The 3D printing industry is developing at an astonishing rate. Over the last 12 months, a number of companies have announced new technologies and launched new machines, indicating an exciting future for the industry.
To help you keep up with the latest in 3D printing, here’s our list of 10 of the most exciting technologies that have recently been announced.
Metal 3D Printing
1. Aurora Labs’ Multilevel Concurrent Printing
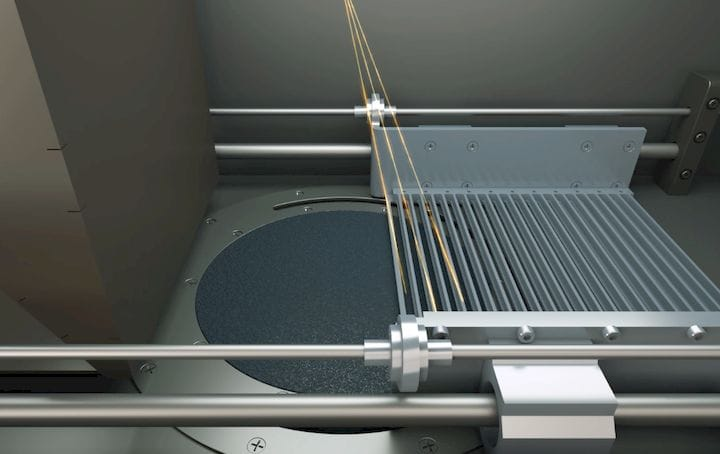
Since 2014, Aurora Labs has been developing a new metal 3D printing technology to enable metal 3D printing at much faster speeds. First unveiled at formnext 2018, the Multilevel Concurrent Printing (MCP™) is based on a familiar powder bed fusion technology — but comes with a twist.
Unlike traditional powder bed technologies that print one layer at a time, MCP prints multiple layers simultaneously in a single pass. At formnext 2018, the company said it was able to print around 30 layers at a time, with the goal to increase this to 100 layers in the next 12 months.
How does it work?
The MCP technology has two key elements: a grid-like recoater mechanism and multiple laser beams. When the print begins, the recoater mechanism, which features multiple hoppers, slides over the print bed, with each hopper depositing different layers of powder in a single pass.
As one layer is deposited, it’s fused by a laser, reaching the powder though the special gaps in the recoater. During that same pass, subsequent layers are being deposited and fused successively by lasers.
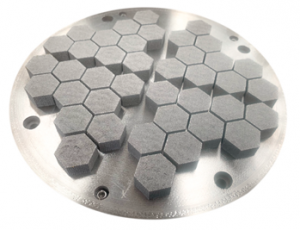
In February this year, the company reported that it had achieved a printing speed of 113 kilograms per day. To illustrate the milestone, Aurora Labs 3D printed a series of 10 mm high titanium hexagon parts, which took only 20 minutes.
Currently, Aurora Labs is preparing to commercially launch its rapid manufacturing system at the end of the year. Will it be able to print a tonne of metal per day by then? Only time will tell.
2. MELD Manufacturing’s MELD technology
MELD Manufacturing Corporation has developed a new way to 3D print metals without melting them.
The technology, which has been in development for over a decade, was first unveiled last year with the introduction of MELD’s large-scale B8 machine.
How does it work?
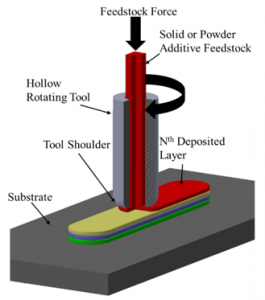
There are many unique advantages to this process. First, MELD technology creates parts that are fully dense, meaning that they don’t require subsequent heat treatment.
Second, the process can be used not only to manufacture parts but also to repair and coat existing components or create custom metal alloys. As Nanci Hardwick, MELD Manufacturing’s CEO, points out:
“We’re the only technology that is able to scale and build or repair very large parts. Another unique capability is that you could take an existing part, place it in the machine and add additional material, whether you want a wear resistance coating on a very lightweight material, or you’d like to add the material to repair a worn surface.”
