Silicone rubber 3D printing is a new and innovative technology, that allows the creation of flexible and durable parts with complex geometries and high performance. Silicone rubber is a polymer that has excellent thermal stability, water resistance, biocompatibility, and electrical insulation properties. It is widely used in various industries such as healthcare, electronics, automotive, and consumer goods.
However, traditional manufacturing methods such as injection molding and casting have limitations in terms of design freedom, customization, and cost-effectiveness. 3D printing offers a solution to these challenges by enabling the direct fabrication of silicone rubber parts from digital models without the need for molds or tooling.
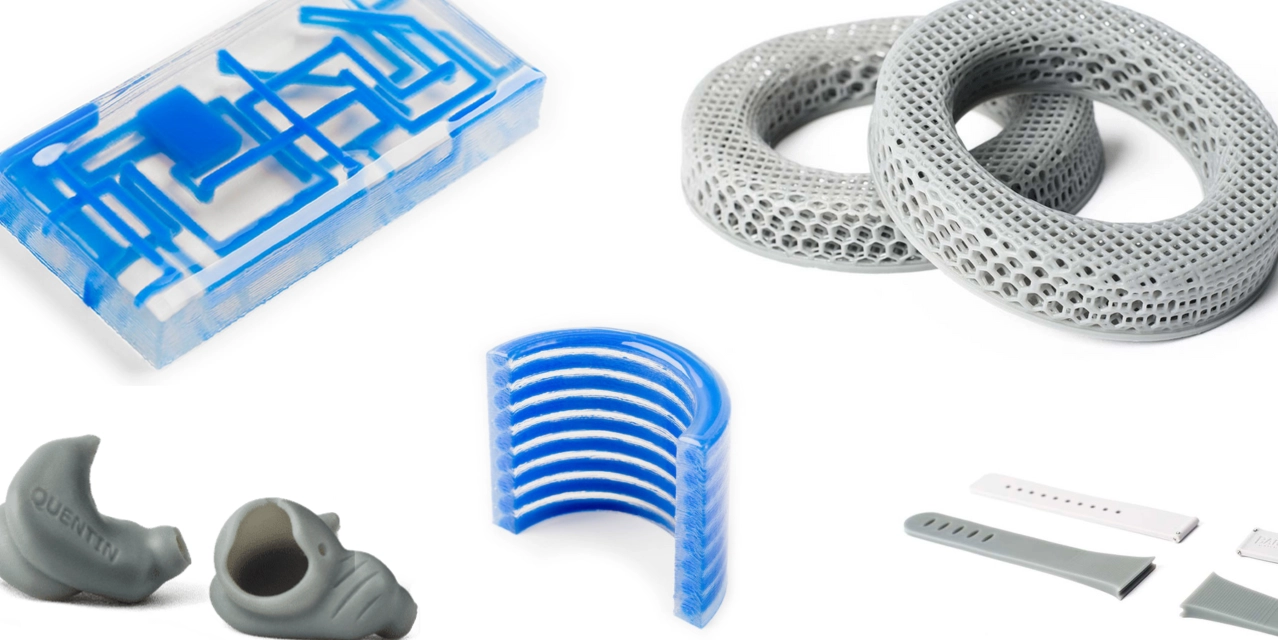
Types of Silicone 3D Printers
Types | Advantages | Disadvantages | 3D Printers |
---|---|---|---|
Print head deposition | High resolution, accuracy, and mechanical strength | High temperature and pressure requirements, limited part size | InnovatiQ LiQ 320, Lynxter S300X, Prayasta Silimac P250, San Draw S053 & S300 |
Vat photopolymerization | High detail, smooth surface finish, and complex shapes | Addition of UV curing agents, reduced biocompatibility | Spectroplast SAM, Desktop Health EnvisionTec Bioplotter, B9 Creations Core 5 Series Med XL, Delta Tower Fluid MT, Carbon3D |
There are different types of silicone rubber 3D printing processes, each with its own advantages and disadvantages.
Some of the most common ones are:
- Print head deposition: This process uses a print head that extrudes liquid silicone rubber (LSR) mixed with a catalyst and a cross-linking agent. The LSR is cured by heat, or UV light as it is deposited layer by layer on a build platform. This process can produce parts with high resolution, accuracy, and mechanical strength. However, it requires high temperatures and pressures, which can affect the material properties and limit the size of the parts.
- Vat photopolymerization: This process uses a vat filled with photopolymerizable silicone resin that is selectively cured by a light source (laser or projector) according to a digital model. The cured resin forms a solid part that is detached from the vat and post-processed. This process can produce parts with high detail, smooth surface finish, and complex shapes. However, it requires the addition of UV curing agents to the silicone resin, which can alter its properties and reduce its biocompatibility.
