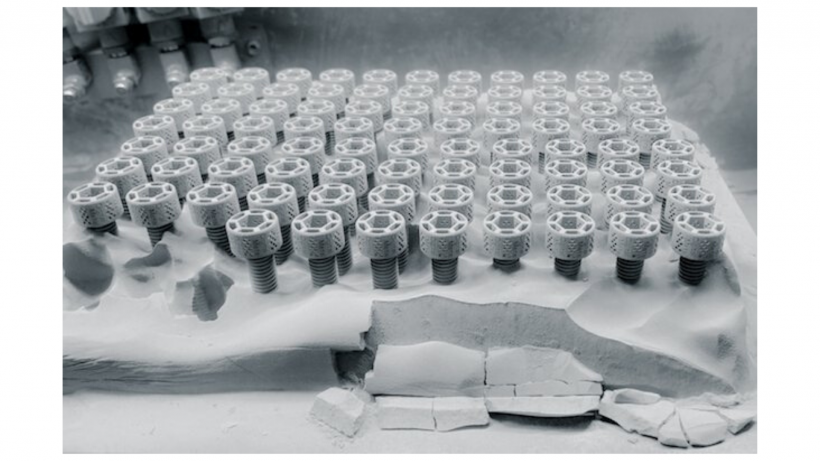
Such activity is in part fueled by many lucrative opportunities this technology presents. For one, the high speed and precision of the metal binder jetting process can help establish it as a new high-volume production method.
But which developments are driving the success of this technology?
Today we’ll be looking at how metal binder jetting has evolved and why it’s taking off as a new manufacturing technology.
The origins of metal binder jetting
The origins of metal binder jetting technology date back to 1993, when the Massachusetts Institute of Technology (MIT) developed an inkjet-based process to create three-dimensional objects using metal powders.
Interestingly, the term “3D Printing” was originally coined by MIT in reference to metal binder jetting technology.
Manufacturing company, Extrude Hone Corporation, obtained an exclusive licence for MIT’s technology in 1996. Since then, the company has developed and commercialised metal binder jetting systems, with the first 3D printer, ProMetal RTS‐300, delivered to Motorola in 1999.
ExOne, which spun off from Extrude Hone Corporation in 2005, remained the only company to offer metal binder jetting services and systems until the early 2010s. At that time, the early MIT patents for the technology began to expire, allowing new companies into the market.
Since then, metal binder jetting has been revived with a vision to make this technology truly suitable for production across industries.
How does metal binder jetting work?
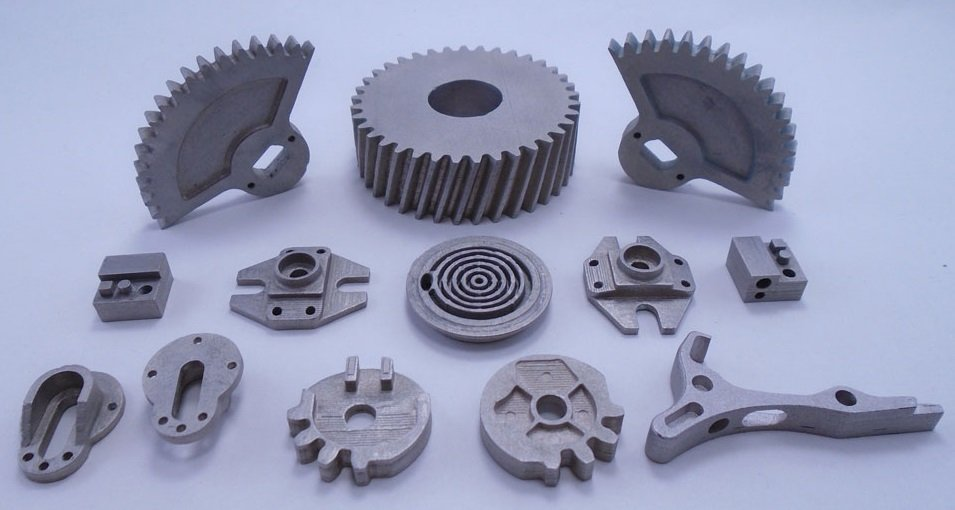
The process begins by spreading a thin layer of powder, with printheads strategically depositing droplets of binder into the powder bed. The printing plate then lowers and another layer of powder is spread.