MELD’s 3D printer doesn’t require an enclosure and the process takes place in an open environment. This means that there’s a lot of freedom for creating larger parts.
However, the technology does have a few limitations. One is the challenge of printing overhangs. The technology also requires significant investment, with its B8 machine costing $800,000. But before committing to the investment, customers can try the technology though the printing service MELD Manufacturing is offering.
3. VELO3D‘s Intelligent Fusion
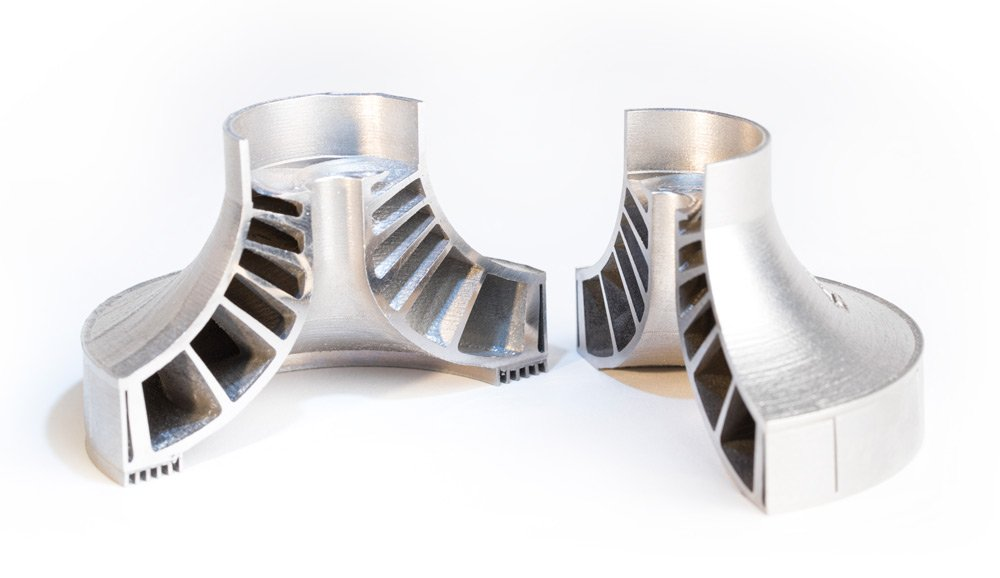
While VELO3D was founded in 2014, the company first appeared on the radar last autumn when it unveiled its laser-based Sapphire 3D printer. Intelligent Fusion™ forms the backbone of both the 3D printer and VELO3D’s print preparation software, Flow™. Put simply, Intelligent Fusion™ enables the tight integration between hardware, software and the process.
How does it work?
The system and the software have been co-developed to achieve a tightly integrated process that has some quite interesting features in store.
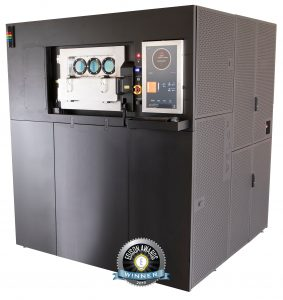
On the software side, VELO3D has developed its Flow software to use CAD files instead of STL files. This decision has two implications. First, since the STL format approximates the surface of a CAD model with triangles, using CAD from the outset results in higher accuracy.
Second, the size of STL files can be very large, making the processing of files cumbersome. Switching to CAD as an initial file format thus makes the print preparation workflow easier and faster.
Furthermore, the Flow software has been developed to be very process-aware. This means, for example, that it can run a simulation before a print starts, as well as predict and prevent failures before they occur.
Combine this with Sapphire’s closed-loop control capabilities, and you get a very intelligent process that should provide extreme reliability.
Intelligent Fusion is said to be capable of achieving first print success rates of up to 90% while reducing the amount of support structures by three to five times.
As VELO3D continues to improve on its technology and acquire new customers, we’re looking forward to more case studies highlighting the unique capabilities VELO3D’s Intelligent Fusion.
