For any company, looking to dip their toes into metal 3D printing, it’s crucial to know which metals can be used with this technology today. From design to manufacturing, choosing the right materials ensures the highest possible standard for the finished product.
To help you get up to speed with the current metals ecosystem for AM, we explore commercially available alloys for Powder Bed Fusion, key material requirements for successful printing and how the use of metals will evolve in the future. But let’s first explore what Powder Bed Fusion is.
A brief overview of metal Powder Bed Fusion technologies
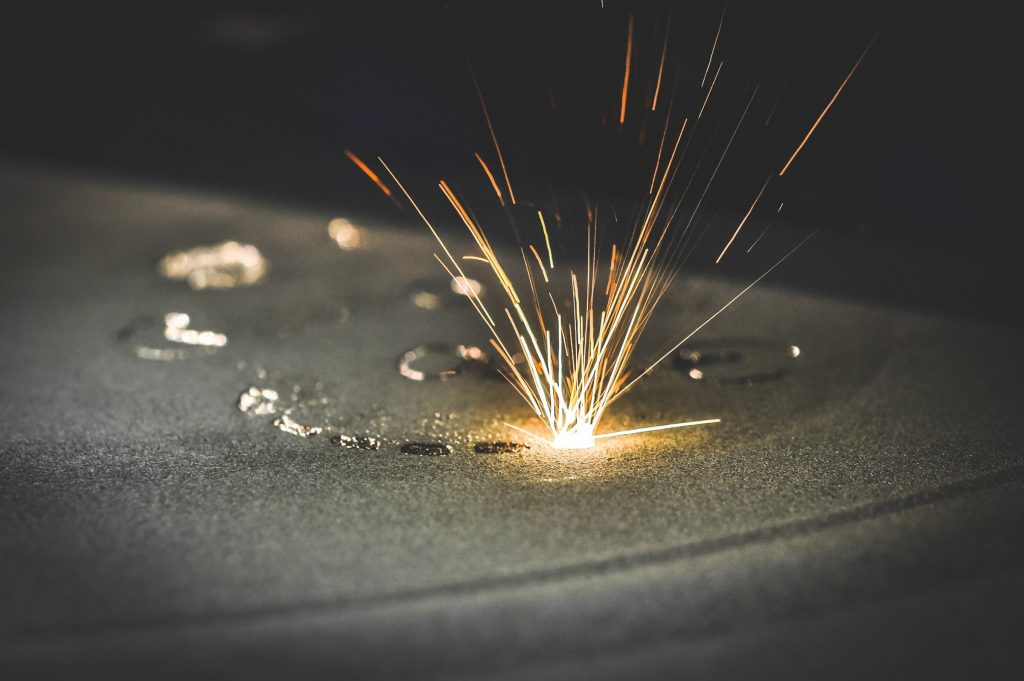
Metal Powder Bed Fusion (PBF) is the most established metal additive manufacturing (AM) technology today.
With PBF, layers of powdered metal are evenly distributed onto a machine’s build platform and selectively fused by an energy source – either a laser or an electron beam.
Two key metal 3D printing processes fall under the Powder Bed Fusion category:
- Selective Laser Melting (SLM) / Direct Metal Laser Sintering (DMLS)
- Electron Beam Melting (EBM)
In SLM, a powerful, fine-tuned laser is selectively applied to a layer of metal powder. In this way, metal particles are fused to create a part.
An important requirement for SLM is an enclosed build chamber filled with inert gas, such as argon. This prevents oxygen contamination of the metal powder and helps to maintain the correct temperature during the printing process.
EBM operates similarly to SLM in that the metal powders are also melted to create a fully dense metal part. To prevent contamination and oxidation of the powder, the EBM process takes place in a vacuum environment.
The key difference between SLM/DMLS and EBM technologies is the energy source: instead of a laser, EBM systems use a high-powered electron beam as the heat source to melt layers of metal powder.
Since an electron beam is typically more powerful than a laser, EBM is often used with high-temperature metal superalloys to create parts for highly demanding applications, like jet engines and gas turbines. Additionally, since the technology relies on electrical charges, EBM can only be used with conductive metals, such as titanium and chromium-cobalt alloys.
Metal 3D printing powder requirements
To ensure accurate and repeatable metal AM production, metal powders have to display consistent characteristics.
Due to the different powder production methods, powder characteristics differ by process and alloy. Some of the most important characteristics include:
- Particle Size Distribution (PSD): Smaller particles allow finer resolution of part dimensions and surface finish. Within PBF, EBM systems traditionally use a 45–105 µm PSD, whereas most laser-based systems desire 15–45 µm PSD.
