Our liquid silicone rubber molding process produces custom prototypes and end-use production parts in 15 days or less. We use aluminum molds that offer cost-efficient tooling and accelerated manufacturing cycles, and stock various grades and durometers of LSR materials.
How Does Liquid Silicone Rubber Molding Work?
LSR molding differs slightly from thermoplastic injection molding due to its flexibility. Like a standard aluminum tool, an LSR molding tool is fabricated using CNC machining to create a high-temperature tool built to withstand the LSR molding process. After milling, the tool is polished by hand to customer specifications, which allows six standard surface finish options.
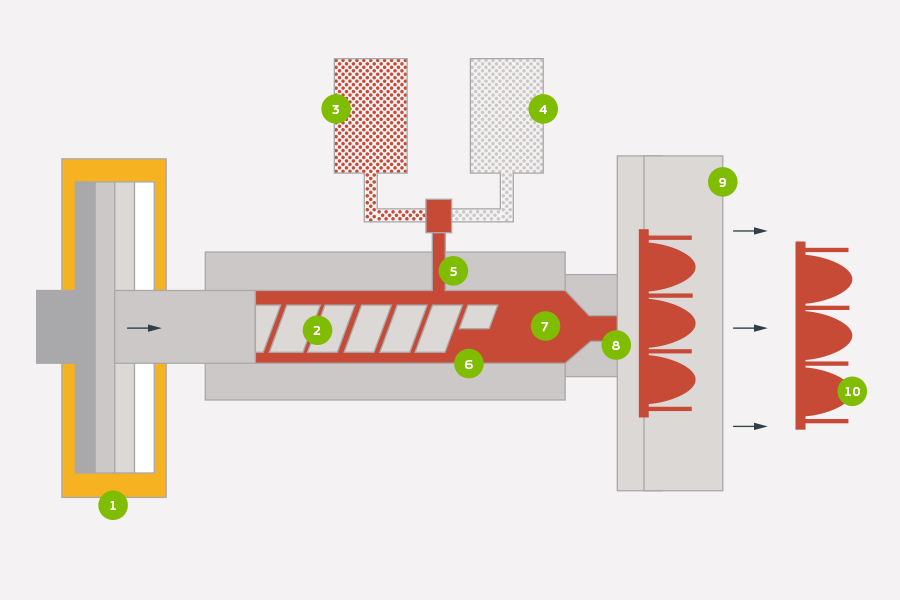
From there, the finished tool is loaded into an advanced LSR-specific injection molding press that is precision geared for accurate control of shot size to produce the most consistent LSR parts. At Protolabs, LSR parts are manually removed from the mold, as injector pins can impact part quality. LSR materials include standard silicones and specific grades to fit various part applications and industries like medical, automotive, and lighting. Since LSR is a thermosetting polymer, its molded state is permanent—once it is set, it can’t be melted again like a thermoplastic. When the run is complete, parts (or the initial sample run) are boxed and shipped shortly thereafter.
Common Applications
- low-volume production
- bridge tooling
- pilot runs
- functional prototyping
Designing Silicone Rubber Parts
Click in and learn how to design parts for the liquid silicone rubber molding process, including maximum feature thickness, surface finish options, and more.