Surface finishing is an important aspect of CNC machining that can enhance the quality and performance of your parts. In this post, we will introduce some of the types and benefits of surface finishing for CNC milling.
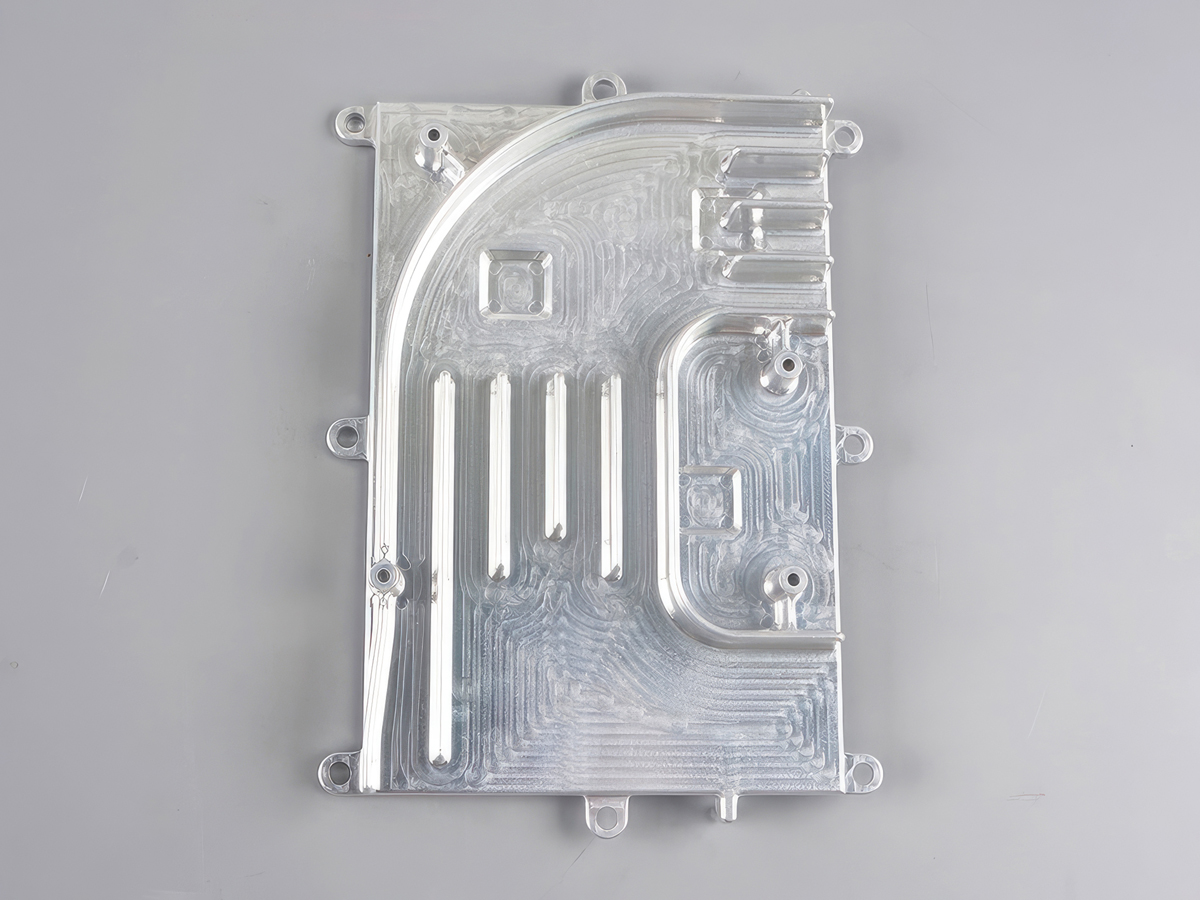
What is surface finishing?
Surface finishing is the process of applying a coating, treatment, or texture to the surface of a part after it has been machined. Surface finishing can improve various properties of a part, such as:
- Appearance: Surface finishing can make a part look more attractive, professional, or customized by adding color, gloss, or patterns.
- Durability: Surface finishing can increase the resistance of a part to corrosion, wear, abrasion, impact, or fatigue by creating a protective layer or reducing friction.
- Functionality: Surface finishing can modify the electrical conductivity, thermal conductivity, magnetic properties, or chemical compatibility of a part by changing its surface composition or structure.
