In recent years, the market for 3D printing materials is growing rapidly with increasing demand, and more and more companies are buying printers and expanding the use of additive manufacturing technologies. In 2019, the size of the 3D printing materials market exceeded $ 1.5 billion. In the next five years, this market is expected to reach a sales volume of $ 4.5 billion. Driven by the growth of this giant market, the material suppliers, especially those chemical and metal material producers, are devoting a lot in the 3D printing industry.
In this article, we’d like to introduce the development of the industry’s material market in 2019, including the companies that are driving the market, and the trends which are shaping the future.
The polymer is the most commonly used 3D printing material
In terms of market share, polymers remain to be the leading 3D printing materials. From 2014 to 2018, 80.6% of global 3D printing materials revenue came from polymers, reaching $ 3.4 billion in 2018. Jabil’s survey of 308 3D printing users revealed that 74% of users were using or ever used polymer as 3D printing materials in 2018.
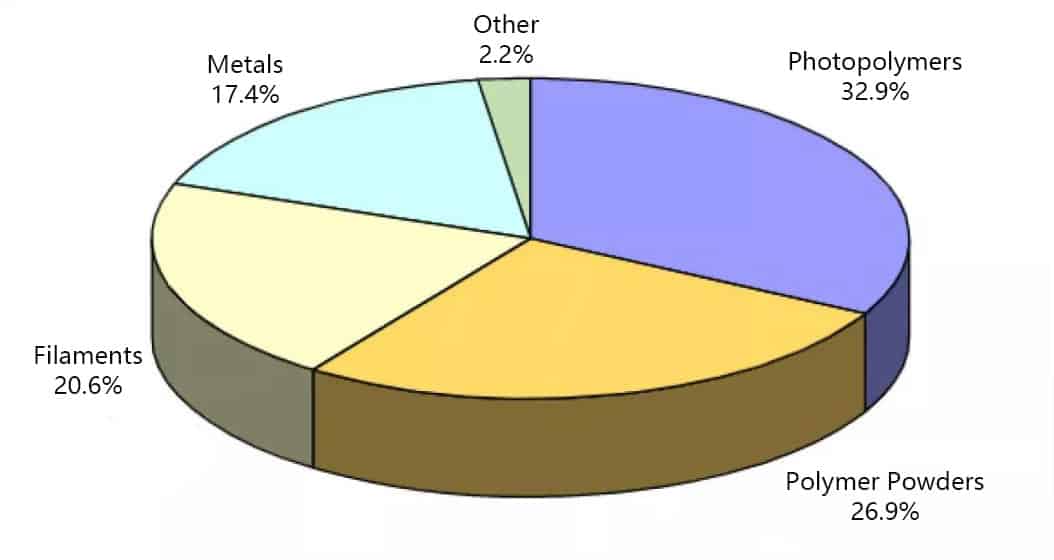
The high market share of the polymer can be explained by the easy installation and operation of the FDM or SLA printers which use polymers, furthermore, the polymer is really cost-effective among all the materials.
High-performance thermoplastics are being concerned
Although low-performance polymers such as photosensitive resins, PLA, and ABS dominate the market, the market demand for high-strength, functional materials that can withstand harsh environments such as high temperatures and corrosion is currently growing. The 3D printing industry is responding to this trend by developing high-performance thermoplastics such as carbon fiber reinforced composites, ULTEM, PEEK, and PEKK.
Not only can these materials be used to print functional prototypes, but they can also be used to directly manufacture end-use parts for a variety of industrial applications. Throughout the industry, chemical companies, such as BASF, Solvay, and Evonik, are increasingly developing these advanced materials, especially those used in additive manufacturing.
Many 3D printing equipment vendors are also working closely with material companies to accommodate the 3D printing hardware required for these materials. For example, Roboze, a well-known manufacturer of high-performance polymer 3D printers, has partnered with SABIC to develop an amorphous thermoplastic polyimide filament called EXTEM AMHH811F. This new material has a thermal deformation capability under 230 °C and excellent high-temperature resistance. Its glass-transition temperature is 247 °C, which is considered by partners to be the highest among all 3D printable materials. In addition, the material has excellent flame retardancy, good chemical resistance, and can maintain mechanical strength at high temperature.
The development of high-performance thermoplastics is critical to the industrialization of 3D printing, and they have accelerated the transition of the technology from prototype to advanced applications in key industries such as medical and aerospace.
At present, PEEK has begun to be applied to create customized implants. The progress and high growth potential in this area have prompted Evonik to invest in Shanghai Meditool, a Chinese startup that specializes in neurological manufacture of PEEK 3D printed implants for spinal surgery.