- Morphology: Smooth regular-shaped metal powder particles are preferable. This allows them to be well packed, which results in a dense product with good and desired mechanical properties.
- Flowability: Powder flowability plays a major role in forming a homogenous powder layer, as the powder is spread by the recoater.
- Density: Optimum packing density of powder during flow and processing positively impacts the integrity and surface finish of 3D-printed parts. Ellipsoidal particles would have better and more consistent natural or random packing.
- Chemical/phase composition: This explains why not all alloys are available as powders. PBF generally favours weldable metals.
What metals can be 3D printed in Powder Bed Fusion?
Steel
Alloys available for AM: 316L, H13 Tool Steel, Maraging Steel, Case Hardening Steel, Stainless Steel 15-5 PH, Stainless Steel 17-4 PH, Stainless Steel 300 series, Stainless Steel 400 series, Low Alloy Steels
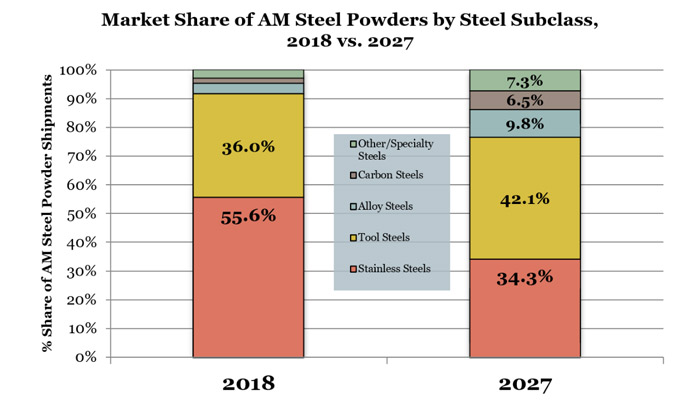
In metal PBF, there are only about ten primary steel alloys that are widely printed today. Though a set of printed steels is quite small today, compared to traditional metalworking technologies, companies like Carpenter, Sandvik, Hoganas, GKN, and Oerlikon are all actively developing new steels for AM to tap into new markets.
For example, GKN Additive Materials has recently pioneered new low alloy steel powders for AM. Due to their toughness and corrosion resistance, low alloy steel powders create new opportunities for AM in sectors such as the automotive industry, where scalability and cost are key drivers.
Today, the use of steel for end-part AM production is growing, particularly in newer markets for 3D printing, such as maritime and automotive. This makes steel one of the keys to furthering the adoption of metal AM technology beyond the traditional medical and aerospace industries.
These advancements indicate that steels are very likely to become the most widely used metal AM materials over the next several years.
Aluminium
Alloys available for AM: Al-Si10Mg, AlSi12, AlSi7Mg, AlSi9Cu3, Al4047, Al-Si-Mg (F357), Scalmalloy (Al-Mg-Sc), Al-Cu-Ti-B2 (A205/A20X)
Aluminium is a strong, light-weight metal that combines outstanding mechanical and thermal properties. For those reasons, aluminium alloys are widely used in the aerospace, automotive and biomedical industries.
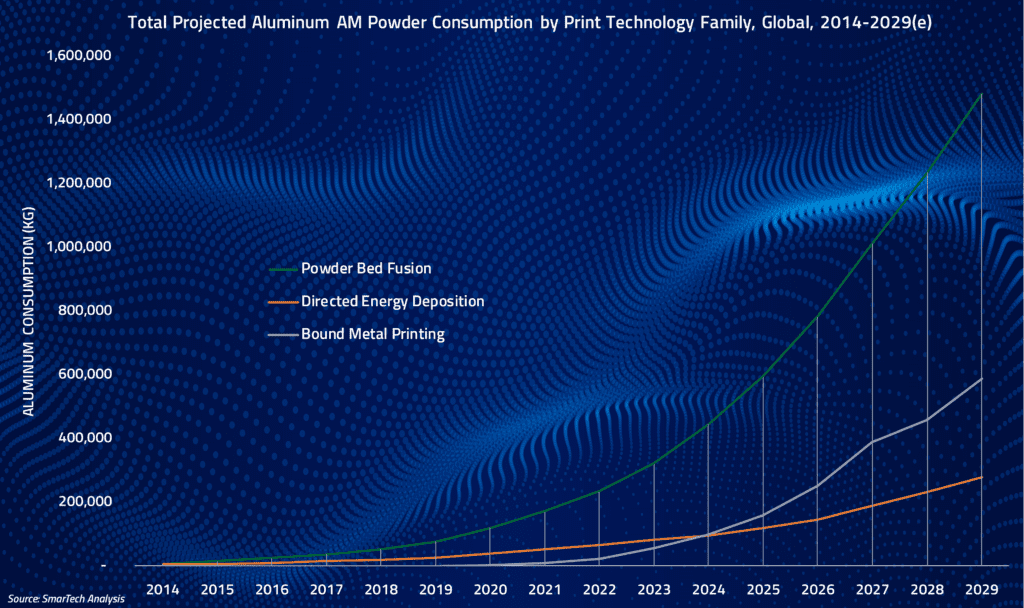
For example, APWORKS, in collaboration with Airbus, has developed Scalmalloy for aerospace applications. The material offers the lowest buy-to-fly ratio, a particular boon for the aerospace industry.
