For many of us, the easiest place to find liquid silicone rubber (LSR) is at the auto store. It comes in a tube and can be used to create flexible, formed-in-place gaskets that cure with the heat of an operating engine. In its extreme form, LSR can withstand constant temperatures of up to 600°F (316°C) and intermittent temperatures of 700°F (371°C). To those more familiar with ordinary thermoplastics, it may seem counterintuitive that such a rubbery material can be used in high-temperature applications, but LSR is actually made to take the heat.
Unlike thermoplastics, which soften when heated, thermosets like LSR are created in high heat and, in their various forms, can easily withstand temperatures that would melt thermoplastics. This suits them well for a variety of high-heat automotive and industrial applications and for medical products that are sterilized with high heat.
In addition to high heat, LSR can typically handle low temperatures, well into double digits below 0°F, while maintaining its flexibility. The exact degree of flexibility varies with the compound, but can be very high; LR3003/50, for example, has an elongation at break of 480 percent. LSR compounds are available in varying durometer (hardness) and can be selected to match the requirements of the application.
The material has excellent thermal, electrical, and chemical resistance properties, although it can be attacked by certain solvents such as gasoline or mineral spirits, which is why it can be used in high-temperature automotive applications but not for fuel lines. And it has low compression set—low permanent deformation when a force is applied and removed—making it ideal for elastomers. In comparing LSR to thermoplastic elastomers (TPEs) like Santoprene, LSR has been described as “TPE on steroids.”
LSR is also approved for medical applications where it will be in contact with skin. Its stability prevents it from affecting skin or, in turn, being affected by skin contact. Some grades of LSR, when combined with the appropriate manufacturing environment can be used in implantable applications. Its hydrophobic (water-repellent) properties make it ideal for water-handling applications. And the fact that it is fire-retardant and does not emit toxins or halogens when burned suits it well for a variety of safety applications. Reviewing material specifications or consulting your molder for more details is generally recommended.
Thermoplastics vs. Thermosets
In some aspects of the way they are molded, thermoplastics—polyethylene, polypropylene, polycarbonate and ABS, among others—and thermosets like LSR are opposites. Thermoplastics start out solid at room temperature, soften when heated, and re-solidify when cooled, which makes them excellent candidates for recycling. Thermosets, on the contrary, typically start out as gels and solidify permanently when heated with a platinum catalyst. That makes them poor candidates for recycling but accounts for their superior performance at high temperatures.
These differences in their response to heat define their respective molding processes. Thermoplastic pellets are heated before injection to liquefy the resin and then allowed to cool in the mold before being ejected. Thermosetting resin, on the other hand, is chilled before injection and then heated in the mold for curing.
Shear Thinning
Before curing, liquid silicone rubber is a shear thinning fluid, also called a pseudoplastic. Shear thinning is the reduction of a fluid’s viscosity when shear stress (like that caused by injection into a mold) is applied, and it significantly impacts the way LSR behaves in the mold. To understand the behavior of a pseudoplastic material, consider ketchup, which, like LSR, is a sheer thinning fluid, as compared to honey, which is not.
Think about what happens when you tip a bottle of ketchup. Then picture tipping that little plastic bear full of honey. At room temperature the honey will flow, albeit slowly; the ketchup probably won’t because the ketchup is more viscous. That’s why you end up shaking the ketchup bottle or fishing down the neck with a table knife. Now imagine the ketchup in a squeeze bottle, and squeeze that and the plastic honey dispenser side by side. The honey is difficult to dispense while the ketchup flows freely, taking mere seconds to cover your burger or fries. This change in viscosity is an example of shear thinning, and the same thing happens to LSR when it is injected into a mold. Shear thinning has both positive and negative effects on the molding of LSR. It actually improves flow through thin-walled areas, reducing the need to maintain uniform wall thickness throughout a part as is recommended when molding thermoplastics. On the other hand, because LSR flows so easily in a mold, it has an increased tendency to flash — to seep into spaces where mold halves meet — creating unwanted vestiges that must be removed by secondary operations (see Figure 3). Flash can be prevented or at least minimized through careful mold design but is still a factor in part design.
Parts molded of LSR will continue to shrink after being removed from the mold as they cool. This is partly due to the typically higher mold temperature. For this reason, they do not cling to cores as thermoplastics do; instead they tend to stick to the mold half with the greatest surface area. Because of the material’s flexibility, different parts of a finished piece may stick to each mold half leaving the part hanging after the mold opens. Preventing this problem may require some redesign of the part.
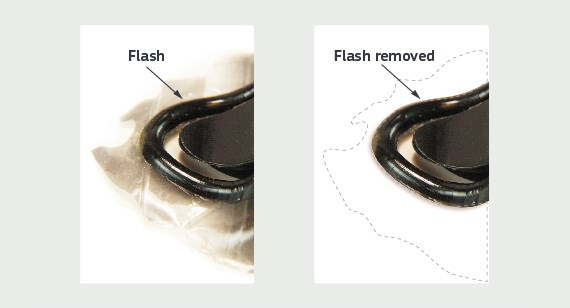
Design Considerations for LSR Parts
From the part designer’s standpoint, design guidelines for LSR are similar to those for thermoplastic though somewhat more relaxed in certain areas. The reason for the relaxation is that LSR, being flexible, is a more forgiving material than thermoplastics. Planes that are parallel to the direction of mold opening typically require some draft to allow milling of the mold, though not to prevent scraping of the part against the mold wall during ejection. About one degree per inch of mold depth is usually sufficient.