The process repeats until the part is complete, with unused powder (around 95%) recycled.
With metal binder jetting, parts that have just been printed remain in a fragile green state and will require subsequent post-processing, such as sintering and infiltration, to strengthen the part.
In addition to metals, binder jetting can work with a range of other materials, like sand and ceramics.
Post-processing Steps for Metal Binder Jetting
Traditional binder jetting technology works by using a print head to apply a liquid binding agent onto layers of powder.
When printing metals with Binder Jetting technology, however, the parts will require various post-processing steps as they are initially printed in their green state, which means that they possess low mechanical properties and are very often weak and brittle. The post-processing stage aims to strengthen the parts, and includes curing, sintering, infiltration and other finishing processes.
1. Curing
Curing increases the strength of the green parts so they can be safely removed from the printing bed. During the process the parts are hardened off in an oven at roughly 200°C for a period of several hours, resulting in much stronger parts.
2. Sintering
Despite the curing, your metal parts will still be highly porous. However, you can significantly reduce the porosity of the parts through sintering or infiltration processes. Typically the sintering process takes place in a furnace with a controlled atmosphere, where the part is heat treated at roughly 100°C for 24–36 hours and the binding agent burnt away. This helps to fuse the metal particles together and results in strong metal part with a low porosity. Sintering, however, can cause non-homogenous shrinkage to the part and can be hard to predict – this must therefore be taken into consideration at the design stage.
3. Infiltration
To achieve high density, the part will need to be infiltrated to fill the voids left by the binding agent being burnt away. This is usually done by applying molten bronze to infiltrate the remaining voids in the part. Undergoing these post-processing steps will significantly enhance the mechanical properties of the metal part; for example, bronze infiltration of stainless steel can achieve a final density of 95%.
4. Finishing
Finally, although optional, the part can be polished and plated with gold or nickel allowing aesthetically pleasing surface finishes.
Why is metal binder jetting taking off as a production technology?
Metal binder jetting offers a number of unique benefits, facilitating its adoption for production applications.
First, binder jetting doesn’t melt the metal powder during the printing process, eliminating issues related to the build-up of residual stresses.
Second, no support structures are required for the metal binder jetting process, since printed parts are surrounded by loose, unused powder. Both of these benefits help to keep post-processing to a minimum.
Furthermore, binder jetting machines are less expensive than 3D printers based on SLM or DED processes. One reason for this is that they don’t use costly lasers or electron beams.
Newer metal binder jetting machines are also able to use Metal Injection Moulding (MIM) powders. These are significantly cheaper than metal powders developed specifically for 3D printing, which are typically produced in low volumes, using expensive production methods like gas atomisation.
Switching to MIM powders will, therefore, allow manufacturers to further lower operating costs for this technology.
In addition to cheaper feedstock, binder jetting boasts the ability to print very accurate parts with mechanical properties comparable to those found in traditionally manufactured metal components.
Finally, the speed of the metal binder jetting process is typically faster than that of other metal 3D printing processes. All of these benefits combined result in a very scalable and production-capable technology.
The latest developments advancing metal binder jetting
The 2010s mark a new era for metal binder jetting. From startups to more established players, a number of companies are actively looking to push the limits of what is currently possible with metal binding jetting technology.
