The development of a new wireless earbud is a tale of innovation and precision engineering. For our client, the journey began with a vision to create a product that not only delivers exceptional sound quality but also offers a comfortable and secure fit. The heart of this vision was the PCB holder part, a small yet complex component that would house the critical electronic circuitry.
Understanding the importance of this component, our client approached FacFox with a challenge: to produce three samples of the most intricate part of the earbud, each using different manufacturing methods and materials. The goal was to determine the best production technique that balances quality, cost, and time efficiency.

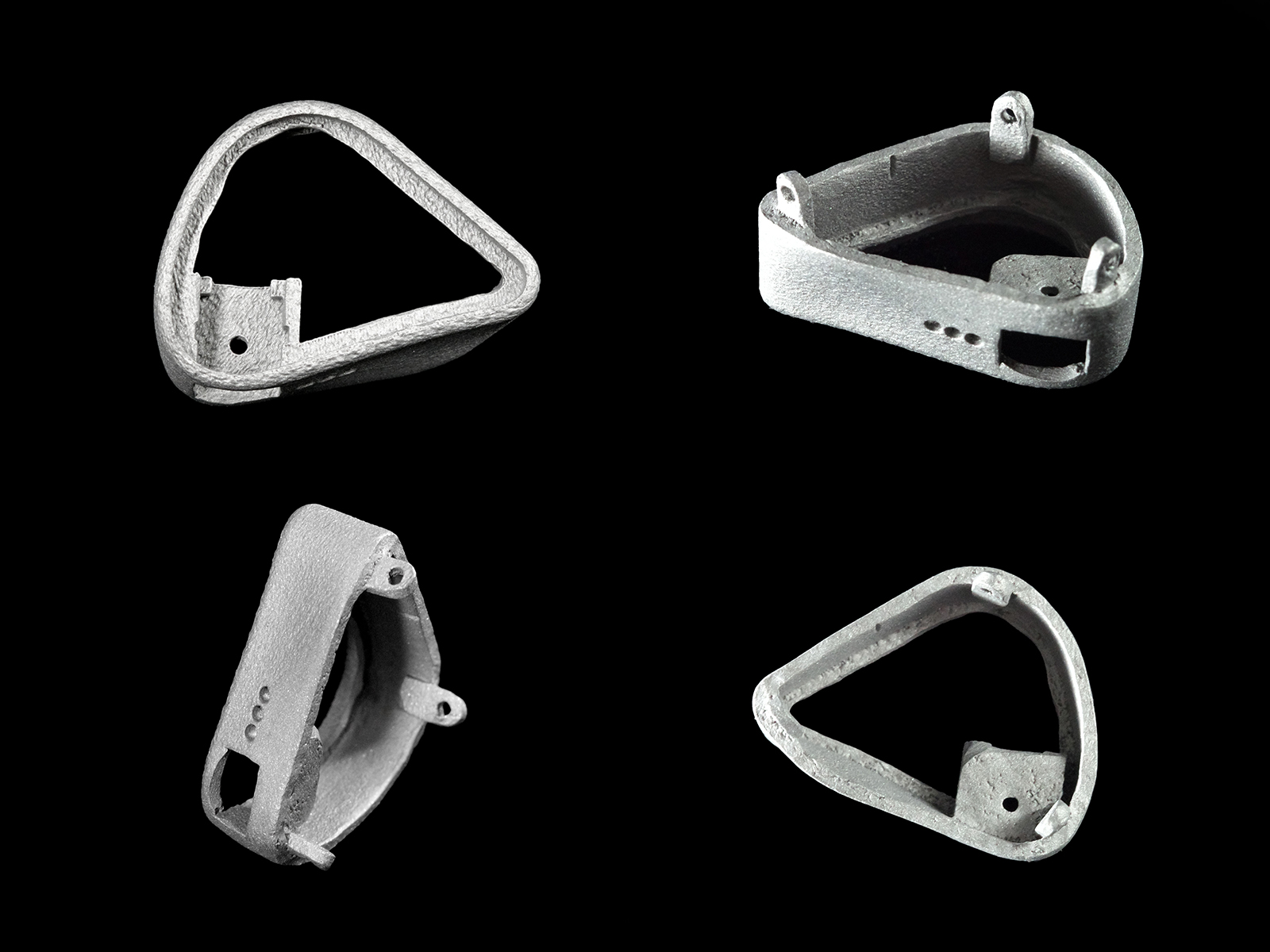
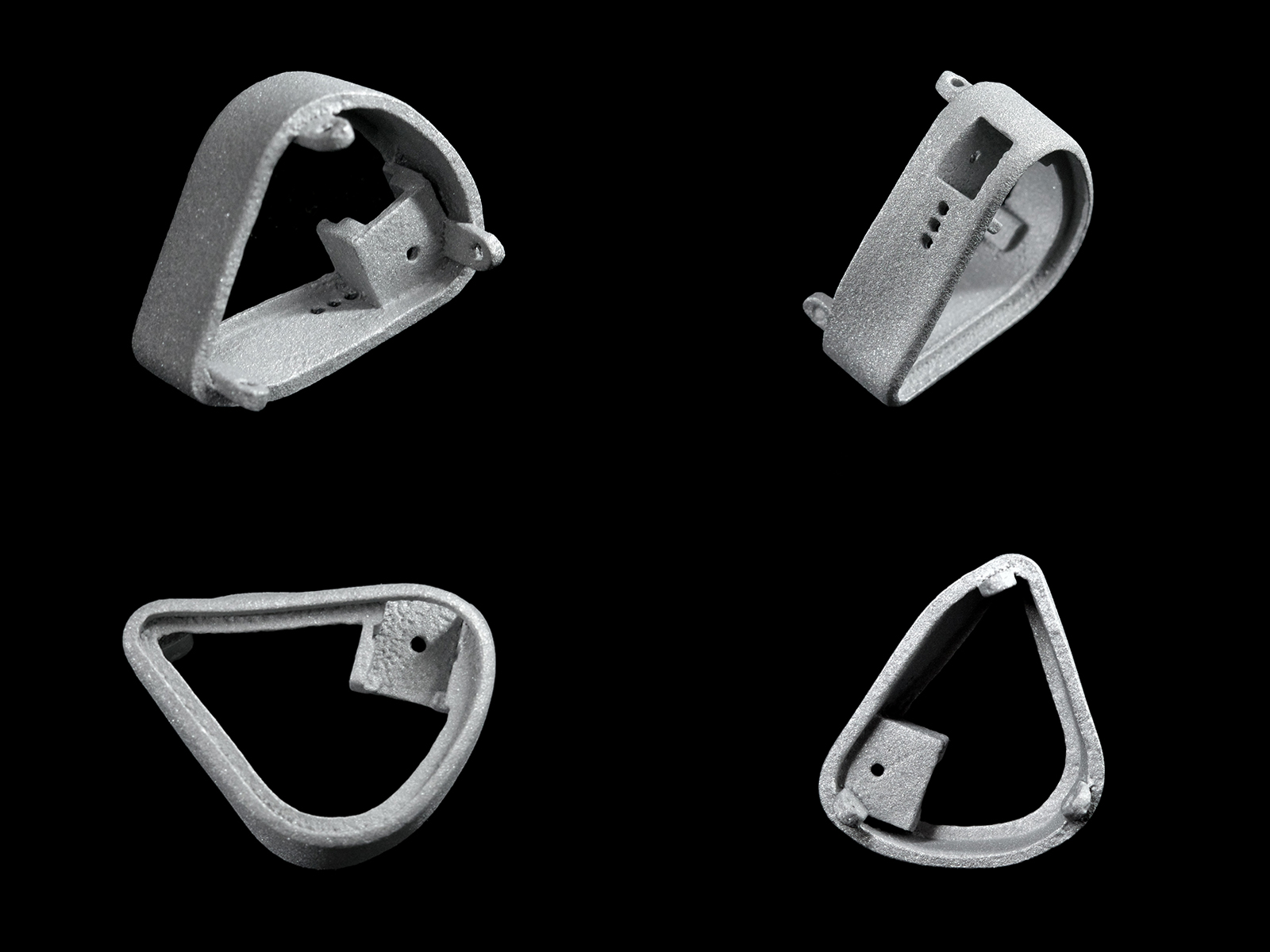
The Prototyping Phase:
FacFox’s team of engineers and designers sprang into action, meticulously planning the production of the three samples. The first sample was to be CNC milled from aluminum alloy, a material known for its lightweight and durable properties. The second and third samples were to be created using DMLS 3D printing, one in aluminum alloy and the other in stainless steel, to explore the capabilities of additive manufacturing.
