The Markforged Metal X is a groundbreaking metal 3D printer that offers an affordable way to produce custom metal parts. Review the specs and use cases to learn more.
The Massachusetts-based 3D printing company Markforged began back in 2014 with the release of their first marquee product, a composite 3D printer called the Markforged Mark One. The company continued its successes with further composite machines and then with the announcement of the Markforged Metal X in January 2017 at CES. The Markforged Metal X comes in at $99,500, a low-cost entry point in comparison to the $500,000+ industrial DMLS/SLM machines.
Learn more about metal 3D printing: The Best Metal 3D Printers of 2022
The move into metal 3D printing was met with pushback in March 2018, when competitor Desktop Metal filed a lawsuit for allegedly copying portions of its patented metal 3D printing processes. The lawsuit would be concluded shortly after with Markforged being cleared of any IP infringement. By November 2018, Markforged had shipped out 100 Metal X 3D printers and post-processing stations to clients across the globe.
With a groundbreaking metal 3D printer and a boatload of financial backing propping them up, Markforged has garnered a lot of recognition on the industrial additive manufacturing stage. What makes the Markforged Metal X so unique? And how has it been used by some of the world’s leading companies? Review the specs to find out.
Technology and Workflow
The Markforged Metal X 3D printer is based on the company’s renowned composite 3D printing technology, but using metal powder instead of composite materials. This machine features a 300 x 220 x 180mm build volume and a 50-micron layer height. Essentially, the Metal X 3D prints metal powder that is bound in a plastic matrix, effectively eliminating risks associated with traditional metal 3D printing, while also reducing part weight and production costs.
The metal 3D printing process used in the Markforged Metal X, called Atomic Diffusion Additive Manufacturing (ADAM), involves the process of using a bound metal powder rod embedded inside a plastic filament. Similar to more common 3D printing technologies like FDM, the metal parts are built up layer by layer, but compensations are made during the design stage to account for part shrinkage.
One of the main benefits of ADAM technology is that it allows for closed-cell structures. Previously, traditional metal 3D printing technologies required the 3D model to have an escape hole for unused powder. This isn’t the case with the Markforged Metal X, however, as the powder burns away during the sintering process. This means designers can create complex enclosed internal structures to create light parts that don’t sacrifice on the part strength.
Once the part is finished on the Markforged Metal X, the so-called “green” part is then taken to two post-processing stations. Firstly the part goes through the Wash-1, a debinder that immerses the part in a specialized fluid to remove the primary binding material. This process leaves the material semi-porous so the remaining binder can be burnt away easily in the next step.
The final stage uses the Sinter-1, a high power furnace which sinters the part burning away any, fusing it into a solid metal part. This final stage makes the part around 99 percent dense which is on par with high-end DMLS machines on the market. To provide more expansive sintering capabilities, Markforged recently released the Sinter-2, a larger-sized furnace for medium volume batch production and large-scale parts. Compared to the Sinter-1, which offers a 4,760 cubic cm of active hot zone, the Sinter-2 has a much larger active hot zone of 19,644 cubic cm.
Both the Wash-1 and Sinter-1 together weigh 274 kg (600 lbs), taking up 1067 x 505 x 720 mm (42 x 20 x 28 in) and 609 x 685 x 1067 mm (24 x 27 x 42 in) respectively. Although the dimensions and weight of the setup is certainly hefty, this still represents a huge reduction in size, cost and weight compared to current post-processing methods employed by other industrial metal 3D printing processes.
There will always be a need for some sort of post-processing with industrial 3D printing technologies. By providing control over the entire process, from CAD to finished part, Markforged can offer quality guarantees that other systems fail to provide. The primary competitor in the space is the Desktop Metal Studio System, which employs a three-step process that is similar to ADAM technology. According to Markforged, the main difference between the two processes is that ADAM utilizes crystal growth throughout all axes, giving parts the mechanical properties of solid metal in all directions.
There are many advantages to metal 3D printing, one of which is the ability to create one-off parts with highly complex geometries. The Markforged Metal X provides to those benefits in a more affordable way with less of the overhead that often burdens large-scale industrial machinery. Although the metal 3D printing process has not really been shortened and still requires extensive post-processing, the Markforged Metal X proves to be a good entry point for businesses and manufacturers to begin 3D printing end-use metal parts.
Priced at under $100,000, the Markforged Metal X may sound like an extraordinarily expensive machine, but the cost is a fraction of what other metal 3D printing systems cost. In order to get an accurate quote for the Metal X system or receive a demo, you’ll have to contact the manufacturer directly (or request a quote by clicking on the button below).
