Imagine holding a miniature skyscraper in your hand, a perfect replica of a towering metropolis masterpiece. This isn’t magic; it’s the power of 3D printing. By crafting exact, scaled-down models of buildings and their components, engineers are unlocking a new frontier in structural testing. These models can then be subjected to various loads and conditions to evaluate their performance.
Here’s a breakdown of the process:
- Design and Modeling: The building or structural component is digitally designed using specialized software.
- 3D Printing: A scaled-down version of the design is created using a 3D printer. Materials can range from plastics to concrete-like composites.
- Testing: The printed model is subjected to different loads, such as weight, wind, earthquake simulations, or fire exposure.
- Data Analysis: The model’s behavior is observed and analyzed to assess its structural integrity and performance.
Benefits of Using 3D Printed Models for Testing
- Cost-effectiveness: Creating physical models is often cheaper than building full-scale prototypes.
- Time efficiency: 3D printing allows for rapid prototyping and testing.
- Accuracy: Detailed and precise models can be produced.
- Flexibility: Different design iterations can be tested quickly.
- Complex geometries: 3D printing can handle intricate designs that would be difficult to create using traditional methods.
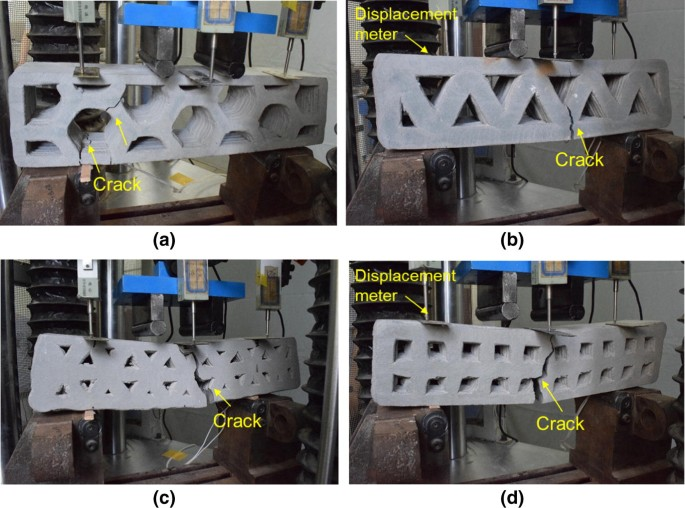
Challenges and Future Developments
While 3D printing offers significant advantages, there are still challenges to overcome. These include:
- Material limitations: Finding materials that accurately mimic the properties of real-world building materials is crucial.
- Scale effects: The behavior of a scaled-down model might not perfectly represent the full-scale structure.
- Testing standards: Standardized testing protocols for 3D printed models are still under development.
Despite these challenges, ongoing research and advancements in 3D printing technology and materials are paving the way for its wider adoption in structural testing.
Materials for 3D Printed Structural Models
The choice of material is critical for accurate representation of real-world behavior. Here are some commonly used materials:
- Plastics:
- ABS, PLA, and Nylon are common choices due to their availability and ease of printing.
- However, their mechanical properties differ significantly from concrete or steel.
- Resins:
- Offer better mechanical properties than plastics but can be more expensive and require specialized printers.
- Digital Light Processing (DLP) and Stereolithography (SLA) are common techniques.
- Concrete-like materials:
- Emerging research focuses on developing printable concrete-like materials to better mimic real-world structures.
- These materials often involve a combination of cement, water, and additives.

Challenges in Scaling
Scaling down a structure introduces complexities:
- Scale effects: Material properties can change at different scales. For example, the strength-to-weight ratio of a material might vary.
- Geometric similarity: Ensuring that the model accurately represents the full-scale structure in terms of proportions and details is crucial.
- Boundary conditions: Simulating real-world support conditions and load applications can be challenging.
Future Applications and Research
The potential of 3D printing in structural testing is vast:
- Topology optimization: Creating structures with optimal material distribution for specific loads
- Material testing: Evaluating new materials and their behavior under different conditions.
- Construction simulation: Simulating the construction process to identify potential issues.
- Disaster response: Rapid prototyping of temporary shelters or bridges.
Research Areas:
- Development of advanced printable materials with properties closely matching real-world materials.
- Improved scaling methodologies to accurately represent full-scale behavior.
- Integration of 3D printing with other testing techniques (e.g. finite element analysis).
- Standardization of testing protocols for 3D printed models.