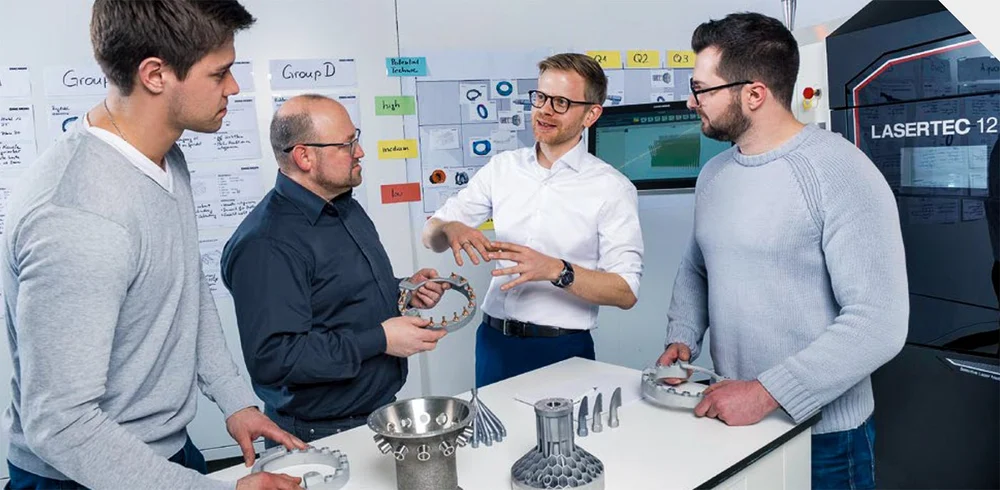
LPBF vs. Traditional Manufacturing
One of the most common questions when it comes to metal 3D printing is how part strength and durability of 3D printed parts using LPBF compare to traditional metal manufacturing methods.
Nick Estock, product manager at AddUp, the French metal 3D printer maker, explains to All3DP that it is possible for LPBF to produce parts with mechanical properties similar to traditional manufacturing. However, he adds, there are some caveats.
“Traditional manufacturing is subtractive and starts with a base material of known mechanical properties through very controlled and mature processes. In any additive manufacturing process, including LPBF, the material is being created simultaneously with the part. The process is fundamentally different and therefore not equivalent,” says Estock.
Donald Godfrey, global director of business development for aviation and defense at SLM Solutions, agrees. He further explains that the SLM process creates parts that have smaller microstructures than cast metal components. This gives them higher tensile properties, but cast parts are currently still stronger.
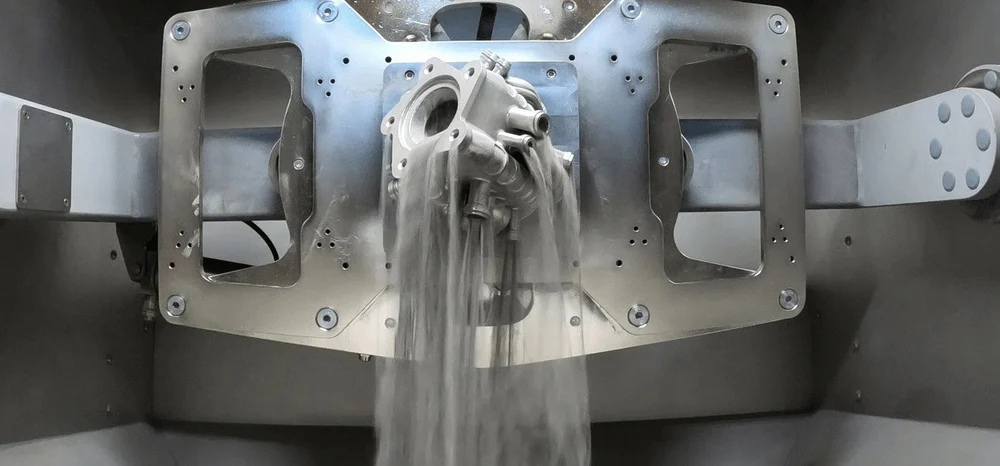
“Typically, LPBF technology is used to replace cast components. In unique cases, printed components can replace forgings,” he adds.
When we asked Meiners if the resulting prints from the LPBF process are equivalent to traditional manufacturing processes, he also said, it depends.
“The properties of LPBF parts can obtain or even exceed those of traditional manufactured parts, but this depends on several conditions like the metal material (steel, aluminum, titanium, etc.) the post process (heat treatment, hot isostatic pressing, etc.), the traditional manufacturing process you compare it with (casting, forging, etc.), and the specific part property (strength at static load, high cycle fatigue, creep, etc.).”
In the end, there’s no general answer, Meiners says. “In many cases, LPBF parts obtain the same properties, but not as a generic standard.”
Let’s take a look at some real-world examples of LPBF 3D printed parts in action.
WHO’S USING LPBF TODAY?
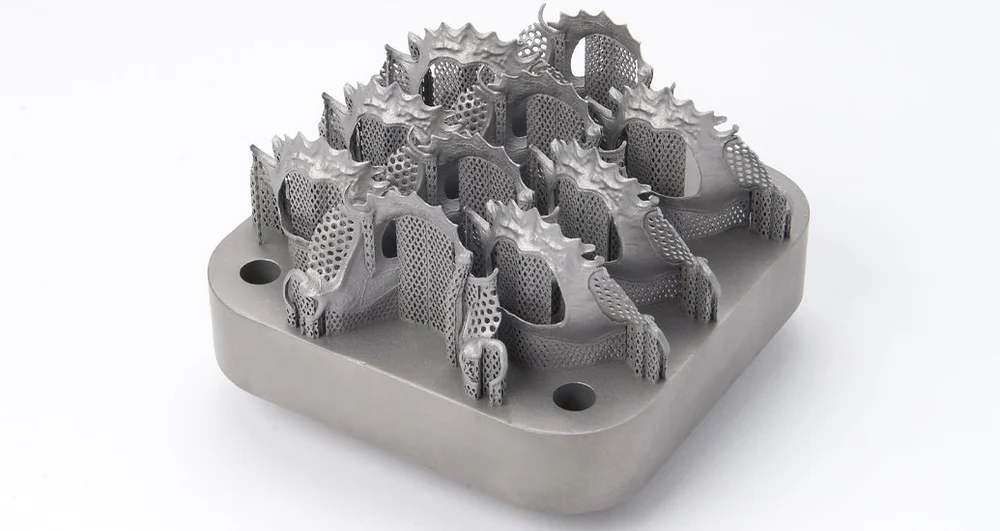
LPBF is used in nearly every industry today where traditional metal manufacturing is employed including aerospace, automotive, medical, energy, and machining.
