Fused Deposition Modeling (FDM), also known as Fused Filament Fabrication (FFF), is a widely-used 3D printing technology that creates objects by extruding melted thermoplastic material layer by layer. While traditionally associated with plastics, recent advancements have enabled the use of metal in FDM 3D printing, expanding its applications in various industries. This comprehensive guide delves into the intricacies of FDM 3D printing with metal, exploring its process, benefits, challenges, and technical considerations.
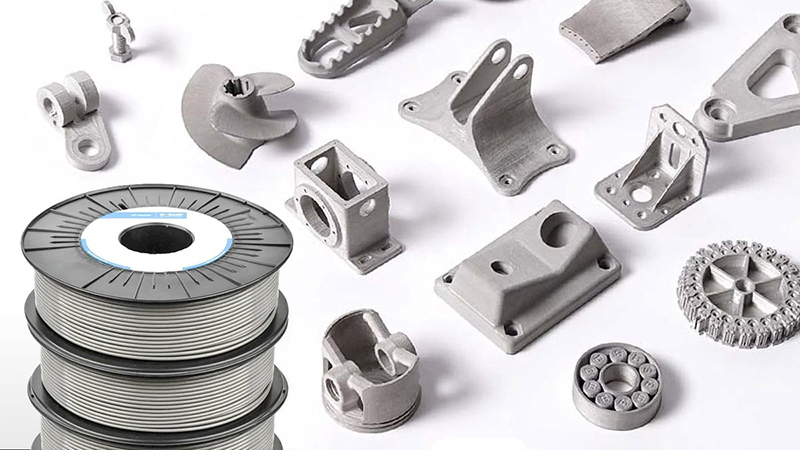
What is FDM 3D Printing?
FDM 3D printing works by feeding a continuous filament of thermoplastic material through a heated printer nozzle. The nozzle heats the filament to its melting point and deposits it layer by layer according to the digital design, which is sliced into thin horizontal sections. As each layer cools, it solidifies, creating a cohesive structure. The process is controlled by computer software that directs the movement of the print head and the extrusion of the material.
How Does Metal FDM 3D Printing Work?
Metal FDM 3D printing utilizes composite filaments composed of finely powdered metal particles embedded in a polymer binder. The process involves several key steps:
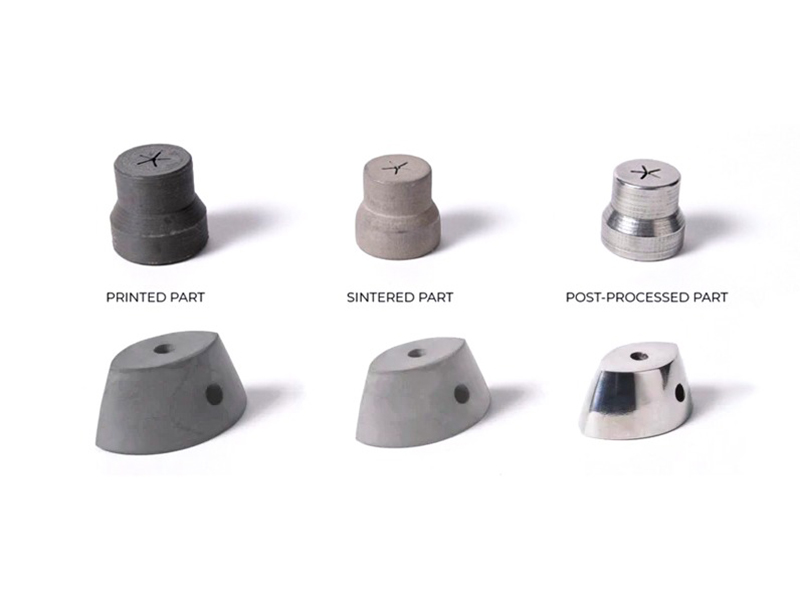
Material Preparation
- Composite Filaments: These filaments typically consist of 60-80% metal powder mixed with a thermoplastic binder. Common metals used include stainless steel, bronze, copper, and aluminum.
- Filament Properties: The filament must have sufficient flexibility to be fed through the printer but also enough stiffness to avoid buckling.
3D Printing
- Printer Setup: Metal FDM requires printers capable of handling abrasive materials. Upgrades may include hardened steel nozzles, wear-resistant extruders, and heated build plates.
- Printing Process: The printer extrudes the composite filament layer by layer to create the “green part.” Parameters such as nozzle temperature, bed temperature, print speed, and layer height are crucial for achieving good print quality.
- Green Part: The printed object, known as the green part, contains both the metal powder and the polymer binder.
Debinding
- Solvent Debinding: The green part is submerged in a solvent bath to dissolve the binder. This process can take several hours to days, depending on the part’s size and complexity.
- Thermal Debinding: Alternatively, thermal debinding involves heating the green part to a temperature where the binder evaporates. This process must be carefully controlled to avoid warping or damaging the part.
Sintering
- Sintering Furnace: The debound part, now referred to as the brown part, is placed in a sintering furnace. The furnace heats the part to just below the melting point of the metal, causing the metal particles to fuse together.
- Temperature Control: Precise temperature control is essential to ensure the metal particles bond without causing the part to melt or distort.
- Shrinkage: During sintering, the part shrinks by 15-20%. This shrinkage must be accounted for in the original design to ensure the final part meets the desired dimensions.