Materials and Software
The first material launched with the machine was 17-4 PH stainless steel, an all-purpose metal that combines high strength, corrosion resistance, and hardness. This metal material is commonly used in the aerospace, medical and chemical industries due to these properties, and is perfect for manufacturing tooling and assembly fixtures.
Other materials released for the Markforged Metal X include:
- D2 Tool Steel – High-compression, wear-resistant properties, ideal for cold-working applications
- A2 Tool Steel – General purpose tool steel for cold-working applications
- H13 Tool Steel – High-temperature and high-wear resistance
- Inconel (IN) 625 –Nickel-chromium-based superalloy that is highly resistant to corrosion and high temperatures.
The company is also currently piloting an impressive array of Beta materials, such as Titanium Ti6Al4V, 316L Stainless Steel, and Copper.
The Metal X comes with Markforged proprietary cloud-based software Eiger. This software allows for real-time fleet management, meaning that if you have several Metal X 3D printers churning out parts you can see the status of all machines and manage production more efficiently.
The machine itself has a touchscreen interface and utilizes the Eiger software to track the materials being used to optimize print settings accordingly. Eiger can also work within most browsers allowing you to easily import CAD drawings without the need of cumbersome software. Within the software, the functionality includes the ability to optimize the printing process for specific pressure points to create the strongest possible part.
Use Cases
While many Markforged customers have kept their of the Metal X under wraps, at least for the time being, there are a number of use cases out there that showcase how this metal 3D printer is being used for various applications.
SHUKLA MEDICAL
The surgical tool manufacturer Shukla Medical, a subsidiary of aerospace manufacturer S.S. White Technologies, has been utilizing the Markforged Metal X to fabricate functional prototypes of surgical instruments. After finding success with Markforged’s continuous carbon-fiber technology, engineers from Shukla Medical decided to integrate the Markforged Metal X into their prototyping workflow.
Using 17-4PH Stainless Steel material, Shukla Medical has been 3D printing metal prototypes of surgical tools for orthopedic surgeons. These functional prototypes allow the tool manufacturer to verify and validate parts before moving onto production, and also gives surgeons that ability practice using 3D printed part. These prototypes have both the look and feel of the final product, providing much more functionality than the prototypes that surgeons are used to testing.
According to Shukla Medical, replacing CNC machining with the Markforged Metal X has helped the company save hundreds of thousands of dollars per year.
“3D printing the prototype product helps our surgeons test the part in their hands before going into the operating room, so they already have the experience and confidence in the tool,” says Zack Sweitzer, Product Development Manager at Shukla Medical.
NIEKA SYSTEMS
Looking to produce crucible clips to place over gas burners, Nieka Systems initially worked with a 3D printing service provider that utilized Direct Metal Laser Sintering (DMLS) to produce clips from Inconel 625. While outsourcing the production of this part was more affordable than CNC machining, the cost started to build up and lead times were difficult to pinpoint.
Worried that they wouldn’t be able to keep up with product demand, the founder of Nieka Systems, Louis Croisetière, decided to bring production in-house with the Markforged Metal X system, as well as two composite 3D printers. After adapting the crucible clip design, the company used the Metal X 3D printer and Inconel 625 material to manufacture the part. These 3D printed clips passed internal testing and can now be found in production units across the globe.
“The Metal X system allows us to make parts faster, reduce lead time, know exactly when we can deliver, go further with the design. And cost-wise, it was very much a no-brainer,” said Croisetière.
