Multi Jet Fusion 3D printing, invented by HP, is quickly becoming the additive manufacturing method of choice for a wide range of industries.
As a technology, Multi Jet Fusion (MJF) is a relative newcomer to the 3D printing scene. Despite its freshness, in just a few years MJF has started moving toward industrial-scale maturity – if it isn’t there already.
To understand if Multi Jet Fusion right for your 3D printing needs you need to understand the technology pros and cons and how to unlock its full potential. In this article, we will cover the basics of what Multi Jet Fusion 3D printing is capable of.
The Basics of Multi Jet Fusion Printing
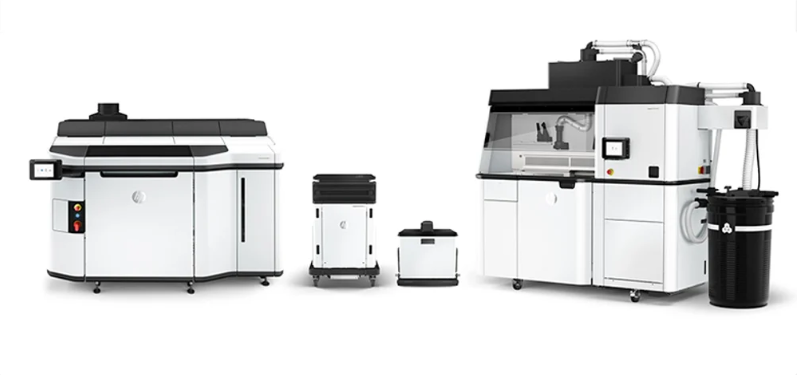
Multi Jet Fusion is a powder bed fusion 3D printing technology introduced to the market by HP in 2016. The company explains its technology is built on decades of HP’s investment in inkjet printing, jettable materials, precision low-cost mechanics, material science, and imaging.
The technology gets its name from the multiple inkjet heads that carry out the printing process. The processes of material recoating and agent distribution and heating are carried out by separate head arrays that move across the print bed in different directions, thus allowing the user to optimize both processes independently.
The 3D file to be printed is rendered as voxels – or volume elements. Voxels are essentially three-dimensional equivalents of pixels that 2D printing relies on.
Just as in 2D printing, where pixels are either printed or not, in Multi Jet Fusion printing, the voxels are either fused into the final print or they aren’t. Another principle carried over from 2D printing into Multi Jet Fusion is the use of color – a full-color-ready Multi Jet Fusion printer can mix inks to produce colored voxels, just like a 2D printer produces color on a page.
Don’t confuse HP’s Multi Jet Fusion with its Metal Jet printing process used in its metal printers, which is very similar and uses metal powder instead of plastic. Our focus here is the Multi Jet Fusion, which only uses plastics.
The Multi Jet Fusion Process
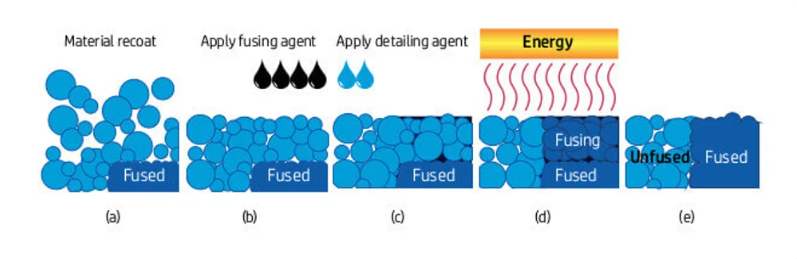
In the Multi Jet Fusion printing process, the printer lays down a layer of material powder on the printing bed. Following this, an inkjet head runs across the powder and deposits both a fusing and a detailing agent onto it.
An infrared heating unit then moves across the print. Wherever a fusing agent was added, the underlying layer melts together, while the areas with detailing agent remain as a powder. The powdery parts shed off, which produces the desired geometry. This also eliminates the need for modeling supports, as the lower layers support those printed above them.
HP says that a Multi Jet Fusion printer differs from most other 3D printing technologies in that each new material and agent layer is placed while the previous layer is still molten. This lets both layers fuse completely, delivering improved print durability and finer detail.