Because shear-thinning LSR flows easily in the mold, it can traverse thin walls that would cause fill problems for thermoplastics. For the same reason, uniform wall thickness is not as critical. And because thermoset material is solidified by heat and is mostly cured before it cools, sink is not a problem, which means that part features can be made thicker than with typical thermoplastic material (although there are still good reasons not to make features thicker than they need to be). But the biggest difference between thermoplastic and thermoset LSR mold design may be in the handling of undercuts.
Rigid thermoplastics can be molded with undercuts either by the use of side-actions that produce the undercut features and then withdraw before the mold opens to allow the part to be ejected, or by complicated techniques like pickouts. But because LSR is so flexible, finished parts can often be “peeled” out of the mold. This means that features that, molded in thermoplastic, would be trapped behind an undercut to be pulled around the projection. The only real constraint on undercuts in LSR is whether they can be milled.
LSR Molding at FacFox
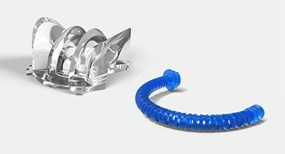
The process for submitting a design for production in LSR is similar to that for thermoplastics.
- Upload the design.
- Specify the material and quantity.
- Get a firm quote with design analysis and pricing information, typically within hours.
Current turnaround time for LSR production is three weeks. For some designs, faster turnaround may be available with an expedite fee. This is far faster than is possible using traditional methods because the Protomold process turns 3D CAD models directly into toolpaths for milling molds. As with thermoplastics, the process for making LSR molds at FacFox is managed using proprietary software running on a very large compute cluster. The toolpaths generated by the software run automatic milling machines that produce the mold halves, which are then placed into specialized liquid silicone molding presses.
The process can cost-effectively produce LSR parts in quantities from 25 to 5,000+. In moderate production quantities, the process can turn out parts faster and less expensively than traditional LSR molding processes, but even at very small production or prototyping volumes, FacFox still uses full-scale manufacturing processes. This is significantly different from other LSR prototyping operations.
Most producers of low-volume LSR prototypes hand mix the component gels in a blender, a process that cannot match the process control of FacFox’ industrial process. In some cases, they don’t use a milled mold or heat-cured LSR. Instead, the prototypes are made using a room temperature vulcanization process that starts with a thermoplastic copy of the part made on a 3D printer. A mold is cast around the 3D-printed part and hand-filled using a caulking gun. The resulting part may be suitable for testing form and fit, but since it does not duplicate the manufacturing process or use real LSR material, it cannot be relied on for functional testing or actual production at any volume.
To get real parts for prototyping, traditional producers have often had to wait until manufacturing molds have been made, which can take weeks or months. At this late stage of development, problems that show up can cause serious setbacks in the development process and the scrapping of very expensive tools. FacFox’ automated aluminum mold milling allows cost-effective prototyping using real materials and industrial processes earlier in development when the redesign is easier, less time consuming and less costly.
FacFox is continually expanding its processes and capabilities. Its current requirements and design considerations are listed.
- Maximum part size is 12 in. (304mm) by 8 in. (203mm) by 4 in. (100mm). This is the size envelope that the part must be able to fit in, although the part cannot occupy that full space.
- Maximum part volume is 26 cu. in. (426 cc).
- Wall thickness can be as thin as 0.010 in. (0.25mm). The issue is not ability to fill, but ability to mill thinner walls and to remove the thinner-walled parts from the mold without damage. Due to LSR’s shear thinning, variation in wall thickness is generally not a problem.
- Rib thickness should be from 0.5 to 1.0 times the thickness of the adjoining wall.
- The radius of inside fillets should be approximately equal to the wall thickness.
- Sink is almost nonexistent, but elimination of unnecessarily thick areas will reduce material cost.
- To eliminate flash, parting lines should be kept as simple and short as possible.
- Removal of LSR from the mold is typically done manually rather than by ejector pins. The part should be designed to be retained entirely in one mold half, and some feature of the part should rise above the parting line surface to facilitate hand removal.
- Many parts with simple undercuts can be easily removed from the mold by the press operator without mechanical assistance. Parts with undercuts will be reviewed on a case-by-case basis for feasibility.
- LSR parts generally require draft similar to that of thermoplastics, approximately one degree of draft per inch of depth. Zero draft may be tolerated on shallow parts. LSR is more tolerant of reduced draft than thermoplastics. This will be determined on a case-by-case basis.
- Due to LSR’s easy flow, it requires relatively small gates for resin injection. Gates should ideally feed into the thickest or broadest cross-section of the part, though this is not an absolute requirement. LSR edge gates will leave a vestige or blemish and should be placed on a surface that is not dimensionally or cosmetically critical or in a recess.
- FacFox will, if necessary, add vents, overflows, or tear strips to improve part quality. These may leave a small vestige on the finished part. FacFox will propose gate and vent locations, which customers must approve, before manufacturing the tool.
- FacFox offers the following finishes on LSR molding tools:
- PM-F0
- PM-F1
- SPI-C1
- PM-T1
- PM-T2
- SPI-A2
- More finishes will be added in the near future, and special requests will be given consideration.
- Typical achieved tolerances for a well-designed part are linear tolerances of +/-0.003 in. (0.08mm) with an included resin tolerance of no less than +/-0.01 in./in. (0.01mm/mm).