ExOne continues to innovate
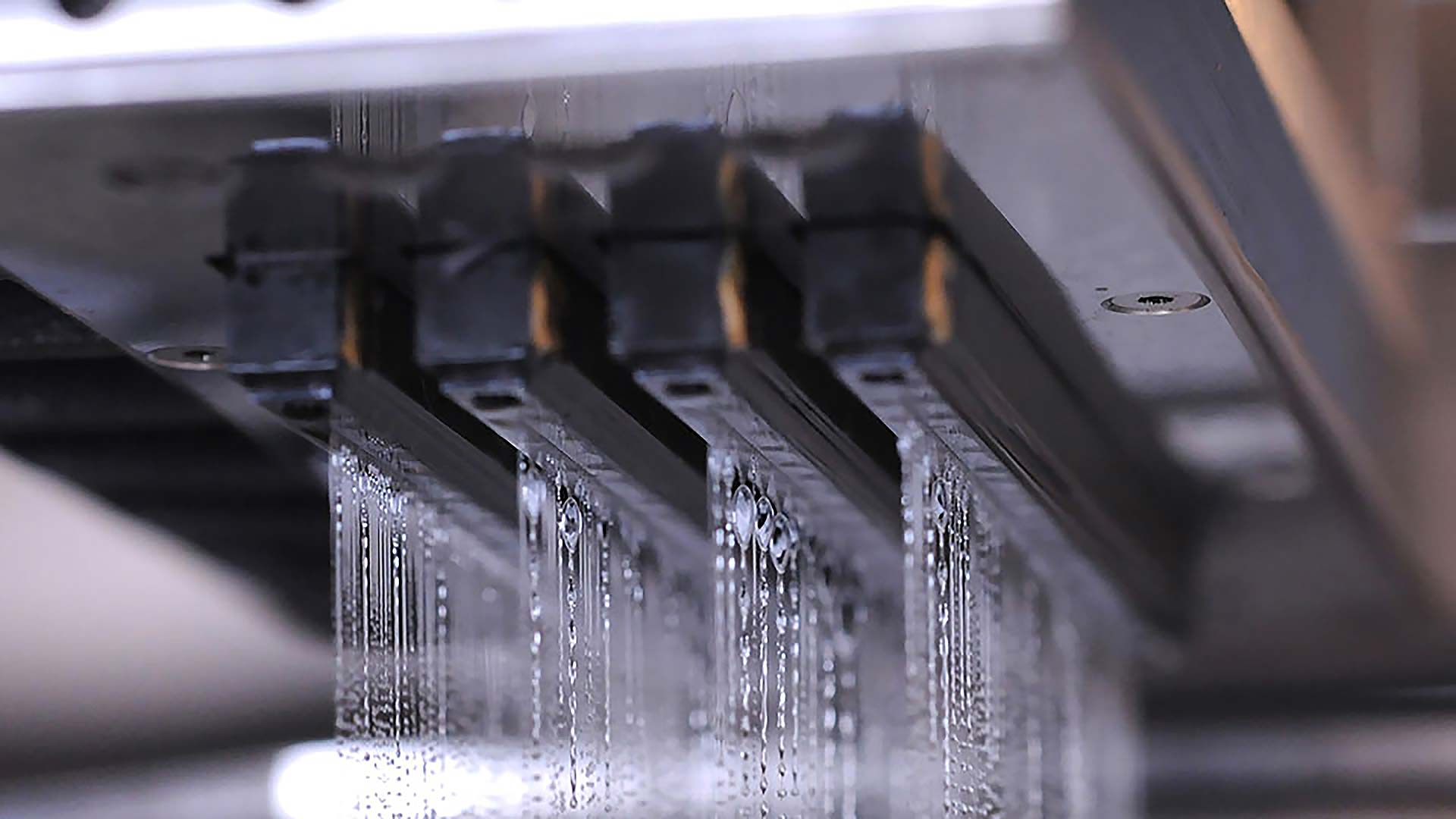
For example, in 2018 the company introduced the Innovent+, marking a new generation of metal binder jetting systems at ExOne. Although the system is slower than ExOne’s previous M-Flex 3D printer, it has two new important features.
First, it’s equipped with an Ultrasonic recoater, developed to improve powder flowability and simplify material change-over. ExOne says that the new recoater represents the most advanced powder dispensing technology on the market.
The recoater comes with four screen configurations for greater material compatibility. This feature plays into another key development: the machine can process standard MIM powders.
Other powder bed metal 3D printers, particularly those that use a laser or an electron beam, require specially formulated powders to work consistently. However, such powders are often much more expensive than materials for traditional metal processing technologies.
By enabling the Innovent+ to support MIM powders, ExOne can introduce cost savings and greater material flexibility to the users of its machines.
Continuing to innovate, the company has scaled up the technology behind the Innovent+ into a production-level X1 25PRO 3D printer. Introduced last month, the machine can print as many as 10 different materials on its large 400 x 250 x 250 mm build volume.
With this system, the company aims to enable the production of industrial metal components with high resolution, tight tolerances and improved surface finishes.
