Tungsten is celebrated for its exceptional properties—such as a melting point of 3422°C and superb high-temperature strength—which make it ideal for high-performance applications. However, these very characteristics pose significant challenges in additive manufacturing.
In this article, we explore three leading techniques for 3D printing tungsten: Selective Laser Melting (SLM), Electron Beam Powder Bed Fusion (EB-PBF), and Binder Jetting. We will also compare these methods, discuss their unique challenges, and highlight key factors to consider when processing tungsten.
Technique Overview
Before diving into the details, it is important to understand the basic premise of each technique. Each method has its unique advantages, process requirements, and post-processing steps.
Selective Laser Melting (SLM)
SLM takes center stage when it comes to fabricating high-density tungsten parts. In this process, a high-power laser selectively melts tungsten powder, fusing it layer by layer.
Key Requirements for Tungsten SLM
- High Laser Power: Tungsten’s high melting point demands significantly increased energy input.
- Atmosphere Control: The process is performed in a high vacuum or inert environment (usually argon with very low oxygen) to prevent oxidation.
- Preheating: Elevating the powder bed temperature (typically between 100–400°C) helps reduce thermal stresses and minimizes cracking.
- Optimized Scan Strategies: Slightly defocusing the laser can widen the melt pool, improving interlayer bonding.
- Powder Characteristics and Layer Thickness: Fine, spherical, and well-controlled tungsten powder is essential for good flowability and packing. Thinner layers improve detail but extend build times.
- Post-Processing Steps: These often include removing support structures, high-temperature annealing (1000–1500°C), Hot Isostatic Pressing (HIP at over 2000°C), and CNC machining for refined surfaces.
While SLM excels at producing dense, high-precision parts, another technique—EB-PBF—addresses some of tungsten’s challenges by harnessing elevated process temperatures. Let’s explore that next.
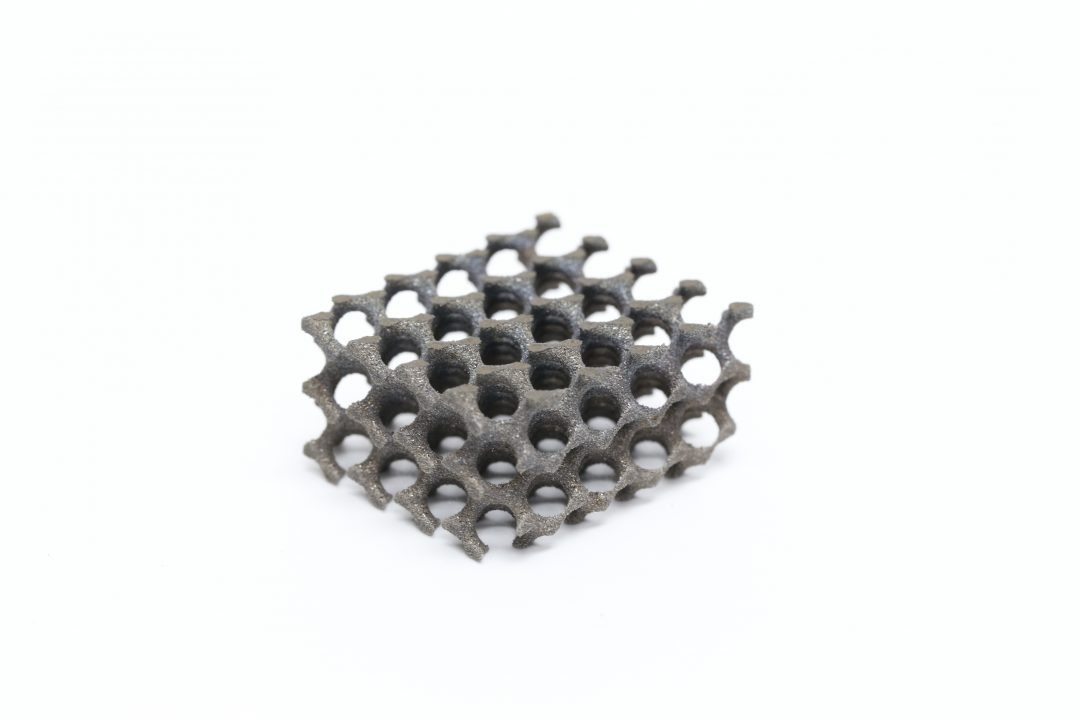
Electron Beam Powder Bed Fusion (EB-PBF)
EB-PBF utilizes a high-energy electron beam in a vacuum to melt tungsten powder. This method offers several distinct advantages:
Key Features of EB-PBF
- Vacuum Environment: Prevents oxidation while supporting high-energy beam operation.