4. HP’s Metal Jet
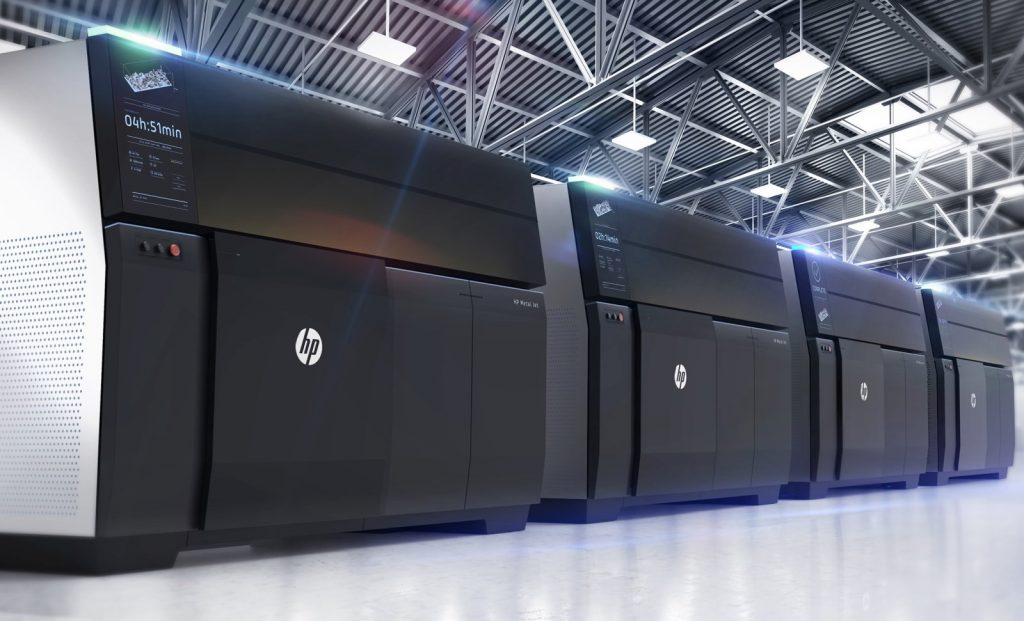
Having established itself on the polymer side of 3D printing, HP has now moved into the metal arena, announcing its Metal Jet 3D printer last year. The system has been developed to be competitive with other production methods.
The technology which enables it is Binder Jetting.
How does it work?
In Binder Jetting, a thin layer of powdered metal is deposited onto the print bed. A line of print heads moves above the print bed, jetting tiny drops of a binder — essentially, glue — where solid metal is needed. When one layer is completed, a new layer of powder is laid down followed by another pass of the binder.
After printing, the final part remains in a “green” state and must undergo a heating operation (called sintering) to burn out the binder and create a dense part.
This process has several advantages. First, it’s fast. With twice as many printheads compared to existing systems, HP claims its Metal Jet printers are up to 50 times more productive than comparable binder and laser sintering machines on the market today.
Secondly, the process uses less binder, making the sintering process faster and cheaper.
“With metal injection moulding you typically have more than 10 % by weight binder that has to be burned out. In our case, we have less than 1%, which is an order of magnitude is less, making it faster, lower-cost and much simpler to sinter,“ says Tim Weber, HP’s Global Head of Metals, speaking in an interview with AMFG.
Interestingly, Metal Jet somewhat resembles the technology and value proposition behind Desktop Metal’s Production System. Both binder jetting-based machines look to disrupt traditional manufacturing by enabling greater speed and scalability. For example, Desktop Metal claims its system is more than 4 times faster than other binder jetting machines.
While Desktop Metal’s Production System was released earlier this year, HP’s technology is slated for a 2020 release and currently available only through HP Metal Jet Production Service.
Once Metal Jet is released, it will be exciting to see how the two systems will compare in the move towards serial AM production.