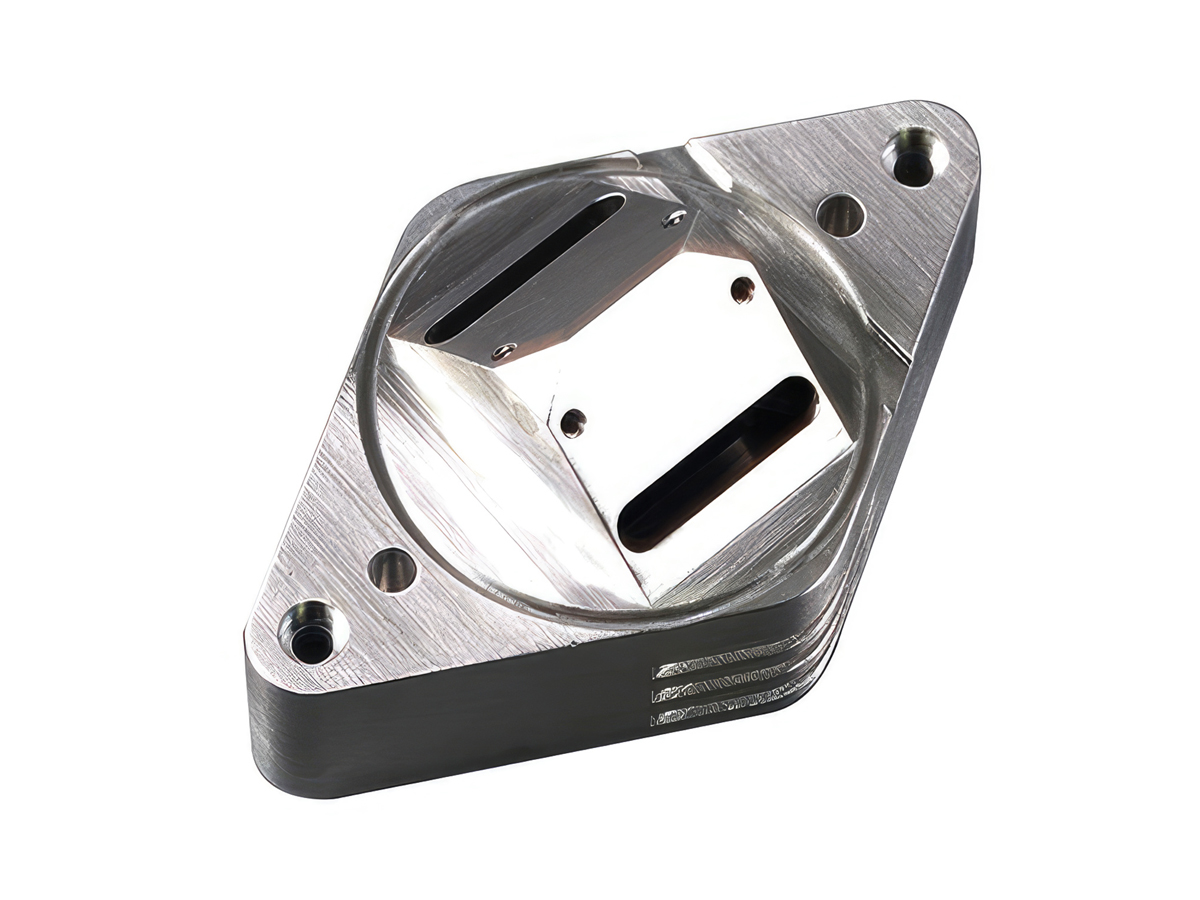
What are common types of surface finishing for CNC milling?