- Elevated Process Temperatures: Operating above 1000°C maintains tungsten’s ductility and minimizes cracking.
- Beam Control: Electromagnetic coils allow for rapid, precise adjustments.
- Powder Flexibility: EB-PBF can use coarser tungsten particles (up to 150 microns) with ease.
- Reduced Residual Stresses: The high processing temperatures help lower internal stresses, resulting in fewer defects.
In contrast to the melting-based processes above, Binder Jetting offers a distinct approach. It is especially promising for larger parts and tungsten composites, although it comes with its own considerations.
3D print Tungsten’s penetrator rounds using EB-PBF technique. Photo credit: HAMR Industries
Binder Jetting
Binder Jetting is a room-temperature process that uses a liquid binder to join tungsten powder particles, forming a “green” part that must later be sintered.
Key Considerations for Binder Jetting:
- Room Temperature Printing: This process significantly reduces energy consumption.
- Sintering Requirement: A high-temperature sintering step is needed to fuse the tungsten particles and achieve mechanical strength.
- Shrinkage Management: Significant shrinkage occurs during sintering, which designers must account for to preserve dimensional accuracy.
- Density and Post-Processing: Although binder jetting typically produces parts with lower densities than SLM or EB-PBF, post-processing (including HIP) can improve this.
- Composite Manufacturing: This method is promising for fabricating tungsten composites (e.g., tungsten-copper) for specialized applications.
- Cost Efficiency: Suitable for larger parts where production speed and lower costs are critical.
Binder Jetting 3D printed Tungsten. Photo credit: Beamler
Comparing the Techniques
To help you assess the best method for your application, the table below summarizes the key differences and considerations for each tungsten 3D printing technique:
Parameter | SLM | EB-PBF | Binder Jetting |
---|---|---|---|
Energy Source | High-power laser | High-energy electron beam | Liquid binder; no direct melting |
Process Atmosphere | High vacuum or inert (e.g., argon) | Vacuum | Ambient (with subsequent sintering) |
Process Temperature | Preheating required (100–400°C) | Operates above 1000°C | Room temperature during build, then high-temp sintering |
Powder Characteristics | Fine, spherical for high flowability | Allows coarser particles (up to 150 µm) | Standard powder; must consider shrinkage |
Residual Stresses | Higher; needs optimization | Lower due to high processing temperature | Managed during sintering and post-processing |
Post-Processing | Annealing, HIP, CNC machining | Minimal (primarily finishing) | Sintering, potential HIP for density improvement |
Application Focus | High precision, high-density parts | Improved ductility and fewer cracks | Cost-effective for larger parts/composites |
Choosing the Right Method
When selecting the appropriate process for 3D printing tungsten, consider the following:
-
Performance Requirements: Need for ultra-high density and precise tolerances points toward SLM or EB-PBF.
-
Part Size and Volume: For larger parts where cost is critical, Binder Jetting may be preferable.
-
Material Combinations: For advanced tungsten composites, Binder Jetting offers promising advantages.
-
Production Speed vs. Quality: EB-PBF can deliver faster build times with reduced cracking, thanks to its inherently high process temperatures.
Applications and Future Prospects
The potential of 3D printing tungsten is vast. Beyond the immediate production challenges, its applications are groundbreaking:
-
Medical and Nuclear Industries: Tungsten is an excellent radiation shield. In medical imaging and nuclear settings, 3D printed tungsten parts can effectively block harmful γ rays, X-rays, and neutrons.
-
Ultra-High Temperature Environments: In nuclear fusion reactors and other extreme-temperature applications, 3D printed tungsten components, fixtures, molds, and electrodes can endure conditions exceeding thousands of degrees Celsius.
-
Electrical Applications: Tungsten-copper contacts produced via 3D printing are highly resistant to electric arcs and wear, making them ideal for high-power electrical connections.
-
Mechanical Systems: In mechanical transmission systems, tungsten alloy counterweights provide precise high-density balancing and excellent vibration damping.
-
Aerospace: Critical components like nozzles and thermal shields in the aerospace industry can benefit from tungsten’s robust performance and high-temperature resistance.
-
Heavy Machine Tools: 3D printed tungsten carbide tools offer extraordinary hardness, making them perfect for machining and cutting challenging materials.
In summary, 3D printing tungsten is more than a technical achievement—it’s a transformative approach that expands the frontiers of additive manufacturing. Whether it’s for precision components, high-performance composites, or cost-effective large parts, the choice between SLM, EB-PBF, and Binder Jetting depends on your specific application needs and process constraints.