Polymer 3D printing
5. EOS’s LaserProFusion
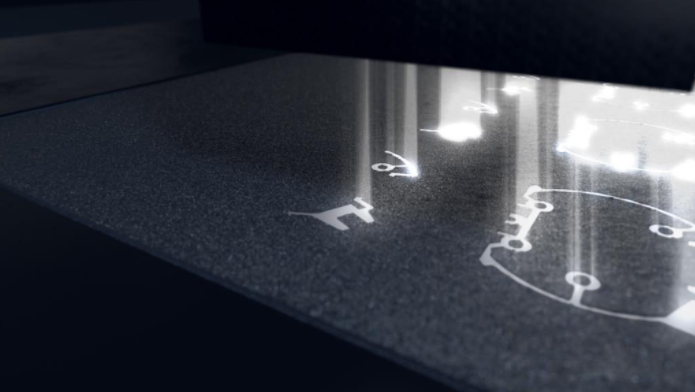
EOS has a longstanding history in polymer 3D printing, particularly with Selective Laser Sintering (SLS). In SLS, a layer of powder, typically nylon, is laid down on a print bed and a laser then contours the cross-section of a part, fusing powder particles together.
While current SLS machines use one or a few CO₂ lasers, the LaserProFusion technology will be able to use up to million diode lasers. This will allow its system to create parts not only with high resolution but also at a much greater printing speed, potentially rivalling injection moulding.
However, the technology, which is said to have been in development for 8 years, will be released no earlier than in 2021. It will be exciting to see what impact LaserProFusion will have when it finds it way into the market.
6. Farsoon’s Flight technology
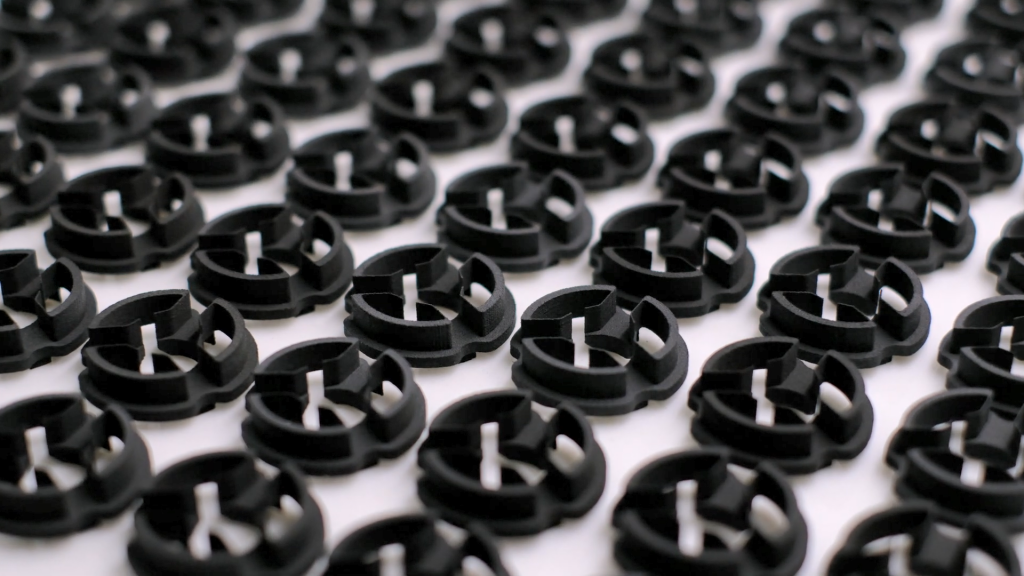
How does it work?
In SLS, a layer of powder is spread on a build platform and then a laser traces the contours of one layer of a part, sintering the powder together.
To improve on this process, the Chinese 3D printer manufacturer has developed a new scanning system and, importantly, replaced the standard CO₂ laser with a fibre laser.
A fibre laser system is capable of delivering more power to the powder bed and improving energy distribution to the material. This is because fibre laser beam enables a smaller laser spot size. This translates into the higher power density, allowing the powder to be sintered in a shorter amount of time.
When combined, these benefits result in a scanning speed of over 20 m/s, which is roughly four times that of comparable technologies. Furthermore, the added power from a laser makes feature details as small as 0.3 mm possible.
Designed to help drive the adoption of 3D printing for high-volume production, Flight Technology is certainly a step forward in this direction.