To finish the printing process, the entire powder bed – and the printed parts in it – are moved to a separate processing station. Here, the majority of the loose unfused powder is vacuumed up, allowing it to be reused instead of producing excess waste.
Industries Using Multi Jet Fusion
Multi Jet Fusion is a versatile technology that has found use in several industries across the board. It has helped manufacturers in all parts of their development processes, from prototyping to parts production and internal housing design.
Some industries that have found success with MJF include:
AUTOMOTIVE
MJF 3D printing is helping car and vehicle manufacturers reduce costs in parts production while boosting operational efficiency. A Spanish parts supplier (Continental Automotive Spain S.A.) for the automotive sector used MJF printing to develop a pneumatic gripper that helped them cut down on time when tooling new parts. At Jaguar Land Rover, car engineers are using HP Multi Jet Fusion to make brackets and interior trim for production vehicles. General Motors’ new 15,000-square-foot Additive Industrialization Center counts HP MJF machines among its 3D printing fleet for prototype part, tools, fixtures, and end-use parts.
MEDTECH
The benefits of 3D printing and digital manufacturing during the pandemic continue to grow, bridging supply chain gaps and increasing speed of design-to-part. HP and its global network of partners and customers have 3D printed well over five million parts to fill urgent needs and convene new ecosystems that enable local manufacturing.
The medical and dental industries are experiencing an explosion of new 3D printed applications and mass personalization. The SmileDirectClub in Nashville, Tenn., has a 60 HP Multi Jet Fusion printers working round the clock to make customized dental molds. HP Jet Fusion 3D printers are also changing the orthotics industry and enabling the production of customizable medical prosthetics.
OVR Technology produces gadgets enabling the use of smell in virtual reality, targeting mainly the medical and therapeutic sectors. They were able to produce durable, highly detailed housings with complex geometry for their prototypes using MJF printers.
CONSUMER GOODS
Many types of consumer goods require the production of low volumes of parts in complicated shapes. PepsiCo, one of the world’s leading food and beverage companies, found this out the hard way when they tried to design a small mask to go over drink cans as part of their product tie-in with the Black Panther movie.
