Prototyping is an indispensable part of the development of new cars. It also costs a lot, both in money and time, for auto manufacturers.
Generally, the development of a new car requires about a hundred times trial production. The value of the prototypes is generally more than 10 times the price of the mass-produced car. Only after multiple rounds of prototyping and trials, design improvement, and technology improvement can lead to the final mass-produced models. The final car model has the best design, reasonable size, good quality, and minimal cost, which can provide a basis for correct market decisions.
As an important driving force of “Industry 4.0”, 3D printing technology has become a general trend for wide applications in the automotive industry. Compared with the traditional manufacturing process, the advantage of 3D printing is that it can directly generate parts of nearly any shape. Currently, it is widely used in automobile research and development, mainly for test models and functional prototypes.
Traditional prototyping method
In the automobile styling process, clay model making is an essential and irreplaceable part. It turns the 2D graphics into a 3D model and presents a very realistic car prototype. The model skeleton is designed based on the CAS data and formed with welding. Then, we glue the foam onto the skeleton, and process the outline with 5-axis CNC machining. Later on, we coat the foam with clay to embellish its surface. The model will be fine-tuned until the engineers and designers are totally satisfied.
Because it mainly relies on manual production, it requires a high technical proficiency for the operator. Not many auto manufacturers can bear the long production cycle and high costs.
The clay for making car models are relatively expensive. So it’s not cost-effective to make the full model with clay. The primary model is cut from a whole piece of foamed plastic to show the basic shape of the car.
A key point is, the size of the primary model should be 3 cm smaller than the expected final dimension. It’s aimed to reserve the space for thick clay coating, also to decrease the sharp edges and corners for the convenience of post-processing.
Then comes the making of the clay models. This part includes applying the clay onto the foamed plastic, rough adjustment, fine-tuning, filming, and painting.
The lights and tires are left to be assembled later.
There are many scales of the car models, like 1:1, 1:4, 1:5, etc. Usually we make scale-down models in the ealier stage and make 1:1 models in the final stage.
A full-scale model means the 1:1 model. Its size is just the same as a new car.
Every full-scale model is produced under strict requirements of shape and dimension.
The full-scale model requires fine adjustments of the surface to make it looks real.
The full-scale model means high simulation. It’s usually assembled with real rims and tires.
Also, all the necessary accessories like lightings, logos, and windows are all put in the right places.
To make the model more look like a real car, we will apply metallic film or spray with metallic paint to form a glossy surface.
Making a full-scale exterior model usually takes 3-4 months while an interior model would take 2-3 months. They have the same process: first making the primary model with foamed plastics, and then apply with clay and adjust the shape.
The interior model requires even higher in detail performance.
Prototyping with 3D Printing
In the design stage, 3D printing can quickly produce conceptual models and functional prototypes, greatly shortening the verification time of automotive parts in the early stage of product development, thereby shortening the development cycle and reducing the cost caused by design.
Traditional prototyping requires at least 2-3 months, while 3D printing can print the product in a few days.
Traditional prototyping relies heavily on the experience of workers. Using 3D printing, the parts with complex structures with high accuracy can be formed in one piece, which can meet the requirements of assembly verification. It has other advantages such as better surface finishes, less post-processing, high simulation and precision. With this new technology, auto manufacturers can greatly improve R&D efficiency.
For consumers’ customization requirements, auto manufacturers can also provide cost-effective solutions using 3D printing technology.
For example, consumers want to personalize a unique car with a distinctive interior and exterior design. If making a new mold with traditional technology, the cost will be astronomical. However, the use of 3D printing for rapid prototyping eliminates the need for additional molds and minimizes the costs. In this way, innovative auto manufacturers can provide customers with innovative experiences at the same price as competitors’ standardized products, thereby gaining a competitive advantage.
