Are you ready to explore the cutting-edge world of 3D printing? This week, we’re diving into one of the most fascinating materials being revolutionized by 3D printing technology: aerogel.
What is Aerogel?
Aerogel, often referred to as “frozen smoke” or “solid air,” is one of the lightest and most insulating materials known to science. It is composed of up to 99.8% air, making it incredibly lightweight and porous. Despite its delicate appearance, aerogel is a solid material with remarkable properties, including high thermal insulation, low density, and impressive strength.
3D Printing Aerogel: A Game Changer
Recent advancements have made it possible to 3D print aerogel, opening up new possibilities for its application. Researchers have successfully 3D printed various types of aerogel, each with unique benefits:
Graphene Aerogel
Known for being the lightest material on Earth, graphene aerogel is superelastic, conductive, and can absorb up to 900 times its weight in oil. This makes it ideal for environmental clean-up and advanced electronic applications.
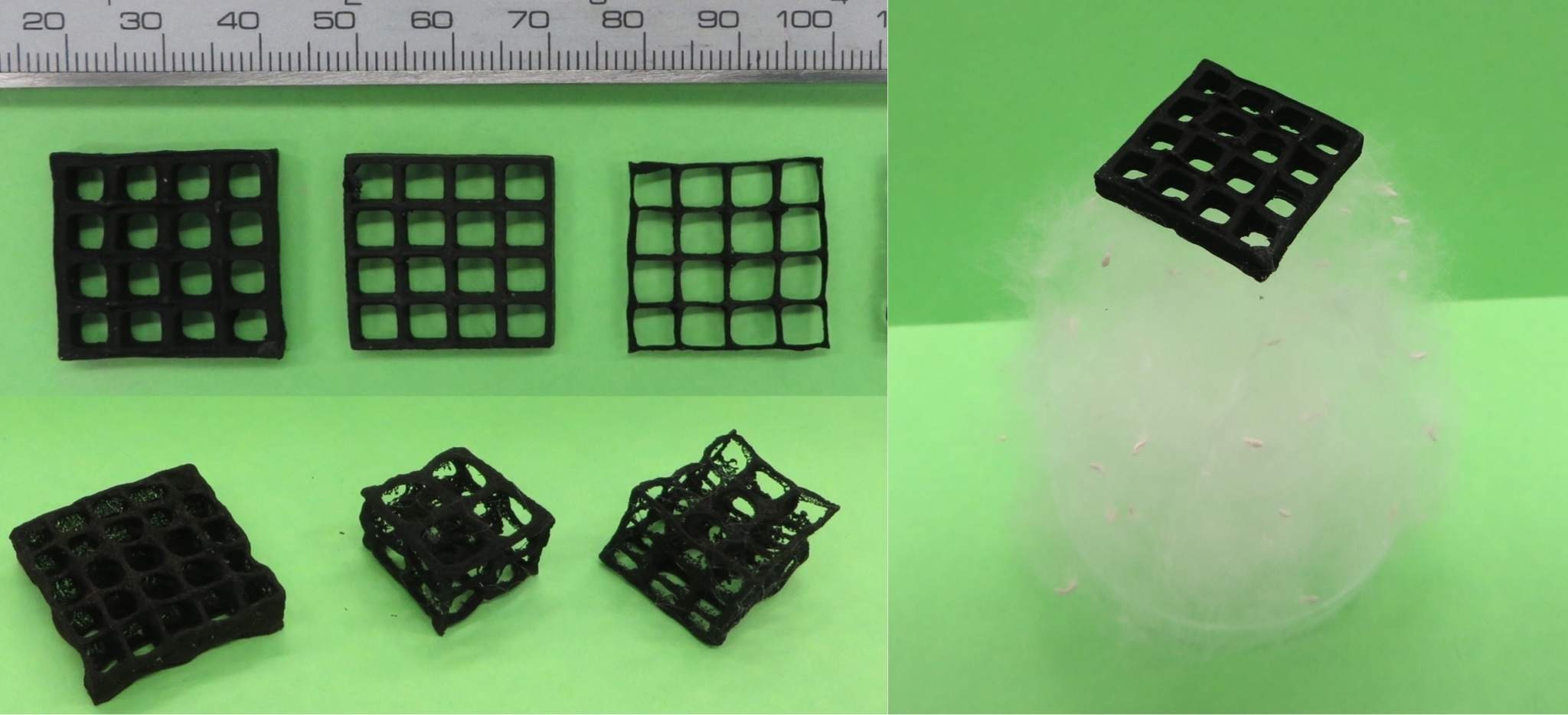
Silica Aerogel
Renowned for its exceptional thermal insulation properties, silica aerogel is now being 3D printed into stable microstructures. This innovation allows for precise thermal insulation in microelectronics, robotics, and even medical implants.