The company tested various 3D printing technologies to replicate the fine details and the deep black color of the famous superhero’s mask. In the end, MJF came on top with the high production speed and durability it could provide.
HP also works with customers in the sporting goods and eyewear industry. Using Multi Jet Fusion, Oakley is reducing the product development stages of its eyewear selection as well as other athletic equipment.
Pros & Cons of Multi Jet Fusion
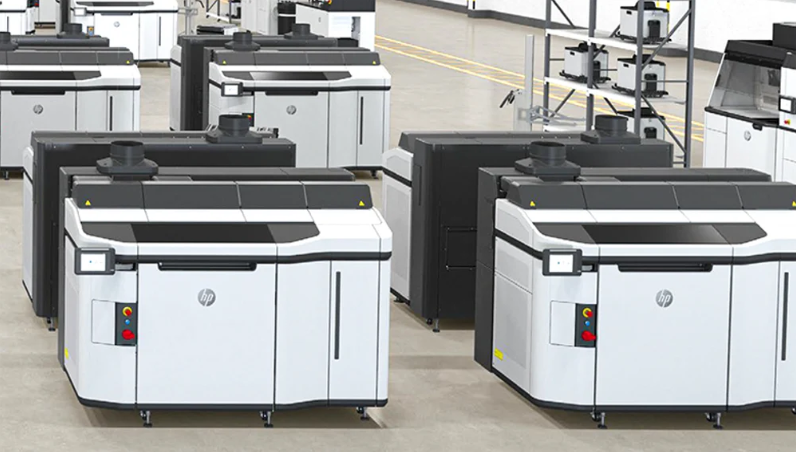
PROS:
- Fast printing speed and production cycle
- Accurate printing for fine details
- Low individual print cost
- Design freedom as no supports are needed
- Little warping in final print
- Less waste due to powder recycling
- Ability to produce colored parts
- High-quality surface finish
- Consistent mechanical properties
- High chemical resistance
- HP’s propertiary polypropylene
CONS:
- Expensive initial printer investment
- Unable to produce some curved, hollow geometries
- Final product is a blotchy gray without dying agents
- Small raised text and cosmetic parts might be lost in post-processing
Materials for Multi Jet Fusion
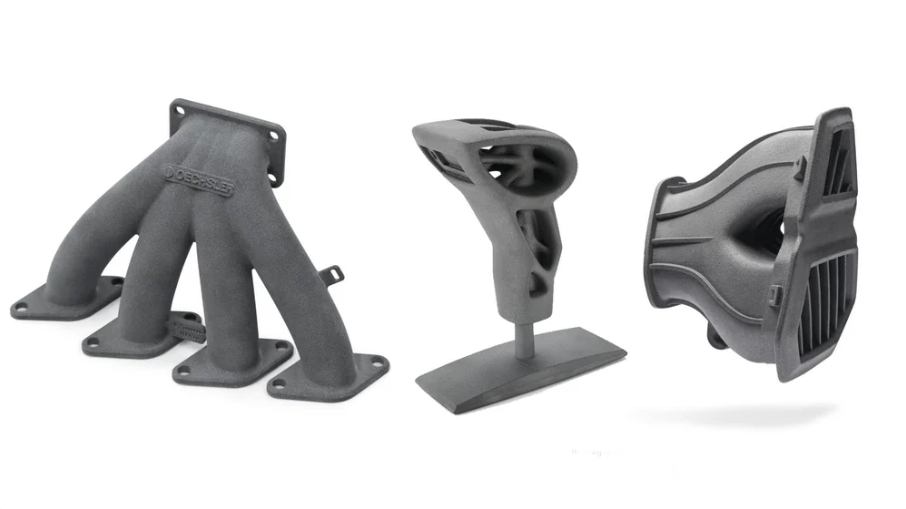
Initially, Multi Jet Fusion was only compatible with Nylon PA 12 powders. Although this is still the most common option, the breadth of available materials has expanded in the few years the technology has been on the market, with new ones still in development. Although Multi Jet Fusion is a type of powder bed fusion that doesn’t mean all powder bed compatible materials will work with MJF. In fact, the material list for MJF is much shorter than powder bed fusion, in part because it’s a propertiary HP process, but material manufacturers are responding the MJF’s growing popularity. In fact, in 2020 HP worked with BASF to develop a new durable and chemical-resistant polypropylene.
MJF-COMPATIBLE MATERIALS INCLUDE:
- High Reusability (HR) PA 12 Nylon
- HR PA 12 Glass Bead (GB)
- HR PA 11
- Estane 3D TPU – M95A from Lubrizol
- Ultrastint TPU01 from BASF/Forward AM
- TPA from Evonik/HP
- Vestosint 3D Z2773 PA 12 from Evonik/HP
Full-Color Printing With Multi Jet Fusion
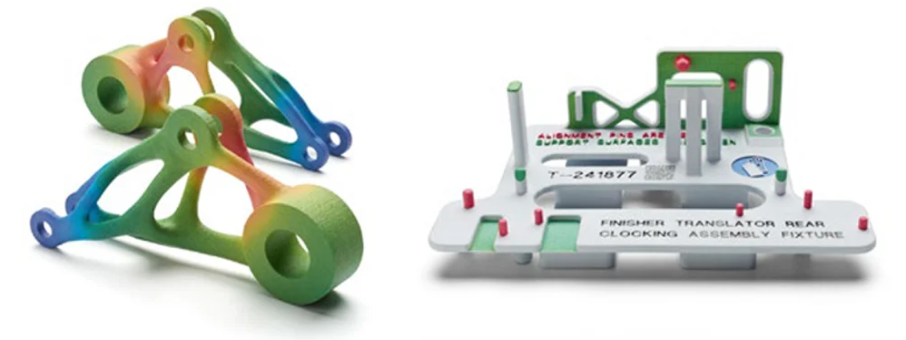
HP used to offer its Multi Jet Fusion technology in full color, but sadly discontinued its HP Jet Fusion 380 machine in 2021. Several on-demand 3D printing services still have this printer, but HP no longer supports it.
If you’re looking for full color 3D prints, check out the 3D Systems ProJet CJP 260Plus, the Mimaki 3DUJ-2207, or the Stratasys J55.