What connects all these industries is their need to produce more efficient and better-performing metal parts, faster, and at a lower cost. Although LPBF is also widely used for faster and cheaper production of spare and replacement parts, where the technology shines is in producing complex shapes and innovative product design enhancements that are not possible with any other metal manufacturing methods. With LPBF, multi-piece components can be 3D printed on one part, products can have internal lattice structures to make them weigh less, and complex internal channels that would be impossible to machine.
Metal 3D printing, in general, also eliminates the need to maintaining standing inventories and ship parts from long distances, plus it’s more sustainable in that it uses and wastes less raw material.
Let’s take a look as some specific, real-world applications of LPBF in action.
Aerospace: Landing Gear
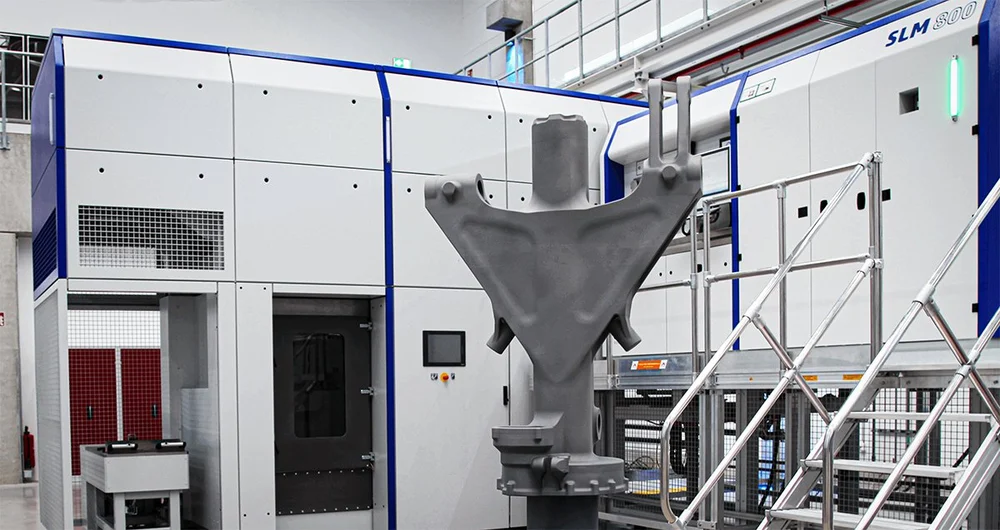
Safran Landing Systems and SLM Solutions worked together to improve a previously forged nose landing gear part for private jets.
At 455 x 295 x 805 mm, the landing gear component is the world’s first LPBF printed part of its size, says SLM Solutions. Since the component is a part of the system that transfers loads from the wheel to plane’s structure, it was manufactured out of titanium. The choice of material gives the part strong mechanical properties while being corrosion-resistant without coatings.
It was printed using the quad-laser SLM 800 machine. Not only is the LPBF printed component 15% lighter than a traditionally forged component, the technology also slashed the turnaround time.
“Additive manufacturing contributes to save time in the qualification and certification phases by rapidly providing the parts for testing. We were able to produce the main fitting in a few days vs. a few months with the forging process,” says Gerhard Bierleutgeb, EVIP of Global Services and Solutions at SLM Solutions.
Automotive: Tools
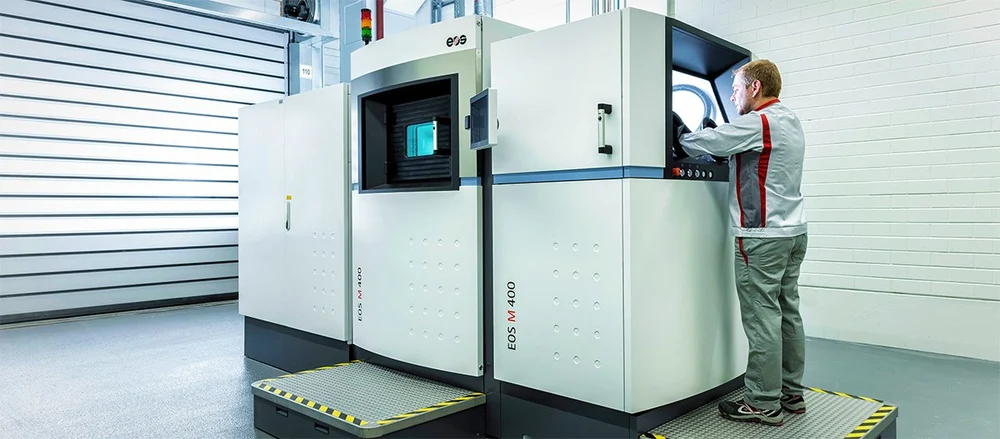
LPBF can replace traditional manufacturing methods in many instances, but they can also work together. Traditional production methods are no longer used to create tool segments for hot forming car parts, which is why Audi has replaced them entirely with 3D printed alternatives.
“Whenever conventional manufacturing methods reach their limit, we use additive manufacturing — which lets us meet quality standards and comply with production times,” said Audi Metal 3D Printing Center’s Project Manager, Matthias Herker.