Digital Metal: automating metal binder jetting
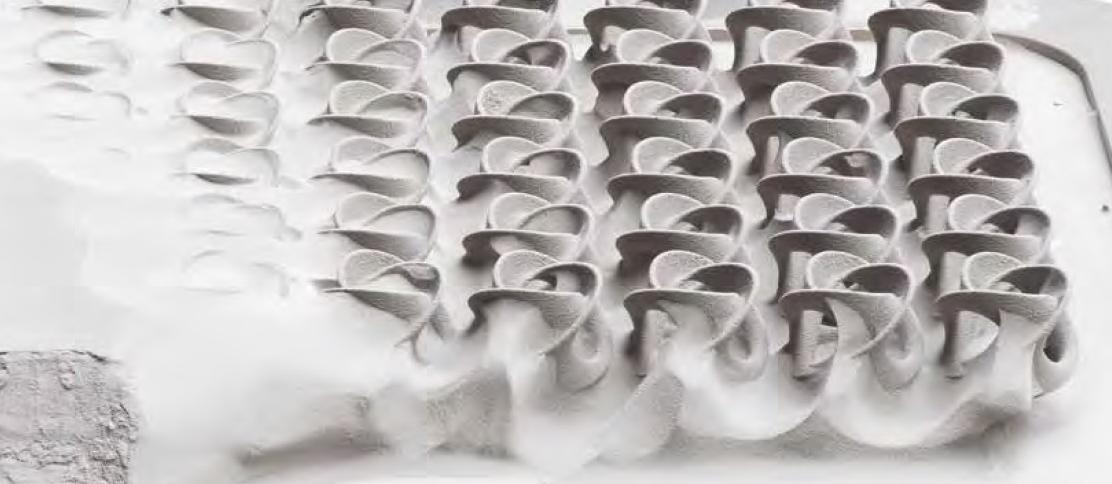
Digital Metal was founded in 2012 and started offering its metal binder-jetting technology as a service in 2013.
In 2017, Digital Metal launched its DM P2500 3D printer, intended for the series production of small, complex parts.
The machine works by spreading a layer of metal powder that is 0.042-mm thick. A binder is then jetted according to the part’s geometry. This process is reported to be accurate and repeatable, enabling it to make very small but incredibly detailed parts at a resolution of 35 microns.
The subsequent sintering process results in average surface roughness of Ra 6.0 micron, fine enough for many end-use parts and features such as internal channels.
Digital Metal says that its metal 3D printers have already produced over 300,000 components in various industries including aerospace, luxury goods, dental tools and industrial equipment.
To further its technology, Digital Metal has launched a fully automated production concept last year.
According to this concept, a robot will handle the majority of the process steps such as feeding the printer with build boxes and then removing them for post-processing. The goal is to eliminate all manual work to facilitate continuous, high-volume production.
By launching this no-hand production line, Digital Metal has made a giant leap forward with its metal binder jetting technology.
HP’s Metal Jet: Making 3D printing a cost-competitive production choice
