The history of plastic is all about replacing other materials, beginning with ivory and tortoiseshell back in the late 19th century. Today, as LEDs increasingly supplant metal filaments in light bulbs, optical liquid silicone rubber (LSR)—in addition to plastics like polycarbonate and acrylic resins—is replacing glass in many optical applications including lens covers and light pipes.
Opting for LSR
Since Edison’s time, glass has seemed like the ideal shell for lightbulbs. It is almost perfectly transparent, inexpensive, has a defined manufacturing process, and is more or less impervious to the considerable heat generated as a wasteful byproduct of incandescent light. Heat loss, or wasted electricity, is the very reason incandescent bulbs are dying. And that same heat is why they have to be regularly replaced. LEDs on the other hand, while somewhat more expensive to produce at this time, more than make up for their initial cost with energy efficiency and long life. While glass could be used to enclose, cover, or direct them, optical LSR is a better choice in almost every way. Here’s why:
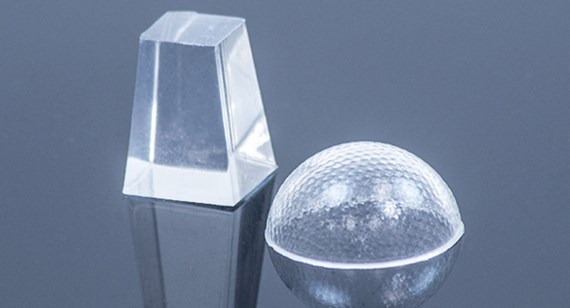
- Optical LSR is almost as transparent as the best glass across both visible and UV spectra.
- It does not discolor or lose transparency with age or with exposure to heat or UV.
- It is significantly lighter than glass and most other plastics.
- LSR is far more flexible than glass, reducing the chance of breakage. While flexible enough not to break, it is significantly stiffer than the LSR that is used in floppy bakeware. That material has a durometer (hardness) of 40 to 50, while optical LSR has a durometer of 70. (For comparison, the heel of a shoe typically has a durometer of about 80.) The stiffness of optical LSR is particularly valuable in applications like vehicle lenses where lights can be exposed to a variety of vibrations and blows.
- The material is also scratch and crack resistant, which helps preserve both its physical integrity and optical properties. You could cut a part made of optical LSR with a razor, but if you were to drag it across the ground or other rough surface it would most likely conform to the surface as it was dragged and not be marred.
- LSR is optically and mechanically stable at temperatures up to 302 degrees F (150 degrees C), which is important since LEDs do generate heat, though far less than an incandescent filament.
- Its wide operating temperature range, UV stability, and flexibility make LSR ideal for outdoor applications.
- Flexibility of the material also allows designers and engineers the opportunity to combine a lens with a seal to reduce assembly cost, inventory control and seams in the assembly.
- In its liquid state, optical LSR can be mixed with colorants or phosphors to extend its lighting capabilities (not available at FacFox, yet).
- LSR molding is an optimized process that uses less manufacturing space and energy than a glass manufacturing facility, which allows for prototype and low-volume production runs.
LSR Simplifies Design, Molding
In addition to its performance-enhancing characteristics, optical LSR has several positive traits that simplify design and molding.
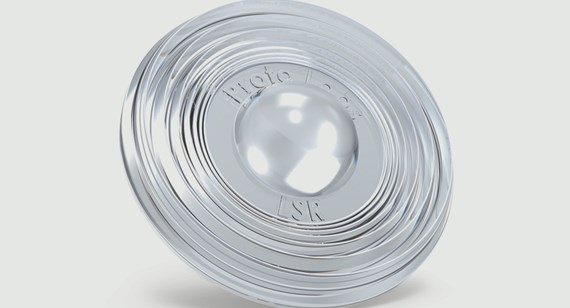
- Its low viscosity allows easy flow within a mold, so the material can move readily through thin areas and fill small voids. This gives the designer greater freedom when creating fine features for function or cosmetics. It allows molding of thinner walls than could normally be produced in other resins. Note: Low viscosity also increases the likelihood of flash where mold halves meet. Chances of flash can be reduced by designing parts that can have clean, flat parting lines.
- The material cools without creating significant sink or internal stresses, and its dimensional stability allows accurate production of lenses. Reduced likelihood of sink also permits designs with thicker walls than would be acceptable in other resins.
- The material can be molded within a polished mold without the use of secondary polishing processes required to polish individual parts, saving time and money in production. Some tooling can support optical surface geometry and finishes.
- Because of the material’s somewhat rubbery consistency, shapes with small undercuts and negative draft that would be unacceptable in a more rigid material may be able to be safely unmolded. These can be treated as bump-offs or pickouts.
To recap, optical LSR is a thermosetting material that is ideal for many optical applications. It is second in clarity only to glass. It can withstand heat in proximity to high-output LEDs and operate in a range of ambient temperatures. It is flexible enough for rough duty, outdoor, and automotive use. It allows for very flexible design including accurate replication of fine features. It can support minor undercuts and negative draft without the need for side-actions, and both thick and thin walls. Designs in this material can often integrate multiple parts into a single unit, combining for example a lens, a clear lens cover and a sealing gasket, reducing the bill of materials for a final assembly. FacFox stocks Dow Corning MS-1002 LSR, a material that has been engineered for molding finely detailed parts for LED applications.
FacFox is currently producing parts in optical LSR in low volumes for prototyping and in higher volumes of 10,000+ for market production. If you have questions about the material or its application, please contact one of our applications engineers at info@facfox.com.