There are many types of surface finishing for CNC milling that can be classified into three categories:
Primary finishes
These are the finishes that result from the machining process itself. They depend on factors such as tool geometry, feed rate, spindle speed, and cutting fluid. Primary finishes affect the roughness and accuracy of a part’s surface. Examples include:
- As-machined finish, which leaves visible tool marks
- Smooth finish, which removes most tool marks
- Mirror finish, which creates a highly reflective surface
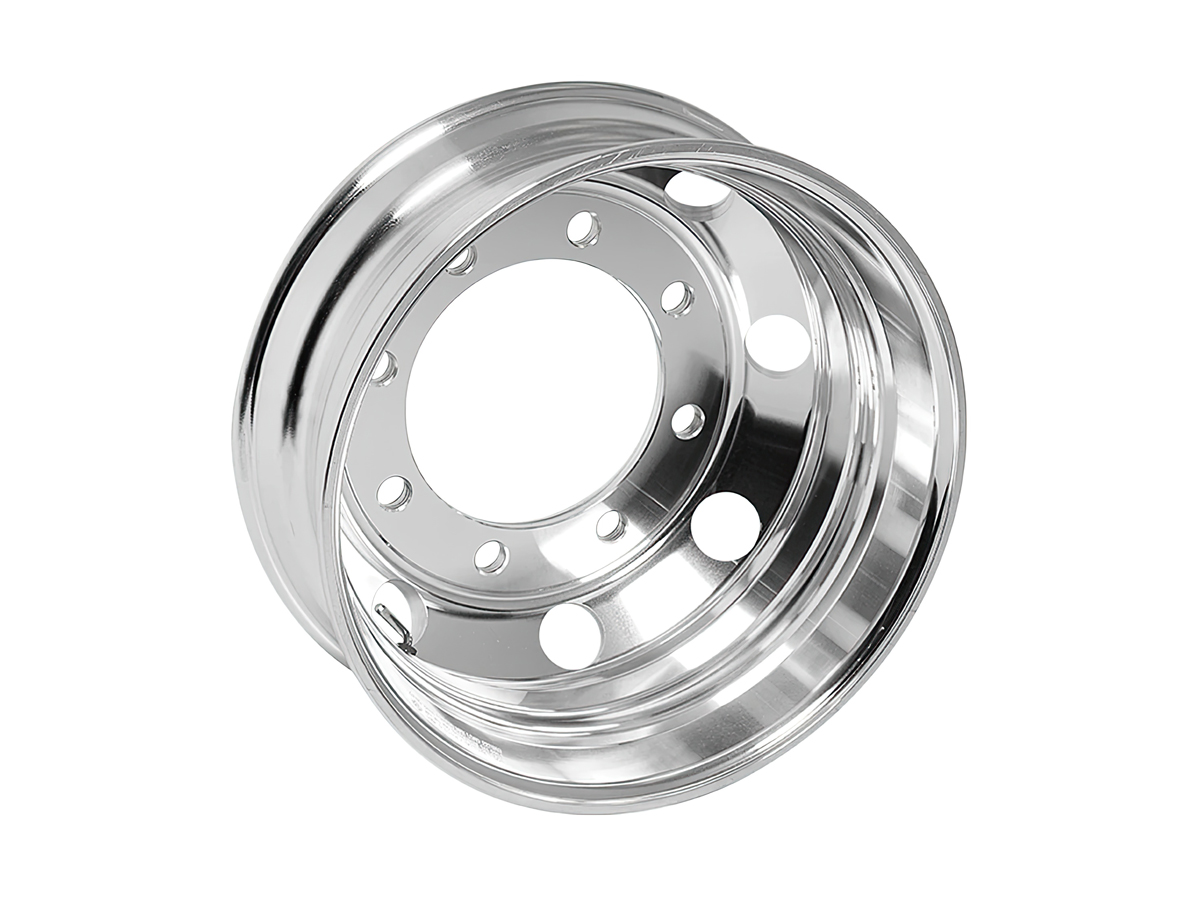
Secondary finishes
These are the finishes that are applied after machining by using additional processes such as blasting, sanding, polishing, lapping, etc. Secondary finishes can further smooth out or roughen up a part’s surface depending on the desired effect. Examples include:
- Bead blasting, which creates a matte texture
- Wet sanding, which removes scratches and burrs
- Fire polishing, which melts away irregularities
- Vapor polishing, which produces a clear and glossy surface
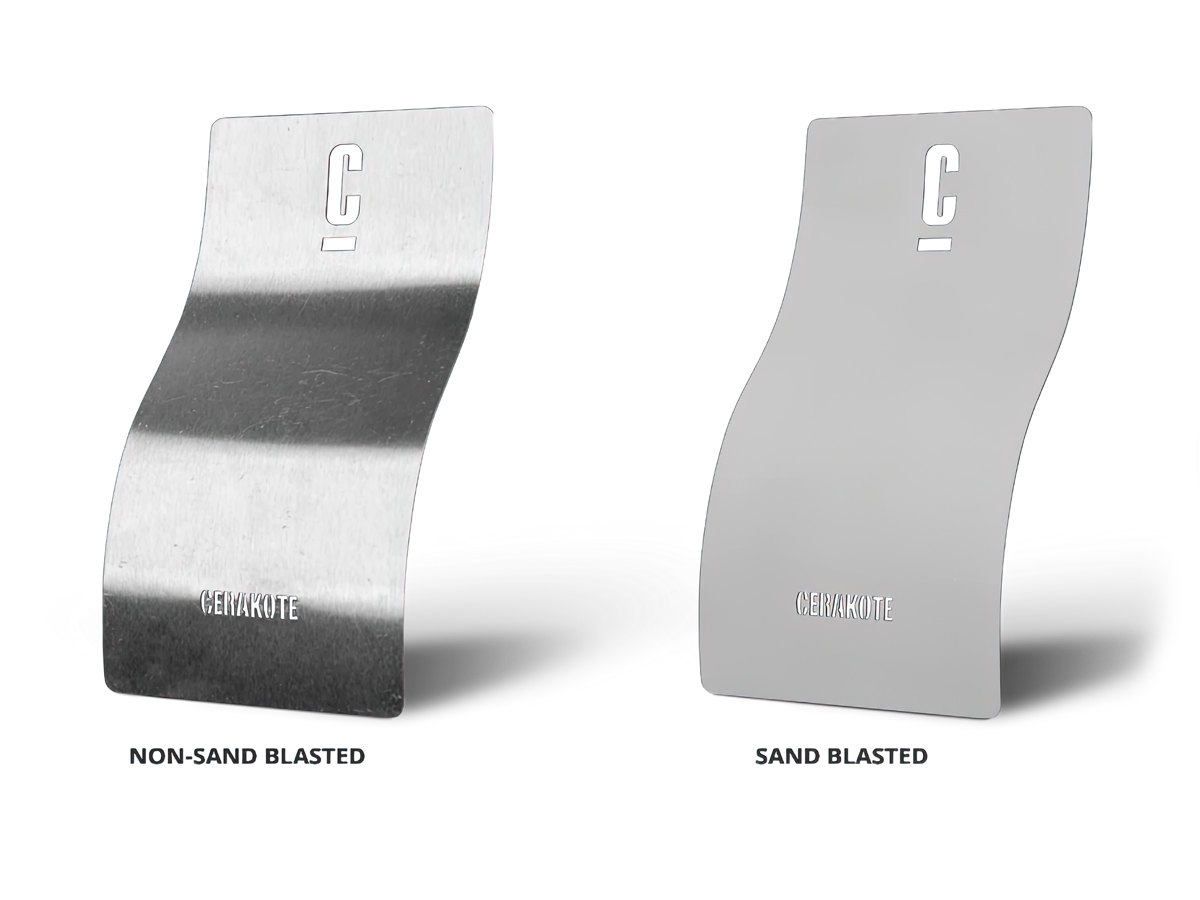
Tertiary finishes
These are the finishes that involve chemical or physical treatments that alter the surface layer of a part. Tertiary finishes can provide various benefits such as coloration, protection, lubrication, etc. Examples include:
- Anodizing, which creates an oxide layer that adds color and corrosion resistance
- Plating, which deposits a metal coating that improves wear resistance and electrical conductivity
- Painting, which applies a liquid coating that enhances appearance and durability;
- Powder coating, which applies a dry powder coating that forms a hard and uniform layer.
How to choose the right type of surface finishing for CNC milling?
The choice of surface finishing for CNC milling depends on several factors such as:
Material
Different materials have different characteristics and compatibility with different types of finishes. For example,
- Metals can be anodized (aluminum), plated (steel), painted (iron), powder-coated (zinc), etc.
- Plastics can be polished (acrylic), vapor polished (polycarbonate), painted (ABS), powder-coated (nylon), etc.
- Wood can be sanded (pine), stained (oak), varnished (maple), lacquered (walnut), etc.
