3D printing may seem like a miracle compared to traditional manufacturing processes: design nearly anything, hit a button and manufacture a real part. However, many potential users of the technology often have questions about processing and finishing printed parts.
This is particularly true for emerging additive manufacturing (AM) technologies, such as HP Jet Fusion 3D Printers . Given the fact that HP Multi Jet Fusion technology (MJF) has been billed as a platform built for mass manufacturing, it’s important to understand how post-processing MJF parts plays into the larger production workflow for the technology.
Here we look at post-processing techniques required for an array of AM methods and compare those to MJF.
What Is AM Post-Processing and Why Is It Needed?
As is the case with most manufacturing processes, AM parts aren’t complete until they’ve undergone the necessary finishing steps. In 3D printing, this can mean anything from ultraviolet curing of photopolymer components to machining off excess metal left by support structures. Whatever the technique, post-processing is required to make the part smoother, stronger or to match the specific tolerances of a job.
Postprocessing With AM Processes and Machines
For many 3D printing technologies, the first step in post-processing includes the removal of the support structures needed to hold up elements of the model to prevent sagging or warping as it is printed. It’s important to note that technologies that use photopolymers will also require rinsing before supports can be removed. This is not true of MJF or selective laser sintering (SLS) technologies.
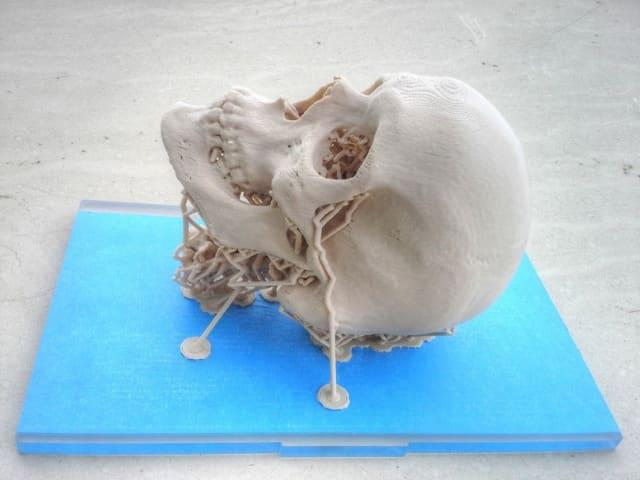
Specifically, support structures must be removed for fused filament fabrication (FFF), stereolithography (SLA), digital light processing (DLP) and metal powder bed fusion (PBF) technologies, such as selective laser melting. For plastics, this can be as simple as using a pair of pliers. For metals, this can be as intensive as CNC machining or wire EDM cutting.
Once these supports are removed, parts are usually sanded and polished, a process that varies depending on the material and the technology. This may include bead blasting, sanding, tumbling or vapor smoothing.
Components made by some technologies require specific post-processing elements in order to strengthen the part. For SLA and DLP, this means ultraviolet curing. For some metal parts, heat treatment may be required.
This brings us to SLS. This powder-based process requires separating the part(s) from the un-sintered powder using a de-powdering station in which compressed air blows the excess powder from the components. Bead blasting may then be used to clear off any remaining powder. A tumbler can then be used to polish the otherwise rough surface of the parts. Dying can bring color to SLS parts, while spray paint, lacquer or other coatings can be used to provide different finishes.
Postprocessing for HP Multi Jet Fusion Technology
MJF is a new technology that delivers certain advantages over legacy print processes, but there are still post-processing steps that are required before items can be considered finished. Worth noting, however, is that the HP Jet Fusion 3D Processing Station has the option of “Fast Cooling,” which allows prints to be cooled down more quickly so that they may be removed for more immediate processing. In addition, the latest HP Jet Fusion 5200 3D Printing Solutions include a Natural Cooling Unit designed for economical continuous printing.
Within the processing station for the Jet Fusion 4200 and 5200 systems, there is a vacuum used to remove powder. Once removed from the processing station, bead blasting, airblasting or waterblasting is performed to clear any remaining powder, not unlike SLS.
Bead Blasting: This process consists of shooting an abrasive media, usually a bead (size and type results in different surface finishes), at high pressure at a printed part with compressed air, knocking loose unfused powder while also smoothing the finish of the part. This can be done manually or automatically, with manual bead blasting relying on a foot pedal-driven system for propelling the beads as opposed to an automated tumbler, turntable or conveyer. Manual may be preferred for fragile parts.
Water Jet Blasting: This process features the jetting of water and air onto a part to remove powder and can include the use of a blast media for preliminary surface finishing. Typically more expensive than bead blasting, this process is ideal for complex geometries and cavities automatically while also reducing surface roughness without the need for additional post processing (such as a vibratory system). No dust is produced, as well.
Airblasting: Air blasting is necessary after bead blasting, but not water jetting, and some bead blasting machines have air blasting capabilities. After bead blasting, air blasting must be used to remove the remaining powder from the surface of the printed part using a closed cabin air pressure machine with a minimum air pressure of three bar.
Secondary Post-Processing
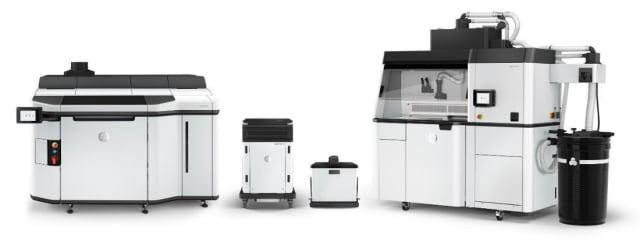
After the necessary post-processing steps described above, parts may need further finishing to bring the part up to technical requirements. This includes methods for reducing surface roughness, as well as methods for changing the color or finish of the part, like dying, electroplating and painting.