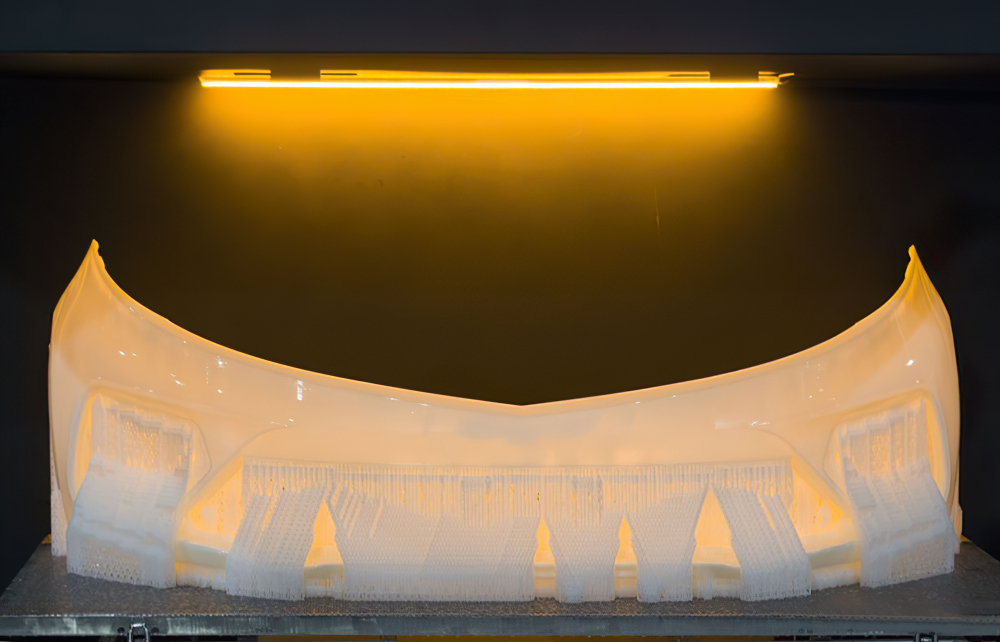
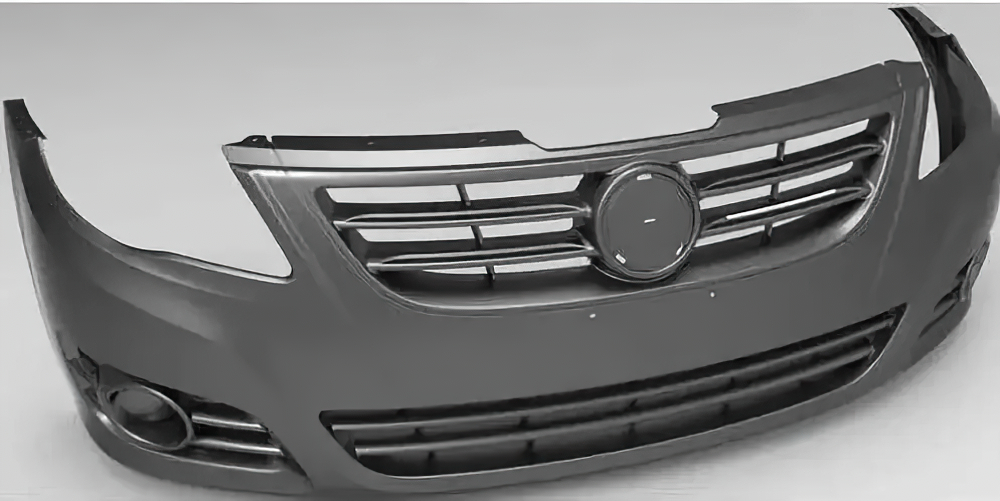
Applications