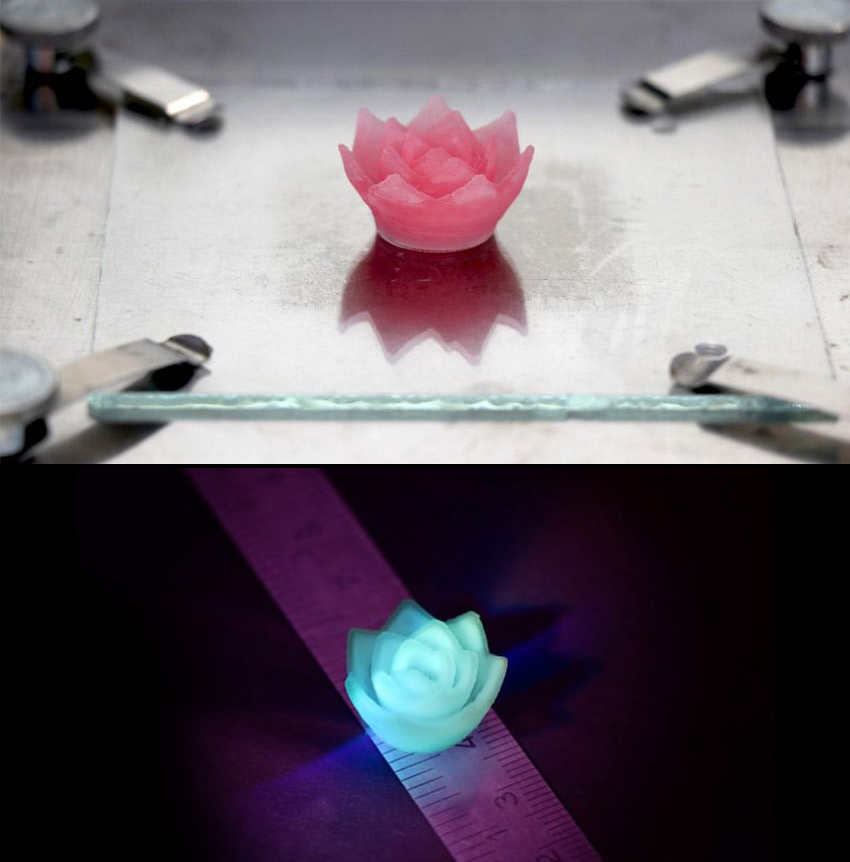
Polyphenylene Sulfide (PPS) Aerogel
A new type of aerogel using PPS, a super strong thermoplastic, has been developed for aerospace and advanced engineering applications.
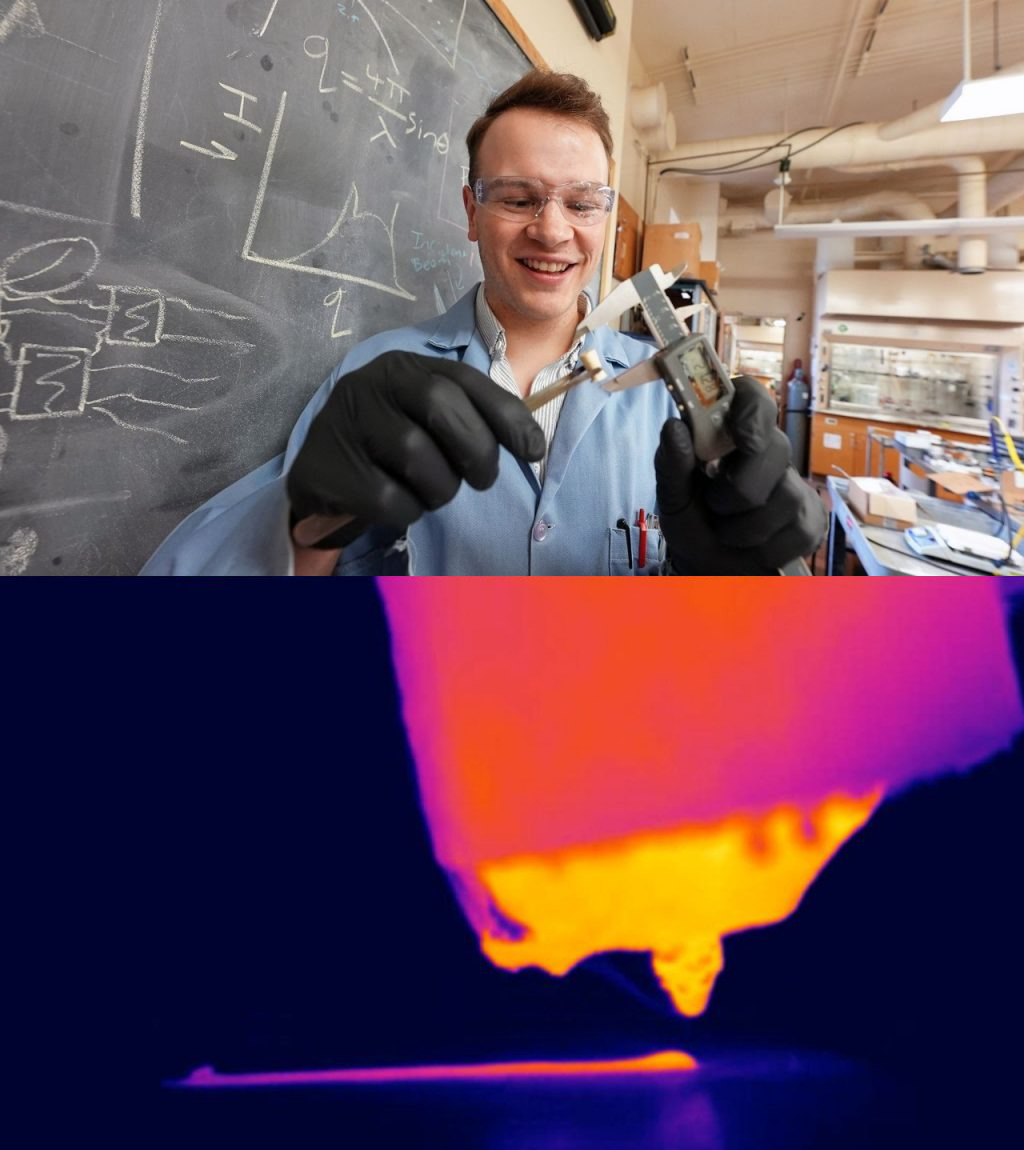
How is it Made?
The process of 3D printing aerogel involves several intricate steps:
Step 1: Material Preparation
- For graphene aerogel, graphene oxide is mixed with an aqueous suspension and a silica filler to form a homogenous, highly viscous ink.
- For silica aerogel, silica nanoparticles are combined with a solvent to create a printable ink.
Step 2: 3D Printing
- The prepared ink is loaded into a syringe barrel and extruded through a micronozzle using a technique called direct ink writing. This method allows for precise control over the deposition of the material, layer by layer, to build the aerogel structure.