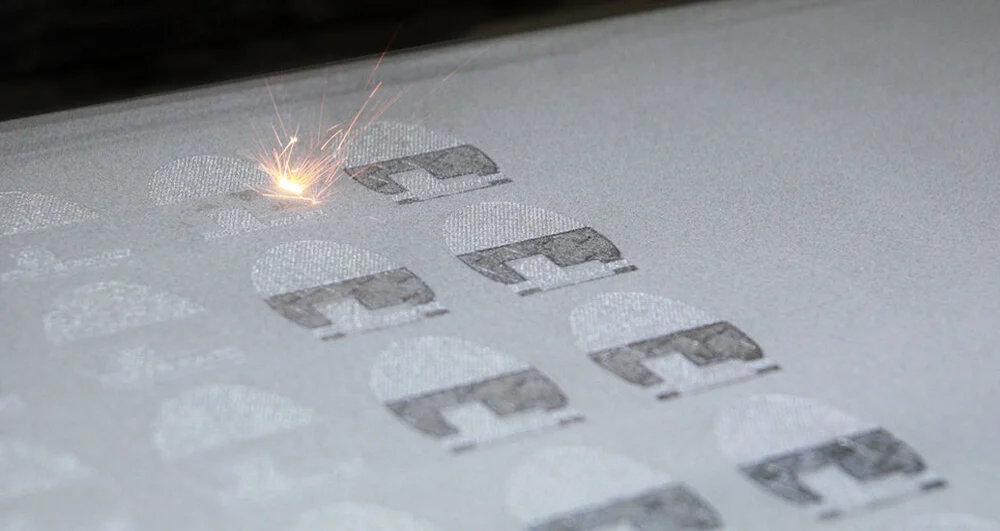
Audi uses the EOS M 400 printer to manufacture hot forming segments and high-pressure die casting tool inserts. The individual segments can be up to 400 mm in length and weigh up to 120 kg.
LPBF 3D printing allows Audi to create topology-optimized, highly complex cooling channels, fine-tuned to the needs of specific components. As a result, the premium car manufacturer has been able to shorten cycle times and get more even cooling, which improves part quality.
Medical: Titanium Implants
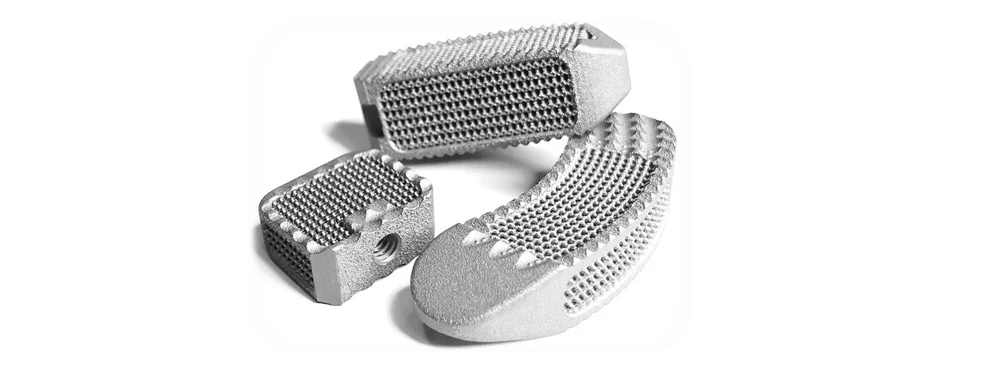
Lumbar interbody fusion devices — or spinal cages — are widely used to treat patients suffering from back issues, such as degenerative disc disease.
GE Additive produces an additively manufactured option made from titanium powder using LPBF printing. These new spinal cages offer several benefits over machined versions, the company says.
Due to additive manufacturing’s greater design freedom, the spinal cages can be made lighter with larger windows and lattice structures. This not only reduces manufacturing costs, but makes the cages more effective as doctors can implant additional bone graft into the cage. It’s also possible to create customized porous structures that mimic human bone, which can further promote bone formation.
The new cages don’t require any coatings, which completely eliminates the risk of delamination. They’re also made of titanium, which is biocompatible and reduces cage migration and bone degradation.
Energy: Steam Distribution Block
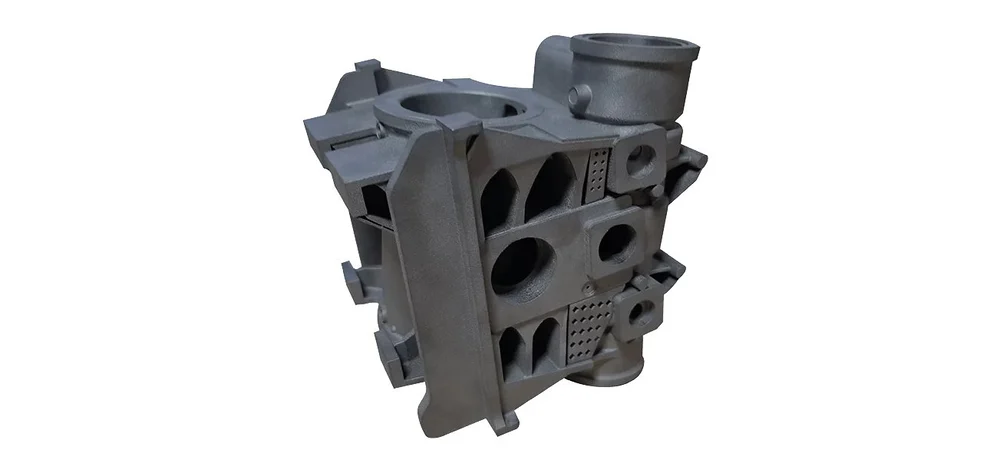
Orano, a French multinational nuclear fuel cycle company, struggled with long lead times and high costs of obsolete spare parts. In early 2021, the company partnered with AddUp to evaluate LPBF’s technical and economic feasibility for their operation.
Using the FormUp 350 printer, Orano and AddUp created several copies of a 3D printed material transfer bridge and a steam distribution block, which has particularly long lead times when manufactured through traditional methods. The parts had identical design and mechanical characteristics to the originals.
Thanks to the use of fine stainless steel powder, the 3D printed parts had a high geometric accuracy and surface finish, particularly in their internal channels. Additionally, at the cost of three machined parts, Orano was able to print 16 additively manufactured components.
“The result is unexpected: the same design with complex geometries, the same mechanical characteristics, and above all, a 50% reduction in production costs compared to machining. Thanks to metal additive manufacturing, Orano now has an additional, agile, reliable, and economical supply chain for spare parts,” says Ana-Paula Serond, innovation manager at Orano.
