What are the secrets to a successful additive manufacturing operation?
This is a question posed by many indusry stakeholders, as additive manufacturing increasingly moves towards end-part production. While 3D printing has come a long way, particularly over the last 10 years, there remain core challenges that need to be addressed.
The 3 pillars of 3D printing success
The keys to a successful AM operation lie in 3 crucial areas:
1. Hardware
2. Materials
3. Software
These elements make up what we’ve termed the 3 pillars of industrial 3D printing, as the technology’s move into end-part production will hinge upon continued advancements in each of these areas.
With that being said, let’s take a look at the challenges faced in each of these spheres, and the steps that are being taken to address them.
Pillar #1: Hardware
Without a doubt, the industrial 3D printers of today are a far cry from the early systems of the 1980s. They have become faster, more reliable and increasingly, manufacturers are developing industrial 3D printers with an eye towards production.
Accuracy and repeatability
But for additive manufacturing to become truly viable for end-part production, it will be vital that the machines are developed to ensure process repeatability and accuracy 100% of the time.
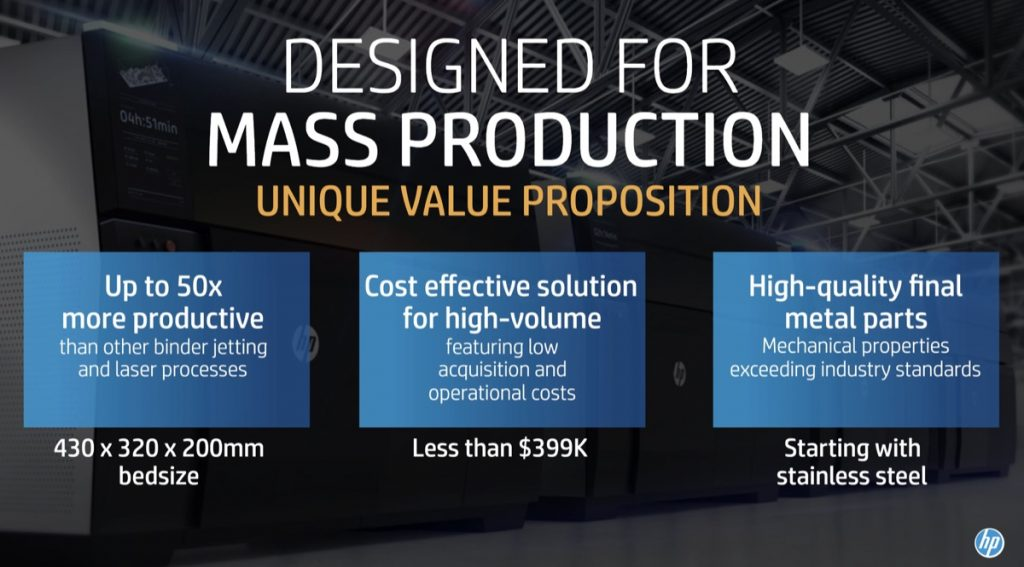
- Orientation
- Position
- Placement of the part (in relation to other parts in the print bed)
And yet, reliability and accuracy remain an ongoing challenge for hardware manufacturers. As it stands, many industrial 3D printers are not fine-tuned to the point where they can create reliable parts 100% of the time, particularly in the case of metals. When compared to established, traditional methods, this is a problem area that will need to be solved for AM to present a valuable alternative.
Additionally, the 3D printing process often results in parts with different properties. This issue can primarily be attributed to the numerous process parameters which need to be tightly controlled and monitored. One way of dealing with this complexity is developing closed-loop feedback control systems which will ensure the quality and repeatability of end-part production.
Velo3D is a company that has incorporated such a closed-loop system into its 3D printers. The US-based manufacturer has recently launched its metal powder-bed Sapphire machine which is said to deliver superior part-to-part consistency thanks to the integrated in-situ process metrology. This enables a closed-loop melt pool control, reducing the chance of deformation and the variability between parts.
Speed and scalability
Issues relating to print speed and scalability limit the mass-production potential of 3D printing systems. But here, too, hardware manufacturers are attempting to overcome this issue. Take HP for example: the manufacturer launched its Multi Jet Fusion system last year with the aim of scaling up AM production of plastic parts. To date, around 3.5 million parts have been produced with the MJF machines, with half of them for end-use applications.
HP has also recently announced plans to go into end-part production for metals, having debuted its Metal Jet machine earlier this year. The machine promises up to 50 times more productive than comparable metal binder jetting and SLM machines. And, with an eye towards meeting certification standards, the system is said to be able to produce stainless steel parts matching ASTM International standards.
Pillar #2: Materials
Materials constitute the second pillar of industrial 3D printing. Again, many advancements have already being made in this area, with the range of AM-compatible materials spanning metals, polymers and even ceramics. However, key challenges relating to costs and standardisation still need to be overcome.