7. Essentium’s High Speed Extrusion
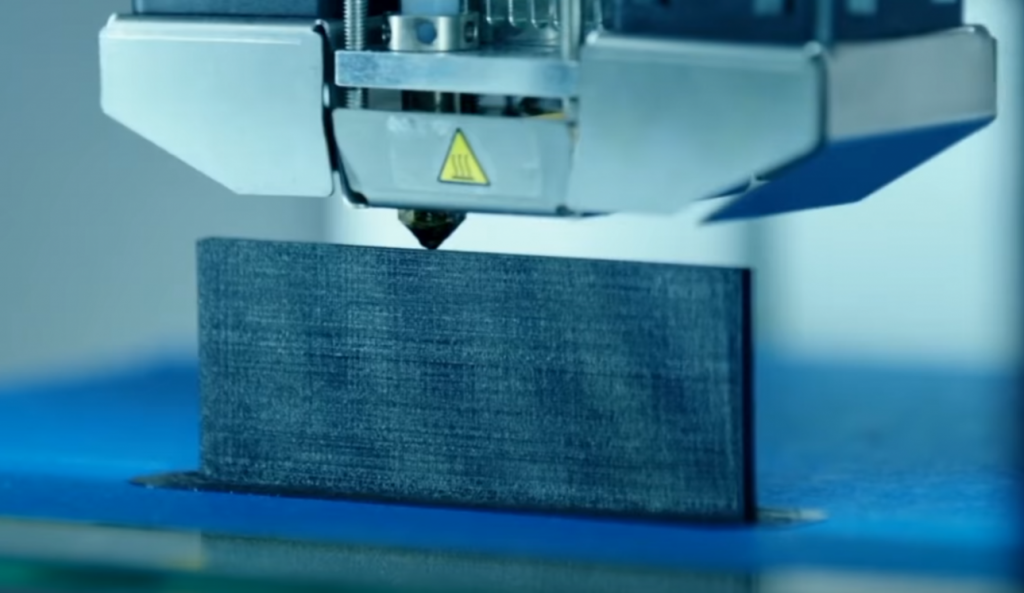
How does it work?
First unveiled at Formnext 2018, Essentium’s High Speed Extrusion (HSE) platform is based on Fused Filament Fabrication (FFF) technology. In FFF, a thermoplastic filament is melted and pushed through a nozzle, printing parts layer by layer. A long printing time, particularly for larger objects, and has been one of the key limitations of FFF.
To overcome this challenge, Essentium’s HSE incorporates a number of design features that could potentially make it one of the fastest available.
For example, the HSE uses all linear motors, meaning that the printhead can move at a much greater speed (1 m/sec) and with greater accuracy. Reportedly, the motion system is accurate to up to 30 microns positioning — quite incredible at such speeds. To match the speed of the motion system, Essentium also incorporated powerful servo motors instead of steppers.
Another element making this system quite unique is Essentium’s proprietary nozzle, the HSE Hozzle™, which can heat from 20°C to 500°C in 3 seconds.
In addition to the HSE technology, Essentium has also developed its FlashFuse technology to overcome part weakness in the Z-axis (the direction in which the layers are deposited), a common issue with 3D-printed parts.
The technology involves the deposition of an energy-responsive filament and the application of an electric current. This current heats up the part, effectively moulding the layers together and creating parts equally strong in all directions.
Planned for release later this year, Essentium will combine its FlashFuse and HSE technology in a single platform, named the HSE 180•S.
By optimizing the motions, extrusion, temperature and, finally, part strength, Essentium is on track to set a new benchmark for extrusion 3D printing.