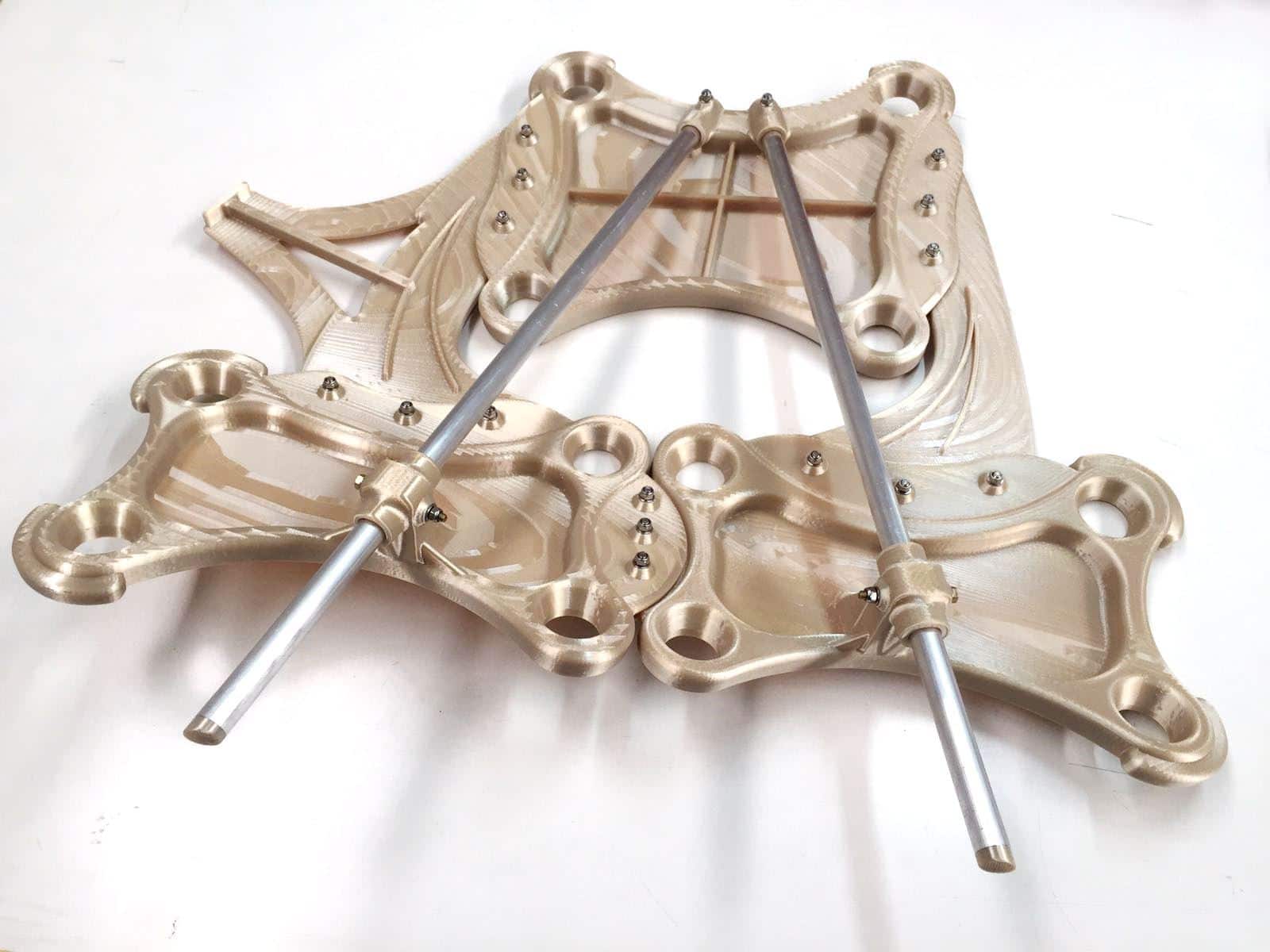
The rise of composite materials
Composite is another significant growth area for high-performance polymers. The composite material consists of a thermoplastic substrate and reinforcing fibers. Currently, the reinforcement materials used for 3D printing are carbon fiber, glass fiber or Kevlar fiber. These materials are available in powder, pellet or filament form, with chopped fiber reinforcement being the most common form of composite material, while continuous fiber reinforcement is also being explored. In November, Desktop Metal announced its latest Fiber 3D printer, which is able to reinforce nylon, PEEK and PEKK materials with continuous carbon fiber.
The SmarTech analysis report predicts that the global 3D printing composites market will grow at a compound annual growth rate of 22.3% in the next five years. The application of such materials in the medical, aerospace and consumer sectors (such as next-generation automotive, energy and transportation) becomes more and more important.
