According to Jacob Nuechterlein, co-founder and solutions developer for Elementum 3D, the aluminum alloy used in the company’s newly invented metal matrix composite (MMC) is not 3D-printable on its own. Not every metal is a candidate for use in an additive process. With this alloy, a form made of the metal will tear itself apart from internal stresses as it is built up in a laser powder-bed additive machine.
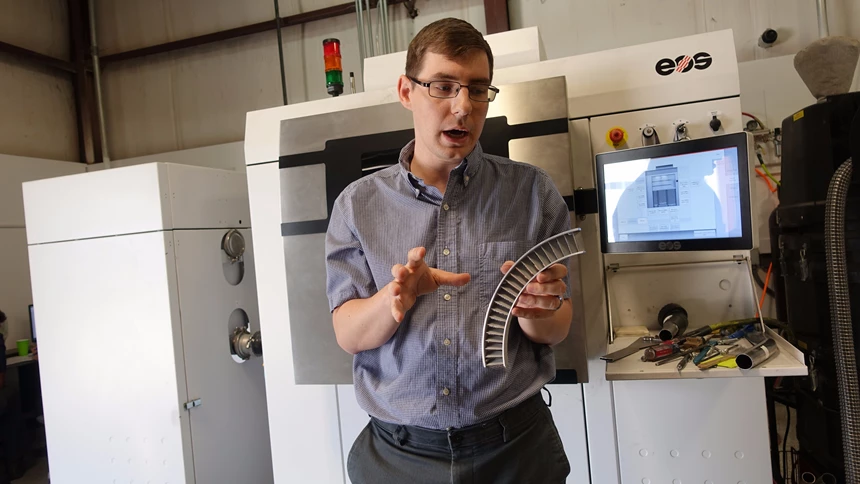
However, when a ceramic is added to the metal—that is, ceramic powder that does not melt during the build—the result is very different. The ceramic, in combination with a proprietary process the company developed for applying this material, makes this metal 3D-printable. More importantly, the combination of ceramic plus metal produces a strong, lightweight, heat-resistant material that holds considerable promise for various future applications, not the least of which is the additive production of dramatically lighter aerospace or car engine components.
This new material is not a compound and not a new alloy. It is a composite, meaning its constituent materials complement one another while remaining chemically separate. Well-known composites include concrete and fiberglass, plus the carbon-fiber-reinforced plastic used in aircraft. But here is a case of a composite in which the components can be seen only under a microscope. MMCs of this type can be made by compacting powder in a mold, but thanks to additive manufacturing, Elementum 3D has now not only pioneered a new MMC blend, but also extended the range of applications for this class of materials into geometries that molding can’t achieve. Through additive, MMCs will do more and there will be more of them. The primary obstacle standing in the way is simply the discovery process and the development work that every new material for AM requires—and this is the obstacle Nuechterlein expects his company to help overcome.
The Knob Problem
The Colorado-based startup developed the aluminum MMC on an EOS M 290 direct metal laser sintering (DMLS) machine. The material will be made available through EOS, Nuechterlein says, and that commercialization represents an important success for his company. It will be the first completion of a material-development process the firm will perform for customers as its core service and its contribution to additive manufacturing’s advance.
The company is already working with customers on several new additive metals (all the current projects involve metals, not MMCs) in various stages of development. In Nuechterlein’s view, this work pursues the most meaningful potential value of AM. He says the too-little-appreciated aspect of the design freedom of additive manufacturing is its material freedom—the freedom to make the part from a material that has been custom-designed for that part’s needs. Applying his background is in material science, specifically powder metals, he started the company to help manufacturers explore this aspect of designing for AM.
