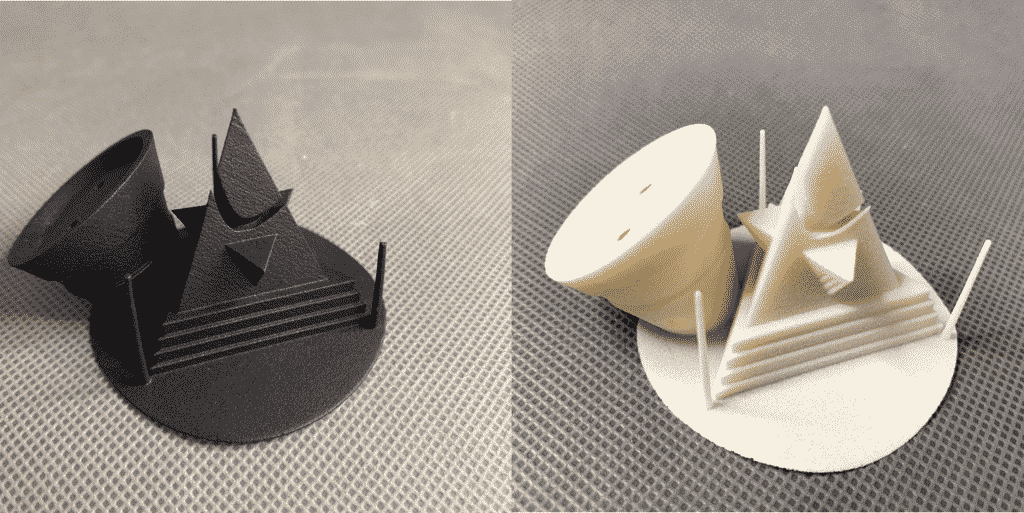
Laser Sintering (LS, aka Selective Laser Sintering and SLS) and Multi Jet Fusion (MJF) are both powder-bed fusion 3D printing technologies. Laser Sintering has been in market since 1992, and Multi Jet Fusion has come on the scene in recent years. Both technologies offer similar but unique value points to customers. The following offers a quick comparison of the two processes.
3D printing’s capabilities continue to evolve with the introduction of HP’s all-new technology, Multi Jet Fusion. This additive manufacturing process takes a unique approach to building parts from thermoplastic nylon powder, which results in faster build times, improved precision, and more consistent mechanical properties throughout the part.
If you’re thinking this process sounds similar to selective laser sintering(SLS), you’re smart. However there are some differences between the technologies that should be understood before making your choice.
What is SLS (Selective Laser Sintering)?
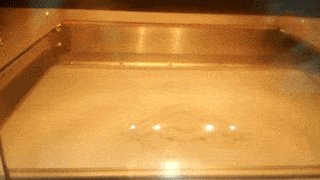
SLS (Selective Laser Sintering) creates geometrically complex plastic parts with powder-bed fusion technology. SLS builds with a CO₂ laser that melts cross-sections of a CAD design in powdered, typically nylon-based, material. While being built, LS parts remain encased in an unsintered powder bed replacing the need for support structures. Without support structures, designers can easily add undercuts and internal features and reduce post-processing time.
Laser Sintering is an ideal way to build prototypes or production parts in a wide variety of applications. LS production parts are strong, water and air-tight, heat resistant and repeatable. The process can build with filled Nylon materials, like carbon or glass-filled, making it an ideal process for applications such as duct work, fuel tanks and brackets.
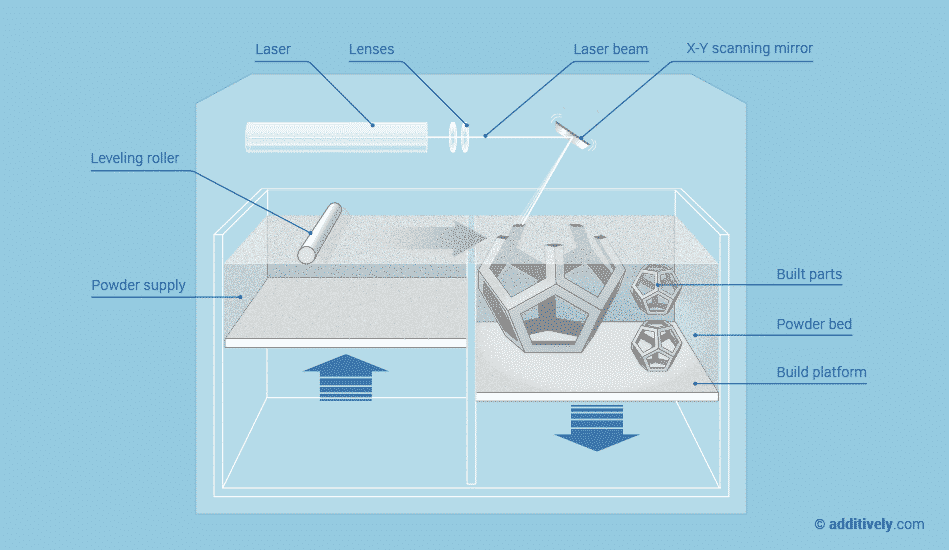
What is MJF (Multi Jet Fusion)?