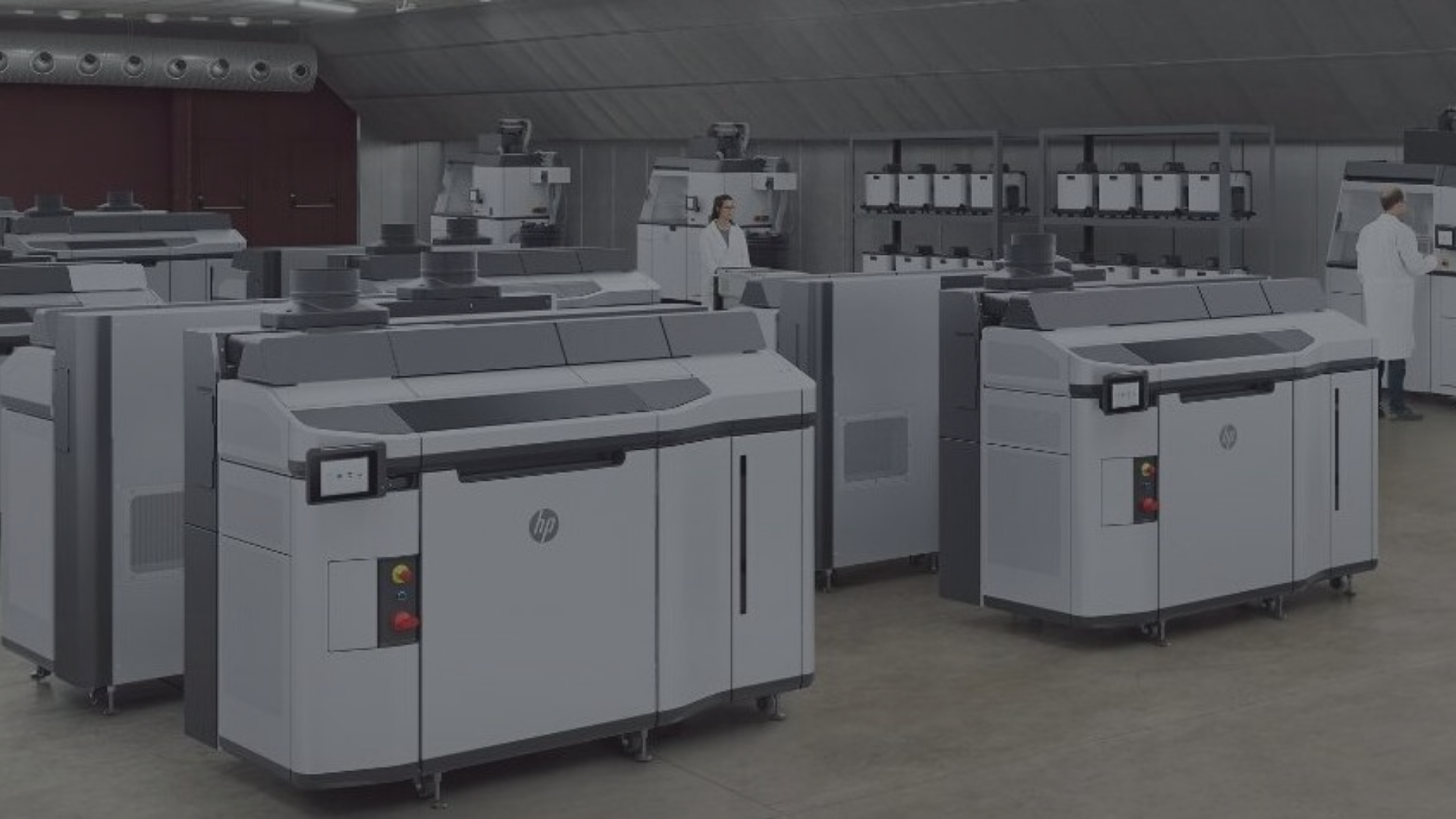
The new metal 3D printer is powered by binder jetting technology. However, the unique advantage HP introduced to this technology lies in its innovative printhead and ink technology.
Although binder jetting technology is inherently fast, HP has applied its knowledge of printhead technology to make it even faster. The Metal Jet system is equipped with 6 printheads with 5,280 nozzles each. Having these multiple rows of nozzles introduces greater productivity and reliability to the printer.
Furthermore, by leveraging its expertise in ink technology, HP has developed an innovative binding agent to make the sintering process faster and cheaper.
“With metal injection moulding you typically have more than 10 % by weight binder that has to be burned out. In our case, we have less than 1%, which is an order of magnitude is less, making it faster, lower-cost and much simpler to sinter,“ says Tim Weber, HP’s Global Head of Metals, speaking in an interview with AMFG.
These advancements combined result in a metal 3D printer which is said to achieve economies and efficiencies comparable to conventional production technologies.
HP is not selling the machine yet. Instead, the company has launched a parts production service, looking to make the 3D printer commercially available in 2020. Considering the claims HP has made about Metal Jet, this technology could become the key to unlocking a sustainable value proposition for metal 3D printing in high-volume production.
