Material choice for any product is a key factor in its success. That’s especially true in medical device development, where the device can be in contact with patients or implanted. While searching for the right material, I’ve had food-grade or FDA approved materials suggested as a possibility. They are not the same as biocompatible.
Materials have been under increasing scrutiny in recent years. Events like the Tylenol recall in 2010 (due to the leaching of chemicals from packaging) have heightened awareness. REACH (European Union Registration, Evaluation, Authorisation, and Restriction of Chemicals) has extended the original RoHS (Restriction on Hazardous Substances) program, with increasing numbers of chemicals making the list.
I’ll run through the essential requirements of food-grade material below to contrast those requirements against biocompatibility.
Extractables and Leachables
As in the Tylenol case, when materials come in contact with other materials, one material can leach compounds into the other. This interaction falls into two basic categories: extractables and leachables (E&L).
- Extractables are substances which can be pulled out of the target material under abnormal use conditions—e.g., solvents, more acidic or alkaline environments, or elevated temperatures.
- Leachables are transferred through normal conditions over the lifetime of the product, such as long-term storage.
The FDA requires E&L studies for some 510(k) submissions. Long-term use (more than 29 days), drugs, known toxicities, and blood contact are some areas where E&L testing is likely required. Testing for E&L is covered under ISO 10993-12 and 10993-18.
Food-Grade
What is food-grade? That’s a reasonably easy definition to provide—food-grade or “food contacting substances” (FCS) are those that can come into contact with food and do not cause any hazards or change the flavor, taste, etc. (FCS is defined in Section 409(h)(6) of the Federal Food, Drug, and Cosmetic Act). Food-grade and food-safe designations are similar to the difference between extractables and leachables. Food-safe means that a food-grade material is safe for its intended use. Food-grade may not be food-safe if boiling liquids are placed in it, or if it’s microwaved. These are examples where use may impact the material negatively. The FDA has an information page on these materials here.
Interestingly, the FDA recognizes it may be impossible to prove a substance is completely safe. If the material is not part of the GRAS list (Generally Recognized As Safe), there are a number of requirements to be met. To be considered food-safe, a report on the material’s toxicological, mutagenic (potential to effect permanent genetic changes), and carcinogenic properties must be submitted to the FDA. An important aspect of food-grade material approvals is exposure time. There are a few levels which are important, and depending on the exposure levels, short term genotoxicity tests like the Ames and mouse lymphoma assay (MLA) tests may be required. Or for higher exposure, full in vivo testing in lab animals may be required.
Additionally, the structure of the molecules in question can be analyzed and modeled for structure-activity relationships. In short, an analysis is required to determine if the material contains any structures or properties which can potentially damage DNA. These kinds of analysis are particularly valuable where the compound is untested or unknown.
To be fully FDA compliant, food-grade materials must be approved for the specific conditions they are operating in, as well as the materials they are in contact with—i.e., acidity, oil or fat contacting, etc. In addition, the material needs to withstand any cleaning processes used. These can have an effect on the ability of the material to leach into a material it comes in contact with.
Biocompatibility
If your medical device comes in contact with a patient, all of the above is insufficient. While there are a few similarities, biocompatibility is focused on risks and is a risk-based approach. The duration of contact, the type of contact (e.g., blood, mucosal membranes), and the category of contact (surface, externally communicating, or implanted) require an increasing level of risk mitigation, with the number and duration of tests increasing accordingly. The required tests are outlined in ISO 10993.
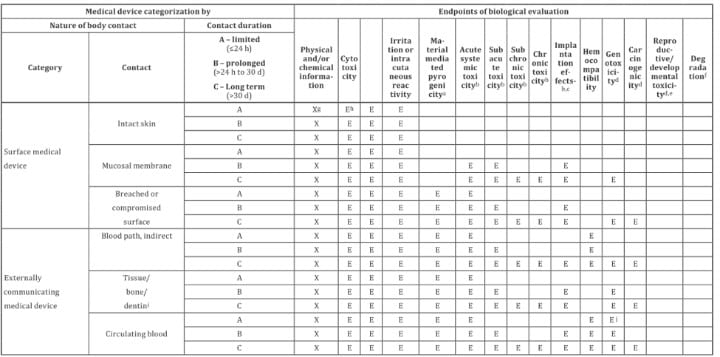
USP Materials
The US Pharmacopeial Convention (USP) designates materials with classifications ranging from Class I to Class VI. The tests involved with USP Class VI have some similarities and cross-over to ISO 10993. Simply using a Class VI material is not sufficient, as the USP classification outlines tests required, but does not include the risk management required of medical devices. For example, USP Class VI requires an intracutaneous irritation test, which is also required for ISO 10993 compliance. However, Class VI also requires subacute toxicity and implantation effects, which are not required for many categories of ISO 10993. It also misses required tests associated with other categories. While it is possible a USP Class VI material could also be ISO 10993 compliant, it’s not a given and USP Class VI alone is not sufficient for adherence to ISO 10993. That being said, if you can’t get an ISO 10993 compliant material (often because the material simply hasn’t been tested), using a USP Class VI material is a less risky option.
It’s possible that a material is food-grade, food-safe, USP Class VI, and ISO 10993 compliant. But just because something is food-safe in no way implies it is also biocompatible. Without going through ISO 10993 and determining use cases and risks, the material may not meet your needs.