As the CNC milling machine carved out the aluminum block with precision, it was clear that this method would set the benchmark for quality. The resulting part boasted a smooth surface, with every hole and hollow precisely as designed. The small protrusions, crucial for attaching the part within the earbud’s shell, were sharp and well-defined.
The DMLS 3D printed samples told a different story. While they embodied the desired shape, the surface quality couldn’t match that of the CNC milled part. The aluminum alloy sample had a matte texture, and the stainless steel part exhibited a rough and porous surface, with minor deformations affecting the overall precision.
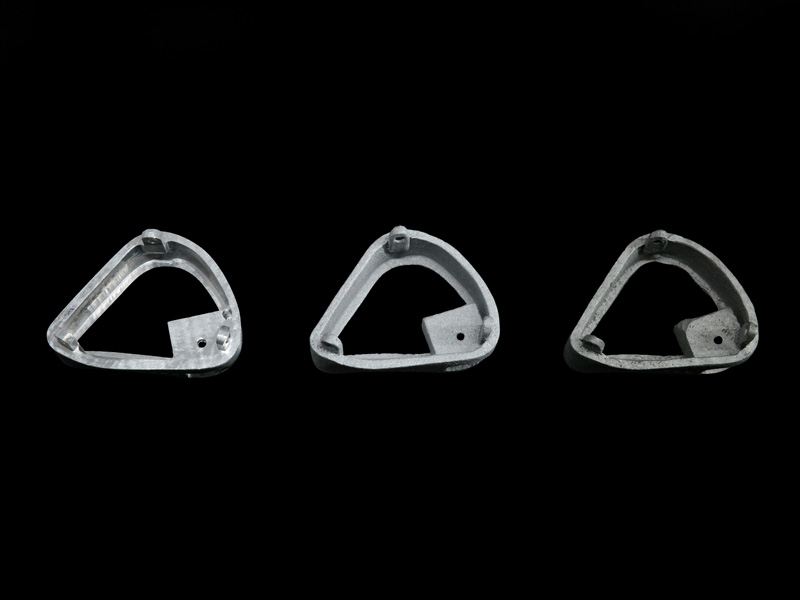
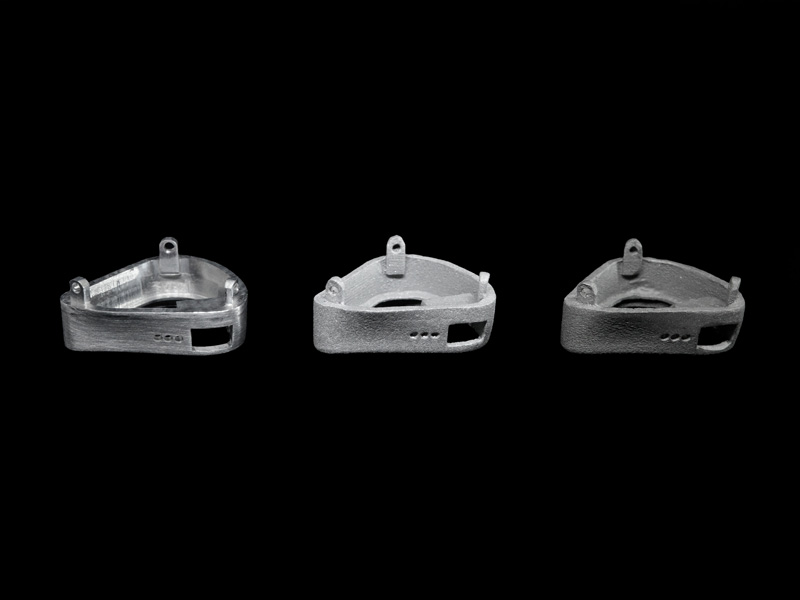
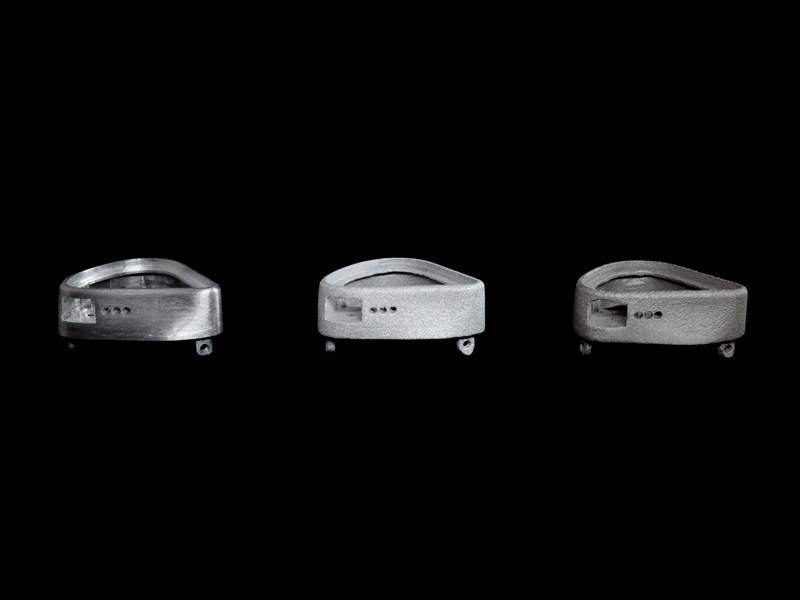
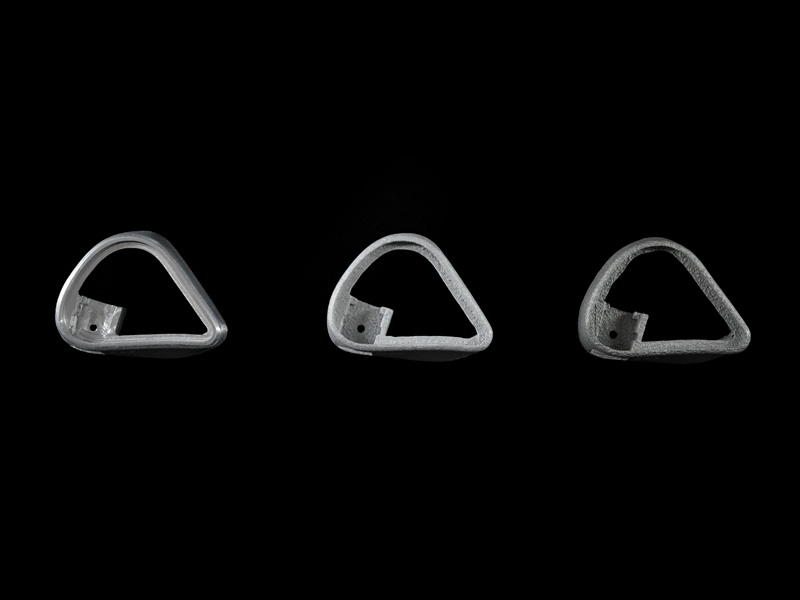
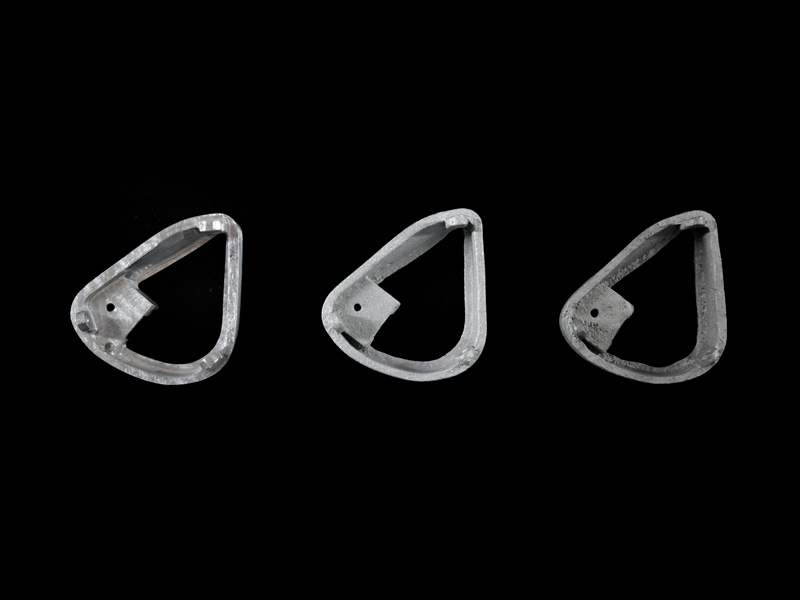