GET YOUR METAL PARTS MADE: CONTRACT MANUFACTURERS
If you’re not ready to purchase your own LPBF machine, there are services to make your parts for you. Generally, there are two different kinds: 3D printing on-demand manufacturers and printer manufacturers.
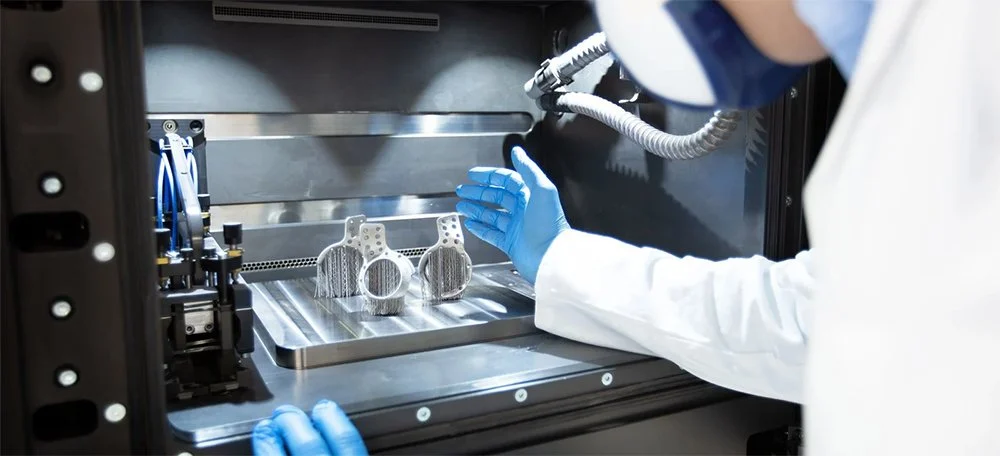
Top Manufacturer Metal 3D Printing Services
Metal printer manufacturers, including 3D Systems, GE Additive, and EOS, offer metal part-on-demand services. These are ideal because working directly with a printer manufacturer also gives you a chance to demo their machines’ capabilities in case you want to buy one. If you’re considering a metal 3D printer purchase for your operation, it might be worth it to order some on-demand parts from a manufacturer to evaluate the machine – especially if you already have a specific printer in mind.
The printer’s manufacturer will know the ins and outs and limits of their technology down to the smallest details. This can make it easier for them to assist you with the choice of technology, materials, and parts design.
It could also be that you already own a printer from one of these companies, but your machine is just too busy to deal with a suddenly increased workflow. Ordering on-demand printing services from your trusted manufacturer is a good option for getting more parts done, and you’ll know exactly what kind of part quality you’ll get.
For all these reasons, consider these best on-demand metal printing services offered by 3D printer manufacturers.
3D SYSTEMS / QUICKPARTS
3D Systems, based in South Carolina, has an on-demand manufacturing service that’s so popular they just sold it to a private equity firm. The new company will operate as QuickParts and can produce parts in steel, aluminum, titanium, cobalt chrome, and nickel alloy. They offer printing and consultation service globally, and can also provide additional services like CNC machining and casting patterns.
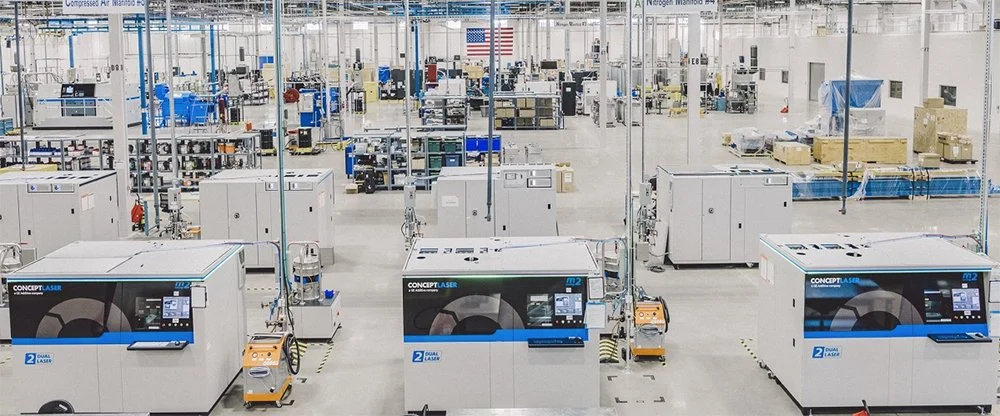
GE ADDITIVE
GE Additive Print Services, part of the General Electric group, makes use of their EBM and DMLM metal 3D printing technologies, most of which have been obtained through mergers and acquisitions. They also provide their own materials, as well as their consultancy and training services. They focus on medical, automotive, military, dental, and aerospace industries. Although their services aren’t available online, they do offer US customers a full range of printing services via their Print Services Center in Pittsburg. The company also provides limited services in Europe through their Lean Manufacturing facilities.
EOS
Although Germany’s EOS doesn’t directly 3D print your metal parts, they do have a handy list of additive manufacturers with EOS machines who do contract manufacturing all over the world, including several in Africa, an underserved area.
ADDUP
AddUp, metal 3D printer OEM and parts producer, works with customers in the medical, automotive, energy, aerospace, tooling and defense industries to print production parts. They offer part design and optimization for AM, consulting services and training, proof-of-concept production, serial part production and post-processing, plus ISO 9001 and ISO 14001 certified. With production workshops in Europe, US, and Asia, AddUp just opened a new 20,000-square-foot facility in Cincinnati, Ohio. The US-based facility is ITAR compliant.
TOP LPBF 3D PRINTERS
Laser powder bed fusion 3D printers come in a range of sizes and powers. Here we feature the “starter” solutions from the top manufacturers, but many companies also offer larger and more feature-rich machines tailored to address specific manufacturing challenges and industry segments.
When selecting a LPBF 3D printer, consider:
- Scalability. If you outgrow the entry-level machine, is there another level to upgrade to?
- Build Speed: How many cubic centimeters per hour can the machine produce?
- Laser Scan Speed: This is not the only indicator in part build speed, but it contributes.
- Layer Height & Resolution: How detailed can the final parts be?
- Gas & Power Consumption: Some machines consume more than others. How does this effect final costs?