3DEO: Combining binder jetting and milling
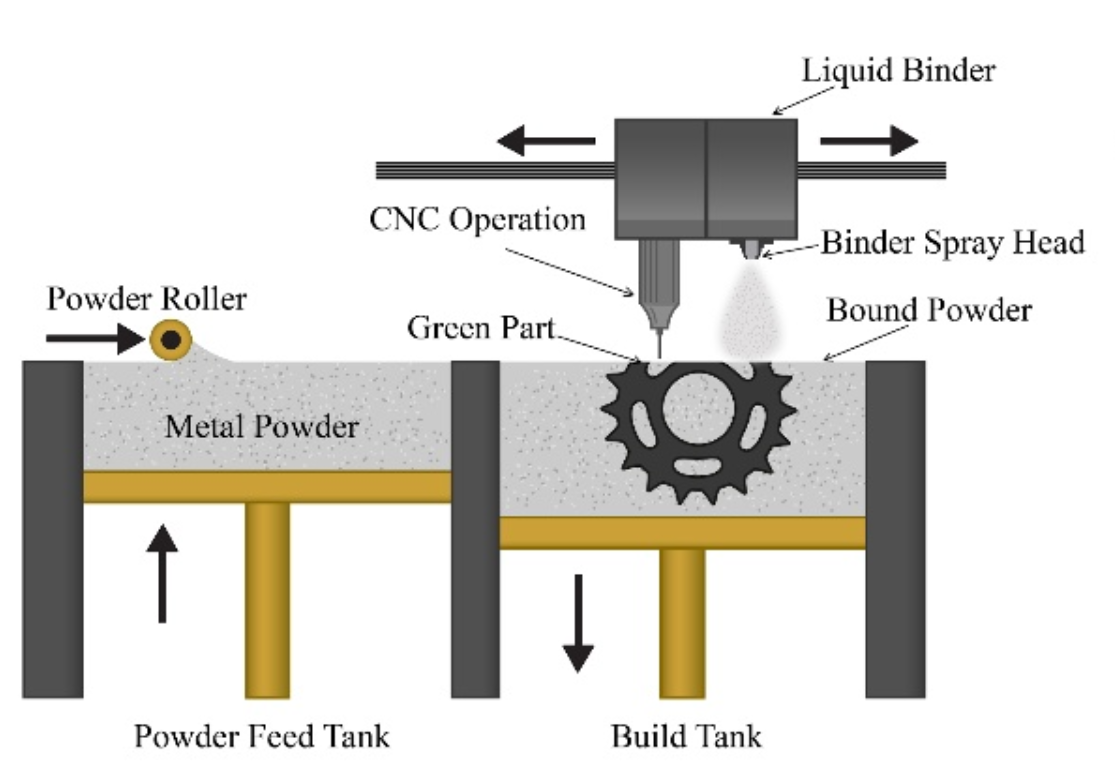
Many companies are looking to make metal 3D printing competitive with other manufacturing techniques. One such company is 3DEO, which was founded in 2016 with the goal to enable high-volume production through metal binder jetting.
To achieve this, the company has entirely reinvented the process. Instead of using inkjet to selectively deposit binder, 3DEO’s machines use a proprietary spray system to apply the binder evenly across the entire layer.
The result is a hard, thin layer of metal powder which is then milled using micro end mills. The CNC operation cuts out the part shape for each layer.
This technology, called Intelligent Layering, represents the first instance of combining binder jetting and CNC milling into a hybrid system. Such a combination allows 3DEO to create very precise small metal parts with over 99.5% density after sintering.
3DEO’s Intelligent Layering technology is currently only offered to clients through the company’s production service. By limiting its technology to its own production service, 3DEO ensures high quality of printed parts whilst keeping its platform very flexible.
Presently, 3DEO is working on some of the largest orders in the metal 3D printing industry, and has recently won a purchase order for 28,000 parts.
Although the company does not plan to sell its machines, its growing production volumes serve as a validation of binder jetting’s capability to deliver production parts on par with conventionally manufactured components.