8. Evolve Additive Solutions’ STEP
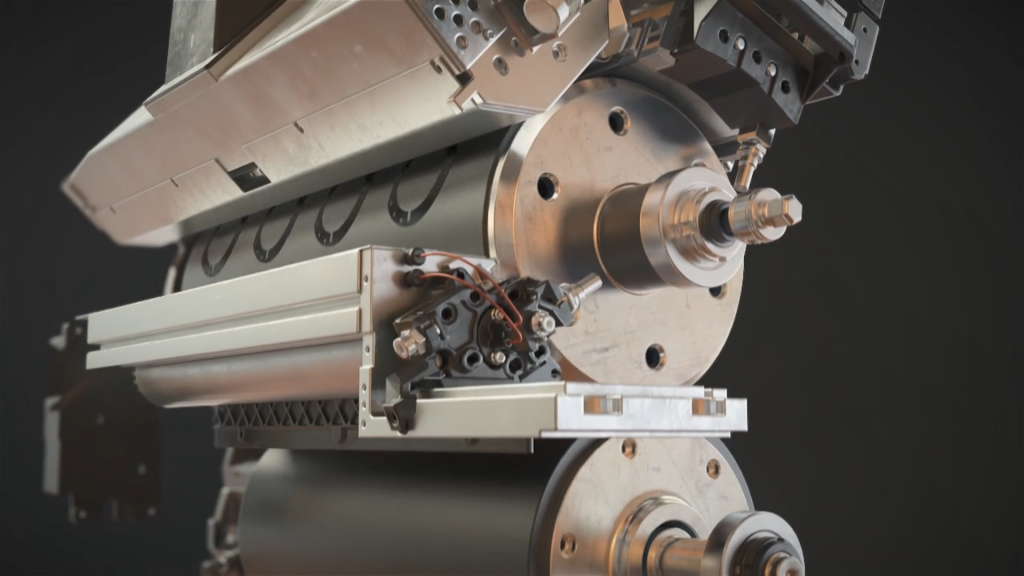
Evolve first appeared on the 3D printing scene last year with its Selective Toner Electrophotographic Process (STEP) — a technology the company has been developing for almost ten years.
How does it work?
STEP is like no other known polymer 3D printing process available on the market today, in that it doesn’t use lasers, nor does it extrude plastic filaments. Instead, it’s based on the same electrophotographic printing technology found inside many office printers.
The STEP process begins by electrostatically charging a roller, which then passes over the powder material, which is referred to as a toner. The one layer of toner sticks to the roller and is then transferred onto a conveyor belt.
On the conveyor belt, the growing part passes through a heating unit, where a new layer is fused onto the preceding one before the subsequent layer of material is laid down.
This technology can potentially enable very high throughput rates, making it cost-effective for mass production 3D printing.
Also importantly, the parts 3D printed using STEP process are isotropic, meaning that they have strength in all three directions. This is due in part to the fact that the Evolve machine preheats not only the part but also the next layer, which results in a superior bonding between layers.
Evolve’s technology is not expected to become commercially available until 2020. But when it does, it could provide a completely new way to 3D print polymer parts.
9. Fortify’s Fluxprint technology
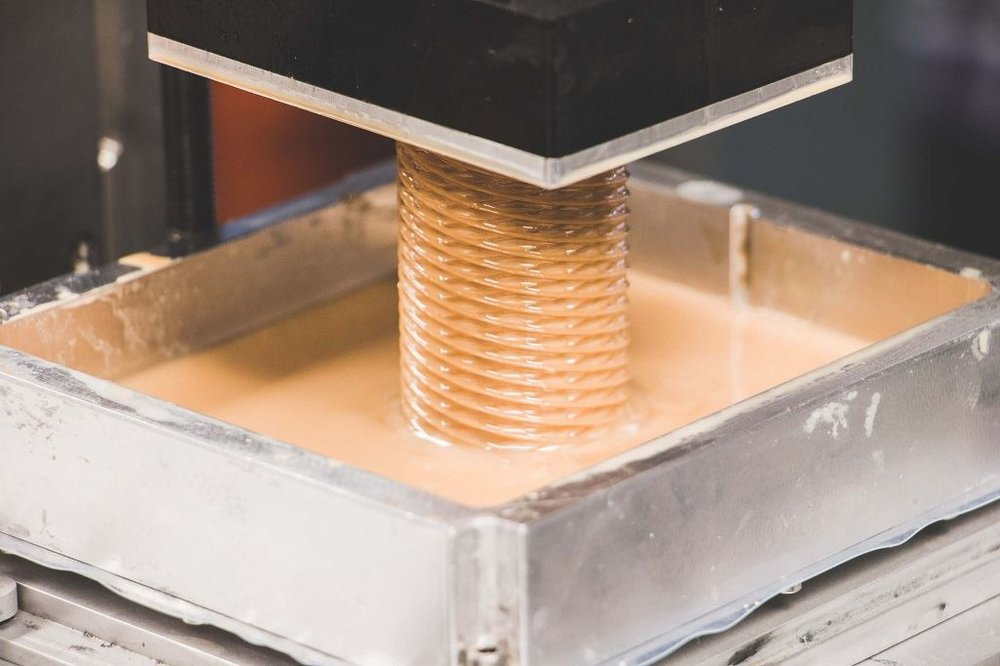
How does it work?