- Material Consumption: Machines with good powder feeding and sieving technology can waste less powder.
- Open or Proprietary Materials: If you have to use the printer manufacturer’s materials, it could affect your manufacturing flexibility and costs.
One Click Metal MPrint+
- Printer One Click Metal MPrint+
- Build Volume 150 x 150 x 150 mm
- Laser Type 200W Fiber Laser
- Materials Tool Steel, Stainless Steel
- Approx. Price $55,000 – $60,000
One Click Metal is a spin-off from well-known printer maker Trumpf. The company says it produces an affordable, easy-to-use metal 3D printing system perfect for companies new to LPBF. One Click Metal MPrint+ works with cartridges eliminating the mess of metal powder, and it’s meant to be deployable with fewer requirements in terms accessories and space.
It has a build volume of 150 x 150 x 150 and comes with the MPrep software.
The MPrint+ is meant to be paired with the MPure, which is the company’s 3-in-1 unpacking station that depowders the component, screens the powder, and provides recycled powder for reuse. The cartridge system of both the printer and the depowder station ensures easy and safe powder handling, so that you have limited contact with the powder. With the side connection for a vacuum cleaner you can efficiently remove excess powder from the unpacking chamber.
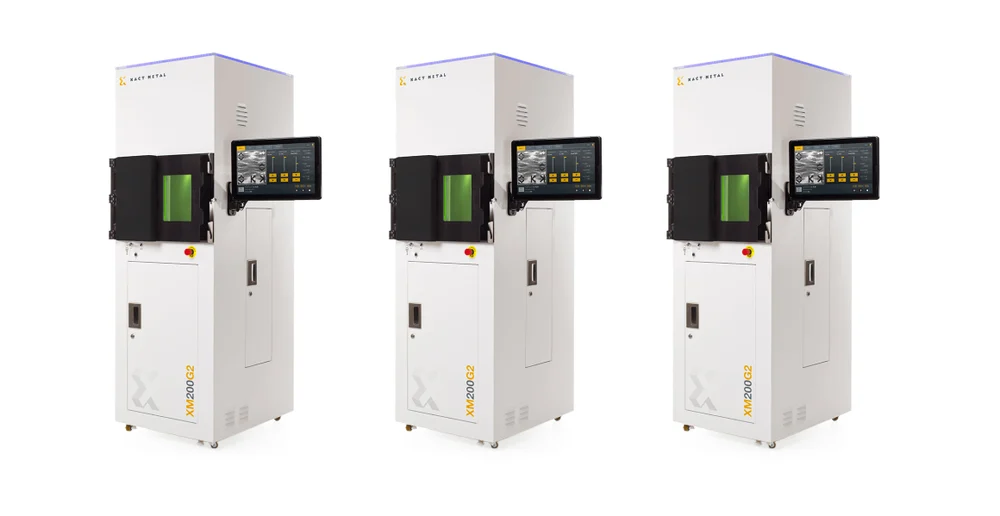
- Printer Xact Metal XM200G
- Build Volume 150 x 150 x 150 mm
- Laser Type Single or Dual 100W, 200W, or 400W Yb Fiber Laser
- Materials Alumiums, Stainless Steels, Cobalt Chrome, Nickel, Hastelloy, Copper, Bronze, Titaniums,
- Approx. Price $90,000 – $100,000
Xact Metal wants to bring 3D printing to a wider audience with its flexible XM200G series available in a choice or single and dual fiber laser powers.
The XM200G is based on Xact Metal’s XM200C metal 3D printer. It integrates a high-performance galvanometer system to move the laser beam over the powder bed. This architecture allows for faster printing times, the company says, and the ability to support multiple lasers.
The XM200G tailors to customers who are starting their entry into metal 3D printing in various applications, including product development, tooling manufacturing, metal powder-bed research and workforce development. It offers the option of using two lasers at one time with either a 100% overlapping work area using a 100-µm spot size or a 66% overlapping work area using a 50-µm spot size. This multi-laser system further increases build print speeds.
The company’s XM300C offers a larger build volume (254 x 330 x 330 mm) and a choice of two or four independent multi-lasers. It is equipped with two feed chambers, which lowers build time and increases productivity, according to the company.
3D Systems DMP Flex 100
- Printer 3D Systems DMP Flex 100
- Build Volume 100 x 100 x 90 mm
- Laser Type 100W Laser
- Materials Stainless Steels 316L and 17-4PH, Cobalt Chrome
- Approx. Price $250,000
3D System’s entry-level DMP Flex 100 metal 3D printer offers a build volume of 100 x 100 x 90 mm and the ability to print parts with overhangs down to 20 degrees without supports. Surface features as fine as 5 microns should mean a minimal need for post-processing. 3D Systems calls its technology Direct Metal Printing, where each layer is melted on to the previous one creating a strong and dense part (up to 99.9%).
The system’s 100-watt fiber laser, while lower power than those of the larger metal 3D printing solutions in 3D System’s line up, is powerful enough to handle a broad selection of the company’s metal powder library, including a variety of titanium grades.
Tailored to niche uses that demand fine detail, the DMP Flex 100 makes use of dedicated gas lines to achieve the vacuum necessary to print 3D System’s additive manufacturing-optimized powders. As such, it requires the necessary building infrastructure to facilitate this.
If you’re ready to move up from entry-level machines, 3D Systems offers five other, larger production units plus a networked factory solution.