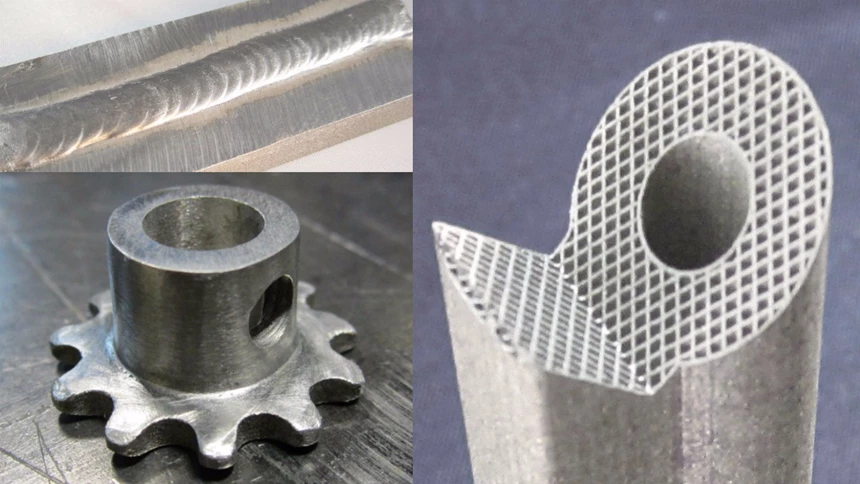
But first they have to realize they have this freedom. The realization is not yet widespread. To date, he says, AM users have tended to remain “stuck within the box of the eight or ten standard metals currently proven for a given additive system.” In fact, additive ought to vastly multiply the range of material options. It ought to open the way to use metals and other materials not currently being applied in conventional processes.
For now, the small firm (currently nine employees) is limited to developing materials for the EOS platform. This is the system it has and the system it is experienced with. For manufacturers who themselves use EOS equipment, the case the company makes for taking on their material development is compelling. Because Elementum 3D has worked to develop other AM materials already, its team is already farther along the learning curve for a new material than any manufacturer could hope to be that tried to develop its own material itself. Given all the inputs and parameters that might be adjusted in search of controlled, successful, repeatable additive building with a new alloy, a machine like the M 290 “gives us practically 1,000 different knobs to turn,” he says. His company is more advanced than most in knowing which knobs to begin with, and which knobs to use in fine-tuning either the material or the process.
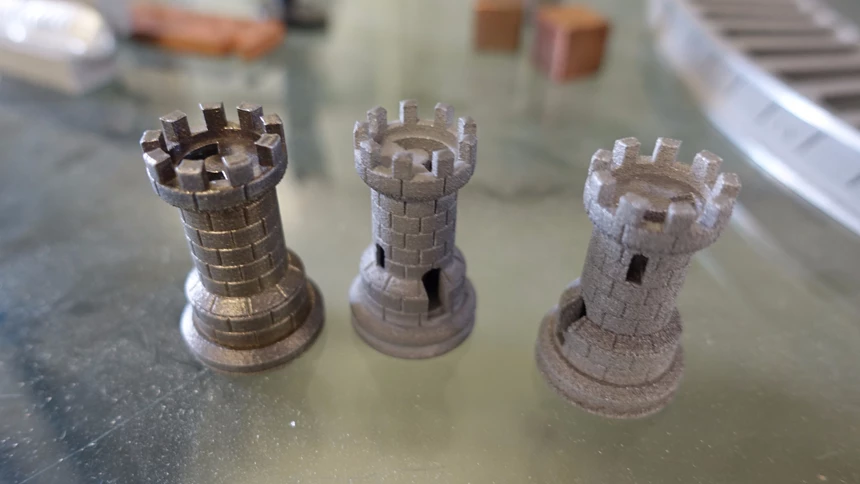
Further, his company hopes to market the materials it develops, and this brings potential cost saving as well. It means that any manufacturer hoping to develop a new material might have the opportunity to split its expenses. If the manufacturer will allow Elementum 3D to supply the new material to other companies that might benefit from it (potentially including the manufacturer’s competitors), then the chance exists to streamline the development cost.
For example, a manufacturer of industrial cutting tools recently came to the Colorado firm in the hope of developing not an all-new alloy, but instead an additive material equivalent to the existing material used for that company’s tooling. The manufacturer hopes to be able to 3D print tools in small quantities for special orders and prototyping using the same steel as its mass-produced products. Nuechterlein did not wish to detail the terms of the agreement with this customer, but in theory, a material such as this might represent an exciting new product for other industrial tooling makers as well.