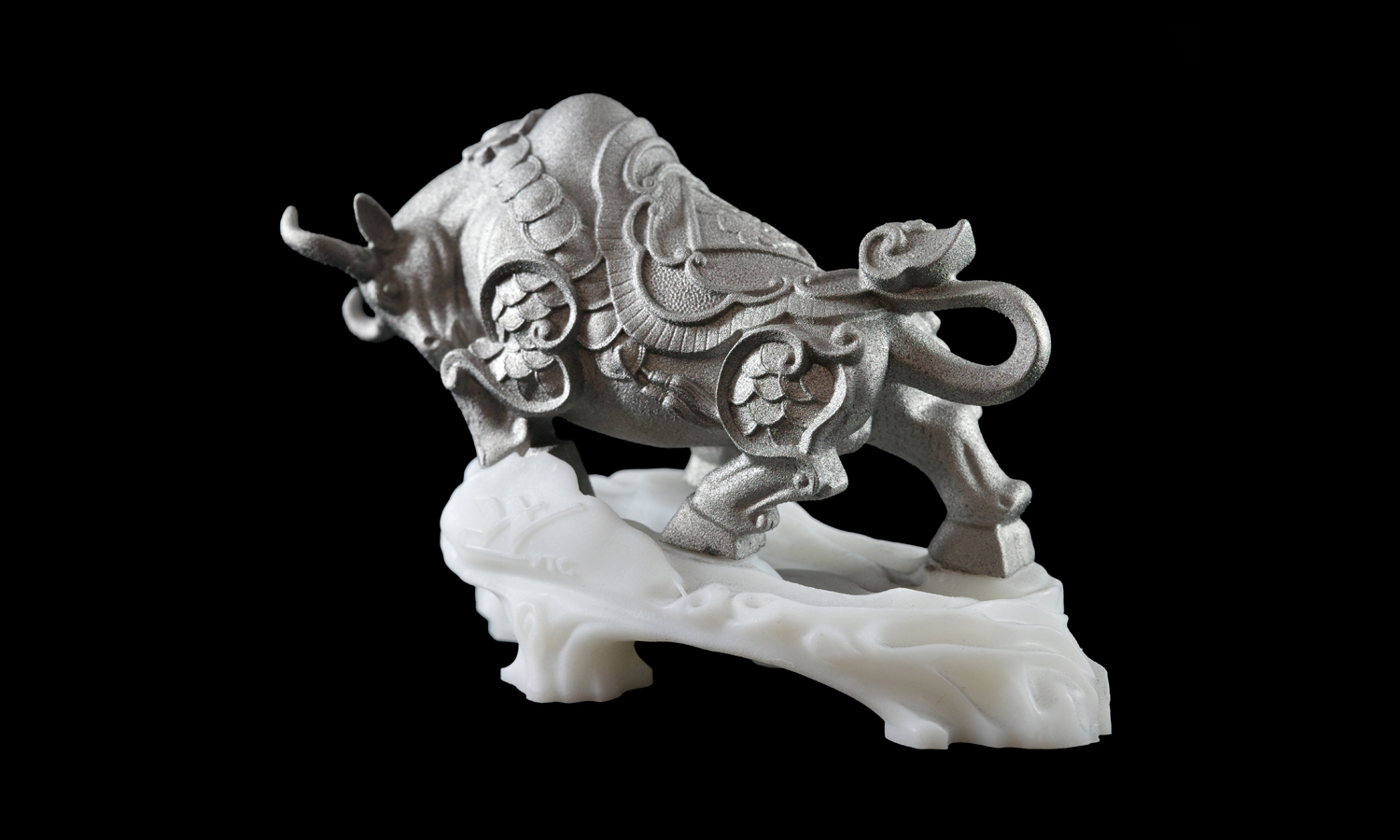
The potential of tungsten is vast—and FacFox is at the forefront of turning that potential into reality. With our state-of-the-art SLM tungsten 3D printing service, we harness the power of high-energy lasers, precise scanning strategies, and optimal process conditions to produce ultra-high-density, resilient components. Whether you’re developing aerospace nozzles, nuclear shielding parts, or high-performance electrical contacts, our SLM process ensures the reliability, precision, and performance your innovative designs demand.
Partner with FacFox to push the boundaries of tungsten additive manufacturing. Experience unparalleled quality and precision, and let us help you turn your boldest ideas into cutting-edge, rugged components that stand up to the most demanding applications. Discover the future of 3D printing with FacFox’s SLM tungsten service—where expertise meets innovation.