Silicone Rubber Applications
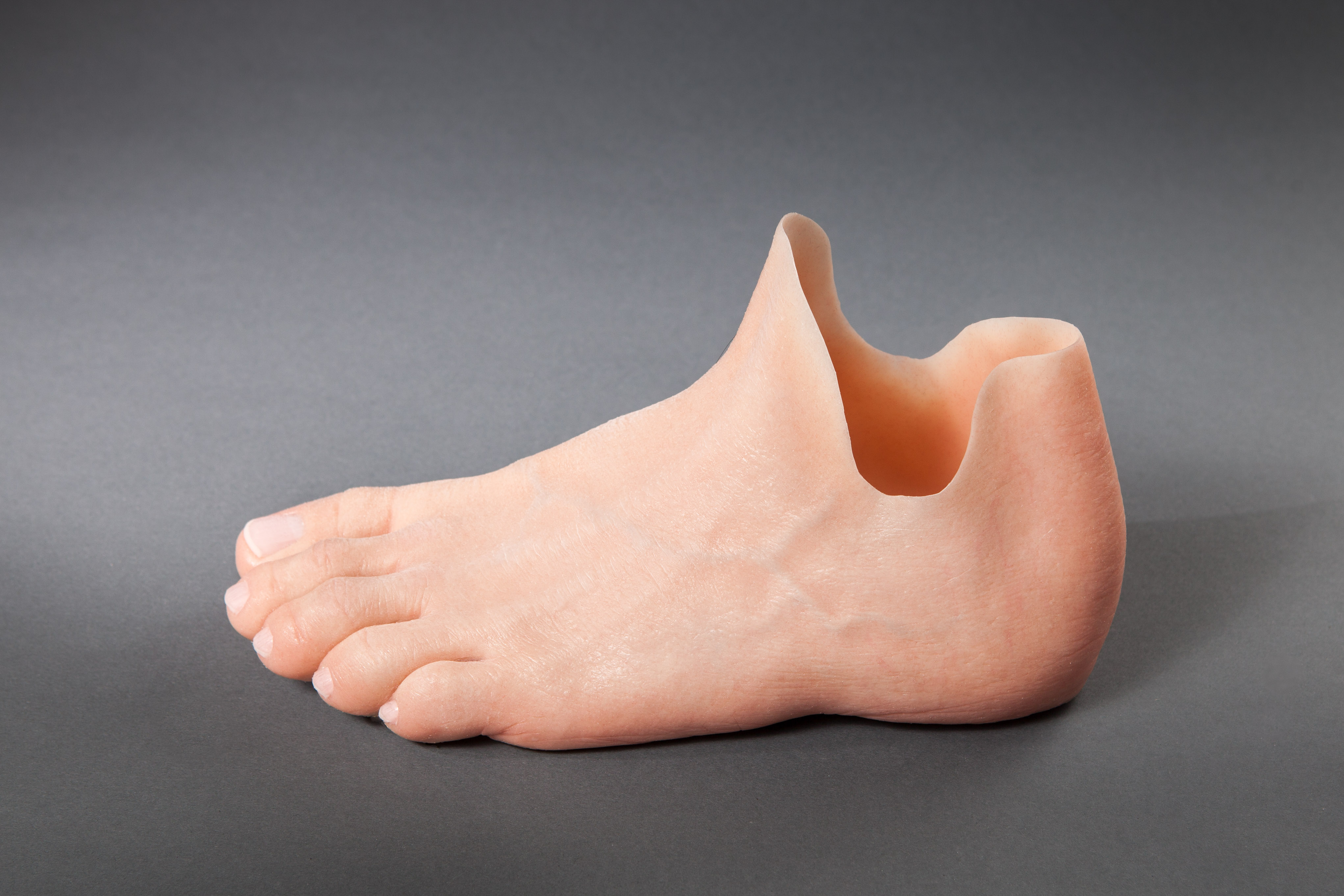
Silicone rubber 3D printing has many applications in various fields, such as:
- Healthcare: Silicone rubber 3D printing can be used to create customized medical devices and implants that fit the patient’s anatomy and needs. For example, hearing aids, dental prosthetics, surgical guides, catheters, valves, stents, masks, wound dressings, and organ models.
- Electronics: It can be used to create flexible and durable electronic components and devices that can withstand harsh environments and vibrations. For example, sensors, actuators, antennas, connectors, cables, keyboards, speakers, headphones, and wearables.
- Automotive: You can create functional and aesthetic parts with silicone rubber for vehicles that require high performance and resistance to heat, cold, moisture, and chemicals. For example, gaskets, seals, hoses, tubes, mounts, bumpers, spoilers, and dashboard elements.
- Consumer goods: It has already been used to create personalized and creative products for everyday use that offer comfort and functionality. For example, toys, jewelry, accessories, kitchenware, and utensils.
Challenges for Silicone Rubber 3D Printing
Silicone rubber 3D printing is a promising technology that offers many benefits over traditional manufacturing methods. However, it also faces some challenges and limitations that need to be overcome. Some of the main ones are:
- Material availability and cost: Most of the silicone rubber materials used for 3D printing are still in the research and development stage and are not commercially available yet. Moreover, they tend to be more expensive than conventional silicone rubber materials due to the addition of curing agents and other additives. Therefore, there is a need for more accessible and affordable silicone rubber materials that can meet the requirements of different applications and industries.