Trumpf TruPrint 1000
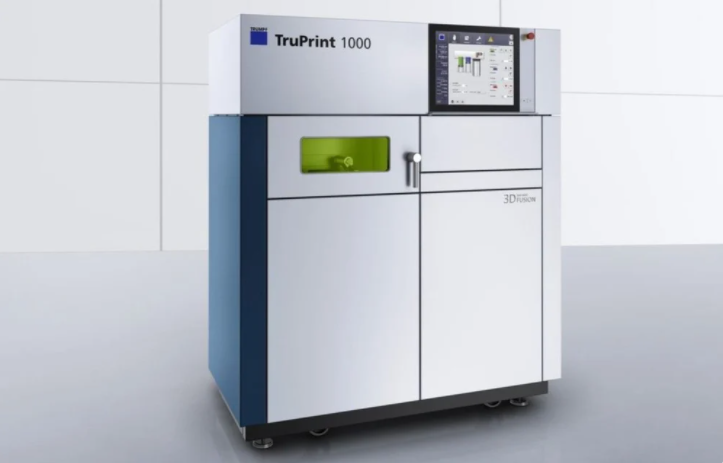
- Printer Trumpf TruPrint 1000
- Build Volume 100 × 100 × 100 mm
- Laser Type 200W Fiber Laser
- Materials Stainless Steels, Tool Steels, Aluminum, Nickel Alloys, Cobalt Chrome, Copper, Titanium, Precious Metals
- Approx. Price $180,000
Trumpf, based in Ditzingen, Germany, offers the TruPrint 1000 metal 3D printer for the production of small industrial parts. The compact machine with quick installation brings to the table high productivity and great detail, with a minimum layer thickness of 10 microns. Trumpf calls its version of SLM, Laser Metal Fusion.
The printer’s two 200-watt fiber lasers scan the build area simultaneously, which the firm claims can increase productivity by up to 80% when compared to similar machines. A powder bed monitoring system analyzes each layer for maximum part quality. A tilting recoated makes the powder application process faster, which further increases production speed and cuts part costs.
As a unique note, TruPrint 1000 can process amorphous metals. These materials make it possible to produce parts with high elasticity and corrosion-resistance, while simultaneously cutting down on wall thicknesses. This reduces production times and final part weight.
In March 2021, Trumpf unveiled the new TruPrint 3000 3D printing system that uses powder-bed-based laser melting to produce metal parts with a diameter of up to 300 millimeters and a height of up to 400 millimeters. The machine can handle all weldable materials including steels, nickel-based alloys, titanium and aluminum.
Trumpf has seven other metal 3D printers in its portfolio. The TruPrint 1000 Green Edition features a green laser that allows it to 3D print highly reflective materials, like copper and its alloys. Other machines in the company’s catalog scale power and production capacity up to higher-volume applications. Trumpf’s laser metal deposition machines combine additive manufacturing with two and three-dimensional cutting and welding.
EOS M100
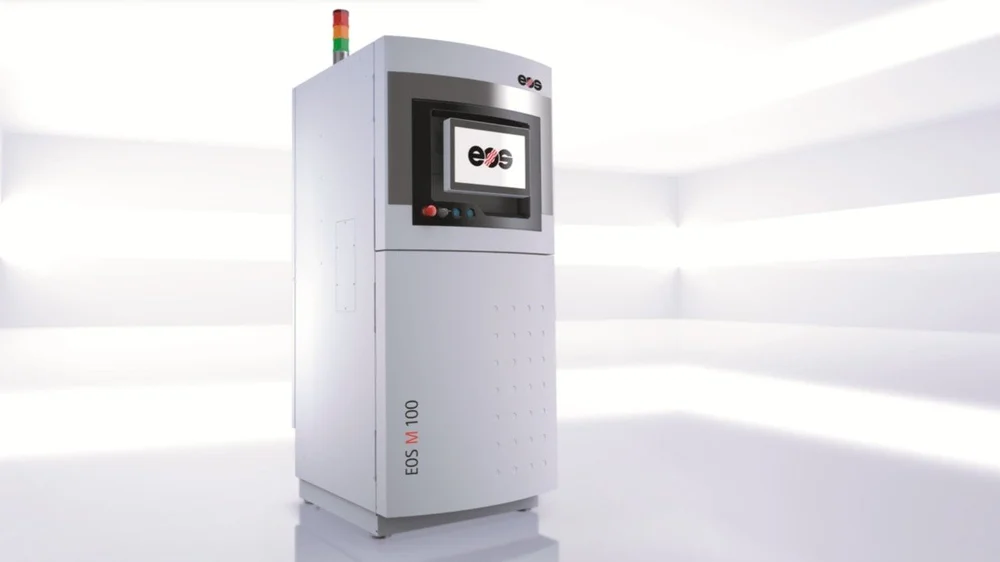
- Printer EOS M100
- Build Volume 100 x 100 x 95 mm
- Laser Type 200W Yb Fiber Laser
- Materials Cobalt Chrome SP2, Stainless Steel 316L, Titanium Ti64, Tungsten W1, Gold, Silver, Bronze
- Approx. Price $350,000
The M100 metal 3D printer is EOS’s entry-level system for metal printing. Featuring LPBF technology the company called direct metal laser sintering (DMLS), the M100 machine is equipped with a 200-watt fiber laser to melt and fuse fine metal powders. The small laser spot enables fine resolution, making it ideal for geometrically complex metal parts.
The M100 is optimized to reduce post-processing and cleaning time, the company says, which in turn allows for parts to be produced quickly. It also has a modular inner design and powder supply bin, which should make operation and maintenance easy. EOS is pushing the machine, especially toward the medical field, to which the M100 is particularly suited with EOS’s certified medical-safe metal materials. The company highlights the printer’s suitability for producing dental bridges and crowns.
The manufacturer is constantly releasing new metal powders, with the latest nickel-chromium NickelAlloy IN939 material launched in February 2021. Do note that the M100 is compatible with a limited number of EOS materials, and may not be able to process some of the more high-end powders.
If you’re in the market for a metal 3D printer for production capacity, EOS has you covered. The German manufacturer offers industrial 3D printing systems that can be flexibly integrated into existing production environments with a range of different build space sizes, laser power ratings, and scalability.