While the material was developed with aerospace in mind, its properties are also attractive for the motorsports sector – that’s why Scalmalloy was recently added to the list of approved AM materials for Formula 1.
However, many aluminium alloys for AM remain very expensive and don’t meet the requirements of the target industries. For example, the automotive industry requires aluminium 3D-printed parts to pass crash tests to be considered for their use in mass-produced vehicles.
Engineering group, EDAG, has developed a new aluminium alloy, known as CustAlloy, as a part of the ‘CustoMat_3D’ research project, focused on adapting AM for automotive series production.
The newly developed material is designed to overcome these challenges by providing both higher strength and higher elongations at the break – essential properties that will allow automotive 3D printed parts to use the new alloy to perform well in crash tests.
Titanium
Grades: Ti-6Al-4V (Grade 5), Ti-6Al-4V (Grade 23), Cp-Ti (Grade 1), Cp-Ti (Grade 2), Ti-Al, Ti-6Al-2Sn-4Zr-2Mo, Ti5553, Ti6242
Titanium has excellent material properties, but its high cost has historically limited its use to high-value applications in aerospace.
Now that metal 3D printing is becoming increasingly recognised as a viable manufacturing method, the technology is making titanium more available to industries like medical, automotive and motorsports.
There is great potential for titanium 3D printing, particularly in the area of orthopaedic implants, thanks to titanium’s non-toxicity, high strength and resistance to corrosion.
When used with 3D printing, medical device manufacturers can create titanium implants with complex, porous structures. Remarkably, these structures imitate the structure of human bones, so the bone cells recognise it as a scaffold through which to grow.
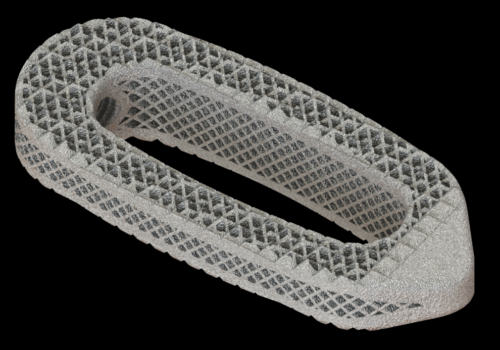
For example, Sandvik opened a powder plant, for its titanium and nickel-based superalloys under the Osprey® brand, at the end of 2019. That same year, PyroGenesis, a Canadian manufacturer of plasma atomised metal powder, increased its production rate of titanium powder, which also allowed the company to lower the cost of a historically very expensive titanium powder production.
Copper and Precious metals
Alloys available for AM: CuNi3Si, CuNi2SiCr, CuCrZr, CuAl10Fe5Ni5, Cu High Oxygen
Not all metals lend themselves well to 3D printing. For example, copper is particularly challenging to print, with the vast majority of 3D-printed copper currently based on alloys of copper, not the pure metal.
Pure copper has a laser reflectance rate of over 90 per cent, and it’s difficult for the laser to continuously and regularly melt the pure copper powder.
One way forward is to develop new systems capable of 3D printing such metals.
At Formnext 2018, TRUMPF demonstrated its green laser technology, which can print pure copper, as well as other precious metals.
The company believes that 3D printing pure copper can become an alternative way to create conductive inductors and heat exchangers, which are particularly useful for the electronics, automotive and space applications.
In terms of precious metals, like gold, silver and platinum, the advantage of 3D printing these materials lies in the possibility of achieving intricate design, ideal for jewellery, accessories and decorative objects.
However, 3D printing of precious metals is usually indirect and involves the production of a wax mould, which is then used in a wax-casting technique.
Direct 3D printing with precious metals, using PBF, is also possible, although the number of 3D printing machines compatible with precious metals is limited.