Desktop Metal: printing metal parts at a striking speed
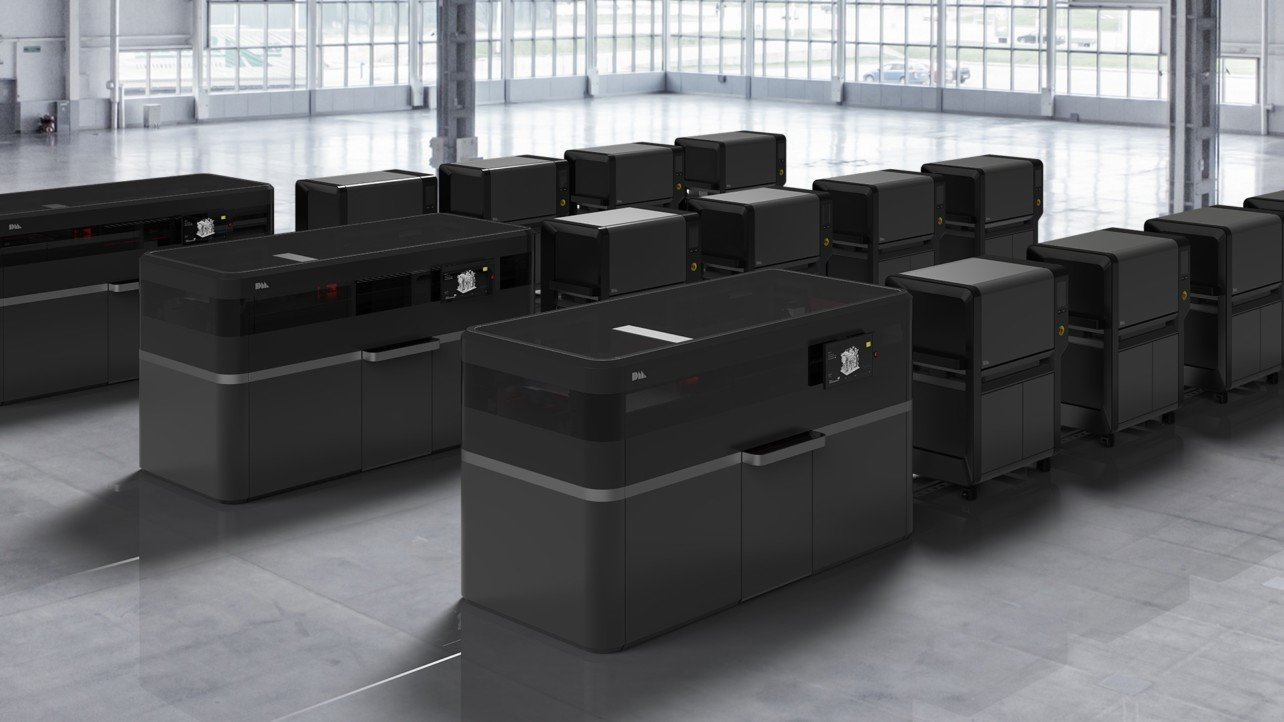
The technology behind the metal 3D printer is what the company calls Single Pass Jetting (SPJ), a faster version of the typical binder jetting process.
The system comes with two full-width printheads, advanced powder spreaders and anti-ballistic system that effectively spread powder and print in a single quick pass across the build area.
With a build volume of 750 x 330 x 250 mm, this bi-directional system enables high-resolution printing at up to 12,000 cm3/hr, which translates into over 60 kg of metal parts per hour. Such speed is orders of magnitude faster than other metal 3D printers on the market, which makes it ideal for the production of complex metal parts at high volumes.
Furthermore, the Production System is the first binder jet system to be equipped with an industrial inert environment that features gas recycling and solvent recovery for the safe printing of reactive metals. This opens up the opportunity for printing a wider range of metals, for example, aluminium.
With its Production System, Desktop Metal has maximised the benefits of metal binder jetting technology by adding substantial speed improvement.
Desktop Metal has only recently made its Production System available for purchase, so it will take some time to see if its production speed claims are proven. But if so, the Production System will become the fastest binder jetting 3D printer available on the market today.
Looking to the future
Metal binder jetting is becoming one of the key metal 3D printing technologies suitable for production. Enabling this is the unique capabilities of the technology to reach high printing speeds and to make high-precision components.
Another key development driving the success of metal binder jetting is its compatibility with already well-known and relatively cheap MIM powders.
A number of companies have recognised the breakthrough potential of metal binder jetting and are now working hard to seize the opportunities it presents.
Going forward, we’ll see these companies evolving metal binder jetting even further. Ultimately, this will help the technology to carve out a valuable share of the total manufacturing market.