SLM Solutions SLM 125
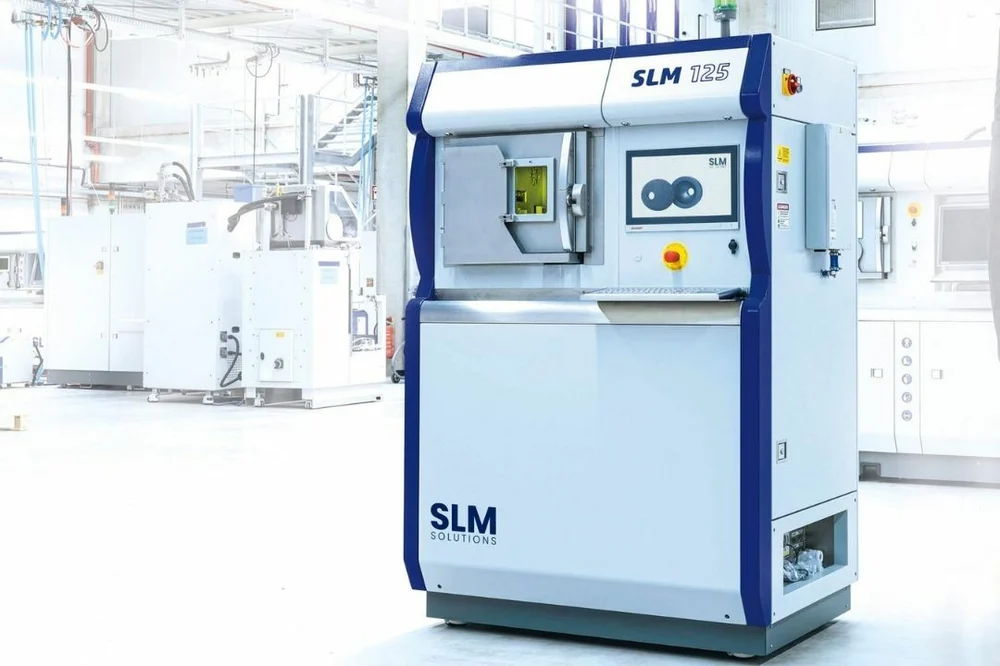
- Printer SLM Solutions SLM 125
- Build Volume 125 x 125 x 125 mm
- Laser Type 400W IPG Fiber Laser
- Materials Stainless Steel, Cobalt Chrome, Nickel Alloys, Aluminum, Titanium
Germany-based SLM Solutions’ SLM 125 is a 400-watt fiber laser 3D printers, which more power than the lasers of other similarly sized machines, the manufacturer claims, which cuts powder consumption by up to 80%. SLM markets the printer toward research work and low-volume manufacturing.
The SLM 125 can process both reactive and non-reactive metal powders, and its reduced number of powder-transporting components makes swapping materials quick and easy. Laser Power Monitoring and Layer Control systems constantly check both laser output and layer consistency for high accuracy, which helps catch any irregularities. The 125 x 125 x 125 mm print envelope is sufficient for one-off parts and prototypes, especially with the wide variety of materials including stainless steel, aluminum, and titanium. Research institutes and parts producers looking for power in a small package shouldn’t dismiss the SLM 125.
A nice feature in SLM Solutions’ technology is the ability to directly scale the production process with the company’s expansive catalog of other, larger printers. The firm has a machine for pretty much every production level, with the latest model addition being the generously sized industry-level NXG XII 600 launched in late 2020. Its 12 1,000-watt lasers and a 600 x 600 x 600 mm build volume provide not only size but speed – the company claims this is the fastest SLM 3D metal printer on the market.
E-Plus 3D EP-M150
- Printer E-Plus 3D EP-M150
- Build Volume 150 x 150 x 120 mm
- Laser Type Single or Dual, 200W or 500W Fiber Laser
- Materials Nickel Alloy, Titanium Alloy, Cobalt Chrome, Aluminum Alloy, Copper Alloy
- Approx. Price $125,000
This Chinese global 3D printer manufacturer has several LPBF machines, as well as SLS and resin-based technologies. Eplus 3D‘s starter machine is the EP-M150 and the company says is affordable and consistent. The machine has a relatively compact design and as the company’s entry level machine it boasts a “one-click printing” function for ease of use. It’s also easy to maintain with the 2-minute replacement time for the filter element, residual material tank substrate, and recoater.
Eplus3D metal printers are scaleable and graduating to the company’s larger , multi-laser machines for additive production is easy, the company says. The machines boast a large menus of metal material compatibility, including aluminum alloy, titanium alloys, cobalt chrome, nickel based alloys, stainless steel, tool steels, and copper.
GE Additive Concept Laser Mlab R
- Printer GE Additive Concept Laser Mlab R
- Build Volume 90 x 90 x 80 mm
- Laser Type 100W Fiber Laser
- Materials Stainless Steels (316L and 17-4PH), Aluminum, Titaniums, Bronze, Silver, Gold, Yellow Gold, Rose Platinum
The Concept Laser Mlab family of metal 3D printer systems from GE Additive offers a versatile solution for ease of use and safe handling of a broad range of materials with small footprint. The modular machine offers different build envelopes in one machine and allows for quick and easy change between different materials.
Plus, all process steps take place under inert gas, shielded from external influences to further promote safety
The Mlab R is capable of building in both reactive and non-reactive materials and produces fully dense parts. The physical separation of the process chamber and handling station offers the possibility of using the handling station for multiple machines. The Mlab R now expands the previous range of materials to include titanium and titanium alloys.
The next level up is the Mlab 200R, which boasts a user-oriented design, with a larger build envelope, a higher laser power of 200 watts and a space-efficient footprint.
Of course, Concept Laser machines get much, much larger and more powerful for industrial applications. The M2 Series 5 features two 1,000-watt lasers, the M Line is aimed at serial production with a build volume up to 500 x 500 x 400 mm, and the X Line 2000R is used for producing large-scale components in the aerospace and automotive industries.
Renishaw RenAM 500Q
- Printer Renishaw RenAM 500Q
- Build Volume 250 x 250 x 350 mm
- Laser Type 500W Yb Fiber Laser
- Materials Titaniums, Aluminiums, Cobalt Chrome, Stainless Steel 316L, Nickel Alloys
Placing emphasis on productivity, Renishaw’s RenAM 500Q system builds on the company’s established range of metal printers and amps throughput with an array of four 500-watt lasers, each capable of hitting the entirety of the build volume. This allows the RenAM 500Q to accomplish full layer sinters quicker than single-laser systems, increasing output and, consequently, reducing cost per part.
A number of inbuilt automation systems – such as sieving and powder recirculation – for material and atmosphere management complement the printer, ensuring operator safety and reducing the time required to operate and maintain the machine. An intelligent gas flow system reduces both argon consumption and emissions.
The RenAM 500Q features a typical build volume of 245 x 245 x 335 mm (substrate dependent) and can output some 150 cm3 per hour, depending on the geometries being printed and other material variables.