Superalloys
Superalloys, a family of metal mixes based on nickel, cobalt or iron, are resistant to high-temperature deformation, corrosion and oxidation, particularly when operating at an elevated temperature close to their melting point.
First developed for gas turbine components in turbojet engines, superalloys are now widely used for high-temperature applications in the aerospace and power generation industries.
Nickel
Alloys available for AM: Inconel 625, Inconel 718, Inconel 738, Inconel 939, Ni-Ti, Waspaloy, Hastelloy, ABD900AM, Haynes 282
Nickel alloys first became commercially available for use in metal PBF processes as early as 2007.
Current demand for nickel alloys is dominated by superalloys in the Inconel family – particularly IN625 and IN718 alloys – thanks to their significant capabilities in applications requiring great hardness, tensile strength, and perhaps most importantly, chemical and temperature resistance.
In addition to these two alloys, there are many more nickel-chromium superalloys offered by leading metals companies. Several Haynes superalloys, Hastelloy superalloys and various forms of Inconel are now becoming more established.
While the aerospace industry is currently driving the majority of the demand for nickel-based additive manufacturing, there is huge potential for 3D printing of nickel superalloys in the oil and gas, energy and general industry segments, like chemical processing.
Cobalt
Alloys available for AM: MP1, CP2, Co-Cr, Co-Cr-MoC, 188 Cobalt Alloy, 509 Cobalt Alloy, CoCr-0404, CO502, CO90, CO212, Co49Fe2V
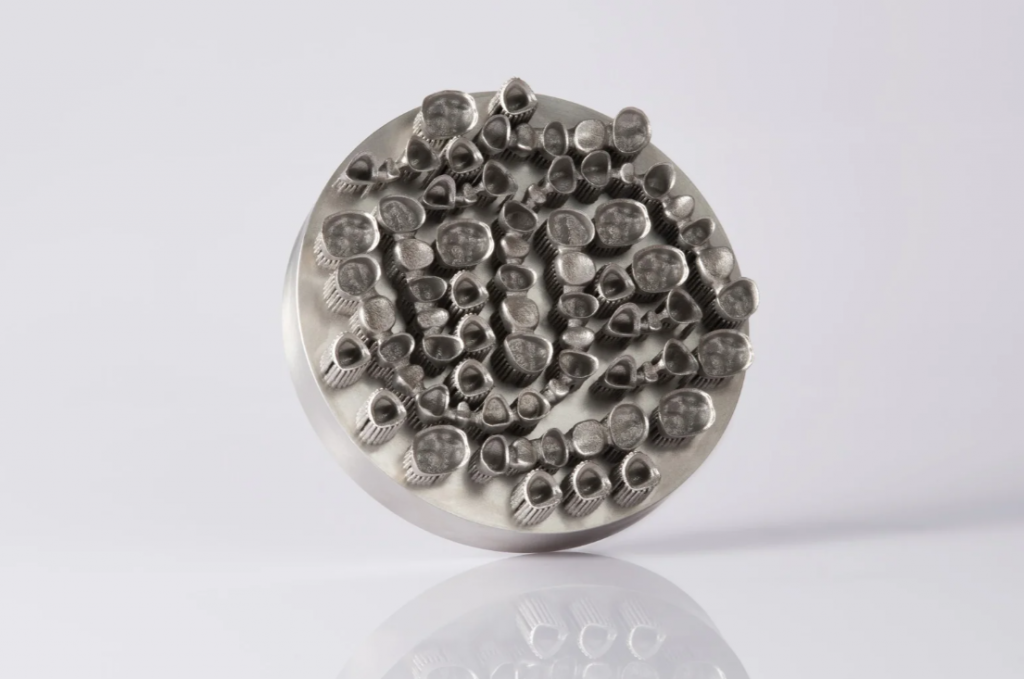
Cobalt superalloys possess great mechanical properties, alongside resistance to corrosion and high temperatures. Cobalt chrome alloy is particularly suitable for medical (orthopaedic implants) and dental applications, as it has excellent biocompatibility.
Iron
Alloys available for AM: Invar 36, Fe-Si, Fe-Ni
A few metal PBF system manufacturers offer the possibility of printing Invar 36, a nickel-iron alloy, notable for its extremely low thermal expansion. Invar 36 is used in components that require high dimensional stability over a wide range of temperatures, such as in radio and electronic devices, aircraft controls, optical and laser systems.
Höganäs, one of the leading manufacturers of metal powders, also provides a range of iron-based powders, resistant to abrasion, wear and corrosion, under its AMPERPRINT brand.