Fit to Print
The course of developing an entirely new AM metal or MMC could require up to 12 months, he says. There is a lot of building of test samples. There is a lot of constructive failure on the way to zeroing in on precisely the properties being sought for that new material. However, in much less time—within a month—he says his company can determine whether a prospective new material is “possible and interesting.” That is, whether it is viable for effective application within the laser-sintering process.
If it is, then Elementum 3D’s material-development work entails several stages. First, the company evaluates sourcing for the powders the material needs, looking to establish whether suppliers exist that can provide the requisite powder in both the consistency and the volume that the intended application will require. Then the team moves into making test coupons and systematically experimenting with different sets of laser settings and other build parameters to observe the effects. Mastery of the material’s core properties comes first, followed by further experimentation to refine the control over the material’s surface properties. Then, the company experiments with postprocessing steps such as anodizing and welding.
Many restrictions potentially impede a material’s suitability for AM, specifically DMLS. The most basic consideration Nuechterlein points to is whether the material is available in the right powder size and particle shape. The powder also needs sufficient flowability. The material needs to be weldable, he says, and weldable specifically to itself. And the microstructure of the metal as it solidifies needs to be stable and conducive for the formation of precise large-scale forms. (This last point is the factor preventing successful use of the aluminum alloy outside of the metal matrix composite.) Thus, AM is like any other manufacturing process in this respect: Some materials work well for it and some do not. Some materials are inherently more “printable” in the same way that some materials are inherently more machinable. But the exciting promise lies in the fact that the materials lending themselves to 3D printing are liable to be different from the materials lending themselves to machining. With additive manufacturing, certain materials can become “easy” that were never practical to apply before.
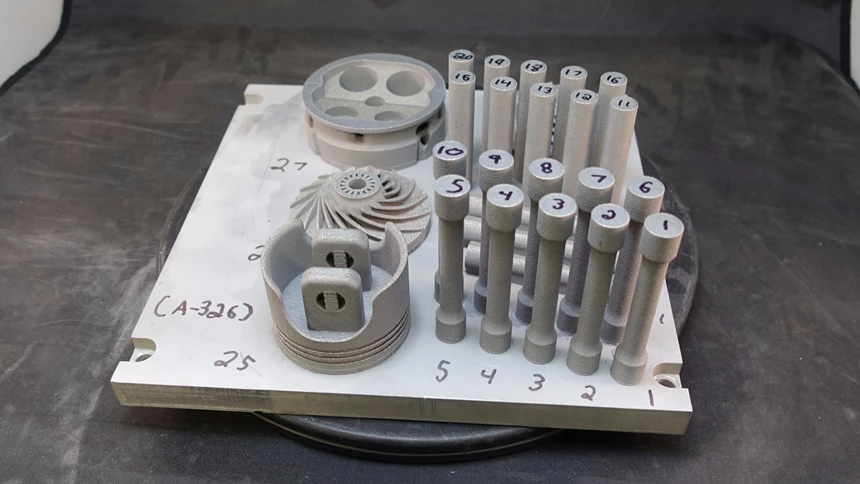
The new MMC is an example. The composite combines the light weight of aluminum with the strength, hardness and heat resistance of ceramic, making this material a promising choice not only for engines but also for applications in which high stiffness is needed for vibration control, or a low coefficient of thermal expansion is needed because of an extreme temperature range (the case with satellite parts). Yet the material’s very combination of heat resistance and hardness makes it difficult and costly to machine. Additive manufacturing addresses this problem because it is not just near-net-shape (true of a molding), but rather very near to net shape. A precisely controlled AM process can minimize the amount of machining to the point of making this hard-to-machine material cost-effective to apply. The AM process also makes it possible to achieve internal lattice forms and other highly complex shapes that hadn’t been possible to realize in a metal matrix composite before.
As a result, there is a message in this material, says Nuechterlein—an implication that offers part of the reason why he was eager to see his company pioneer this unusual material first.
That message is simple, and it gives words to the realization he expects manufacturers to come to in increasing numbers. The message of this material relates to the advantage of AM that might ultimately prove to be its most important capability. With additive, says Nuechterlein, “I can have the material properties I want.”