AddUp FormUp 350
- Printer AddUp FormUp 350
- Build Volume 350 x 350 x 350 mm
- Laser Type up to 4 x 500W fiber lasers
- Materials Aluminum, Copper, Steels, Nickel-based Alloys, Titanium
Launched in 2021, the FormUp 350 PBF machine from AddUp is modular and scalable to provide productivity while boasting user safety features. Available in four configurations with more than 25 options to be integrated at any time, the FormUp 350 has up to four 500W lasers, a bidirectional coating system with fast powder spreading and more than 160 print parameters, making the system an open platform for any application.
The FormUp 350 lets you to use extremely fine powders (5-25μm), something often overlooked among laser powder bed fusion systems. This, coupled with a roller recoating system, enables support-free production of cantilevered parts down to 10 degrees. The printer also enables surface finishes of sub 10 μm arithmetic roughness (Ra).
The FormUp 350 also offers an autonomous powder module for powder management that ensured a constant supply of powder, without interrupting production, regardless of the quantities to be produced.
Kurtz Ersa Alpha 140
- Printer Kurtz Ersa Alpha 140
- Build Volume 140 x 140 x 200 mm
- Laser Type 140W Fiber Coupled Diode Laser
- Materials Stainless Steels, Nickel Alloys, Aluminums, Tool Steel Alloys
The Alpha 140 from German company Kurtz Ersa (with a technology center in Fort Worth, Texas) is another printer trying to make LPBF easy and accessible. The Alpha 140 is a solution for tool-free production of metal parts, especially for small and medium-sized companies.
Because it’s an open system, you can set the process parameters in the slicer according to your part’s individual requirements. The small size of the machine with a footprint of 1.675 x 0.92 meters saves space.
Kurtz Ersa is 250-year-old company that also makes a wide range of equipment for electronics manufacturing.
Farsoon FS121M
- Printer Farsoon FS121M
- Build Volume 120 × 120 × 100 mm
- Laser Type 200W Fiber Laser
- Materials Stainless Steels, Maraging Steel, HX Steel, Coppers, Cobalt Chromes
Farsoon, the large Chinese 3D printer manufacturer, aims to cover all the bases of metal printing with a wide range of printer sizes. Its smallest is the FS121M. This flexible and open system enables you to select between multiple laser spot sizes, different recoating blades, and powder choice.
The FS121M features a 200W Yb-fiber laser, inert gas supply, and over-sized protective filter systems to create a safe environment for the product and your staff.
Materials include 316L, 17-4PH, Maraging steel, HX, Cu, CuSn10, CoCrMoW, and CoCrMo.
Earlier in 2021, Farsoon introduced its latest, the FS273M laser powder bed fusion 3D printer. The company spent six years optimizing the productivity and performance of the machine while pushing to reduce costs.
The FS273M has a large build volume (275 × 275 × 355 mm) and dual fiber lasers (2 × 500W) or a single 500W fiber laser. Other new features include a brand-new re-coater design that enables faster speed and more stable powder delivery throughout the whole manufacturing process, a preheated base-plate, removable overflow containers, and a back-up powder supply sufficient for a full build.
The FS721M is an open platform system, which means that all machine parameters are unlocked for the user as well as an open material policy.
Not quite ready for prime-time the FS273M is open for early adopter program application.
Velo3D Saphire
- Printer Velo3D Saphire
- Build Volume 315 x 315 x 1000 mm
- Laser Type Dual 1000W Lasers
- Materials Aluminum, Inconel, Hastelloy C22 & X, Titanium, Nickel-based Superalloy Amperprint
The Velo3D Sapphire “next-gen” metal 3D printer sets itself apart as a volume production system with the advantage of support-free 3D printing and a one-meter tall build volume. Using dual 1-kilowatt lasers in its 315 x 312 x 1,000 mm print space, the Sapphire can print in aluminum F357, Inconel IN718, Ti 6Al-4V Grade 5, and Hastelloy (a nickel-chromium-iron-molybdenum alloy) C22 and X.
For Velo3D, support-free geometries mean the Sapphire can achieve prints with overhangs of zero degrees – flat surfaces on the horizontal plane, basically. In addition to saving time on post-processing prints, the printer able to realize internal channels and volumes without consideration for support structures.
In 2020, Velo3D introduced the new Sapphire XC printer, the name standing for “Extra Capacity.” True to its name, the Sapphire XC can increase production by five times compared to its sibling and reduce cost-per-part by 75%, the company claims. This XC has with a build volume of ø600 x 550 mm and eight lasers.
DMG Mori LaserTec 12 SLM
- Printer DMG Mori LaserTec 12 SLM
- Build Volume 125 x 125 x 200 mm
- Laser Type 200W or 400W Fiber Laser
- Materials Aluminum, Cobald Alloys, Copper Alloys, Steel, Nickel-based Alloys, Scalmalloy, Stainless Steel, Titanium, Tool steel
German machine manufacturer DMG Mori makes CNC machines, lathes, die & mold machines, directed energy deposition 3D printers, and two PBLF 3D printers; the Lasertec 30 Dual SLM and the smaller Lasertec 12.
The Lasertec 30 Dual SLM system is equipped with two 600 W (optionally 1 kW) lasers. It is an upgrade introduced in 2020 on the standard Lasertec 30, which features a single laser. The scan field of each laser on the Lasertec 30 Dual SLM covers the entire build chamber, which measures up to 300 x 300 x 300 mm. This enables build rates of up to 90 cm³/h, and raises the output of the machine by 80 percent compared to a machine equipped with a single laser. The Lasertec 30 also featured an active cooling system for the build area that enables you to remove finished components faster.
Equipped with Optomet software for parameter optimization, and Celos software for CAM programming and machine control, the Lasertec 30 identifies the scan strategy that is most efficient for the print job at hand, thus optimizing its performance, the company says.
Another feature is rePlug module for material change and powder supply that enables automated powder handling and powder-recycling. It let you change materials without contamination in less than two hours, the company says. The Lasertec 30 Dual’s material compatibility ranges from tool steel and stainless steel through aluminium and cobalt-chrome to Inconel and titanium.