- Process optimization and standardization: Different silicone rubber 3D printing processes have different parameters and conditions that affect the quality and performance of the printed parts. For example, temperature, pressure, curing time, light intensity, layer thickness, and support structure. These parameters need to be optimized and standardized to ensure consistent and reliable results across different machines and materials.
- Post-processing and quality control: Silicone rubber 3D printed parts often require post-processing steps such as washing, drying, curing, trimming, and polishing to remove excess material, improve surface quality, and enhance mechanical properties. These steps can be time-consuming, labor-intensive, and costly. Moreover, there is a lack of standardized methods and tools for testing and evaluating the quality and performance of silicone rubber 3D printed parts in terms of dimensional accuracy, surface roughness, mechanical strength, elasticity, biocompatibility, and durability.
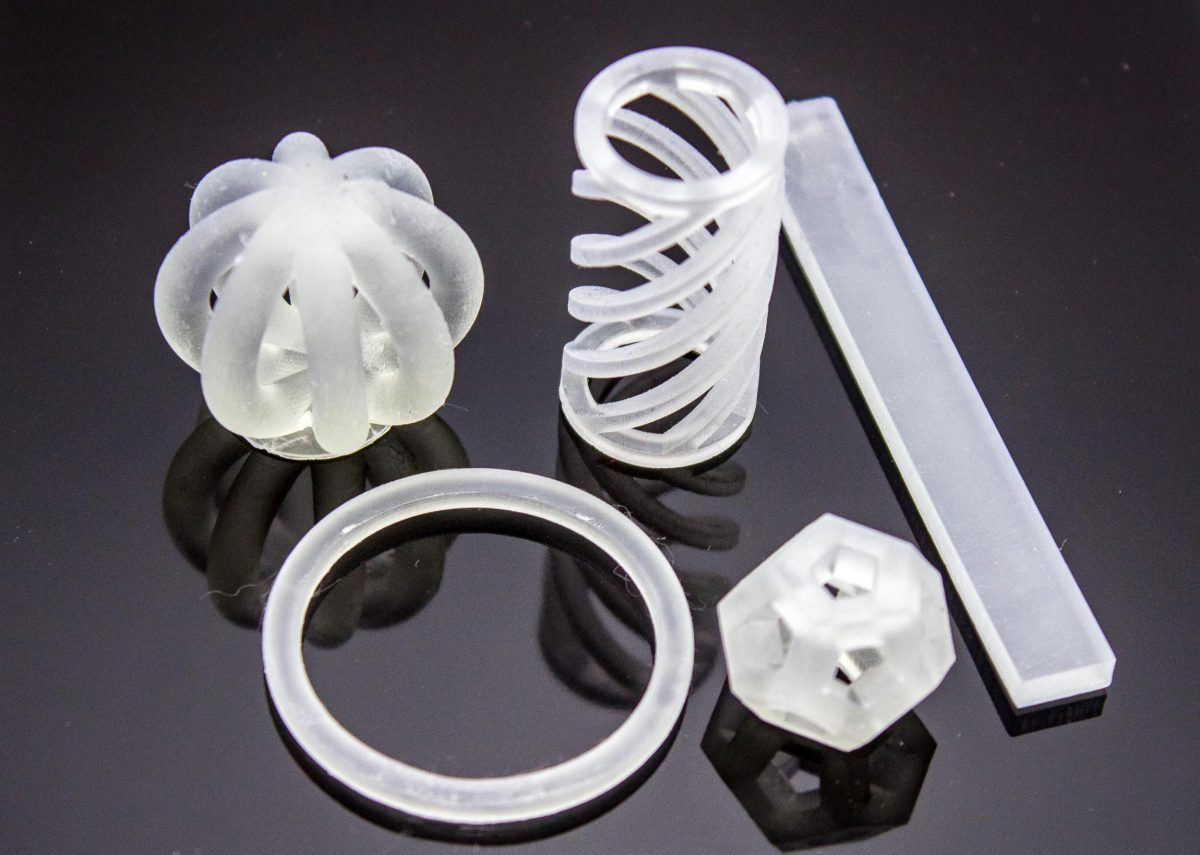
Silicone 3D Printing Service
Silicone rubber 3D printing is a rapidly evolving technology that has the potential to revolutionize various industries and applications. By overcoming the current challenges and limitations, it can offer more design freedom, customization, functionality, and efficiency for creating flexible and durable parts with complex geometries and high performance.
If you are interested in silicone rubber 3D printing, you could check out FacFox‘s 3D silicone rubber 3D printing services. FacFox is a leading online 3D printing service provider in China that offers high-quality, low-cost, and fast turnaround time for various 3D printing technologies and materials. We can help you with your silicone rubber 3D printing projects, whether you need prototypes, small batches, or large-scale production. FacFox can also provide you with professional design tips, material selection, post-processing, and quality control to ensure your satisfaction.
To get started with silicone rubber 3D printing at FacFox, simply upload your 3D model to our website facfox.com and get an instant quote! You can also contact our customer service team for any questions or requests. FacFox will take care of the rest, and deliver your silicone rubber 3D printed parts to your doorstep in no time.