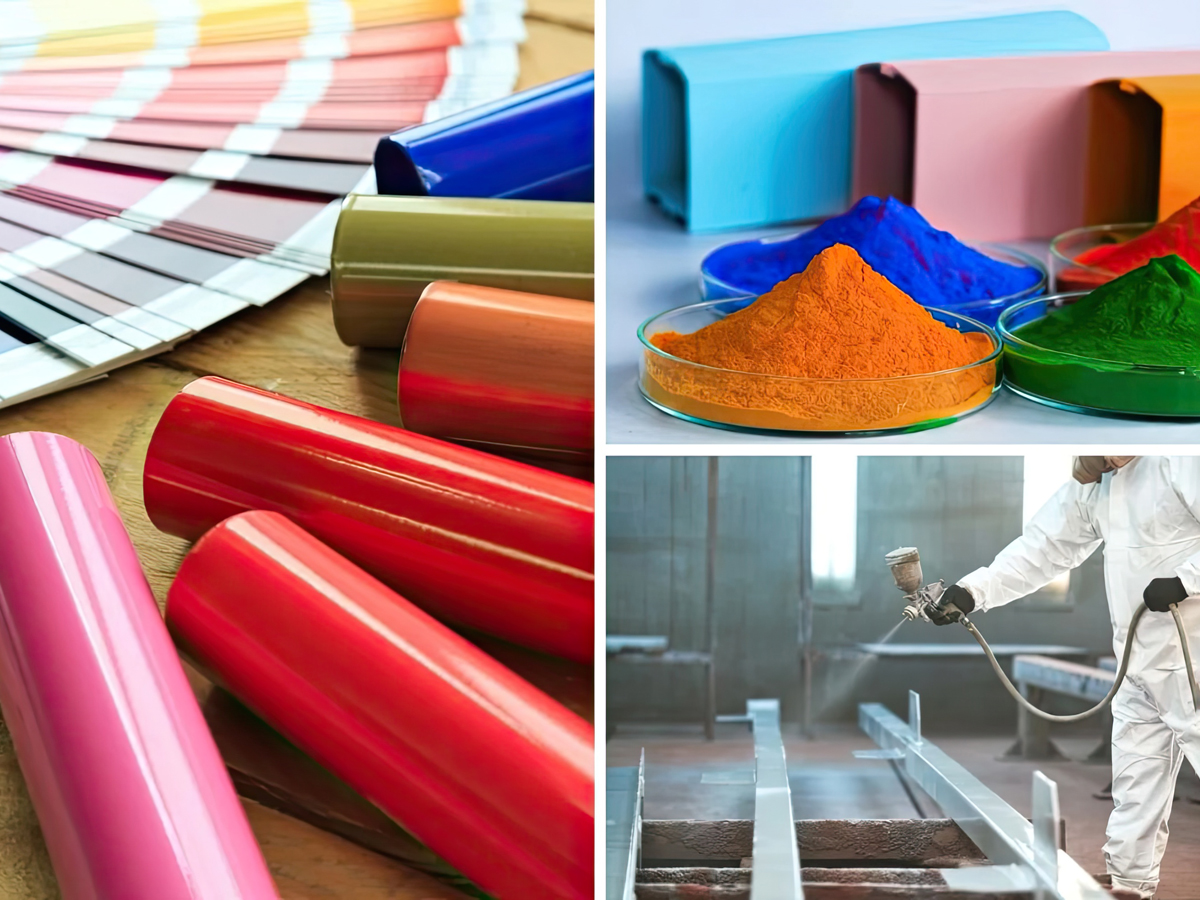
Design
Different designs have different requirements and constraints for different types of finishes. For example:
- Complex shapes may need more flexible or conformal finishes such as painting or powder coating.
- Fine details may need more precise or delicate finishes such as polishing or lapping.
- Large surfaces may need more economical or efficient finishes such as blasting or sanding.
