Want to improve your wood processing results? Looking to increase efficiency? Here are some tips.
Which types of wood can be laser processed?
Authentic wood is a natural material that is ideal for use with a laser machine, and laser users need to evaluate the materials various characteristics such resin content and density during processing.
Rule of thumb:
Wood that offers consistent coloration and uniform grain patterns will often be easier to use, as well as allow for more even engraving.
Main wood types suitable for laser processing |
|
---|---|
Soft woods | Soft woods such as poplar or balsa can be cut and engraved faster by using a lower power level. The engraving process will produce less contrast if the wood being used is lighter. |
Hard woods | Hard woods including cherry or oak are typically denser, which will require higher power levels for engraving and cutting. Compared to soft woods, this type of wood will offer more contrast when engraved. |
Coniferous woods | Coniferous woods such as fir or larch are not suitable for laser engraving because of its hard density and uneven grains. The surrounding wood (“non-graining”) is quite soft on the other hand, which makes it rather difficult to find optimal laser parameters. |
Veneers | Veneered wood consists of real wood on the surface, so it is able to be engraved similarly to solid wood panels. |
Plywood | Plywood is composed of typically three or more layers of wood, with grain that is glued and pressed at a 90° angle. Plywood is offered in various types including a wide range of color, texture, and thickness. The glue that is used to manufacture the plywood is important for laser processing, especially when cutting the material. Select plywood panels made with white-glue, or that is otherwise marketed specifically for laser processing. |
MDF (Medium density fiberboard) | MDF is a uniform wood-based material composed of finely defibrated, mainly bark-free, softwood, which is gently pressed in the transverse and longitudinal directions. The surface and edges of MDF are typically firm and smooth, which makes it ideal for laser cutting and engraving. However, it should be noted that the cutting edges become very dark during laser processing. |
A rule of thumb for laser engraving:
When laser engraving, hardwoods will produce a darker appearance while softwoods will produce a lighter appearance.
A rule of thumb for laser cutting:
When laser cutting, wood that is resin-free or drier by nature will result in a brighter cutting edge.
Determining the proper cutting and engraving parameters
Woods are natural materials that will react differently depending on the type being processed.
Determining the engraving parameters
Using the grayscale matrix will allow you to efficiently determine the correct engraving parameters for individual applications.
Tip: The more you defocus (z-offet: approx. 0.5 – 2 mm), the darker the engraving of the wood will be. Defocusing the laser beam will increase the spot size of the laser as well as decrease the performance density, resulting in more burning instead of letting it pass directly into the gaseous form. Detail can be lost from using this technique.
Determining the cutting parameters
Laser cutting parameters can be tested by drawing a rectangle with two differently rounded corners, and then sending the graphic to the laser machine. Depending on the wood being processed, you can achieve your desired cutting quality by reducing the speed gradually. For example, using 3mm thick wood should start with a cutting speed of 2-5% as well as high performance.
Things to consider when laser cutting and laser engraving wood
Preparation of materials
Laser processing wood will result in some dust or debris being generated, which can get stuck in all of the intricate grooves and engravings that you have created. To reduce excess post-processing cleanup, we recommend gluing an application tape onto the working surface of the material, which will serve as a protective barrier that can be easily engraved along with it. Application tape is the perfect solution when cutting or engraving larger areas, and it can be easily removed after laser processing. However, we do not recommend using application tape for very fine engravings or for photo-engraving, since the tape will be cut into many small sections which will be harder to remove. When purchasing application tape, make sure to validate that the tape does not contain PVC and that it is removable.
Choosing the right optics
Laser cutting wood is a sublimation process that will require the use of proper optics and precise focusing, as well as a distinction must be drawn between engraving and/or cutting. When laser engraving wood, as the level of detail that a graphic offers goes up, the shorter the focal length of the lens should be. As a rule of thumb, 1.5″ or 2.0″ lenses are suitable for almost any laser engraving on wood. When laser cutting wood, you will need to increase lens focal length as material thickness increases. For example, we recommend using a 2” lens for 1/8” wood, and a 2.5” lens for 1/4″ wood.
Compressed air
Using compressed air especially when cutting wood is highly recommended, and a small-diameter nozzle should be used to protect the lens. Additionally, the small nozzle diameter directs the compressed air straight into the cutting gap, resulting in any dust or gas produced being extracted more efficiently so that cutting quality is significantly improved.
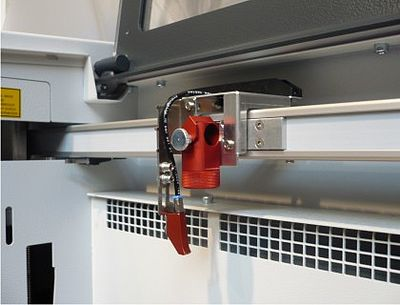
Cleaning
Cleaning the hardware and optics of your laser system is an important step in woodworking. Wood resin and oils are extremely sticky, and any dust produced from laser processing will often settle in the machine. So it is very important to clean your machine on a regular basis.
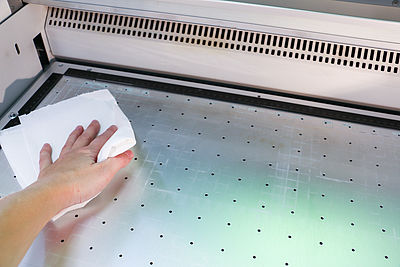
Suitable exhaust system
Laser cutting and engraving wood produces lots of excess gas and dust, which will need to be properly extracted with the use of a suitable exhaust system.
Special applications: Inlays and relief engraving
Relief engraving on wood
Wood is an ideal material for relief engraving. When processing a relief engraving, the grayscales adapt to different laser power levels resulting in three-dimensional engravings. Several passes can be processed with relatively high-performance, and then only one or two passes cleaning are required to remove any smoke residue produced.
Inlays in wood
Wood inlays such as intarsia are extremely popular with woodworking, and typically various woods are laid flat so that s smooth surface with variations of color and structure are created. Commonly, the base material is engraved first followed by the material to be laid (usually veneer), which is then cut and inserted. When laser processing the veneer, ensure that the laser beam width (cutting gap) is properly adjusted so that the carrier is slightly larger.