3D printed Boeing 777X large composite parts (20% carbon fiber reinforced ABS) In the past 12 months, the composite 3D printing market has been developing, and the types and applications of materials are rapidly increasing. Earlier this year, Continuous Composites partnered with Arkema. The former’s patented continuous fiber 3D printing technology will be combined with Arkema’s light-curing resin solutions to provide new options for continuous fiber composite 3D printing. Similarly, Sandvik created the world’s first diamond composite for 3D printing. This material has excellent hardness and thermal conductivity, as well as low density, corrosion resistance, and good thermal expansion, which is particularly beneficial for space applications.
Graphene is one of the strongest materials on the planet and has high electrical and thermal conductivity. Its applications cover a variety of industries including battery manufacturing to aerospace. In October, 3D printed wire maker Terrafilum partnered with graphene nanocomposite designer and manufacturer XG Sciences to develop graphene reinforced materials for extrusion 3D printing. In addition, researchers at Virginia Tech and Lawrence Livermore National Laboratory have been developing a novel method of using graphene to 3D print complex objects since 2016. Graphene is still a very challenging material for 3D printing, and it is expensive and difficult to produce. Therefore, 3D printing of advanced graphene materials is still in its infancy, but progress has been significant.
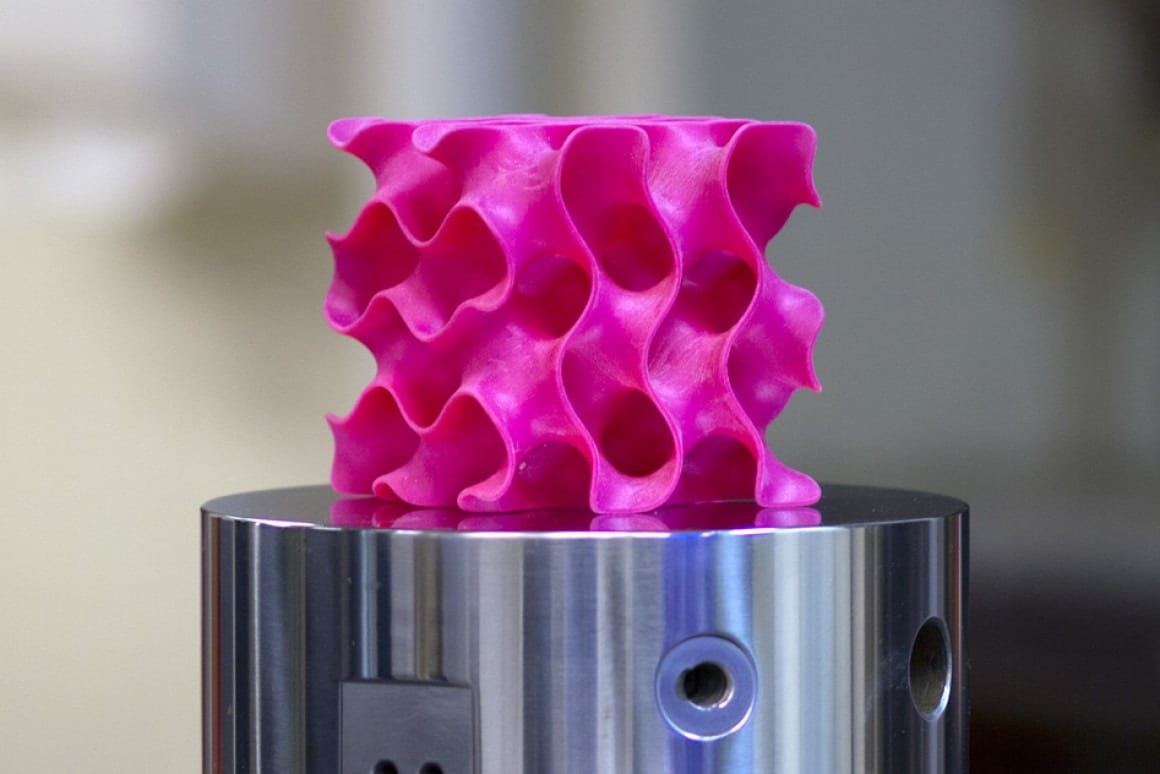
Elastic materials show explosive growth
More and more companies are applying 3D printing to consumer products, medical and industrial areas, which demand the materials to own flexibility, toughness, and flexibility. This demand is driving the growth of flexible materials markets such as TPU and silicone. In the past six months, multiple announcements have been made on 3D printed flexible materials.