High costs
The need to ensure that additive manufacturing remains cost-competitive when compared to traditional manufacturing methods is vital. And yet, high material costs are one of the main challenges facing manufacturers.
Here, perhaps what is needed most is greater collaboration. Ultimaker is one example of this; the open-source desktop 3D printer manufacturer has announced collaborations with several global materials companies.
In a recent interview with AMFG, Ultimaker North America President John Kawola reiterates the need for more competition to drive down costs: “The reality in 3D printing today is that the cost of filament for an FDM machine is very roughly around $50 per pound whereas it’s $3 dollars a pound for injection moulding. That’s an order of magnitude off. But over time with more competition, more development and more of an eye toward production, that gap will start to close.”
Standardisation
Another challenge lies in the lack of standards for 3D printing. Related to this is the current portfolio of AM-specific materials. While plastics are comparatively well established, the industry awaits greater material diversity, particularly with metals and ceramics. For example, many alloy grades for metals are either unavailable or have not yet been developed for additive manufacturing. Broadening the portfolio of AM materials, adapted to the different industry requirements, will ultimately allow for a wider range of applications across industries.
ASTM International, a standards developing organization, is one of several working to address this. The organization has partnered with a number of key industry players to launch the Additive Manufacturing Center of Excellence, with a focus on developing standards for metal powders, among other initiatives.
The increase in materials companies entering the AM space is also addressing the challenge of material diversity. These new players come with new material offerings, particularly with regard to high-performance thermoplastics and lightweight metals.
Pillar #3: Software
Last, but not least, comes the third pillar of 3D printing: the software. A company may have the 3D printers and the materials in place to produce the required parts — but how can you guarantee that the management of your production processes are streamlined and efficient? How do you ensure complete visibility across facilities, departments and teams?
Managing workflows
This is where software comes into its own. Indeed, as a digital technology, 3D printing heavily relies on software to drive each element of the production process.
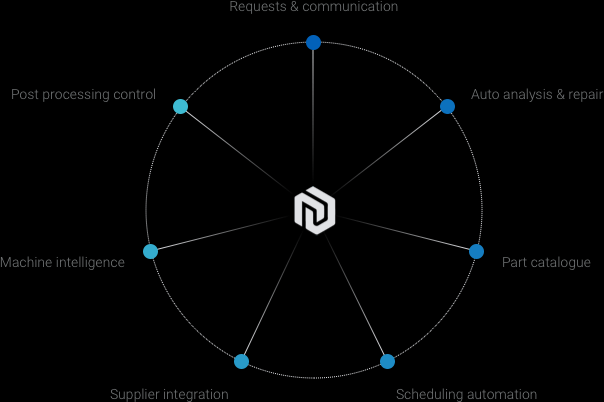
One of the major challenges for OEMs and service bureaus lies in the lack of an appropriate software system capable of handling the specific requirements needed for additive production. Since AM production involves steps that are not required for subtractive manufacturing (CAD design, analysis etc.), standard PLM or ERP systems will not be sufficient to handle the requests, CAD operations and other necessary activities. As it stands, the vast majority of companies are stuck using separate software packages, built for different functions that ultimately do not communicate with each other. This has a negative impact on both efficiency and visibility.
Fortunately, huge strides are being made in this area, with key developments in workflow management software. Taken at its most basic functions, such software assists in automating manual, client-facing tasks like incoming request management. However, taken to its fullest extent, such software, like AMFG, can also automate production tasks like build preparation and machine scheduling and provide real-time production metrics and insights.
Aside from workflow management, simulation software is also helping to solve many of the current challenges the industry faces. For example, predicting and analyzing 3D printing processes with simulation can help to prevent a costly trial and error approach, by ensuring that all parameters are the correct first time around.
Machine control
Perhaps one of the biggest problem areas lies in the ability to directly stream to and communicate with the AM machines in your production facility. The benefits of this are obvious: being able to control the machine remotely, assess capacity in real-time and so on. However, the vast majority of machines have not been developed with direct communication in mind. For 3D printing to become a method for end-part production, hardware manufacturers must work with software developers to ensure that their machines are open to such integration.
Overcoming challenges in 3D printing
Over the last decade, additive manufacturing has reached key milestones across hardware, materials and software innovation. However, the key to establishing 3D printing as a manufacturing method lies not in the success of one, but in the success of all three pillars.
We’re already seeing this on the hardware and materials side with announcements of new AM systems and materials collaborations developed for production. On the software side, AMFG is working to ensure that project and production management is automated for additive production.
What remains clear is that the industry will need to work more closely together to develop true solutions to ensure the technology’s shift towards production. Only by focusing on overcoming the challenges across the board can we can ensure that the industry continues on its continued growth path towards mainstream adoption.