Refractory metals
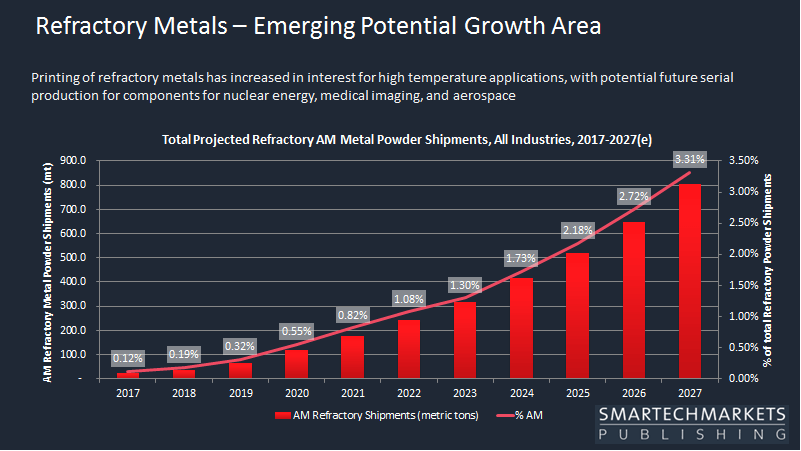
The most common use of refractory metals in AM today is in alloying with steels, nickel and cobalt materials to create many popular superalloys.
Currently, only a few companies are offering refractory metal powders for AM.
H.C. Starck Tantalum and Niobium GmbH, which has recently been rebranded as TANIOBIS GmbH, is one such company, providing a range of atomised tantalum and niobium (Ta/Nb) powders and their alloys, designed for AM under the AMtrinsic brand name.
Tantalum and niobium, TANIOBIS believes, will open up new opportunities in AM, citing their high melting points, high corrosion resistance and high thermal and electrical conductivity.
Properties like these would enable companies to apply AM in chemical processing, the energy sector and a range of high-temperature environments.
The ever-growing range of metal 3D printing powders
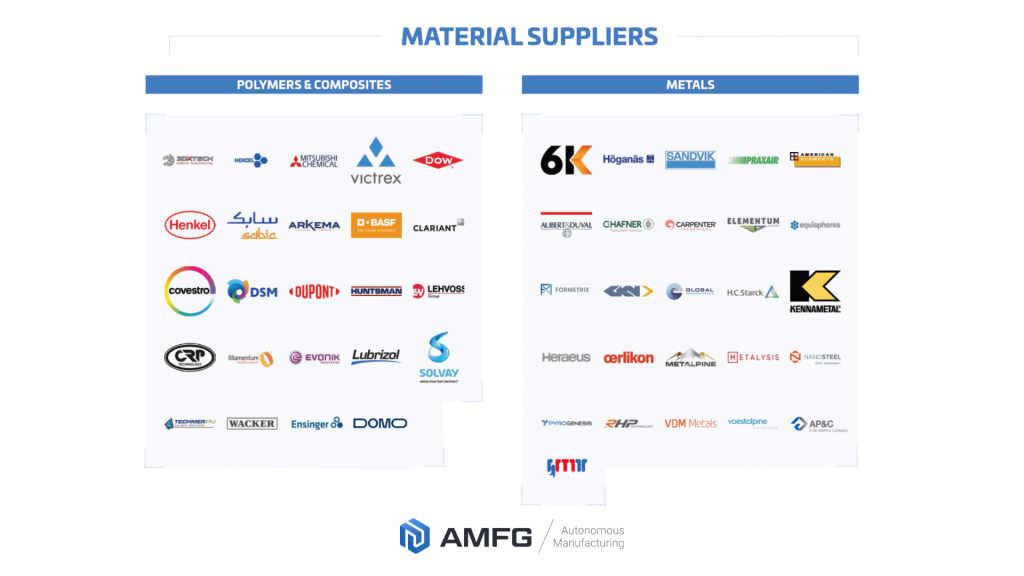
One reason for this is the time and resources it takes to develop new metal powders for AM – in some cases, the development process can take a few years.
Another reason lies in the hardware limitations, like it was in the case with the copper powder, which requires a different laser wavelength, compared to other metals, to be printed successfully. Fortunately, hardware challenges are being overcome to further expand the scope of printable metals.
Despite the challenges, the future of metal PBF looks bright, as its adoption in production grows and more industries start to embrace the technology. This means an increased focus on new material chemistries that will help to unlock new applications and take metal 3D printing to the next level.