- For graphene aerogel, the ink is often laid out on a surface cooled to -25°C to freeze individual layers instantly.
Step 3: Post-Processing
- Freeze-Drying: For graphene aerogel, the printed structure undergoes freeze-drying to remove the ice scaffolds without damaging the delicate aerogel structure.
- Chemical Processing: Additional chemical treatments are applied to remove any remaining solvents or supporting materials, ensuring the final aerogel structure is stable and functional.
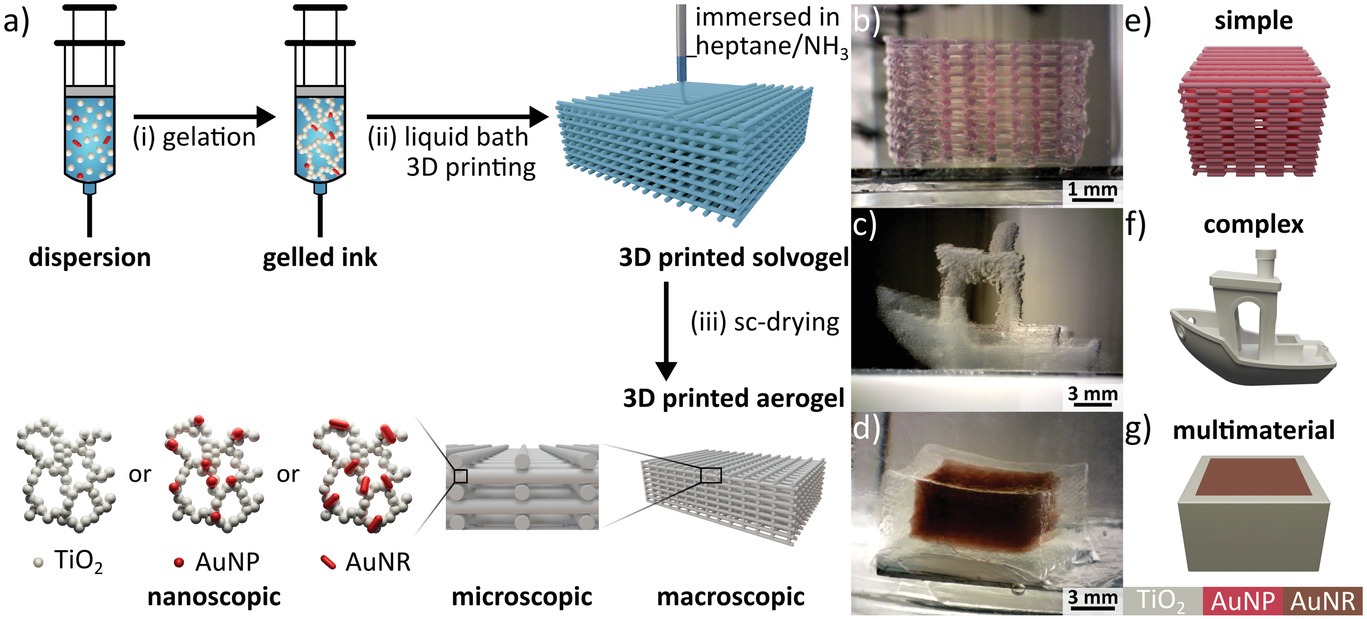
Real-World Applications
The ability to 3D print aerogel opens up a world of possibilities. Here are some real-world examples:
Thermal Insulation in Electronics
