Dunmore is a leading provider of vacuum metallization services and contract metalization with over 40 years of experience.
The Vacuum Metallization Process
Vacuum metallization is a form of physical vapor deposition (PVD), a process of coating a metal such as aluminum or copper to a non-metallic substrate through evaporation. The most common metal used in vacuum metallization is aluminum, but other metals such as copper can be deposited on substrates.
Cacuum metallization is used add the following properties to materials:
- Optical and reflective properties
- Electrical conductivity properties
- Oxygen & moisture barrier properties
- Aesthetic Effects
The physical vapor deposition (PVD) of the metal takes place by feeding aluminum wire onto heated sources or “boats”, which operate at approximately 1500°C (2700°F). The vacuum metalization process takes place in a closed chamber under high vacuum, which allows the liquid metal to go from a condensed phase to a vapor phase. The aluminum vapor adheres to the surface of the substrate, producing a metal coating on a film or fabric. The vacuum deposited aluminum coating is uniform across the entire web of the substrate.
Vacuum Metalization for Aesthetics
Vacuum metalization is done for many reasons; aesthetically it adds a unique, eye catching appearance. Metallized substrates can have a highly reflective mirror like finish or be used in conjunction with other processes, like coating or laminating to create a decorative effect. Film that has undergone vacuum metalization can also be dyed and / or coated to give the substrate a unique color. Also, any vacuum metallized film can be laminated to a variety of other substrates such as leather, ABS, or polycarbonate to give the material a high-end metal appearance. Decorative applications that utilize substrates produced through the vacuum metallization process include:
- Label stock for a variety of applications
- Decorative surfacing film for appliances, point-of-purchase displays, & wallcovering.
- Personal care packaging
Vacuum Metallization for Insulation Applications
Vacuum metallization is widely used to increase the functionality of a film or fabric. Vacuum deposited aluminum film is an ideal material for insulation applications due to the optical reflectance properties achieved with film metallization. For instance commercial and residential radiant barrier insulation materials get their functionality from the vacuum metallization process. Passive thermal insulation systems that are used to protect spacecrafts for critical missions are constructed with multiple layers of polyimide films and other films that go through our film metallization process.
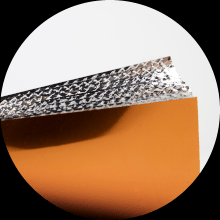
Vacuum Metalization Increases Barrier Properties
Another function derived from the vacuum metalization process is increased barrier properties. Metallization of a plastic substrates makes it an ideal material to achieve improved moisture and oxygen barrier properties. Applications include food & beverage packaging and medical applications. The film metallization process also decreases the substrates light transmission making it an effective light barrier, which is critical to limit the amount of UV exposure. Dunmore is capable of adjusting the amount of vacuum deposited aluminum on a substrate. This gives you greater flexibility in performance characteristics that are critical for your design. Some functional barrier and insulation applications include:
Metallization, Metalization, Metallision, or Metalisation?
In American English usage, both metallizion (with two “l”s) and metalization (with one “l”) are used interchangeabley; neither version is wrong or misspelled. Similarly, in British English, both metallision or metalision are used, though metallision (with two “l”s) seems more prevalent. Vacuum coating is another term that is synonymous with vacuum metalizing.
Source: https://www.dunmore.com/technical/vacuum-metallizing.html