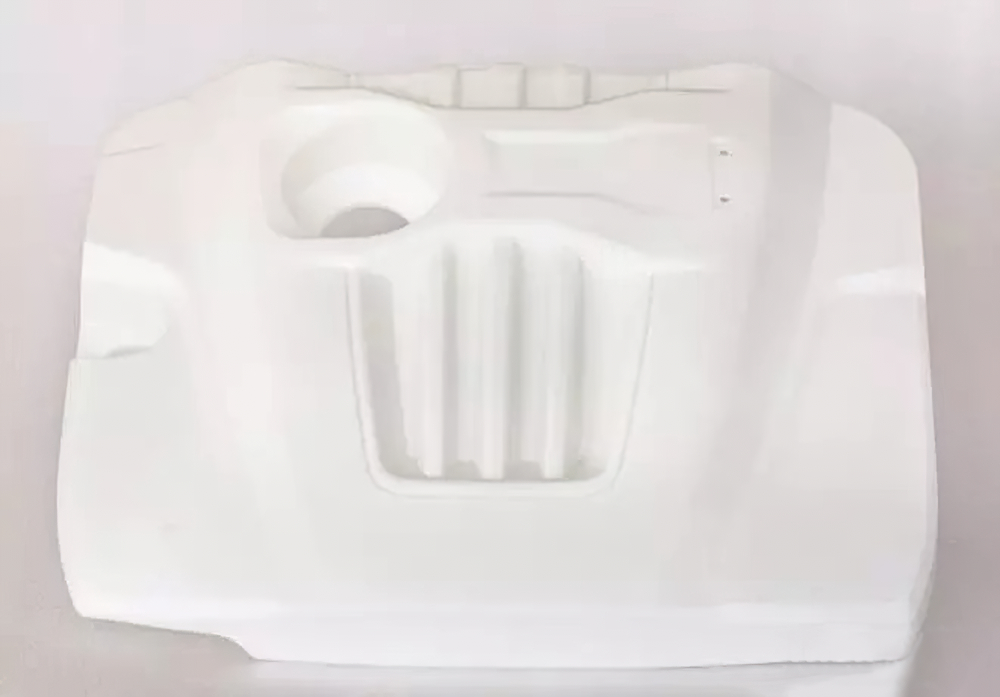
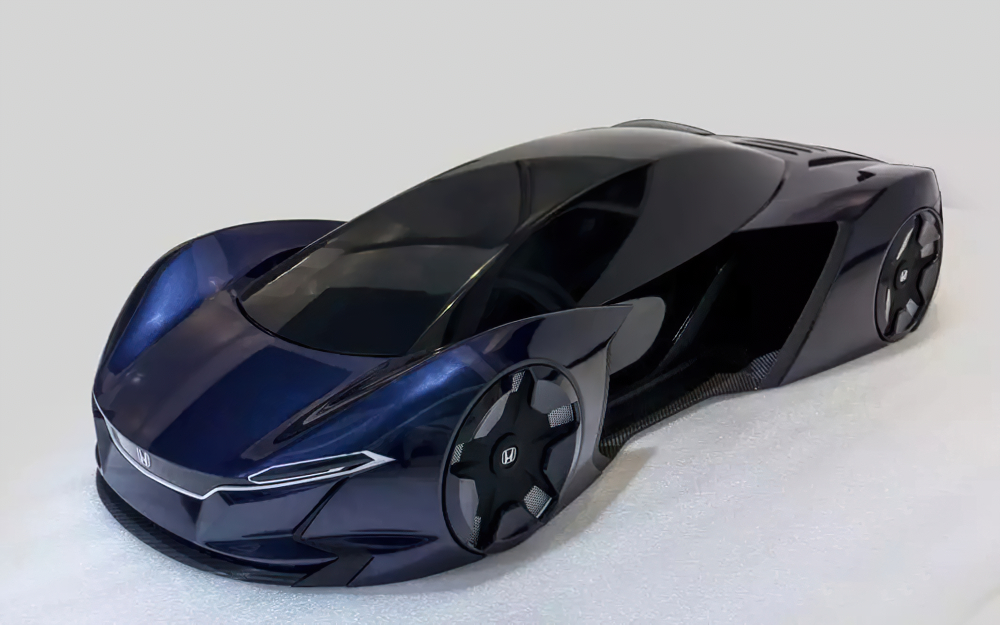
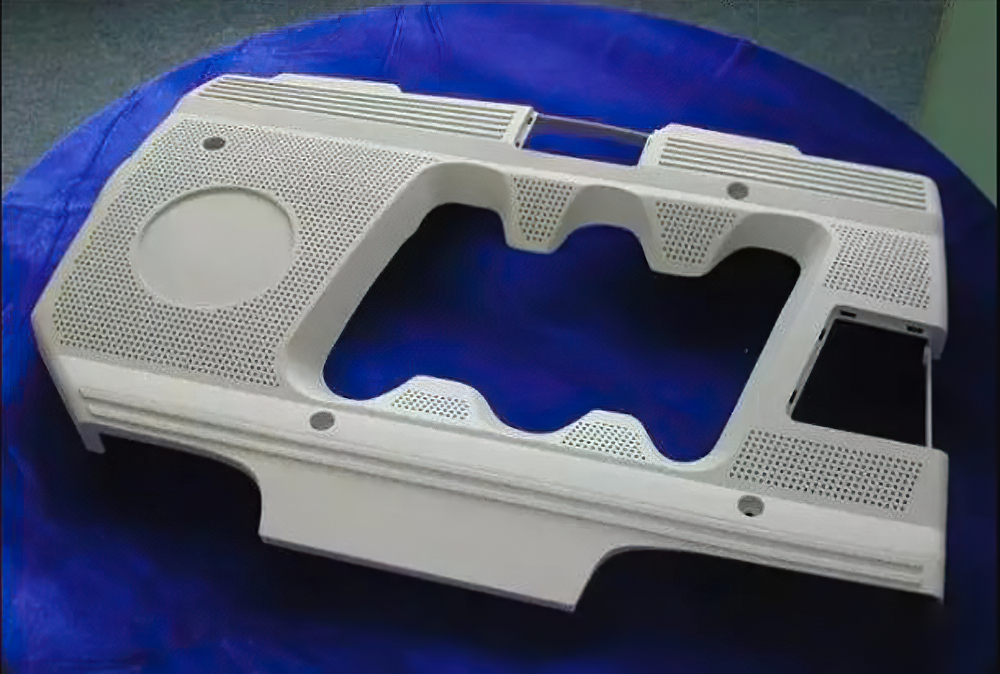