MJF vs. SLS
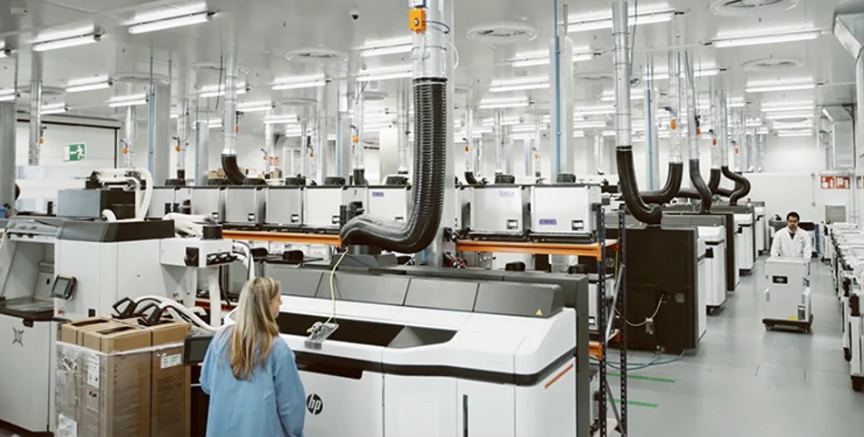
Multi Jet Fusion’s biggest direct competitor in the powder bed 3D printing space is selective laser sintering (SLS). On a superficial glance, they are quite similar – both use a heated chamber in which individual material powder layers are fused together without the need for support.
But whereas MJF uses inkjet-dispensed agents and a heating element, SLS fuses the layers together with a directed laser beam. When we start looking at the more technical details, other major differences quickly pop up.
FEATURE RESOLUTION
MJF printers produce prints in layers 0.0003 inches (80 microns) thick, with a minimum feature size of 0.02 inches (0.5mm). This means it can produce finer surface detail than SLS, which has a feature size of 0.03 inches (0.75mm).
That said, Protolabs notes that SLS can provide better small feature accuracy than MJF.
WALL THICKNESS
MJF has a minimum wall thickness of 0.02 inches (50mm), while SLS can produce walls as thin as 0.04 inches (1mm). As such, if thinner walls are a requirement, MJF is the way to go.
PART SIZE
SLS comes on top in part size, with a maximum envelope of 19x19x17 inches against MJF’s 11.1×14.9×14.9 inches. With that said, Multi Jet Fusion should still provide plenty of print size for most 3D printed parts.
MATERIALS
As mentioned, Multi Jet Fusion is currently limited in suitable materials. SLS on the other hand has a much larger compatible materials catalogue, and is therefore the technology of choice if specialty materials are required.
That said, new materials for Multi Jet Fusion are in development as you read this article, so this situation may change at any moment. Additionally, MJF-printed parts provide higher tensile strength than SLS and have much more consistent mechanical properties.
This is where color also comes into play. SLS provides more consistent surface color without additional products, although MJF’s capability for full-color CMYK printing might offset the salt-and-pepper-like gray of the untreated print.
BUILD VOLUME
In build volume, there is no competition. MJF trounces on SLS in print times, making it possible to produce several high-quality prints in the time it takes for SLS to complete one print.
WHICH ONE WINS?
Although it’s not a silver bullet technology, most 3D printing companies have begun to recommend MJF over SLS. The ultimate choice, however, comes down the requirements of each individual project. You should therefore evaluate your needs before making the final decision.
Buy a Printer or Outsource Your Printing

Although it provides lower unit costs than many other technologies, the MJF train can be expensive (starting at $50,000 just for the printer). Fortunately, most of the busiest on-demand 3D printing services worldwide have fleets of MJF printers at your disposal for one-off prints or ongoing serial production.
Because all MJF printers are manufactured by HP, all 3D printing services listed below can offer consistent part sizes and detail accuracies. This enables manufacturers to offer consistent part quality but localized production.
Just because all MJF printers are the same, doesn’t mean all MJF on-demand service providers are. When selecting your printing partner, focus on lead times, materials libraries, and additional services — such as coloring, polishing, chemical smoothing, design consulting, and NDA contracts — when choosing the best service for your purposes.
An easy way to pick the right third-party service provider for your needs is to use the 3D print price comparison platform Craftcloud, where you upload your part and MJF on-demand services provide quotes for you to pick from. Alternatively, check out our guide below to the top MJF 3D printing services.