Silica aerogel microstructures are used to thermally insulate electronic components, preventing overheating and improving device performance.
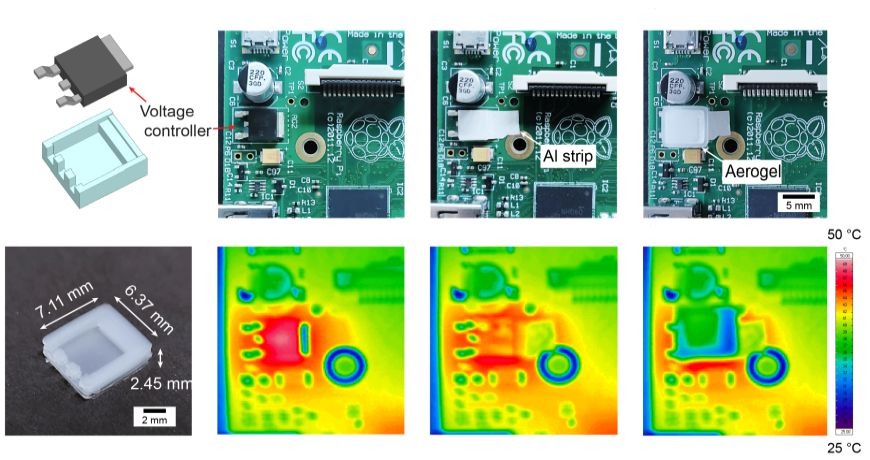
Environmental Clean-Up
Graphene aerogel is used in environmental clean-up operations, effectively absorbing oil spills.
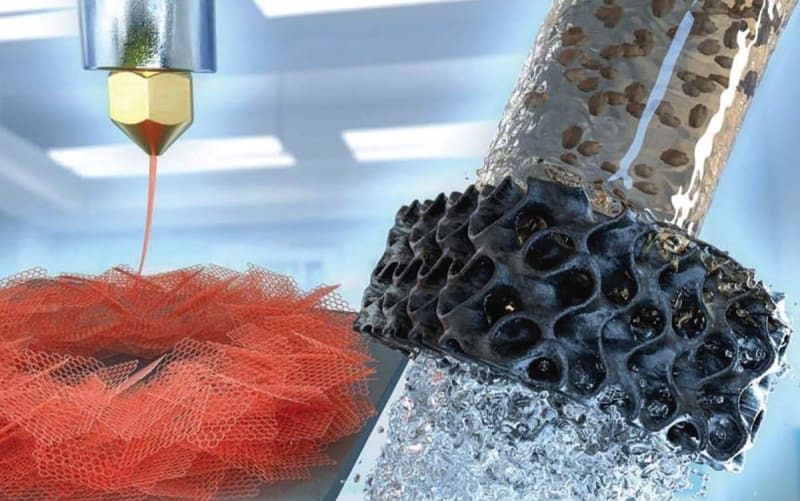
Medical Implants
Silica aerogel microstructures are explored for use in medical implants, shielding heat sources within implants to protect surrounding body tissues.
Energy Storage
Graphene aerogel microlattices are designed for enhanced energy storage applications, such as batteries and supercapacitors.
Stay tuned as we continue to explore the latest innovations in 3D printing and materials science. The future is light, strong, and incredibly cool with 3D-printed aerogel!