Sanding: Post-processing techniques can range from manual to almost entirely automated. For example, a company may want to smooth their Multi Jet Fusion parts; this could be done with manual sanding, though it would take a long time and be cost-prohibitive. However, it may work for one-off objects or visual prototypes.
Vibratory Tumbling: “Vibratory tumbling is another method that can be used to smooth Multi Jet Fusion parts that is hands-off and largely automated,” she added. “Though it can take several hours, because the process does not require supervision and can process many parts at once it is very cost-effective. You can buy vibratory tumblers of different sizes, according to your particular specifications such as quantity and part size.”
Vibratory finishing can be performed as a wet or dry process. In wet vibratory tumbling, ceramic and plastic media are used and create a more polished finish, with less wear on the part, but produces waste from the liquid-abrasive media. The dry process is cleaner and wastes less, but may be more aggressive.
Chemical polishing: This process uses a chemical to smooth the surface of printed parts without impacting its mechanical properties, resulting in a controllable level of glossiness from matt to gloss to shiny.
Dying: In addition, not unlike other processes, MJF parts can be subject to any number of finishes. Though there is an MJF line dedicated to full-color 3D printing (HP Jet Fusion 580/380 series), these systems are currently designed for smaller batches. When coloring parts that haven’t been printed on those machines, dying can be performed, either manually in pots of hot water or using automated dying equipment. The DY130 system from Girbau is the recommended automated dyeing solution for MFJ Parts.
Dyeing is the most common secondary post-processing technique of MJF users and may be best for parts that are visible or subject to wear, as the color penetrates the surface of the part. Dying white parts, rather than grey, offers a greater range of dying options. Manual dying, which usually involves leaving the part in an 80-100°C dye bath for about eight minutes, is comparatively inexpensive. Automated dying machines, however, may be more efficient, as they use specific programs for mixing the dye bath, as well as conditioning, dyeing, part rinsing, dye disposal, and cleaning.
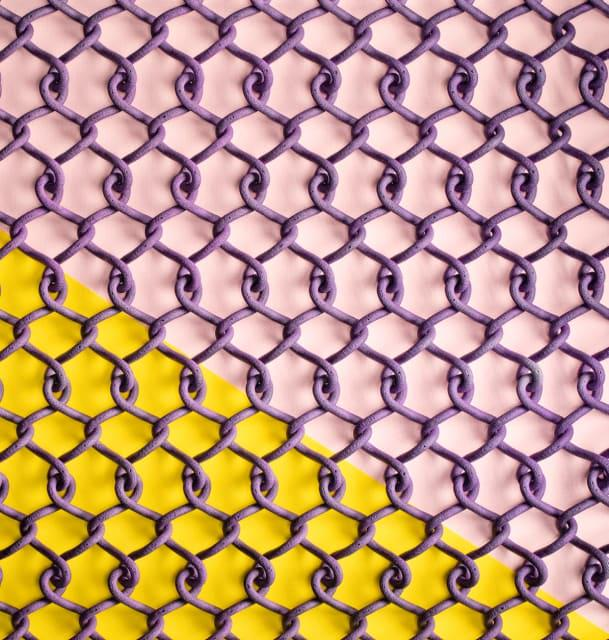
Painting and Electroplating: Painting and plating are other options for coating Multi Jet Fusion parts. Performing surface smoothing first will help achieve the best results with the least additional effort. Since every industry has its own paint specifications, the best bet is to have samples done with existing paint suppliers. Hydrographs are another method of coating. An image or pattern is floated on water, and the part is dipped in it to transfer the pattern over. Given that a layer of material is applied in the process, hydrographs also result in a smoother surface.
Electroplating consists of dissolving a metal in a solution and attaching the metal particles to the surface of the printed part using an electric current. Before this process can be performed on a polyamide part, the part must be made electrically conductive through the use of electroless plating, gas activation, or a conductive coating.
Graphite Blasting: Graphite blasting uses the same process as bead blasting but aims for giving parts a uniform, metallic appearance, with glass beads and graphite projected at the part. This can also reduce friction between moving parts, though it is not recommended for final parts that are handled frequently.
Making Post-Processing More Efficient
The time and cost involved in post-processing can vary depending on the finishing needs. While dyeing parts is quick and inexpensive, other finishing processes, such as plating, can be more costly and require added time. However, there are methods that can be used to reduce the amount of post-processing needed, such as adding texture into 3D models to mask layer lines.
It’s also worth noting that designs and post-processing techniques are not always immediately compatible. For instance, internal lattice structures may not be accessible to a paint gun and the finish may not uniformly cover a part.
For its part, HP is working on methods for improving the efficiency of post-processing MJF parts. This includes fully automating post-processing, to provide a complete end-to-end solution for manufacturing part producers.
Apart from post-processing improvements, MJF technology is evolving in other ways. HP appears to be providing regular releases for MJF and its Metal Jet process, which the company promises will upend both the world of manufacturing and the 3D printing industry. With that in mind, it’s possible that even more exciting 3D printing news from HP is just around the corner.