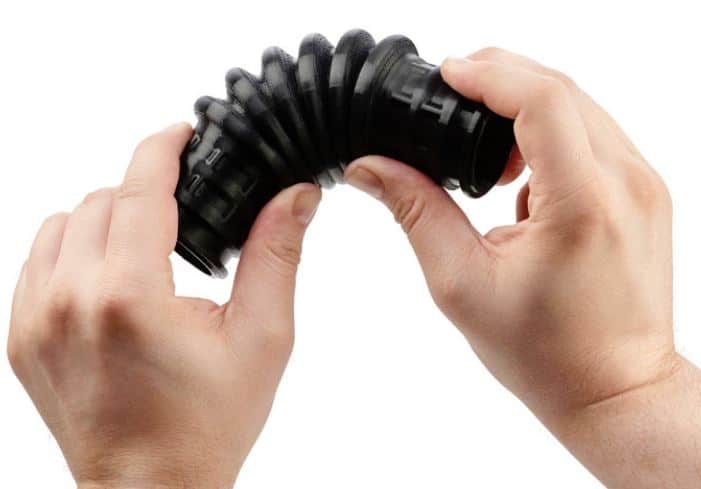
In July, the global chemical company Huntsman launched a line of flexible IROPRINT 3D printing materials for footwear applications. The materials can be produced in resin, powder, and filament, which can be used to produce footwear, hoses and washers, robot grippers, seals and other rubber-like applications.
In September, EOS launched a new flexible TPU 1301 powder, expanding its polymer material product line. The material has excellent elasticity and shock absorption after deformation, besides it has excellent process stability. It is especially suitable for the manufacture of protective equipment and soles in the sports field, and the manufacture of parts such as cushioning elements and protective gears in the automotive field.
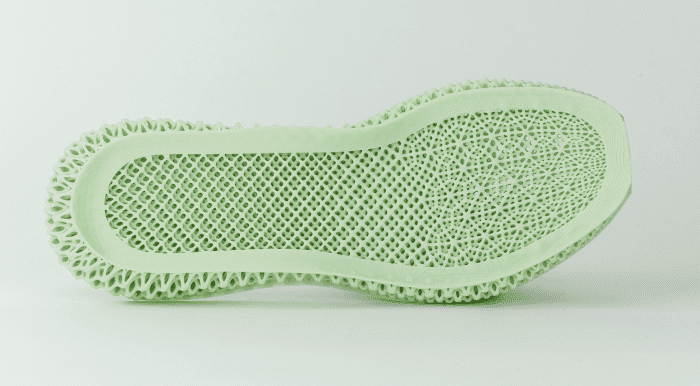
In October, the German chemical company Covestro developed a new application for its TPU material: 3D printed orthopedic insoles. Covestro’s TPU products cover a wide range of hardness and can be adjusted by changing the structure of the insole design. This means that manufacturers can print insoles with soft and hard contact areas for final customization.
In addition, Dow, the global leader in silicone elastomer science, has introduced two new 3D printing materials for liquid silicone rubber. The company has partnered with Nexus Elastomer Systems and Germany company RepRap to provide users with 3D printed color and functional silicone rubber parts.
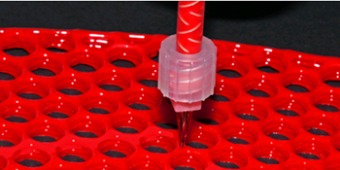
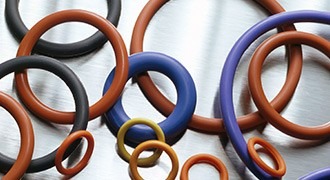
Obviously, the availability of flexible materials allows companies to expand new applications and benefit more from 3D printing.
Flame-retardant polymer
Materials with specific properties in the industry are gaining rapid development, and flame retardancy is one of them. This trend may be driven by demand from industries such as transportation and electronics that have stringent fire safety requirements, and these industries are beginning to make heavy use of 3D printing.
DSM Novamid AM1030 FR is a UL certified flame retardant material that can be molded by extrusion 3D printing and is suitable for the automotive and electronics industries. Similarly, Markforged has also released its own flame retardant material, Onyx FR, which is also a composite material (nylon-filled chopped carbon fiber), which is ideal for many key industrial applications.
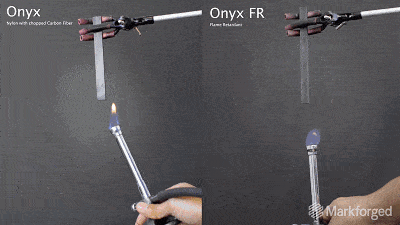
As companies develop more and more 3D printing applications, research on specialty polymer materials will continue to make impacts. Another high-growth area that will emerge in the future may be polymers with higher UV resistance, which will help to promote applications in the automotive field.