DIXON VALVE
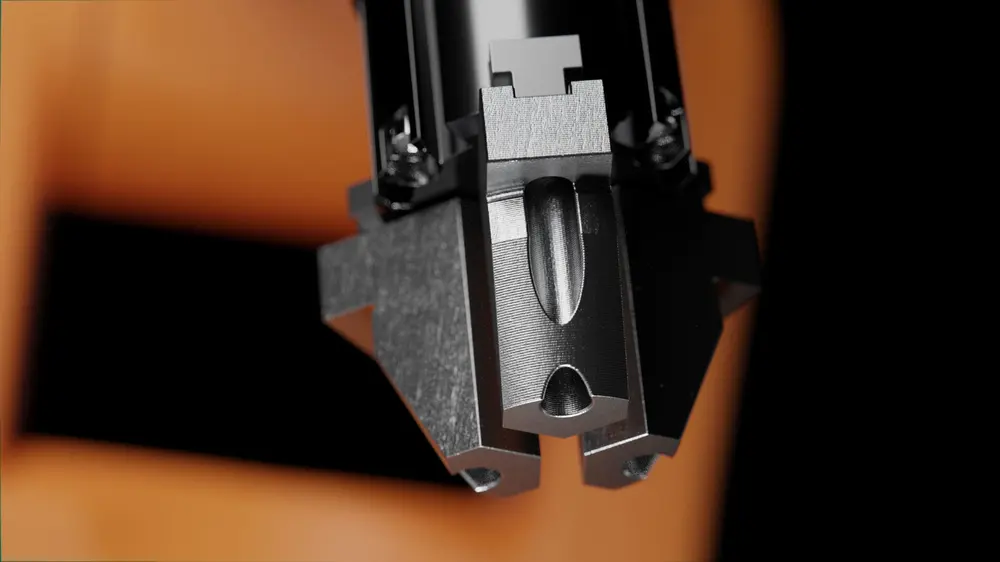
Dixon Valve, a manufacturer and supplier of hose fittings and accessories, is another customer of Markforged that has increased production speed and reduced overall costs by utilizing the Metal X 3D printer. Using Markforged composite 3D printers to produce End of Arm Tooling (EOAT) for robotic arms, Dixon Valve found that the threads of the grippers, which are designed to hold fittings, would quickly wear out 3D printed composite parts.
And so, the company integrated the Markforged Metal X into the production workflow and used it to manufacture specialized gripper jaws. These 3D printed metal jaws were hard enough to prevent thread abrasion while also conforming to the shape of the fixture. By making this switch and 3D printing the jaws with the Metal X, Dixon Valve reportedly achieved 30x cost-savings and 10x time savings.
Markforged Metal X Tech Specs
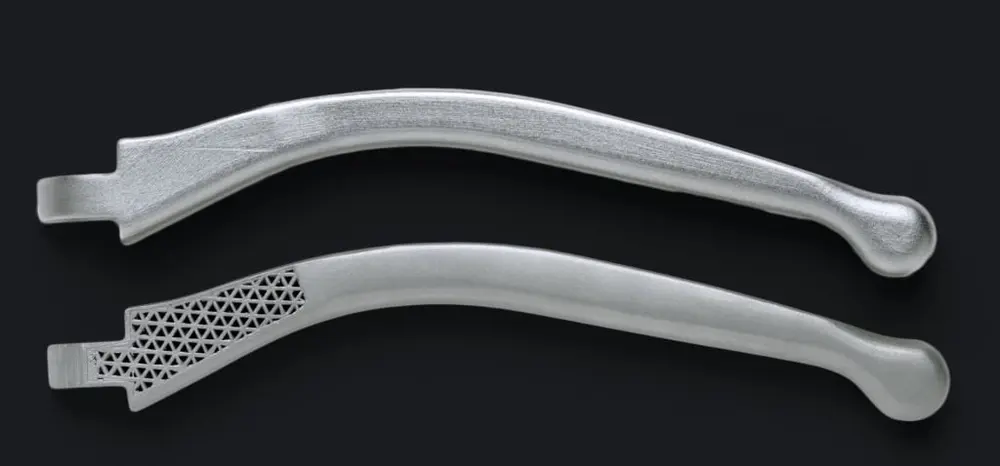
These are the current technical specifications of the Markforged Metal X:
- Print Engine: Atomic Diffusion Additive Manufacturing (ADAM)
- Build Volume: 300 x 220 x 180 mm (11.8 x 8.7 x 7.1 in)
- Machine size: 575 x 467 x 1120 mm (22.7 x 18.4 x 44.1 in)
- Print Chamber: Heated
- Print Bed: Heated, Vacuum-Sealed Print Sheet, Auto Bed Leveling
- Print System: 2 Nozzles – Metal Material and Support Release
- Max Part Size: 250 x 183 x 150 mm (9.8 x 7.2 x 5.9 in)
- Max Part Weight: 10kg
- Resolution: 50 micron – 200 micron
- Connectivity: Ethernet or Wi-Fi
- Weight: 75kg (160lbs)
- Power Requirements: 100-240VAC, 2400W (20A peak), IEC60320 Type C2
- Materials: 17-4 PH Stainless Steel, Tool Steel (H13, A2, D2) Titanium Ti6Al4V, Inconel (IN) 625, Copper, Aluminum (6061, 7075)
- Supports: Ceramic release layer
- Print Preparation: Eiger Software
- File type: STL
Where to Buy
If you want more information, samples, or to request a quote for the Markforged Metal X, you can either go to their website or just click the link below.