A promising Italian start-up sets out to change minds about metal 3D printing for industry by focusing on design and a printer from Desktop Metal.
A3D printed metal part can come to the rescue when a business-critical specialty component has to be replaced as soon as possible, but that has never really been the point of the technology, argues Marco Preziosa, CEO at Additive Italia, an engineering company outside of Milan focused on additive manufacturing (AM) for metals.
“What people don’t understand about 3D printing metal is that it’s not just about the metal, it’s about the design,” he says. “It’s not just different machinery to do the same old thing with some fancy features. You have to scrap all of your previous knowledge and start thinking about how you can engineer more value into your part with additive manufacturing.”
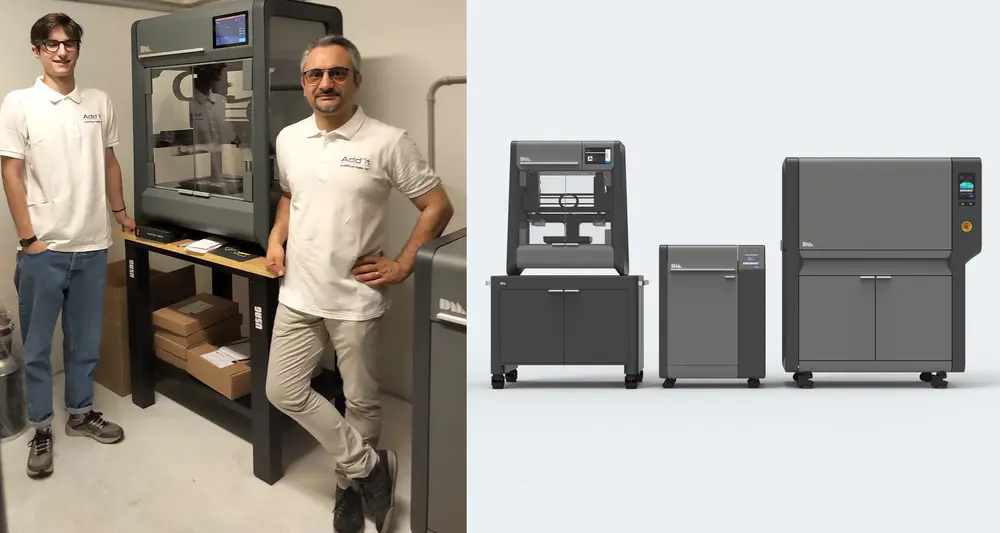
This mission of Preziosa’s start-up—to evangelize the benefits of metal 3D printing for manufacturing beyond spare parts—of course, isn’t unique. Leaders in additive manufacturing, from Siemens to HP to EOS, have been working for years (decades even) to educate and further the adoption of technology to industrialize 3D metal printing through innovations in part design. So what’s different now?
Moving 3D Metal to Manufacturing
Metal AM is still a small niche within the broader industrial 3D printing movement despite major global companies, such as Airbus, BMW, and Ford, investing millions in their own printer facilities.
“At the moment, we are still getting people convinced that if they want to get value out of AM, they need to rethink their entire industrial process starting with the invention of the part,” says Preziosa. “It’s a reassessment of the function of the part, then a reengineering of the part, then metal additive manufacturing is just the final step.”
Take, for example, the olive harvester, which is a long-handled, vibrating tong used to shake olives and other fruits from their branches. Additive Italia was tasked with not just printing new metal grippers for this tool, but reimagining them. Using software to analyze the part’s features, functions, and stress points, the resulting design (pictured below) used less than half the stainless steel of the original casted part.
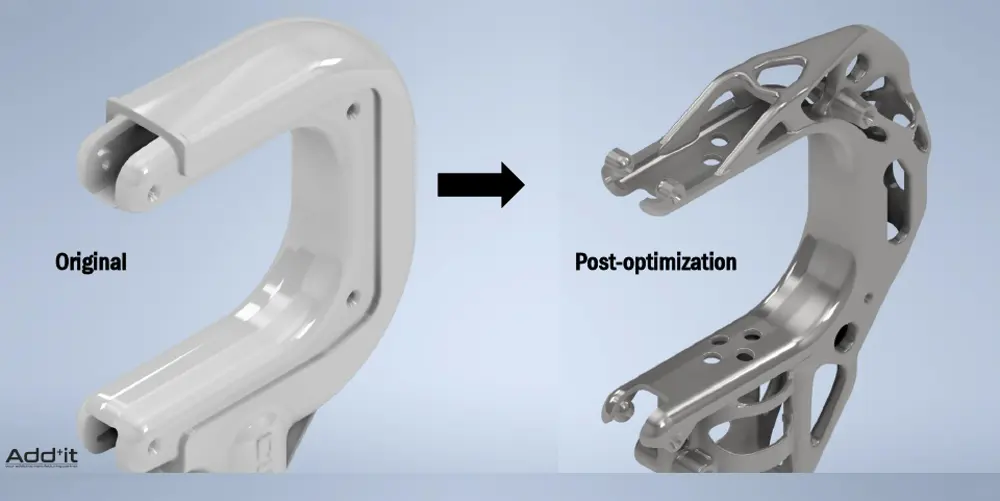
Getting the Word Out About 3D Printed Metal
Although more large companies are getting onboard, AM adoption is far lower among small and midsize businesses. This is for a number of reasons, but primarily the fact that manufacturing, in general, is slow to evolve, says Preziosa.
Local manufacturers with plants running 24/7 tend to focus more on incremental advancements that promise efficiencies, not disruptive ideas. This limits the appeal of Additive Italia’s approach, for the moment. But Preziosa is confident that the promised industrialization of metal 3D printing could be (finally) on the cusp of wider adoption because of two developments: new lower-cost metal 3D printers and a heightened desire—prompted by the pandemic—of manufacturers to shorten the supply chain.
And then there’s the aspect that all manufacturers value, reliability.
“Getting additive manufacturing into industry needs to be, most of all, about the reliability of the process,” says Preziosa. “It has to prove that it is at least as reliable as the traditional methods since no one wants to put their reputation at stake to adopt a new technology.” Proving reliability takes time.
Is Metal 3D Printing Mature?
Compared to machining, metal AM is still relatively new, and many of the most innovative companies developing the technology are less than a decade old. So when it came time to choose a printer partner that fit Additive Italia’s mission, Preziosa chose the Massachusetts-based venture-backed unicorn Desktop Metal.
Desktop Metal aims to bring metal 3D printing to small and midsize manufacturers by providing technology that is reliable and affordable, overcoming what it says are the two major barriers to adoption. The company’s design software – the backbone of its metal 3D printing ecosystem – was recognized by Fast Company magazine as one of the World-Changing Ideas for 2020.
Additive Italia owns a Digital Metal Studio System, which is one of the only desktop-size metal 3D printers on the market and comes with a debinder unit and a furnace. Designed more for prototypes than final metal parts, the Studio System enables Preziosa to demonstrate the potential of metal 3D printing for his customers, who, at the moment, are mostly interested in prototyping, which is the seed for industrial adoption, he says.
“You need to get your customer involved in the learning process and go with them on the journey from the concept all the way to the final samples if you want to industrialize metal AM,” he says. Eventually, Preziosa hopes his clients purchase their own metal 3D printers, but he isn’t worried about losing customers.
“I’m confident that even after we’re successful in helping companies transition to using AM, they will still need someone who is on the edge of the technology providing new possibilities and new knowledge,” he says. “This technology is moving fast.”
Source: 3D Printed Metal, It’s Not About Spare Parts | All3DP Pro