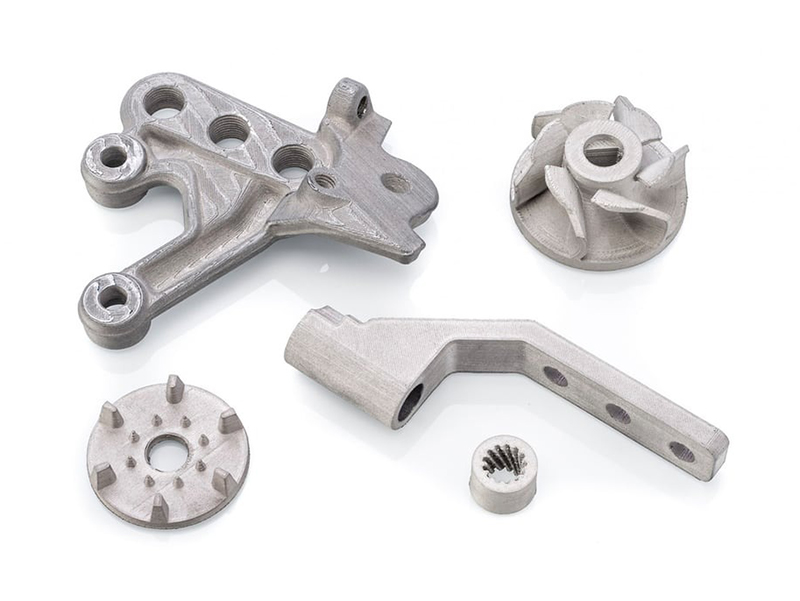
Metal Filaments for FDM 3D Printing
Stainless Steel Filaments
- Composition: Typically made with 316L or 17-4 PH stainless steel powders.
- Properties: Offers good corrosion resistance, mechanical strength, and thermal stability.
- Applications: Ideal for creating durable parts used in harsh environments, such as medical tools, automotive components, and industrial fixtures.
Bronze Filaments
- Composition: Composed of bronze powder mixed with a polymer binder.
- Properties: Exhibits a unique aesthetic with a metallic sheen and patina development over time.
- Applications: Popular in art, jewelry, and decorative objects due to its appealing appearance and ease of post-processing.
Copper Filaments
- Composition: Contains high-purity copper powder.
- Properties: Excellent electrical and thermal conductivity, making it suitable for electronic and heat dissipation components.
- Applications: Used in electrical connectors, heat exchangers, and intricate sculptures requiring high detail.
Aluminum Filaments
- Composition: Composed of aluminum powder with a polymer binder.
- Properties: Lightweight with good strength-to-weight ratio and thermal conductivity.
- Applications: Suitable for aerospace and automotive parts, as well as lightweight structural components.
Titanium Filaments
- Composition: Made from titanium powder, often blended with a polymer binder.
- Properties: High strength, low weight, excellent corrosion resistance, and biocompatibility.
- Applications: Ideal for aerospace, medical implants, and high-performance engineering parts.
Other Specialty Metal Filaments
- Nickel-Based Alloys: Used for high-temperature and corrosion-resistant applications.
- Tool Steels: Suitable for creating durable tools and dies.
- Precious Metals: Gold, silver, and platinum filaments are available for high-value applications like jewelry and electronics.
Benefits of Metal FDM 3D Printing
- Cost-Effective Production: Metal FDM is generally more affordable than traditional metal additive manufacturing methods, such as Direct Metal Laser Sintering (DMLS) or Selective Laser Melting (SLM). This makes it accessible for small businesses and individual makers.
- Ease of Use: Many existing FDM printers can be adapted to use metal filaments with minor modifications, allowing users to leverage their current equipment.
- Rapid Prototyping: Metal FDM enables the creation of metal prototypes quickly and at a lower cost, facilitating iterative design and testing processes.
- Material Variety: A wide range of metal filaments is available, each with distinct properties suitable for various applications.
Challenges and Technical Considerations
Shrinkage and Warping
- Compensation: Designers must compensate for shrinkage in the CAD model to ensure the final part has the correct dimensions.
- Uniform Heating: Uniform heating during debinding and sintering is critical to minimize warping and achieve dimensional accuracy.
Post-Processing Requirements
- Specialized Equipment: Access to debinding and sintering equipment is essential. This equipment can be costly and requires proper handling and maintenance.
- Part Handling: The green and brown parts are fragile and must be handled with care to avoid damage during post-processing.
Material Properties
- Density and Porosity: Sintered parts may have lower density and higher porosity compared to traditionally manufactured metal parts. This can affect their mechanical properties and performance.
- Surface Finish: The surface finish of metal FDM parts may require additional post-processing, such as machining or polishing, to achieve the desired smoothness and precision.
Printer Modifications
- Hardened Components: The abrasive nature of metal filaments necessitates the use of hardened nozzles and extruder gears to prevent wear and tear.
- Temperature Control: Precise temperature control is essential for successful printing. Printers should have heated beds and enclosed chambers to maintain stable printing conditions.
Applications
- Prototyping: Metal FDM is ideal for creating functional prototypes that require the strength and durability of metal. It allows designers to test and iterate on their designs before committing to full-scale production.
- Tooling and Jigs: Custom tools, jigs, and fixtures can be produced quickly and cost-effectively, improving workflow efficiency in manufacturing settings.
- Art and Jewelry: Artists and jewelers can experiment with intricate metal designs, producing custom pieces with detailed features that would be difficult to achieve with traditional methods.
- Small Batch Production: Metal FDM is suitable for low-volume production runs, offering an alternative to casting or machining for small quantities of parts.