The Fortify 3D printer is based on Digital Light Processing technique, where a digital light projector screen is applied to solidify polymers sensitive to light. Wth Fluxprint process, the polymers are mixed with chopped fibre, which are treated with a metallic coating.
A magnetic field is then applied to the fibres making them to orient themselves according to the magnetic forces.
In the next step, the printer applies light to cure one layer of a part. The process repeats, layer by layer, to complete the print.
By controlling the orientation of fibres on each layer, Fluxprint can create very stiff and strong parts. This technology could be particularly useful for producing injection moulds and automotive tools.
Fortify is looking to release its first commercial 3D printer in the next 8 to 12 months. We’re excited to see this technology taking shape and we’ll certainly be hearing from Fortify a lot more in the future.
10. Origin’s Programmable Photopolymerisation
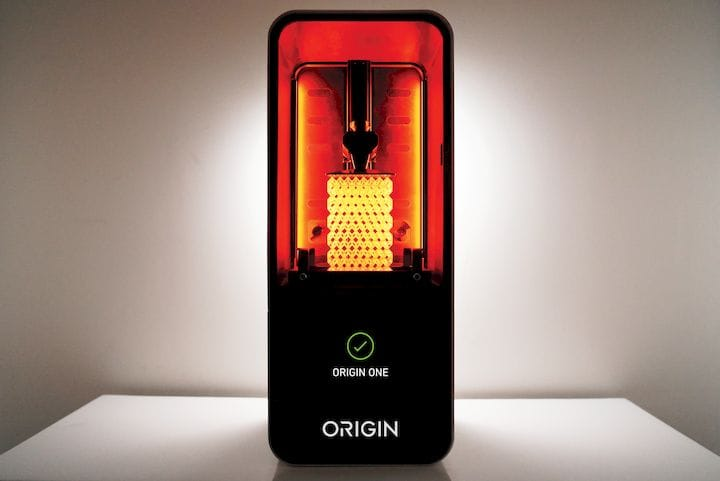
At first glance, you’d be forgiven for thinking the Origin One is simply yet another resin 3D printer. However, the secret of the Origin One lies inside the machine. The company has developed a Programmable Photopolymerisation (P3) technology, which enables high throughput, reduced post-processing and a much larger range of materials to be printed.
How does it work?
Unlike current resin 3D printers, P3 is oxygen-free. Origin’s 3D printer uses an inert gas, allowing the print bed to pull away to build the next layer with extremely little force. By reducing the force, the machine can achieve higher throughput.
Furthermore, Origin says it has been able to significantly reduce the post-processing time required by integrating the curing process inside its 3D printer. With other resin 3D printers, curing usually takes place in a specialised unit, sometimes taking up to several hours.
With P3, parts achieve 99 % of their final properties during printing. Subsequently, they are just cleaned and quickly passed through a final UV curing conveyor system which uses a powerful microwave fusion lamp. The process is said to take no more than five minutes, which is quite remarkable.
Currently, Origin has around 50 validated materials optimised for its P3 process. This has been achieved thanks to Origin’s open material approach, which relies on chemical experts to expand the choice of materials available to users.
Although the company has just started its journey to transform manufacturing, Origin’s recent wave of partnerships with large material companies and shoe manufacturer, ECCO, suggest they have a very promising future ahead of them.
Unleashing the potential of 3D printing
Despite being so diverse, all of the technologies on our list share one common goal: driving 3D printing further from its prototyping origins to full-blown industrial production. To achieve this, the technologies are developed to be faster, more accurate and reliable.
Clearly, it will take some time to see these promises fulfilled. That said, the emerging technologies lay the foundation for pushing 3D printing beyond its current limitations into the bright future.