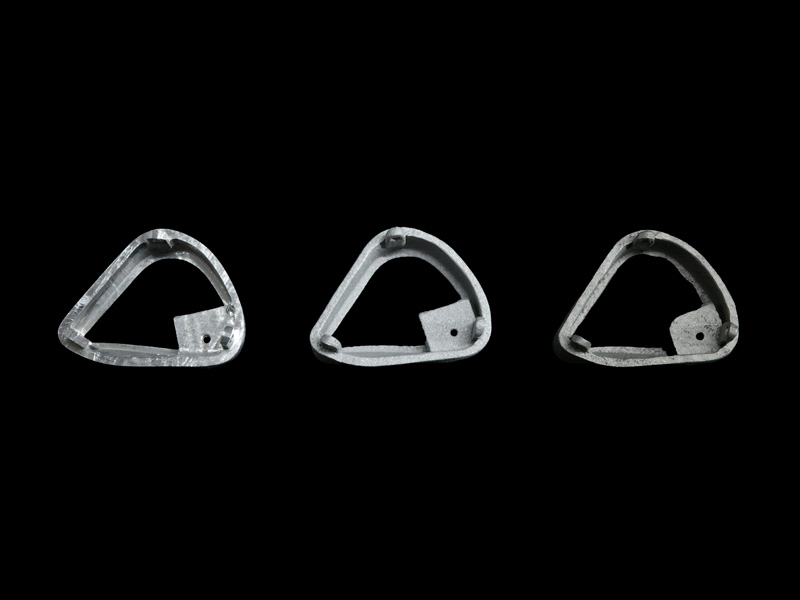
The Decision-Making Process:
CNC Milled Aluminum Alloy: The CNC milled sample made from aluminum alloy demonstrated superior surface quality. With its smooth finish and precise detailing, it stood out as the best option for manufacturing complex prototypes. The round holes and square hollow were cleanly executed, and the small protrusions on either side of the shell served as perfect attachment points.
DMLS 3D Printed Aluminum Alloy: The DMLS 3D printed sample in aluminum alloy, while still maintaining a complex shape, had a rougher surface with a matte texture. The granular and uneven finish was noticeable compared to the CNC milled sample, though it still held its shape well.
DMLS 3D Printed Stainless Steel: The stainless steel sample produced through DMLS 3D printing showed the roughest surface of the three. The material’s porous nature led to a less precise finish, with one hole not being perfectly round and an overhang bridge deformed, indicating that DMLS 3D printing with stainless steel may not be the ideal choice for projects requiring high precision and surface quality.
Armed with the three samples, our client faced a decision. Each method had its merits, but for a product where every detail mattered, the choice became clear. CNC milling with aluminum alloy emerged as the champion, offering the best surface quality and precision—a testament to the craftsmanship and technological prowess of FacFox.
The Final Touch:
With the prototype phase complete and the manufacturing method decided, FacFox was ready to move forward with full-scale production. Their commitment to excellence ensured that each earpod part would be crafted with the same attention to detail as the samples, promising a final product that would exceed expectations.