Two broad categories of plastic materials exist: thermoplastics and thermosets, which are differentiated based on their behaviors in the presence of heat. This design tip offers a few considerations to keep in mind when using these materials.
One way to explain the difference between thermoplastic and thermosetting polymers, is to consider an omelet.
We start with an egg, a slice of cheese, and a warm pan. The egg begins as a liquid (a colloid, actually, but let’s not quibble) which, when dropped in a warm pan, becomes a solid. The cheese, on the other hand, begins as a solid, but when heated (but not overheated) becomes a viscous liquid.
After heating the egg you can cool it or reheat it but it will never return to its liquid state. It remains solid, just as thermoset polymers do. But if you cool the melted cheese it regains its solid form. Reheat it and it flows again, just like thermoplastics.
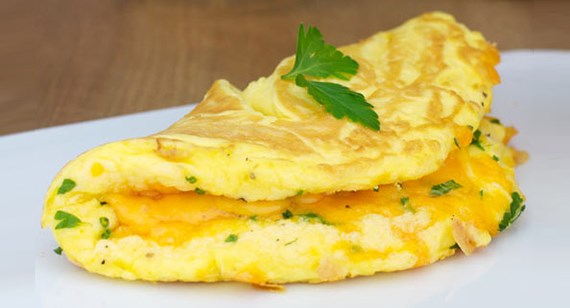
Guidelines for Using Thermoplastics
Keep in mind that even a well-designed part can fail if manufactured from the wrong material. Accordingly, carefully consider factors such as strength, impact resistance, performance at high temperatures, and other elements when selecting materials for injection molding.
In addition, make sure to review properties of common resin types, such as Acetal, Acrylic, high-density Polyethylene, polycarbonate (PC), polypropylene (PP), and polystyrene (see table). Consider that if a standard material doesn’t provide everything you need on its own, you may be able to find a blended resin that meets your needs. After all, the material is your part. For example, the table on this page shows, when polycarbonate and ABS are combined, the new material is stronger and is capable of forming a part more accurately than ABS alone.
RESIN TYPE | STRENGTH |
IMPACT RESISTANCE | DIMENSIONAL ACCURACY | CAPABILITY TO FILL SMALL FEATURES | PERFORMANCE AT HIGH MOLD TEMPS | COST |
---|---|---|---|---|---|---|
Acetal | Medium | Medium | Fair | Fair | Fair | Medium |
Acrylic | Medium | Low | Good | Fair | Good | Medium |
Acrylonitrile butadiene styrene (ABS) | Low to medium | High | Good | Fair | Good | Low |
High-density polyethylene (HDPE) | Low | High | Fair | Excellent | Good | Low |
Polycarbonate (PC) | Medium | High | Good | Fair | Good | Medium to High |
Polycarbonate/ABS alloy (PC/ABS) | Medium | High | Good to excellent | Fair | Good | Medium |
Polypropylene (PP) | Low | High | Fair | Excellent | Good | Low |
Polystyrene (PS) | Low to medium | Low | Good | Good | Good | Low |
Considerations for Thermosets
At FacFox, for thermosetting polymers, we offer a variety of liquid silicone rubber (LSR) materials.
LSR is a common thermoset and is a useful material because of its superior flexibility and heat and chemical resistance. Typical applications include soft-touch surfaces, gaskets, and heat insulation. Molders mix two components of uncured LSR to form a relatively low viscosity “liquid rubber” solution. The material cures in the presence of heat forming a bond that can’t be undone.
The following table shows our general workhorse LSR materials, plus special grades for fluorosilicone, medical, and optical uses.
TYPE | MATERIAL |
---|---|
LSR | Elastosil 3003/30 A/B, 3003/40 A/B, 3003/50 A/B, 3003/60 A/B, 3003/70 A/B, 3003/80 A/B |
LSR (Fluorosilicone) | Silastic FL 60-9201 |
LSR (Medical) | Dow Corning QP1-250 |
LSR (Optical) | Dow Corning MS-1002 |
When working with LSR materials, you’ll find a whole set of unique design and material challenges. To meet those challenges, here are several items to consider:
Wall and rib thickness. LSR typically fills thin wall sections with minimal challenges, and walls as thin as 0.010 inches are possible, depending on the size of the wall and the location of adjacent thicker sections. Rib thickness should be 0.5 to 1.0 times the adjoining wall thickness. LSR is accommodating to variations in wall thickness and sink is almost nonexistent.
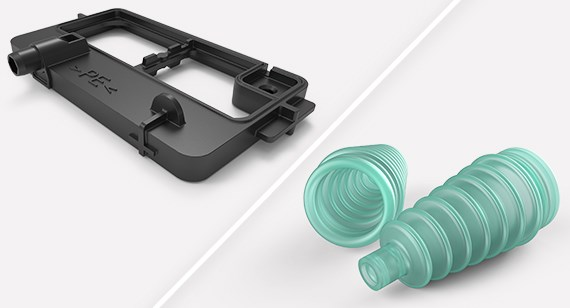
Shrink and flash. The shrink rate on LSR is fairly high with an expected tolerance of 0.025 inches per inch. LSR also tends to flash easily during molding (in gaps as small as 0.0002 inches), which we, at FacFox, help reduce by incorporating additional features into the mold design.
Parting lines. Simplifying and minimizing parting lines in your design will help you get cleaner LSR parts as quickly as possible.
Undercuts. LSR can be molded to accommodate parts with undercuts, which are manually removed by a press operator. Mechanical tooling actions to release undercuts are selectively offered at FacFox.
Part ejection. Ejector pins are normally not used during LSR molding due to the flexible and low-viscosity nature of the material. Therefore, parts should be designed so they can be retained on one-half of the mold when it’s opened at the end of the molding cycle. The part is then manually de-molded, often with air assistance.
Next, on thermosets, a word about cross-linking. Cross-linking determines many of the characteristics of thermosets. It makes them strong, dimensionally stable, and highly resistant to heat and chemicals (see illustration below).
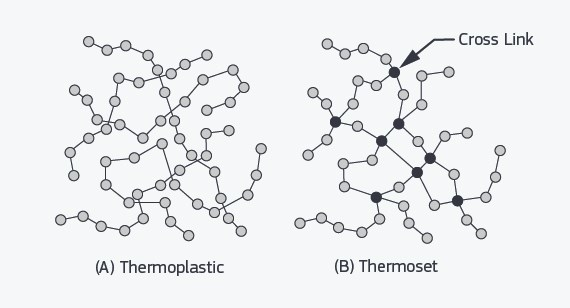
One familiar example is rubbery silicone bakeware. Cross-linking lets it easily withstands 400 degrees F oven temperatures and makes it inherently non-stick—very desirable characteristics for bakeware. However, thermosets have their liabilities as well. In harder forms, thermosetting plastics are not as impact resistant as thermoplastics and can tend to shatter.
Finally, every type of material has rules and guidelines.
Ultimately, we at FacFox cannot make resin choices for you, but we are always available to help you consider the characteristics of thermoplastics and thermosets. Just consult with one of our applications engineers at info@facfox.com.