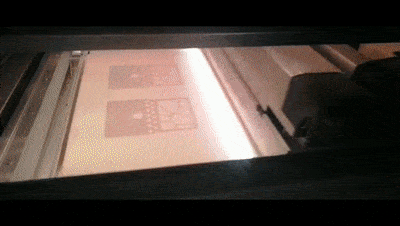
Multi Jet Fusion’s unique build style includes fusing and detailing agents within a powder-bed fusion process. MJF uses an inkjet array to selectively apply fusing and detailing agents across a bed of nylon powder, which are fused by heating elements into a solid. After a layer is built, a fresh layer of powder is distributed on top of the previous layer and the next phase continues until the part is complete.
Multi Jet Fusion is ideal for hidden parts like complex ductwork, connectors or non-cosmetic housings. The process produces parts with extremely fine details, exhibiting small intricacies in complex designs such as embossed text, small holes or living hinges.
When it comes to build, the core difference between Multi Jet Fusion and Laser Sintering is the heat source. LS uses as CO2 laser to sinter cross-sections, while MJF uses the fusing agent to promote the absorption of infrared light.
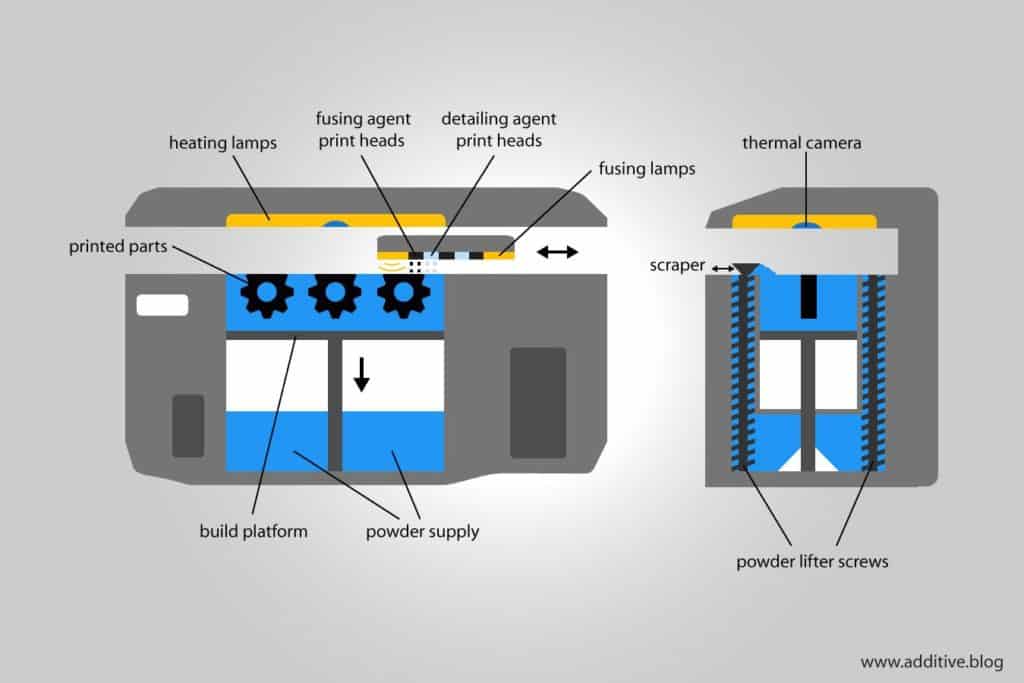
Side-by-side Comparison
MATERIAL PROPERTY | MULTI JET FUSION – PA 12 | SLS – PA 12 | SLS – PA 66 |
---|---|---|---|
Heat Deflection | 205-350°F
(95-175°C) |
186-350°F
(86-177°C) |
118-370°F
(48-188°C) |
Tensile Strength | 6960 psi
(48 MPa) |
6,962 psi
(48 MPa) |
6,050-6,946 psi
(42-48 MPa) |
Elongation at Break | 15-20% | 24% | 14-51% |
Color | Black | White | White |
Feature Resolution | 0.02 in(0.5mm) | 0.03 in(0.8mm) | 0.03 in(0.8mm) |
Dimensional Accuracy | ± 0.3% (with lower limit on ± 0.2 mm) | ± 0.3% (with lower limit on ± 0.2 mm) | ± 0.3% (with lower limit on ± 0.2 mm) |
Small Detail Accuracy | 0.025mm/mm | 0.1mm/mm | 0.1mm/mm |
Build Volume | 16 x 12 x 16 in | 30 x 20 x 20 in | 30 x 20 x 20 in |
High | Medium | Medium | |
Printing Speed & Quantity | High | Medium | Medium |
Add a Comment
You must be logged in to post a comment