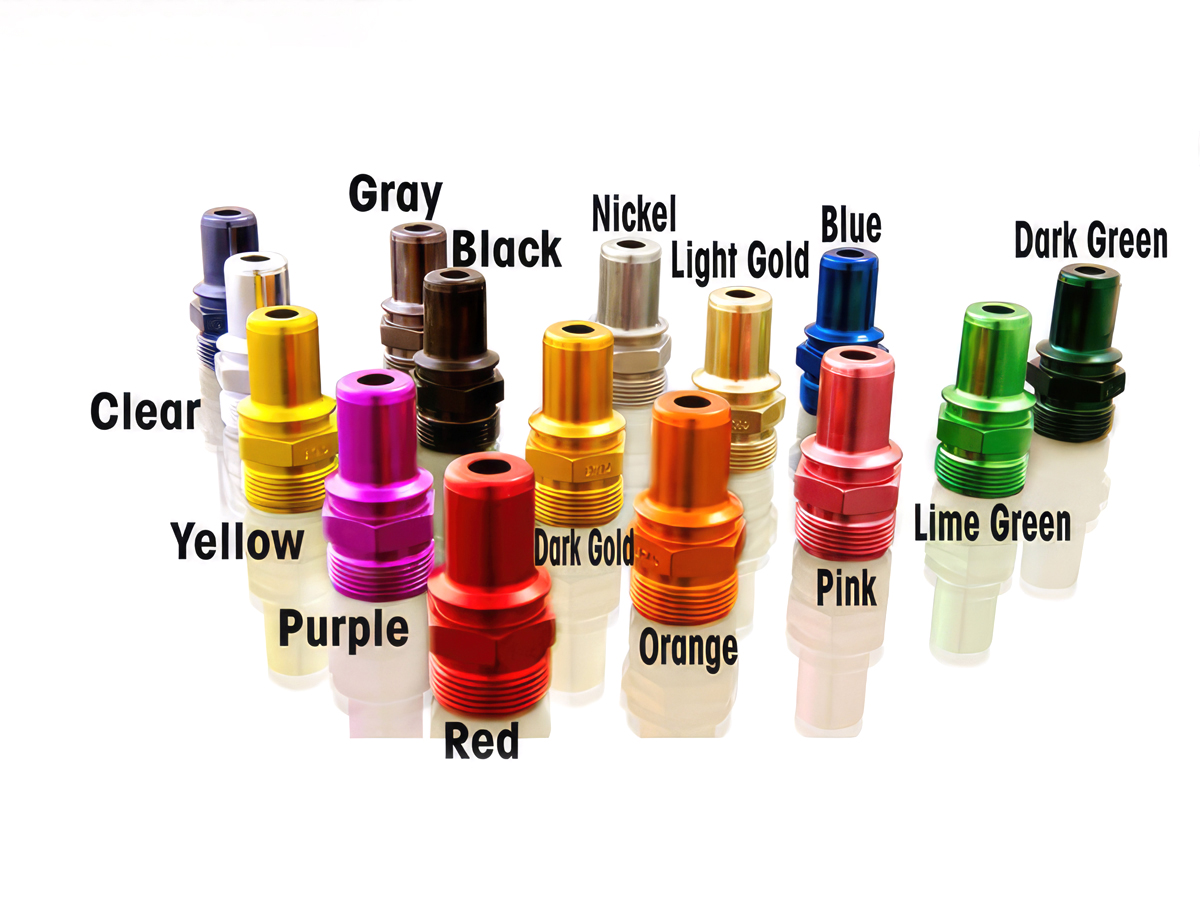
Application
Different applications have different expectations and specifications for different types of finishes. For example:
- Aesthetic parts may need more attractive or customizable finishes such as anodizing or painting.
- Functional parts may need more durable or performance-enhancing finishes such as plating or powder coating.
- Medical parts may need more biocompatible or sterilizable finishes such as polishing.
These are some general guidelines for choosing the right type of surface finishing for CNC milling. However, the final decision should also consider other factors such as cost, availability, and environmental impact.

Conclusion
Surface finishing is an essential step in CNC machining that can improve your parts’ quality and performance in various ways. If you need high-quality CNC milling parts, then FacFox is your best choice.
FacFox not only offers accurate and fast CNC milling service, but also provides various surface finishing services to give your parts the ideal appearance and performance. Whether you need brushing, bead blasting, chrome plating or any other surface treatment, FacFox can meet your needs.
FacFox has a professional team of engineers to provide you with optimized design and technical support. FacFox also offers an online quotation and order tracking system, so you can always know the progress of your project. Don’t hesitate, contact FacFox now and let us create perfect CNC milling parts for you!