As additive manufacturing evolves, optimising designs for the technology is becoming ever-more important to unlocking the full potential of the technology.
Complex geometries, lightweight components and optimised material distribution are only a few of the advantages that additive manufacturing offers. However, such design freedom and complexity come at the cost of rethinking the way in which objects are designed for additive manufacturing.
The challenge many engineers face is in adopting an entirely new approach to designing for additive manufacturing. Applying traditional (subtractive) methods to the additive manufacturing is inherently impractical, since the requirements and considerations of both are vastly different. Therefore, understanding the considerations and limitations of AM, such as support structures, post-processing and a range of new materials, will be key to successfully implementing the technology.
So what can you accomplish by making design for additive manufacturing a core element of your AM strategy?
1. Create parts with greater complexity
Additive manufacturing can overcome the limitations of traditional manufacturing methods to create highly complex parts with improved functionality.
One example is the traditional manufacture of injection moulds: here, cooling channels are typically straight, leading to a slower and less consistent cooling of a moulded part. In contrast, with 3D printing the cooling channels can be re-designed to create more complex or curved shapes, providing more homogeneous heat transfer. This results in improved cooling characteristics, helping to produce higher quality parts whilst prolonging the service life of a mould.
2. Minimal material waste
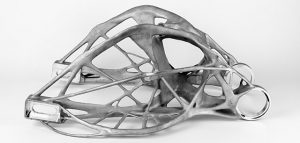
This can be achieved in part thanks to advanced software like topology optimisation, and tools like generative design and lattice structures. Based on mathematical calculations, topology optimisation can help to analyse the best shape for a part and remove unnecessary material without compromising the structural integrity of the part. Using traditional (subtractive) methods, this material would simply be cut away.
Coupled with 3D printing, generative design and topology optimisation software are already used by industrial giants like Siemens and General Motors. While Siemens used generative design software to develop its 3D printed gas turbine blades, General Motors aims to reduce the weight of a vehicle by exploring various options for material distribution within a component.
3. Simplified assembly
Part consolidation is another game-changing design benefit of additive manufacturing. With traditional manufacturing, multiple components must be produced and then subsequently assembled to create the final part.
However, with 3D printing, several smaller components can be integrated into a single custom part during the design stage, allowing you to print the entire part at once. This significantly simplifies the assembly process, and can even eliminate the need for assembly at times. In addition to this, a consolidated part eliminates the need for procuring and storing any additional subcomponents or spare parts, ultimately reducing inventory and maintenance costs.
4. Material innovation
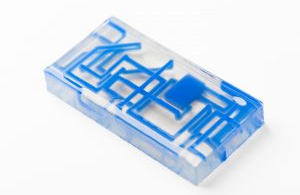
Advancements in materials research have led to the exciting development of new materials. Consequently, unique 3D printing materials have been developed that would be difficult to machine or mould, such as TPU filaments and metal superalloys powders). Or take for example3D printing with high-performance thermoplastics, developed specifically for engineering applications. In some cases, these high-performance materials can even substitute metal parts, providing a lightweight, cost-saving alternative.
Therefore, when designing a part for 3D printing, engineers can explore new options that offer better material properties, such as thermal conductivity or malleability. In addition to this, 3D printing gives an opportunity to design parts withmulti-material properties(e.g. rigidity and flexibility) or integrated insulating and conductive properties.
5. Cost-effective customisation
3D printing enables quick and multiple design iterations at no extra cost, taking customisation possibilities to new heights. And as additive manufacturing creates parts directly from digital files, the manufacturing process is significantly accelerated. This means that companies can produce customised products much faster and cost-effectively.
Customised designs will enable mass customisation across industries, from consumer goods to medical and automotive. For example, in the medical industry, mass customisation is already revealing itself in the 3D printed devices, tailored to the needs of the patient. Such devices range from individualised braces and prosthetics to surgical guides and hearing aids, designed to perfectly match patient’s anatomy.
6. Minimum support structures
Part orientation is one of the key benefits when designing for additive manufacturing. Choosing the correct part orientation during the design stage can reduce the printing and post-processing time whilst minimising the need for supports. In spite of the fact that support structures are virtually a necessity for many complex 3D printed parts, it is ideal to design parts with as few supports as possible, as this will make post-processing easier, saving you time and material.
While there is no a one-size-fits-all solution when it comes to minimising the number of supports used, with careful design a part can often be orientated and optimised to carry itself whilst using a minimum amount of support structures, saving post-processing time.
Looking ahead, as automation trends take hold in the AM industry, part orientation, as well as supports, could be automatically generated with a new generation of AM software.
The Future
Currently, when faced with AM, many designers and engineers are limited by the conventions of traditional manufacturing. However, developing new approaches for AM will be crucial as the technology matures into a robust industrial solution.
For this reason, it will be vital for universities, research institions and companies themselves to develop new educational programmes to support training for DfAM. Much is already being done in this area; for example, Loughborough University has launched its Masters’ programme for additive manufacturing, while there is a range of programmes and courses for those seeking to deepen their knowledge.
As more universities are offering degrees in additive manufacturing, the next generation of AM professionals will be able to forge new trends in the AM industry, particularly in the area of digitisation and automation.
Looking ahead, we anticipate that much of the design for additive manufacturing process will be automated, from design optimisation, validation and process simulation to automatically generated supports and lattice structures.
Ultimately, mastering the design considerations for AM will truly unleash its true potential, enabling the technology to rewrite the rules for product development.